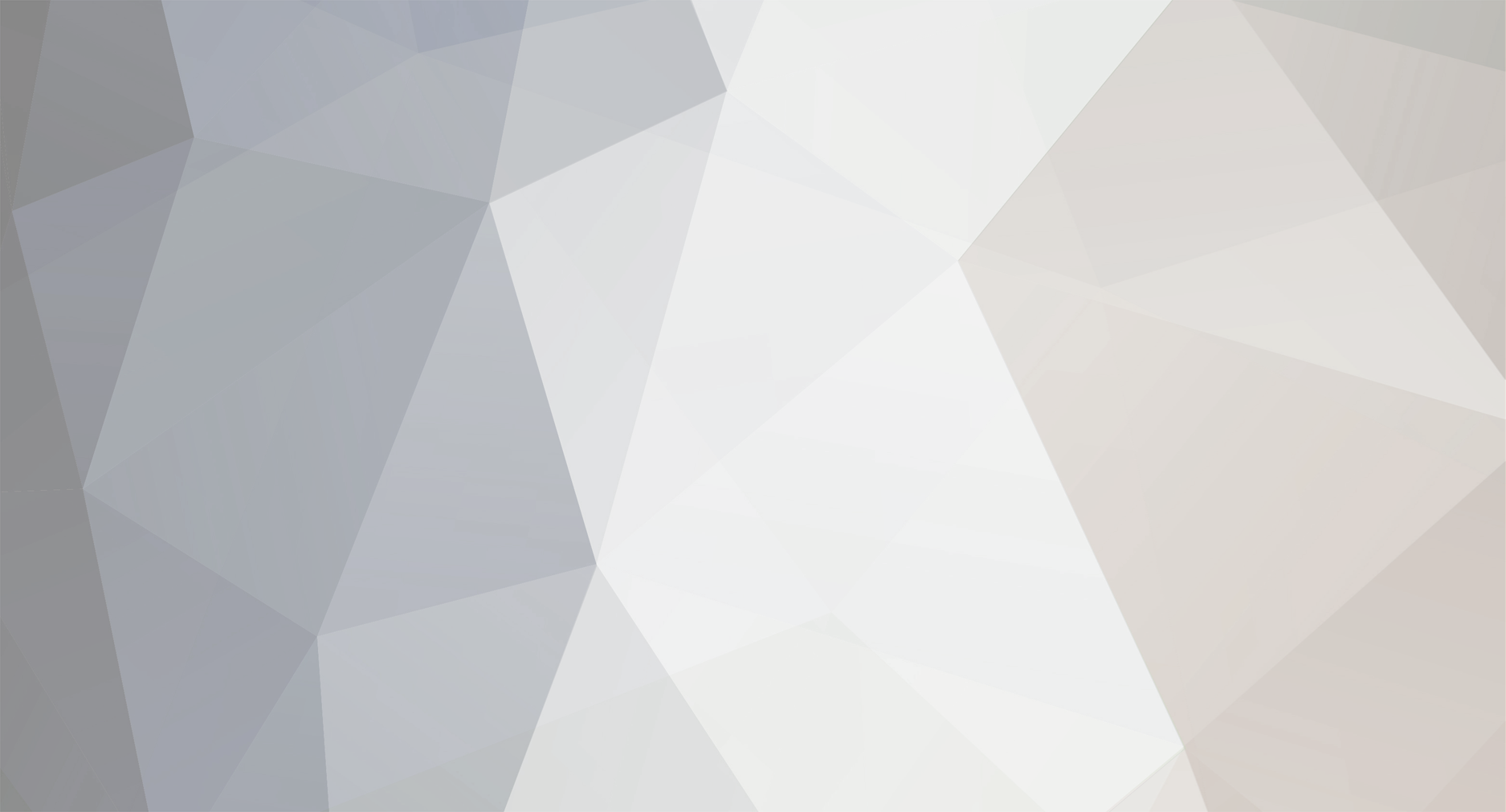
carlsnilsson
-
Posts
27 -
Joined
-
Last visited
-
Days Won
2
Content Type
Profiles
Forums
Gallery
Downloads
Blogs
Events
Store
Aircraft
Resources
Tutorials
Articles
Classifieds
Movies
Books
Community Map
Quizzes
Posts posted by carlsnilsson
-
-
On 11/03/2011 at 8:13 PM, Guest Wigg said:
Sue: Could you msg me please or post how to contact you thru this website. I am now looking to replace my lost copy of a CA22 T/W Pilot Operating Handbook (POH or Pilot Notes or Flight Manual, as it is variously called). Regards Carl
-
G'day Keith: that's most kind. Q. Do you have a paper book copy or CD? If the former, I am presuming there is a procedure for removing and replacing the horizontal tailplane. If you have a scanner, perhaps you could scan those pages and upload a file or zip it and email me PM (not quite sure how to do that, but I guess the procedure is explained by the webmaster somewhere on this board - my son tells me it is bad practice to publicly post an email address). I'll look tomorrow. Alternatively, if no scanner, I should be able to PM you my postal address and ask you to copy pages and post.
Of course, if there is nothing in the manual about removing the tailplane, we can forget it and I'll just follow my normal procedure of simply winging it. It's not exactly complicated - i just thought it would make a nice change for me to read what i'm meant to do before I go ahead and do things in the wrong order. (Removing the carbies from the 912 is one such example - there's the right way and several wrong ways of going about it!)
On the other hand entirely, if you have it on CD, we should talk some more! I'm talking about the maintenance manual for the aeroplane, not the 912.
