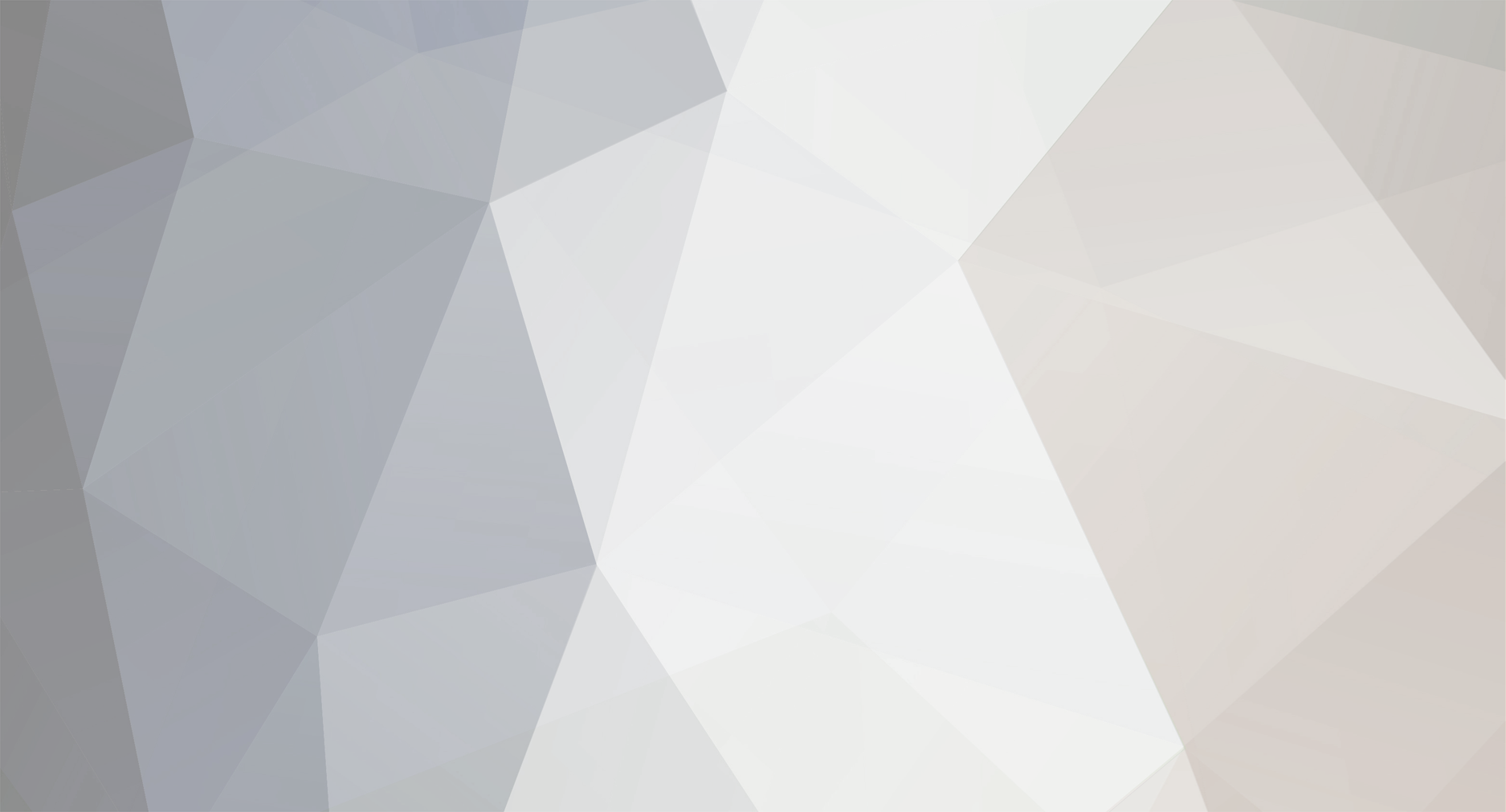
Bob Llewellyn
-
Posts
558 -
Joined
-
Last visited
-
Days Won
5
Content Type
Profiles
Forums
Gallery
Downloads
Blogs
Events
Store
Aircraft
Resources
Tutorials
Articles
Classifieds
Movies
Books
Community Map
Quizzes
Posts posted by Bob Llewellyn
-
-
Have a look at an Auster installation, or the Royal Aeronautical Establishment tests of 1920; or better, the NACA Report on baffles for a Continental C-85. The Jab baffles are pretty lame, sorry guys...Ive installed gull wing deflectors under cylinders, wasnt easy but achievable. Didnt do anything dramatic but did assist even cht out along with Jabiru usa tech doc on cooling ducts, temps between 90 to 120 most of the time, not a big difference in cht no matter what the duty or outside temps actually nowIts a solid lifter with fine heads, cht probes down in hole.-
1
-
-
Sorry to be a gloomy bastard... I've worked up a design like that, but (by standard analysis) the mongrel is unstable in pitch in the balked landing case (or hauling it off the ground early), because of the high prop efficiency of the 503 (geared)... works fine with a DD VW, but the power to weight goes down the sink. Technically, it's an ASTM 2205 (LSA) non-compliance, but I suppose you could go experimental and be carefulI cant find one of my good drawings to show, but I will try to explain;[ATTACH=full]17502[/ATTACH]This is a project I have on hold, that was to use a R503 mounted upright with the gearbox also upright, and having cheek cowls like a flat motor.
On one side is the carbi's and filter(s), on the other side is the exhaust.
These items are more or less in line with the prop shaft so the effect is quite neat.
