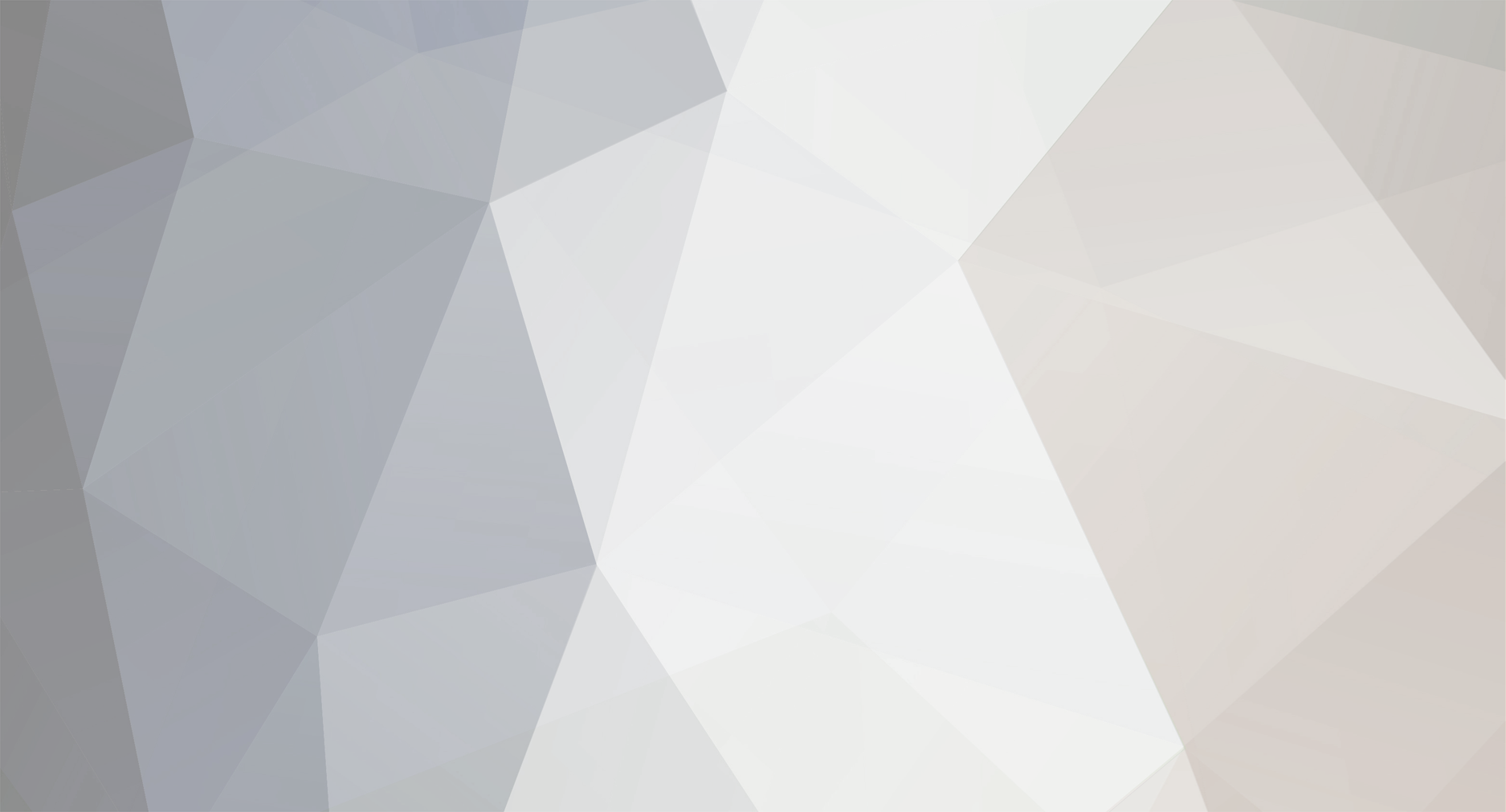
rogerpl88
-
Posts
5 -
Joined
-
Last visited
Content Type
Profiles
Forums
Gallery
Downloads
Blogs
Events
Store
Aircraft
Resources
Tutorials
Articles
Classifieds
Movies
Books
Community Map
Quizzes
Videos Directory
Posts posted by rogerpl88
-
-
Ian, I dont know how to post a picture on this forum but if you send me your email address to [email protected] (re-insert @) I will send you one showing a new rubber that failed soon after it was installed on the aircraft.No heavy landings this end.Ac has done just over 200hrs and ALWAYS hangared.What year were these defect rubbers installed and why wern't pilots in Australia as well informed as those in the UK? The procedure you describe would be difficult to perform unless you had another pair of eyes behind the nose wheel to inspect for cracking.