Regards Carl
-
G'day Wigg:
In note above where, nearly five years ago, you offered to post a CD copy of the Skyfox (CA22 or 25) maintenance manual to someone in need. I have a CA22 taildragger Ser. no. 22027 Reg. 55-0688 for which a copy would be most useful. Is your kind offer still open? I would quite happy to make a modest payment for your costs plus post - maybe could use Paypal if you have an account or whatever. I fly out of Cambridge, Hobart.
Regards
Carl
-
I was wondering the other day if anyone has thought of having a Skyfox/Gazzelle flyin' date=' maybe even have it as a part of Natfly, just some thoughts and I realize that as soon as a good idea crops up someone gets to work hard to make it happen, it would be cool to have a line up on the apron!!! [/quote']Good thinking 99! 'bout time we did that again. I really like Temora - friendly people, good old pub, old warbirds flying - and I haven't been there for 5 years.
I just had some comms with Daffyd Llewellyn - he confirmed that the Darwin fatal accident was with a CA21 which had suffered some significant rot problems - Llewellyn's analysis, which was submitted in Court with a heap of supporting evidence, read like the denoument in an Agatha Christie episode of Poroit. To my mind, it confirmed that that accident almost certainly was not caused by flutter or even rotten hanger breakage (which I had always understood from the initial report), but rather was probably initiated by overloading the wing and breaking a rib near the rear spar (the rib nearest the lift strut attachment point), which itself had suffered weakening due to moisture ingress. That rib (and hanger) suffers the most strain from the ailerons when using them over-vigorously at speed. You should pay particular attention to drain holes in those bays and the condition of that hanger. "Look after the aeroplane and it will look after you", is the main message.
Regards Carl
-
1
-
-
Guys my question might have got overlooked in the flurries of posts' date=' the skyfox forum has never been as busy, so does anyone have any clues as to the flutter I've heard they can exhibit! [/quote']There is no real "issue with aileron flutter on Skyfoxes compared with Avid Flyers or Kitfoxes". That's a furphy. We have been taking about possibilities and precautions and' date=' by and large, these apply to many recreational aircraft. [/quote']Just to finish up my comment on the fact that there is no particular issue re flutter, providing the ailerons are kept adequately in balance, I have dug out some correspondence I had with Daffyd Llewellyn (the testing Reg. 35) in Dec. 2004 following the Bluff Central accident in which a 'Fox tragically lost a wing through being flown too fast in turbulence. He wrote (copied to then RAA-Aus tech manager Jeff Shepherd):
"Carl, thanks for copying us in. I had already let Jeff know about the development history of the Skyfox aileron system; however I would comment, from prior experience, that it is counter-productive to hypothesize on the cause of an accident until ALL the investigation data is in. I would, however, comment that so much effort went into eliminating the aileron flutter problem during the pre-certification development phase, that a Skyfox that was both built to plans and correctly maintained, is extremely unlikely to experience any flutter, let alone a catastrophic flutter, so long as it is being operated within its certificated limitations.
Therefore, if indeed aileron flutter was a factor in this accident, it would follow that some defect condition must have existed that would pre-dispose the aircraft to flutter. Because it takes a fairly significant excitation to initiate flutter in that aircraft (due to the friction in the aileron hinges) such a condition could develop over time, and the fact that the true flutter onset speed was reducing down into the normal operating range would be masked until the aircraft encountered something (e.g. turbulence) that set it off.
Further, for that to cause the wing to come off, suggests that there was more to it than simply flutter, because I fluttered the ailerons on the prototype CA21 a number of times (approaching a dozen) with no detectable structural damage until the last one, which occurred at around 108 KCAS; it broke a single aileron hanger.
Therefore, detailed examination of the wreckage is necessary to identify, if possible, whether any pre-existing degradation to the airframe existed; and until we have the results of that, I believe it is unwise to speculate."
"The accident" to which Daffyd refers is the Bluff Central accident, on which he subsequently supplied a full and detailed report on which I intend to write further, as it holds some important lessons for Skyfox owners. I hope the above lays to rest any unfortunate impression that may have been given on this thread that Skyfoxes have a particular problem with aileron flutter. It just aint so.
Regards Carl
-
hey guys I have always wondered why the skyfox had the issue with aileron flutter but I've never heard of it on the kitfox or the avid' date=' I check out the kitfox forum at times and you never hear of them having a problem ,even with much higher VNE, any explanations? [/quote']give me a call as I know someone who can probably supply strut material etc. for your repairs' date='(he is also approved to build new struts as well if need be), and "possibly" a spar if you require one [/quote']To continue on the question of flutter on 'foxes but not on Avids or Kitfoxes: I'm trying to remember, but I think the Kitfoxes have flaperons? Can't see that that would help. Also, the Kitfox spars do have an inserted vertical web, but I doubt that would resist bending as well as the integral web on the fox spars. In general, I do not think that the Kitfoxes were as sturdily built as the CA22's. For example, the CA22's sometime after serial 22010 but well before 22027 has 5/8 inch moly (4130) longerons, whereas the earlier ones and the CA21 had 1/2 inch tubes. I suspect (but don't know) that the Kitfoxes of that period only used 1/2 inch also.
Perhaps someone can enlighten me on the Vne for the Kitfox? I see no reason offhand why it should be greater than that for the CA22 (93 kn). That Vne is conservative, in line with proper practice. I can admit to (quite foolishly) exceeding Vne on the dial on a few occasions and having nothing bad happen. So Tony Curzon's report of mild flutter or at least vibration on one occasion and the suspected flutter as cause of the Qld incident are about the only two occasions that flutter has been raised as (possibly) occuring on production model foxes. I am discounting the accident in the NT as that was most likely caused simply by a rotten hanger snapping under load. The report (no. 199800361 for Skyfox CA21017) does not even refer to flutter. So in fact there are no confirmed cases of serious aileron flutter in any production 'fox of which I am aware. There is no real "issue with aileron flutter on Skyfoxes compared with Avid Flyers or Kitfoxes". That's a furphy. We have been taking about possibilities and precautions and, by and large, these apply to many recreational aircraft.