More of this project at; https://plus.google.com/photos/113292981019876413104/albums/5194978509871592929?banner=pwa
I'll get back to it one day.
Arthur.
-
1
-
-
This bloke did a lollydrop at the local school or fairground, then picked up a near relative for a private flight, then appears to have hit a horizontal shed vortex off the range. I am reluctant to go into more details here, but the personal tragedies were compound.maybe not the same prang. My mate came unstuck during a lollydrop. That not the one?-
1
-
-
Yes, several times over - extremely unusual atmospheric conditions, truly tragic circumstances.hmm..Sounds like the same prang... Such a loss too..This is perhaps not the appropriate time to get on my engineering horse, but that crash was partly caused by the combined effect of two regulations, and SHOULD NOT HAVE BEEN POSSIBLE if the CAR 35 engineers consulted on CAO 101:55 had been listened to. Bah, Humbug.
-
I inspected the wreckage of the 'fox that shed a wing up North, not very nice. The atmosphere is very powerful.yea Bob. The gazelle was/ is a true lady. Lost a good mate in one a few years ago due to wing departure,:( By all accounts the aeropower is a good performer. Although the numbers arent there yet. Not here anyway. Ill be testing a homebuilt with one it it soon so Ill have a better idea. Look good on paper though.As the ballast for the MTOW climb tests of the original Calair skyfox, I don't remember the Aeropower as exactly a stellar performer, but it was both adequate and reliable. Like the Jab, a smaller prop than the 912... I'm not sure how many 'foxes retain them.