The other pilot that I know of had just performed a 100 hourly and had checked this area thoroughly.
When he heard of my problem he inspected again and saw some very small cracks. When proded lightly the rubber failed.
Where did you find out about the preflight procedure for the nose leg?
You seem to be quite knowledgable on this subject. Thanks for the reply Roger. Ian.
What year were these defect rubbers installed and why wern't pilots in Australia as well informed as those in the UK? ..........Not sure exactly but must have been around 2007. I cannot say why you are not informed but once the problem was known in the UK the yelllow rubbers were changed for the red type.
Where did you find out about the preflight procedure for the nose leg?.........Over time you make your own procedures so that you are know that the aircraft condition is to your satisfaction. Heavy nose wheel landings were a common occurrence when the Jabiru was introduced in the UK. It was due to a combination of poor rigging and pilot technique. As Inspectors, we quickly recognised the signs of a heavy landing with crushed rubber being one of them. For a preflight, I put my foot on the front tyre and pull the nose of the aircraft down - it checks the tyre pressure and also the 'give' in the suspension. After a while, you dont even have to see the rubber - you can feel the amount of 'give'. For the pilots with fairings - you have to make the choice of your aircraft looking good over a proper pre-flight check. Personally, I like to eyeball all critical areas so any fairing that cover these areas are not fitted.
Incidentally, the 'foot on the tyre' check can also be done on the main tyres. Gently move the aircraft back and forth by the strut while looking and listening. There should be NO movement where the leg is bolted to the fuselage. If you have a fairing fitted, you should be able to hear the movement.
-
2
-
-
There were indeed a batch of yellow suspension rubbers that did not last the first full power run. This was flagged up and many owners in the UK changed to the red rubbers that were being used for the larger 4 seater aircraft.The suspension bush collapsed without warning during the runup check about 3 weeks ago,causing the prop to contact the ground. Not happy:( Another pilot from my area heard of my misfortune and checked his ac. It looked ok until he poked and proded a little and then it fell to bits.We have both lodged SDR's with RA-Aus. Have had less than poor response from the Buisness Manager of Jabiru. She seems to want to blame me for not inspecting propperly but this is not the case. AC have always been stored in a hangar and well maintained. An email from their spares dept told me "the red bushes are better quality, and the yellow ones appear to wear out after a period of time." Thanks for nothing!!! I thought they were supposed to warn pilots of this in a Service Bulletin. I'm just lucky this did'nt happen on T/O or landing. I also had a passenger at the time. I don't want this to happen to someone else so have created this thread.Does anyone physically check their suspension? Apparently your supposed to although I can't find mention of it in the Flight Manual or Technical Manual or on their website.Going back a bit, the first suspension was made up of individual black rubbers identical to the top rubber suspension. These were sandwiched together with aluminium washers and locktite. They did the job but started cracking (just like the top rubber) after long exposure to the weather. The first batch of yellow nylon rubbers lasted quite well and only failed after a heavy landing.
There is of course no excuse for not recalling these poor quality yellow rubbers but owners also have the responsibility to preflight the nose leg assembly and if this is done properly, the failing rubber will show up. Put your foot on the nosewheel tyre and pull down on the propeller flange and inspect the rubber. If they dont hold their shape then change it.
-
With the problems Jabiru are having with their hydraulic lifter engine, one solution is to go back on step and offer a solid lifter version. While this engine may not appeal to the demands of busy flying schools, I know that many private owners will accept the compromise of reliability and power over the chore of having to adjust the tappets twice a year.
Adequate oil flow was the biggest problem with the solid lifter and this would have to be resolved if it were to be my 'forever' engine. In fact the oil flow problem was carried over to the hydraulic engine and in my opinion, one of the major reasons why the new engine was released with so many problems. Proving an engine on a test bed in a controlled environment (including a steady oil pressure) is not representative of an engine that looses its oil pressure when it gets hot. The hydraulic lifter and valve timing depends on a steady pressure.