I have refered to foxworker's comment about building new struts. If I were putting a new strut on my 'fox I would incorporate a modification suggested by Daffyd Llewellyn - who, as a Reg. 35 engineer, can properly sign it off on a certified aircraft. I will refer to it more fully in another post on the behaviour of these wings in turbulence.
regards Carl
-
Guys my question might have got overlooked in the flurries of posts' date=' the skyfox forum has never been as busy, so does anyone have any clues as to the flutter I've heard they can exhibit! [/quote']Not much of a clue, actually, except that the incidence seems to have gotten a bit exaggerated. Flutter has been implied as a possible cause of two incidents of hanger breakage, so far as I'm aware - and been reported by Tony Curzon in mild form on one Fox. One case of hanger breakage (in NT) was with rotten hangers. The other in Qld, as best I recall, also had some incidence of rot in the hangers, but I would have to check that report. The case with pilot and Tony Curzon was mild, I am told, resulted in no breakage of anything, and did not repeat itself after the fuselage bush was maintained/replaced. Only the NT hanger breakage resulted in a crash.
From what I recall of what Daffyd Llewellyn wrote, the flutter he observed during testing was caused by feedback between the wing structure and aerodynamic forces from movement of the ailerons. This seems to be made worse by out-of-balance ailerons. That was his advice resulting from the incident (departure of an aileron) in Qld. The lesson is pretty clear - periodically check the balance of the ailerons - particularly note any rattle due to a loose weight when you move them up and down sharply and make sure that they are adequately drained and water does not have a ready ingress - and you'll be OK. I have never experienced flutter myself. Visitors - got to go - will continue later.
Carl
-
.That's good advice. You can get pretty compact emergency parachutes that open smartly. Glider pilots sometimes have them. Use as a cushion - either for the back or the bum.If you think that there is a chance of even "moderate flutter" and you are going looking for it perhaps consider all the risks and mitigating actions eg a parachute.Carl
-
Firstly, it takes a pretty good crack to bend that spar. When I pushed mine (backwards) through hitting a tree, the shear force tore the mounting of an internal diagonal drag brace and showed that shear by tearing the fabric above the fuel tank. The innermost bay with the tank has no drag brace and hence can be more easily distorted in shearThere's no tears near the tank - the only one is in the underside near the spar attachment point where I think the spar bent & went through the fabric. - apart from the spars & the broken hangers the tear is the only other sign of damage on the wing. I will check the wing attachment points.There is one other issue for me and that is that one of the frame tubes - the one from the upper corner of the left windscreen/ front wing attachment point and runs diagoally down to the centre of the screen is bent slightly in toward the pilot.- the tank taking some of the distortion. My front wing mount bracket (the short vertical tube into which the clevis pin goes) was also bent, as was the pin itself. I managed to straighten the bracket tube, after checking that the weld was not damaged, although I spent a couple of days doing it rather carefully. In your case, it rather sounds as if the frame tube took up the distortion. If it is not kinked, then it likely could be straightened.
As for the spar, all may not be lost. If you decide to go ahead with repair, get into contact with foxworker. He has some good contacts in prime Fox country (SE Queensland).
Regards Carl
-
G'day Mike:Hi 'Foxworker' - I've just started looking at a CA25 TG that has been 'flipped' - tripped while on the brakes.Either my brain (?) has gone to sleep or I'm not familiar with the "TG" in CA25TG. I presume that's a taildragger CA25 -yes? If all the aileron hangars snapped and the wing struts ruptured, it would seem that the left wing took a pretty severe impact. Did the fabric tear above the fuel tank in the bay nearest the fuselage - that would indicate a fair amount of shear on the wing which may have bent the spars - or at least the front spar. Also, take a look at the wing attachment points.
On the other hand, I have a friend with a Fox that hit power lines on final approach and nose-dived into the ground. He and his wings were undamaged, although the fuselage needed some repair. It flies beautifully today.
Carl
-
John:GA LAME has done a airframe check last year however I was not in attendance to point out my concernI'd be surprised if anyone could answer your question authoritatively. There has not been any AD or AN re wear on these bushes, to the best of my knowledge. Certainly a number of Foxes have done lots more hours - some up around the 5000 hour mark, I believe. There are probably quite a few which have done 3999.9 hours! However, I would use my own judgement, based on the following:- firstly, can you rattle the whole aileron on the ground inside those bushes? Flutter would probably be more easily induced by a change of aileron angle of attack rather than a minute wobbling of position. (I'm speculating, but this would be my thinking). Flutter is an oscillation, so you have to have at least two opposing forces. When an aileron is out of balance, the moment of inertia changes (probably increases). Flutter occurs when wing/aileron distortion (i.e. elasticity of the system, which may have several components) opposes the air pressure distribution which is distorting the system. In addition, some important part of the wing/aileron structure needs to have a resonant frequency in tune with, say, the fluctuating control surface. "Out-of-balance" for the ailerons is an important factor because it effects the moment of inertia which determines the natural frequency. If you ever felt a vibration of the ailerons that came and went, for example, that would be a warning sign not to be ignored.
