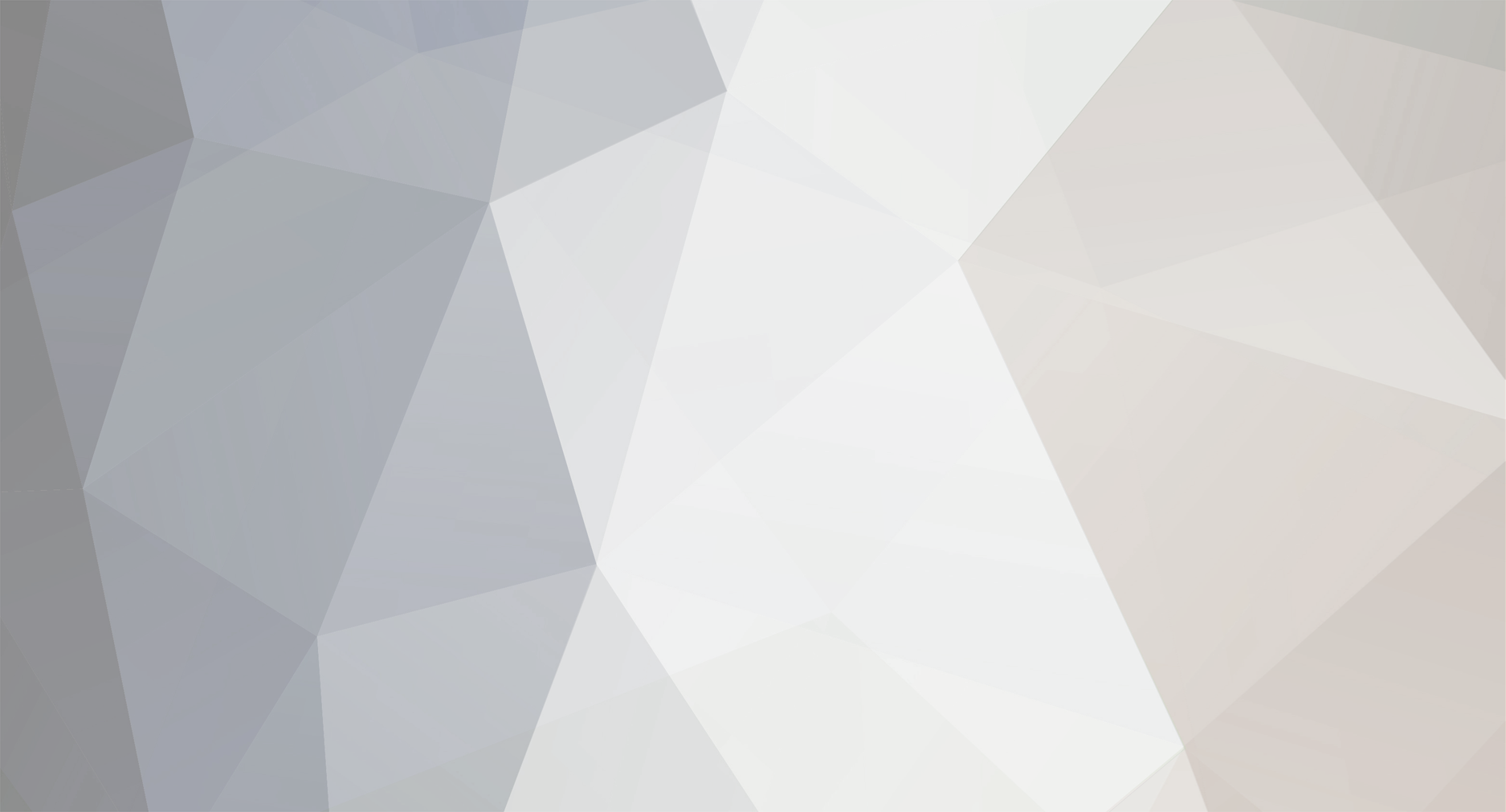
Rotax Service Centre
-
Posts
5 -
Joined
-
Last visited
Content Type
Profiles
Forums
Gallery
Downloads
Blogs
Events
Store
Aircraft
Resources
Tutorials
Articles
Classifieds
Movies
Books
Community Map
Quizzes
Posts posted by Rotax Service Centre
-
-
Hi Foxworker.Am I correct in stating that the wing assy has a 4000hr limit?? but what about time??is there a year limit..Thanks Richard..If I can be of any assistance to anyone with respect to skyfox wings, repairs, rebuilding etc. feel free to ask me any questions. I built pretty much all of the Gazelle wings, updated and re-wrote the specs. for them, and know them inside out. Also have access to the covering process and the fellow who did the covering in the factory. Repairing 'fox wings including hangar brackets, trailing edge sections, epoxy joints, drag braces etc. isn't rocket science however if you're going to do it yourself and you're not an L2, you need the correct info. and the correct proceedures on how to go about it. I've read some pretty disturbing comments written by people fixing their wings obviously not really knowing what they're doing. I am happy to help anyone who is prepared to listen and do it properly. cheers. -
Hi To all..With regards this placard concerning RPM operating range.during the 90's we experianced quite a few crankshaft problems with both the 503 but more so with the 582 engine.Rotax identified detrimental vibration harmonics at various RPM range,depending on whether the engine was fitted with a pull start or electric starter(addition of ring gear added weight and changed inertia of crank).The crank was nitrided,centre gear for rotary valve modified and later vibration damper fitted..We placed placards at the time to avoid continues operation within these critical ranges,however I dont believe I have noticed any current warnings by Rotax..In the case of the Stutbraced Drifter the aircraft is so heavy that operating out of this range would be difficult to say the least.saw this placard on a 503 drifter on the bay.does anyone know what its about ive never seen a warning like that befor does it apply to all 503s?AUSTFLIGHT AVIATION
Avoid continouos operation between
5800rpm and 6400rpm.