-
Andrew,Finally i have been able to source an alternative to the standard Machined Thread Engine Through Bolts supplied by Jabiru. To go along with the ARP Nuts (rolled thread) that are supplied now as the fix for the failing through bolt (machined thread) issues we all know about, i have spoken at length with a manufacturer in Western Australia and he has imported in the correct thread dies to be able to manufacture a complete set of new Rolled Thread Through Bolts. There are 10 long studs and 4 short studs to make up a complete set. They are made out of 4140 round bar and will have a much higher strength due to the rolling process than the standard 4140 machined threads that are the only option out there at the moment. He is producing the first 10 sets for me tomorrow and will hopefully post them over to me early next week. They will be the slightly longer length so that you will still have a couple of threads protruding out of the new 12 point ARP nuts. The cost of these sets are currently around the $120 mark plus postage which is a great price. The more orders he recieves the cheaper he will be able to manufacture them for as he can buy in more material at a bulk discount.For those of you that are in need of replacing the engine through bolt and would like a set to match the new ARP nuts i have included the manufacturers details and you can deal straight with the Director of the Company.TL Adlard - 0430135816
Alliance Fasteners
8 Coolibah Way
Bibra Lake
Perth, WA 6163
I must stress that i have no interest in this company and i am not interested in becoming a supplier of these bolts but i thought that i would pass on the information for those of you who would like to eliminate the potential of the through bolts failing once and for all. I am not the first to use the rolled thread through bolts and, as i have always tried to do, i am just trying to find ways to improve the reliability of this jabiru motor.
I hope this can be of help to you and if you have any questions just ask.
Regards
Andrew
With reference to your post above.
I am new to this forum and joined having read your contributions on the subject. Until recently, I have been overhauling and servicing all the marks of engines in the UK with the earliest being serial no 24. I have learnt that it is always best to read between the lines when looking at a JSB and the one concerning the through bolts is worth looking at in detail.
Certainly there are problems with the threads failing and the JSB gives a number of contributory factors as to why. All quite plausible but the logic fails when the remedial action is applicable only to engines post 2200A1707 and 3300A6637. Why are engines 2200A1706 and earlier immune? I have stripped down and rebuilt scores of engines and never had a problem with the older through bolt threads failing.
Measure the OD of a pre and post thread and you will find that the later batch of bolts have undersized thread diameters. The worst case I measured was 10 thou undersized when compared to an equivalent AN6 bolt. Run a plain UNF nut up the thread and the play will be un-acceptable. in addition,inspection of the used MS nut threads and witness marks shows that a fraction of the nut thread is holding down the 30 ft lb torque. The MS nut is slight oval at the top to provide the 'self locking' feature and, in worst cases, the grip is only where the ID thread is smallest. That they are holding in the first place is testament to the inherent strength of the nut.
When you appreciate the above, you understand the rationale behind the JSB's use of a plain 12 point nut and locktite 620.
The proper solution is what you are doing and that is getting a set of through bolts made to the correct specification. If they are, you can revert back to the original MS nut or 12 point self gripping nut with no locktite. I would steer well clear of using locktite 620. It is was unnecessary before when the threads were to the correct spec. The use of locktite prevents the correct assembly of the barrels where the gradual torque down sequence and intermediate checks are essential. Knowing that incorrect torquing can distort the barrels when they get hot, I always use a hot air gun to gently heat the barrels and check for increased friction as I progressively torque down. Sometimes it can take 2 or 3 attempts.
I always thought that the original threads were rolled but had my doubts with the new batch because the threads were failing. A second opinion from a local engineering company say the are rolled. Certainly the thread quality of the earlier batch of bolts were acceptable and never showed any signs of failing when removed from 2000 hr engines.
Thanks for your work and offering us another source of through bolts.
-
2
-
Rolled Thread Engine Through Bolts Available as alternative
in Jabiru
Posted
Sorry to hear of your problem. A couple of observations.
1. Oil leaking from the base of the barrels does not necessarily mean that the nuts are getting loose. It could be worse. It could mean a failure(s) of the bush o ring seals which the through bolts go through. Since it is a through bolt, check the other side of the engine and if there are signs of oil seeping near the corresponding through bolt then use must be suspicious of these seals.
2. If the through bolts are failing because the threads are undersized then increasing the bolt diameters are not going to improve matters. Using locktite to make good is not good engineering practice - especially as the locktite can soften when heated.
I cannot understand why owners are prepared to use through bolts with poor quality threads
Roger