Now, Daffyd Llewellyn, when testing, found that he could sometimes induce flutter in the Fox ailerons (I can't remember whether they were one piece or segmented, but I can check) at speeds as low as 65 kn IAS by giving the stick a sideways rabbit punch. If you are worried about your ailerons, try that! Try it first at low speed, say 60 kn with a very modest sideways knock. If nothing results, increase the force of the sideways knock a little. A small step at a time is the watch phrase of a test pilot! On one occasion instructor Tony Curzon discovered that he could induce some modest flutter at cruising IAS in a friend's Fox and immediately reduced speed (the correct thing to do) and promptly landed. The torque tube bushes through the fuselage were pretty loose so they did something about that and the effect went away, so I am told. I have given my stick the sideways knock test at 70 kn with no effect. That's good enough for me. "If it ain't broke, don't fix it" might be applicable here with regard to the hanger bushes. The point about the sideways knock is that it generates a sudden force. That is, the suddenness - the short rise time - incites a range of frequencies, unlike a gradual push. The range of frequencies might be enough to excite some resonance in the system. That would be a warning and that, I think, would be what an aeronautical engineer might suggest in order to answer your question.
Regards Carl
-
1
-
-
John: Remember, this is a flexible wing. The original ailerons before certification were one piece. When loaded in flight, the wing bends enough such that the original one-piece ailerons jammed solid. That's what Llewellyn was testing. That's why the ailerons are now segmented. The wings still bend in flight and so does the full length of aileron. Play when the wing is unloaded on the ground does not necessarily mean play in flight. I suspect that you need some degree of clearance in those bushes to prevent binding in flight. So long as the bushes are still in one piece, I don't think I would worry about it, unless the aileron as a whole rattles around. The wings can flex inches in flight. I think the one bush you should pay attention to is the one that constrains the torque tube where it emerges from the fuselage/turtle deck, based on the experience of my friend Tony Curzon who once suffered aileron flutter. I'm not an expert in this matter. Few people are. Llewellyn is.Yes the plastic bushes round the aileron tube it is only slight play but I would like to take it out if possible. I can see no way of doing this apart from taking the whole aileron apart.Carl
-
G’day Mike:I'm new to RAA and learning on a CA21 with a 912UL that I bought late 2010. With all the rain up in Mackay the airfields have been wet, so not many landings occuring. The skyfox (55-0606 - ca21-037) has the ply hangers. I have read as much as I can find about the hangers. Checking mine and getting a number of opioions from L2's and a L4 all appers good condition. I did purchase one alloy hanger kit from Gympie for the hanger at the strut to see whats involved in fitting the alloy hangers.My present plan being considered is that if I ever decided or had to reskin the wings i'll replace all the hangers. Also I have a thought that it could be a plan to mod two hangers on each wing (4 in total) the inboard ones and the ones at the strut. (THIS IS ONLY AN IDEA THAT I WOULD GET EXPERT OPION ON BEFORE DOING.)I am keen to learn of pre flight procedures to assess the sufficiency of the hangers. Presently I have a good close look at them, including at the attachment to the trailing edge area and then I apply pressure up and down and side ways slightly to judge the firmness including the press test on the sides to check for softness (rot) of the ply.
Cheers
Good luck to you learning on a CA21. I don’t know if you have previous experience with taildraggers, but learning on a CA21 is not the easiest way. I had a few hours solo on a Piper Cub back in 1968, but when I started again on a CA22 in 1996 at Penfield, Vic., I was classed as a slow learner. I had difficulty, to say the least, in landing! Eventually circumstances caused me to transfer to a Drifter on which I made better progress and eventually, much poorer in pocket, I got my certificate! I then hotfooted up to Caloundra and bought a much-used, much loved and sometimes-abused CA22, namely 55-747, which my friend Tony Curzon (instructor) and I flew back to Penfield. At the time, I was not aware of some of 747’s chequered history, but I have to say that I kept that aircraft on line at Penfield for many years and it never gave any significant trouble and helped a lot of students get their certificate. Since then I have bought two others and sold one, keeping 55-0688 for my own use sinceY2000. I could converse at some length on the joys and pitfalls of learning on a Fox, but maybe not on this thread.
In my opinion, wooden or aluminium hangers is not too much of an issue with respect to Fox wings. Get hold of Skyfox Aviation’s Service Bulletin No. 24 or the equivalent issued by the (then) AUF – now RA-Aus. There was an AD or similar issued by CASA on the subject, as there were a number of VH-registered CA-22’s, not to mention all the Gazelles. Basically, SB 24 gives some guidelines on examining wooden hangers. As best you can, look for any signs of wood rot. You can’t really examine them properly unless you remove fabric. What you can and should do, is make sure every wing bay has a decent (>4 mm say) and clear drain hole close to a rib and as near to the trailing edge as possible. Ailerons should also have drain holes in each segment near the trailing edge. Also, there was an AN and AD (Airworthiness Notice and Airworthiness Directive) regarding the removal of the outermost bit of the outboard aileron (outside the last hanger). The aim was to prevent water ingress – which can also be achieved by application of a suitable filler material through the slot for the hanger bracket. Use your common sense – you are acting to prevent water getting into the aileron segments and providing a means of letting any water out.
Wood rot takes place when moisture is present around unsealed wood and there is lack of air circulation. Water inside wings is a pretty good starter for the fungus. That’s why foxworker stressed the sealing of all wood surfaces. Unfortunately, on some early wings (CA21 and CA22), some epoxy joints were not made with proper attention to smoothing out fillets with a sufficient amount of epoxy and blending to the wood , particularly around the trailing edges where they attach to the ribs. Any cavity, be it in your teeth or an epoxy joint to a rib inside the Skyfox wing, provides a nucleous for rot. This could well apply to the attachment of aluminium hangers to the wooden ribs, just as to the wooden ones.
Foxworker would advise you to take a look at your trailing edges. Are they even where they join each rib – that is, does one side sit higher than the other? Feel them between thumb and forefinger. If one is loose and co-joins a hanger, you have a potential site for water penetration. You seem to be doing this OK. Don't get too obsessed with this matter. If you read the ATSB report of the NT accident (No. 199800361) you will see that the rot was widespread and advanced and should have been very detectable.