As usual these are my opinions based on my experiances and not necessarily those of the Factory..Regards Richard..
-
1
-
1
-
-
Hi to all concerned with this debate..Rotax make and design the engine to a specification to deliver the required power output,max and cruise and to obtain the specified TBO without any failures.This output is Dyno performance and they are not really concerned with what aircraft you have or your frugal attempts to reduce fuel consumption or cruise speeds.There is to many varied designs of aircraft,draggy ones and slippery ones.Rotax publish recommendations to cover the best for their engines and its up to the manufacturer or operator to use this or apply their own and except the consquences.There is a lot of threads on topic of what the maximum rpm should be on a Rotax 2 stroke so I decided to find out the truth behind all the beliefs.I first checked the rotax manual,then rang Wal at bert flood ,then a few other dealers (qld and uk)eventually I was able to email bombardier Rotax HQ Austria. was interesting on what they specified.All Rotax 2 strokes share the same RPM
.MAX 6800 rpm REDLINE REDLINE REDLINE BEFORE ENGINE DESINTIGRATION.
Max Rpm should NOT exceed 6500 rpm. running no more than 5 mins max(IN STREIGHT AND LEVEL FLIGHT ONLY)
static full power should be around 6000 -6200 rpm max
take off climb should be 6200-6400 rpm max
and streight and level flight at full power should be 6500 Rpm 5 mins MAX
maximum rpm refers to full power in streight and level flight NOT TAKE OFF CLIMB!!
I however climb out at 6500 rpm but I may be rethinking this now.
Whilst Rotax manufacture the engine the ultimate responcibility of performance etc is the aircraft manufacturer.Whilst the max limit is 6800 RPM for 5 min the 582 is robust enough to over prop and under prop and still do the job,depending on the propeller you have fitted..
We set the Austflight drifter 582 strut brace with 4 blade Brolga prop with 17degree pitch blocks to obtain 6420RPM static which related to about 6550 climb out and 6800/6900 full throttle straight and level and advised owners after reaching a safe height on take off to then reduce Rpm back to around 6200..
Rotax fuel the engine to assist cooling of the combustion chamber during full power and yes it uses a lot of fuel,but it is the safety valve,if you dont use full power on take off and resist pulling back on the throttle to early,this is when the dredded piston siezure occurs.Your life is worth more than a little less of fuel.. I have seen a lot of engine prop combinations over the years and this 582 engine can handle a lot of punishment but it is still a 2 stroke engine and as such is subject to design/operator limitations.Since unleaded fuel and better oils come on the market we have very little problems with the 582 and my customers regulary obtain 600 hrs between overhauls with no decarboning and only carby maintenance,regular servicing etc,no opening of the engine..
-
3
-
4
-
-
I'm looking at Ed3 Rev 0 (2012), operators, installation, maintenance and heavy maintenance manuals. Searching the pdf's for "ignition" or "plugs" or "CDCI" I get no hits which refer to that statement.If you can find the source, I'd be very interested.
.
Hi..as far as I am aware I have seen no Rotax publication that states about grounding the CDI's when carrying out maintenance proceedures other than If the aircraft has seperate Toggle type switches,then no problem,however as Maj pointed out if you have the combined starter and ign switch then you need to isolate and or ground the CDI modules.I know of only one site that states/ shows this and this is Rotax Owners Assoc Network vidio on Direct compression proceedure in which they advise to disconnect the 6pin nylon connector from the stator to the CDI'S consquently isolating them from the voltage imput during cranking..
As we have recently had isolated CDI module failures I aggree that it would be a good cockpit practice to attempt the first start using only one switch and alternate switches with next start as a means of checking if the CDI'S might be getting a bit tired at the low cranking RPM ..
Rotax needs to be aware of field problems and the more imput from Forums like these can only be to every operators advantage.Thats my opinion anyway!!
Safe and happy sky's..Richard
-
1
-
5
-
Running Hot
in Skyfox/Gazelle
Posted
Hi Keith..I believe the 80 hp gazelle if fitted with the radiator cooling kit(shroud on sides of radiator and oil cooler) requires coolant at 80/20 Glycol/water..
Most installations require around 2 ltrs..Oil temp should operate between 90/110 c and CHT temp the same with max to 140c..
Unmodified cooling system requires 100% Glycol or it will spit the coolant out.. Not sure about Evans as i have not come across anybody using it in a gazelle or Skyfox. With regards air entrainment i think its recomended to lower the tail and bleed the system.
Regards Richard..