It helps a lot if the aircraft is hangared (I’m spelling it correctly this time!) – a Fox is not a machine which should be left outside in the elements for months at a time. This is not to imply that it has to be cosseted and is particularly fragile – but a machine of wood and fabric is not designed for prolonged outdoor storage in the tropics.
To me, these are the issues that warrant attention – more than the question of wood vs aluminium hangers. The other matter to arise from the two occasions of which I am aware a hanger has broken in flight is the question of ensuring the ailerons are balanced – that is, the C of G of the ailerons has not moved aft either due to a weight coming loose or water ingress and retention. There is an AN on this and you have to remove the ailerons (not a big job) to check. As I said, if you get severe aileron flutter due to unbalanced or insufficiently supported ailerons, things will quickly tear apart regardless of whether the hangers are aluminium or wood. I would prefer the guilty aileron to depart swiftly from snapped hangers and broken aluminium torque tube and good luck to all who sail in her! I would watch it flutter to the ground as I flew home with one good aileron! But it won’t happen to me!!
Now you have me going on this forum, I want to write something about the behavior of the wing in turbulence – the easy guide to Daffyd Llewellyn’s enlightened report. Give me a couple of days.
Regards Carl
-
2
-
-
I'd like to design a wing with a friese aileron and flaps' date=' or maybe adapt the highlander wings , they look pretty good [/quote']Go for it. However, remember that the Skyfox is a certified aircraft and, unless you have half a million dollars or something of that order, you won't get your wings certified! As a comment, I would say that I've never really felt the need for flaps on the Fox - it sideslips pretty well and you can safely carry that slip close to the ground. Pilots of this type - or most types for that matter - should go to a safe altitude and then try stalling with backstick in a heavy sideslip. In other words, real crossed controls. See what the aircraft does. My Fox is benign - it simply wallows down. Some aircraft are real nasty, can flip and/or go into a spin. It pays to know your type. So, in the Fox, you can carry or initiate a good sideslip right down to the flare. Just straighten up! Flaps would give you a lower landing speed, but I don't know by how much. The wing is already somewhat inefficient with the undersurface cambered.
Daffyd Llewellyn designed a new wing for the Fox, but the estimated cost was somewhere around $20,000 about a decade ago. The Eurofox has a completely redesigned wing, but I note that the two spars are about the same diameter as those in the Fox (61-62 mm), are made of heavier material (2 mm instead of about 1.6 mm), but don't have that marvellous central vertical web that gives the custom-drawn Fox spar greater stiffness and strength - and makes it so difficult to replicate or get a spare. Reputedy, after Skyfox folded, the spare spars went to Dubai and were (possibly) melted down. My guess is that there are one or two still squirreled away somewhere in the country by far-sighted owners.
To the best of my recollection, the Fox wing was static tested to above 7G - "'til it bent like a bow", I have heard. I know I have pulled 4G plus a bit with my earlier Fox, as recorded on a G-meter, without any ill effects. Don't recommend it as a normal practice, though, as all stress has cumulative effects.
Just making a few comments in response to your input. Treated right, the wing is fine, in my opinion. Two weeks ago I flew mine back to Hobart from a trip to Melbourne and Canberra through some most unpleasant turbulence in NE Tasmania. When between Flinders Is. and NE Tas., Melbourne Centre passed on a severe turbulence warning for NE Tas. just issued by BOM. Not much I could do about it! The wings and control were just fine and show no signs of over-stressing - more than can be said for the pilot!
Some of the older Fox wings were not built with quite enough attention to detail as regards the epoxy joints of metal to wood and wood to wood and the trailing edges were a bit inadequate - you will see some scalloping under the tension of the covering. Foxworker, who opened this thread, is the master here. He repaired my broken wing (replaced the front spar) and generally showed me some of the skills of a master tradesman regarding the refurbishment of these wings. When it comes to appreciating the behaviour of these wings in flight, I defer to (retired?) Reg. 35 Engineer Daffyd Llewellyn, who brought the wings and ailerons to certification for Skyfox - and who flew them beyond their certified limits. These are the people who know what they are talking about and not just posting wind! I will say more about this in a reply to Blueadventures.
Regards
-
I'm a CA22 Skyfox owner and have been for 15 years. I have also followed accidents involving Skyfox wings and ailerons reasonably closely, having disagreed with the AUF's Technical Manager Mr Hewitt-Cook over the incident in Qld in or about the year 2000 which a Skyfox lost one aileron and landed safely. That resulted in an AN 2-2000 which required the chrome moly insert to the aileron torque tube OR an X-ray inspection of that tube and it's junction with the aileron crank. At the time I wrote (to AUFCHAT) " it is likely the root hanger broke first - but the real question is why did they (or at least one) break? Both Bill Whitney and Daffyd Llewellyn (Reg 35 Engineers) believe flutter is the likely cause - most probably due to an out-of-balance aileron....". Now, those two CAR35 engineers are two of the most knowledgeable and respected Reg 35's in the country and Daffyd Llewelyn hada lot to do with testing the Skyfox wing and aileron - of which he is not particularly fond. Out of balance ailerons will flutter and that will likely tear off an aileron regardless of whether it is attached with Al or aircraft quality plywood. In this particular instance it was and still is my view that Mr Hewitt-Cook incorrectly attributed the initiating cause as torque tube attachment failure when that failure was subsequent to a hangar failure due to flutter - due to an out-of-balance aileron probably due to water ingress. Two good things came from this, however: firstly, further checking revealed a lot of out-of-balance ailerons and more attention was paid to having proper drain holes in each wing panel and each aileron segment."One aileron failure accident was in the Darwin area, there was evidence of wood degradation on that one. There was one in the Cabulture area, where the female pilot threw a prop blade, and the resulting vibration shook one of the ailerons off the aircraft. She did not survive that encounter. The aircraft in question was rebuilt and I saw it about a year ago at South Grafton airport. There was one other involving an aileron failure, which was also a double fatality, I believe possibly in Victoria somewhere.The one in central Qld, also a double fatality, was probabily the strut failure you mention. I read the accident report closely, and they basically blamed a failure of the jury strut, leading to wing separation.I disagreed totally with their report summation, and some...
Another result was that here in Tasmania one Skyfox owner tested a standard aileron section flying free (no restraining control) at about 7o kn and it was perfectly stable with no sign of flutter - as expected. Thus, if you lost one aileron and it broke free of the aircraft or the controlling torque tube snapped for some reason, you could adequately fly on one aileron, as happened in the incident in Queensland that gave rise to AN 2-2000. I would much prefer an aileron to depart entirely than hang on and inhibit the use of the other.
I am aware of the accident in the NT, in which a hangar broke due to wood rot and that was a fatality because the aileron hung on with the remaining hangars and the aircraft was uncontrollable. Note the common factor here - the aicraft were left out-of-doors in tropical climates and the hangars deteriorated due mainly, I believe, to inadequate drainage.
The awful fatality of father and son in central Queensland was not "probably" due to strut failure - it was certainly due to strut failure. Again, Daffyd Llewellyn was the engineer whom the ATSB had investigate and his investigation and report were both thorough and professional. The forward lift strut buckled under severe compression load caused by a strong turbulent downdraft (which pushed the jury struts into the wing) and then the following updraft snapped the weakened lift strut. There was some evidence, if I recall correctly, of excessive speed in the severe turbulence of the day. Quite frankly, to disagree with the expert report by a Reg 35 engineer of great experience who knew the Skyfox limitations intimately and had examined the broken aircraft and all other evidence, does not do you much credit. It is not widely appreciated that, above 70 kn IAS, the forward lift strut on a fox is not under tension, but rather under comprsssion. That is why it is of larger cross-section than the rear strut which actually carries most of the load. The front strut needs buckling strength. It is also why, when you are flying in turbulent conditions, you should SLOW DOWN! I'm talking about 60 - 65 kn - forget the maneuvering speed limitation of 80 kn.
I am not aware of any of the fatal accidents to which you refer due to wooden aileron hangar failure apart from the one in the NT. Rather than vague assertions of fatalities here, there and everywhere, I ask you to do a little research and list the history accurately. Certainly I may have missed one, but you have made these sweeping assertions, so please back them up with references.
Carl
-
2
-
-
Oh dear! There's me rattling on about SCR's based on a misunderstanding! Comes of being late at night and those funny pills! I agree, the 26 deg may be fine for full power, although Ducati didn't have much room to play around. (You have to be able to start - would not want any more than 6 deg BTDC or the poor old sprag clutch would suffer even more - and the 26 deg would be set by a trigger pulse width apparently of 20 deg). If you only need positive delays - i.e. no more than 26 deg BTDC, then that makes it simpler to design a "front-end add-on". I'm a bit curious as to how they switch from trailing edge of the trigger pulse (6 deg) to leading edge (26 deg). Have to look at the pulse shape sometime. Anyway, all (!) one really needs to do is adequately simulate that pulse shape and provide a variable delay based on rpm. As I said before, I have an ambition to be able to hand start the 912 (in the case of a flat battery in some corner of a foreign field) and it would be beneficial to time the spark a bit later for that. The SoftStart module must do that. An agent in CA for that module told me that it was no use on these older ignition units - which doesn't make sense to me. Has anyone who might be still be following this thread actually looked at the timing on these older 912UL engines with the modules inside an Interference Supression Box? If all the SoftStart does is simply delay the two timing pulses in one circuit, then there is no obvious reason why it should not work.
Yes, I know we have drifted away from solving a slightly excessive mag drop problem, but then that's the beauty of a forum like this and maybe why they are called "threads". All hail and thanks to Ian the webmaster.
Carl
-
Roger et al:
Well, I thought it was time for me to butt out, but I can't let Roger's brief report on the "Silent Hektic" go without comment. It's the "takes 10 amps" that has stirred me up. As an old "semi-electronic wierdo", I have to comment that if a system takes 10 amps (i.e. 120 VA) , then it is almost certainly supplying the power for the primary ignition. That's not necessary to provide a smooth advance - retard timing system. For the Rotax 912 /Ducati system, you can let the magneto continue to provide the primary power and provide the timing control independently - as the present Ducati system now does - except that that damn part is sealed and buried in the units. In principle, you simply (?) delay the triggering pulses by an appropriate amount dependent on the rpm. According to the manual, the present system does that now in two crude steps - 6 deg BTDC for starting and 26 deg BTDC for rpm > about 600-900. One reason the engine may run very rough below 900 rpm is that the timing will chatter between the two. (I thought "piston slap" was the stated reason behind having to keep rpm > 1400 on the 912 UL - I don't fully understand that - why is that worse at low rpm?). In any case, the triggering of the spark is done by triggering a silicon-controlled rectifier (SCR) and that doesn't take much current. Takes more power at high revs because it has to trigger more often, but I can't see needing anything like 5 amps (!!) per circuit. Gate currents for SCRs may be up to 100 ma (I think) , but that is on for only a small duty cycle, say 2 X 5% for one ignition unit or about 10 ma average. (I could be a long way out, because I have no idea what Ducati actually have in their "timing control circuit" within the ignition module and I've never actually used an SCR). The fact is that SCR's are pulse amplifying devices and the power going into the whole modules for sparking will be less than, say 100W, and so only a few watts at most should be needed for triggering. My guess is that the two triggering circuits per module would need less than 200 ma. (yes, I know I don't actually "know"!).
Integrated circuits have progressed since the Rotax/Ducati systems first came on the market. Conceptually, you could now measure the rpm with a cheap microprocessor drawing virtually no current and use that to control a (always positive) delay on the triggering pulse you send to the SCR.
In practice, I would not want to replace my Ducati modules and so, like the "SoftStart" module, I would only want maybe an additional delay to the triggering to make for a "softer" start. You don't need a microprocessor for that - just some simple fixed delay. You can't generate a true negative delay to advance the spark for high revs; however, with a microprocessor, come to think of it, as the whole thing is cyclic, if you measured the rpm, you could delay the triggering by a whole 360 deg (crankshaft) LESS however much you wanted to advance the spark! Hmm, that would work. Then you could produce a nice timing curve as a smooth function of rpm. That would be a cool add-on! You saw that here, dear readers! (If I've thought of it, it is probably very old hat and used in cars already).
Rergards
Carl
-
Roger: no worries. I too have had a number of Beetles thru my life, first one being a 1958 1100. I think it was the first model with the one-piece big rear window. In 1959 my mother also bought an 1100 and I recall her being upset that the dealer didn't tell her about the 1200 that came out a month or so later! I still have that car, sitting in the back yard and simply needing some TLC and a paint job. In about '94 I had the engine thoroughly rebuilt by a specialist VW mechanic who had bought up all locally available 1100 cc spares and had them tucked under his caravan! Taught my daughter to drive in that car and since then, it's been resting - except for an occasional engine start to blow out the cobwebs. So the engine only has about five hours on it! I was driving a 1972 model until a few years back, until the rust beat me and a great 1973 restored model came my way courtesy my ex-wife. That's what I now drive - if only the Skyfox/Rotax would let me be, I should get the 1959 VW on the road. What I love about them, is that if they do stop, I can generally get them going again. Look under the hood of a modern car, and I don't know what many of the parts are or do.
Now, to make this relevant to flying, I will note that the steel exhaust tube that my old mechanic-friend had so much trouble locating in Tasmania for the 1100 engine - and could only buy a length such that I had a generous surplus to my needs - turns out to be the very tube I need for the exhaust of the Rotax 912 UL!
I now note that the darkening on my HT cables for about 1 - 1.5 cm just inside the box lid before they hide inside a rubber tube is evident on all 8 cables and suggests HT shorting to the lid, which is closer than the edge of the box/clamp. This would explain similar (mis)behaviour on both ignition circuits. I'm pretty sure that's the smoking gun, but the proof of the pudding will be in the eating. When I have confirmed that the new HT cable has fixed my ignition problems and tested whether or not the shielding makes any difference to radio noise on my installation, I'll get back to you. I'll also ask our kind webmaster to pass on my email address to you.
Thanks for the convers.
Carl
-
Roger:
Not as sophisticated as the old VW beetle that I drive! I have a mechanical (centrifugal) advance distributer for mine that works a treat. Also, many is the time that I've wished my Rotax would start with the same reliability and ease that the VW does! Being an old "wierdo" myself, I have designed (but not yet built) a substitute power source for one ignition module just for starting - runs off the 12V battery. Not too difficult - my ambition is to be able to hand start the ba*****d.
Cheers
Carl
-
Roger:
I suspect this is the case, but I have not tried it. Could you tell me if this opinion is based on a test - or whether your present leads are unshielded and, if so, about how long are they. Mine are all around 1.0 m. You would have to turn the squelch down or off on the radio to get a valid comparison. One thing I am pretty sure about, the 5mm diam inside the shield of the old blue Rotax leads is insufficient for safe insulation of HT as the leads age. The older 912 system had the modules, coils and connections packed inside an Al box and the HT lead shields were clamped to the box at the entry point - which was as far as the shield braid went. I note that on all my leads there is dark discoloration for about 1 cm plus just inside that clamping point and before the leads go inside another protective rubber tube. I have a suspicion that this darking is due to discharge through the translucent insulation, which is less than 2mm thick. Not sure, but no other explanation springs to mind. I'll cut one soon and see if the discoloration extends through the insulation.Hi,In my opinion the HT leads do not have to be shielded at all!IceBob made a good point about looking at the unit running when it's reasonably dark. If it is sparking where it shouldn't, it should show up. I should have taken the cover off my "Interference Suppression Box" and taken a look.
One test I did do, after a lot of thought, is crank the engine over with one circuit off and, for the "on circuit", one pair of plugs connected in the open air and one plug connected (in the open) and its mate disconnected. I know some will say that's a no-no, but I do not think it likely to damage the ignition module at cranking rpm of 300. If anything is at risk, I would say it is the coil with a disconnected plug. The HT voltage wants to discharge somewhere and hopefully, that's not back through the insulation in the coil to the primary or ground. If that happened, I think Rotax would be regularly replacing a large number of dead coils around the world and I don't think that has happened. Anyway, in this case the plug with the other end of the coil disconnected from its plug went on sparking just as though there were two plugs on the coil. This was definitive in my view - there had to be leakage for the the one plug to spark. One plug on its own should not spark. I only wish I had taken the lid off my anti-interference box to observe where that might have been.
Re the carbie issue - I agree - Rotax's statement is a bit of a mystery. One way to test it is to have one deliberately maladjusted carbie and see if it effects the relative rpm drop. Not on my list of priorities.
Go back out in the sun and join your wife! I don't think you have a serious problem either. My engine, when it did occasionally start and let me fly, ran beautifully with full normal power - no missing at full rpm. Once it's going, there seems ignition power to spare - even apparently with severe HT leakage.
Carl
-
Roger:
as to the question about carbs - surely it depends on how the plugs are connected to the ignition units. Don't carbies tend to feed each side of an engine - that would be why, if they are not properly synchronised, the engine runs rough? Now, on my 912, as detailed in my earlier reply, each ignition unit feeds two plugs on each side of the engine (i.e. 4 plugs). So a maladjusted carbie should, to first approximation, effect rpm on both ignition circuits equally. Don't know for sure, haven't experienced it, but that's what I would expect. (Often wrong, though!)
Carl
-
Roger:
Tenerife eh! I'm real sorry for you! I'm right in the middle of changing my HT leads now, which I had put off doing for far too long. I had other problems for the best part of two years (no wings on the a/c!) that took priority. Then I did some tests that suggested (falsely, I believe) that the plugs were firing OK under compression. The real test is how the engine runs - or doesn't run! Don't know what the C2K is fitted with, but my Rotax 912 UL had HT leads (probably even older than my engine - viz. about 19 years) that B. Rotax supplied with the 912. These are the blue shielded leads. Note the shielded bit. Under the braid, the leads are only 5 mm in diam. I don't think that's enough insulation for a long life. Talked to Wal at Bert Flood's a few days ago. He doesn't like those leads much either. He suggested I make up my own using 7mm (black) leads. Slight problem is that, if you can buy the older 7mm HT cable (you can, with some difficulty) it is unshielded. How important the shielding is in keeping radio noise tolerable, I'm not sure, because I haven't tried. Rotax seem to have dropped the shieding on their later installations, so maybe it's not really necessary if the ignition unit is mounted on the engine and the leads are short. Hey, maybe that's why Rotax went to engine-mounted ignition units? I'm shielding my HT cables with a braid sheath that you can buy (GA use it) by the metre. I've looked on the net and cannot find any HT cable that is both shielded (with a grounded sheath) and at least 7mm inside that sheath. "Magnecor" cable seems the most sophisticated noise reduction lead, but the leads have to be made up for you and fitting the ends to the tapered screw ends of both the coils and caps might not be practicable. RF noise suppression is not just about hiding the radiating leads under a shield - the braid sheaths also serve as distributed capacitance which, coupled with the 5K resistors in the caps, form some sort of R-C circuit to dissipate the RF. Because of the greater diameter, shielded 7mm leads will have less capacitance than 5mm leads, but I don't expect the effect to be too significant. Magnecor and other leads work with a different sort of distributed capacitance. If your present installation has unshielded leads, then you don't have a problem with HT cable - if they are, I suggest you contact me next month and I'll tell you (a) whether I have solved my problems or I'm full of hot air and (b) how to make up your own shielded 7mm HT cables.
Carl
-
Roger:
I'm unsure if you have a 912 80 hp or 912S, but I assume ignition layout is similar. On my older 912UL, ignition circuit A goes to plugs (1T, 2T) and (3B, 4B) (one pair per coil) and circuit B goes to (1B, 2B) and (3T, 4T). So, theoretically, all being equal, each circuit supplies a symmetrical set of plugs and should produce same rpm. I assume all your plugs are gapped the same? Does the engine start with the same facility on each circuit separately? On my 912 the power input to the ignition modules flattens off (at about 35V equivalent AC on a multimeter) at around 3000 rpm. If previous answers were "yes", then I would put a multimeter (AC volts) on each of the ignition circuit power input lines (red wires) with the engine running and see if the readings were similar from starting rpm to about 4000 rpm. The mag drop indicates that the plugs on one circuit are not getting the same power as on the other - in your case above 3000 rpm. That's either due to input to the modules or within the modules (expensive) - or maybe one coil has a problem - unlikely but possible - or there is leakage on one or more HT leads - more likely. All this assumes your spark plugs are really identical. However, if this problem has been progressive over time and apparent through changes of plugs and caps, then it would appear to rule out the plugs. Leakage in or around the HT leads is the most likely cause, in my opinion.
Carl
-
G'day JG3 and other contributers:
I have read this thread with great interest. I have a vaguely similar problem with my Skyfox CA-22 912 UL in that, after a rest of 15 months, I cannot get the 912 started. After considerable messing about, problem seems to be that the spark from both IGN modules is very weak. This particular problem has plagued me for several years - very difficult starting that has got slowly worse with time. Today I turned the engine over with no compression in any cylinder, but each HT lead going to a properly connected plug externally and producing a very weak spark. All four HT coil secondary windings measure similarly on a DC meter- about 8 K ohms DC, as best I recall - could be more or less, but all about the same and no obvious leakage to ground on ohms X 1K. Not sure of the turning rpm, but more than sufficient from past experience - will measure it in a few days. I note the manual re the "Interference Suppression Box" containing the two IGN circuits says (Sect. 6.18.5 in my 1992 version) "Apply Lithium grease to all cable connections to prevent leakage currents". Like others, I have occasionally been guilty of turning the engine over without every spark plug properly connected. However, if this was the problem, I would expect to have a problem on Circuit A 1T and 2T (usually pull 1T or 2T plug to check spark), rather than the whole shooting match. Maybe excess leakage fits the bill better? Have other owners pulled the leads off and used a Lithium grease to inhibit leakage? What's the latest on your problems, JG3?
Also, I don't understand the "dead" or "lazy" stator description - a stator has the 10 coils mounted, but is not magnetized itself - is that not so, or do I have it wrong? I thought the magneto ring had the magnetized bits?
Skyfox flight manuals
in Skyfox/Gazelle
Posted