-
Yes, Tony was a loss. He trained me to Pilot Certificate stage, and gave one of my L2 recommendations when we upgraded the front spar / boom bracket on -381 (his training aircraft).Fair dinkum? Good stuff mate. great to have you on the forum mate. We all miss Tony.. he was a legend around these parts.. -
Ahem. Due to CASA's changing position on Authorised Persons, I'm not playing in GA at present. Due to personal economics, I've been hiding under a rock for a while; but I am the principal of the Thruster Operator's Support Group, and have been doing some work on LSA Certification issues here and there...Nice to see qualified responses from members with 'real' background. Are you still in the game?-
2
-
-
Gazzle's not a bad bird, but that wing!!! (!!!!)! Pity the price went up when the wing section entered the 20th century... Hey, we're meant to be talking about Jabs; how do you reckon a Jab 2200 would compare with an Aeropower?yea, right. My old memory not too shabby then. :) Seen the name in many many gazelle log books. -
Dad. I was working with him at the time, we wrote 60 or 80 EOs for Skyfox-y ailerons... turned into a package of paired EOs, one for the root drive production variability (had slim margins), and one for re-mass-balancing.Yes, im a little familiar with some of those docs, and quite familiar with others..I agree, ZZZZZZZZZZ time. But no mattrer what rule or reg you find, theres always 3 or 4 somewhere else that add ambuguity to the one you just spent 1/2 an hour looking up!!...Your last name rings a bell. Did you have the gazelle aileron mod authority? -
It's a few thousand words of mindbogglingly boring text, but if you read the entire list, you'll be one-up on the poor overworked crew at CASA... they just get force-fed the latest policy directives... it cures insomnia too, I personally garauntee!I like that Bob. Just pop out and read ANA1920 etc.. Just a few pages of light reading for us. :)-
1
-
-
For what it's worth - (1) the HS is too small for stability. Yes, the pusher prop has a small stabilising effect with power on, but it doesn't have much arm in that position; and yes, gapless controls are 5~15% more efficient than a 0.5% chord unsealed gap; but control efficiency contributes naff all to stability.G'day guys. You know that I love to dream and design new planes with the hope that one day I'll actually be able to build. Well, I've returned to my first off ever design and updated it. What do you think.Introducing the DeMansfield Bolt Mk ?[ATTACH]27027[/ATTACH] [ATTACH]27028[/ATTACH] [ATTACH]27029[/ATTACH] [ATTACH]27030[/ATTACH] [ATTACH]27031[/ATTACH]
Originally, this was to be a mid to shoulder wing but I've had to go lower to fit the wings. It will have a tricycle under carriage with a retractable nose wheel and differential brakes for ground steering. Probably be powered by a Jabiru for lightness, driving a specially made prop, around the tail boom. There's no contact between the prop and the boom. All control surfaces will be fake 'morphing' (shape changing) and not hinged as per normal. It will have extending and drooping leading edges, extending and 2 stag flaps, and hopefully, (nearly)seamless ailerons, elevators and rudder. Most of it is designed in my mind having spent countless hours working and reworking the details. Yes I know, morphing surfaces will be heavier and more complex, but due to their increased efficiency (no gaps), will be more efficient and therefore can be smaller. The boom and tail-assembly are removed in one piece and each wing is removable for towing purposes. It should all fit into a double horse box or similar trailer.
This is early in it's development and there's a lot of work still to do.
(2) the HS is either in the wrong place, or needs to be MUCH BIGGER, for power-off stability - on final at flight idle, the propellor stagnant wake will be dragged down by the wing wake, completely masking the tail surfaces. Look at the size of the Seabird Seeker tailfeathers, and study one in the flesh - particularly the directional control system. (3) the fuselage bum just fwd of the prop will separate, causing turbulent flow into the prop, strong vibrations, prop fatigue, and extra drag - see Cessna 336 / 337. (4) The rear fuselage boom will either weigh a ton, or have a very short life - the empennage is being flogged by the shed vortex system from the propellor (if a wing is interposed between the prop & empennage, it acts as a flow straightener and turbulence damper to a great degree); and the full up-elevator at Va, at full power (ie extra dynamic pressure from the slipstream) case will superimposed rather substantial quasi-static loads onto the prop-induced vibrations. (5) The boom joint will be a nightmare - as discussed, the boom base is about the most highly stressed and fatigue-loaded item in the structure, exactly the wrong place to put the stress concentrations of a joint (particularly non-permanent). (6) the stall handling will be, er, challenging - normally pre-stall buffet is produced by premature separation in the wingroot-fuselage junctions (low wing), but you have a propellor vacuuming that nasty separation away; so the initial stall will be one wing, outboard of the prop, generating a healthy wing drop.
Have a close look at the Taylor Mini-Imp / Micro-Imp; that layout raises none of the above issues, which is partly why Molt chose it.
By the way, how do you mass balance "morphing" controls? If it's doable, a two-stage morph, or variable camber surface, would definitely have applications...
Apart from that, looks nice. Oh, what kind of energy absorbtion in the U/C?
-
Nice idea. RAAus never used to have any enforcment authority, bar suspending maintenance Authorities and Pilot's Certificates. Suspending the Jabiru engineering team's pilot license unless thay upgrade their LSA - self complianced - product would give any magistrate a good laugh. Now, part of the current CASA audit involves a reconsideration of how CASA supports its responsibilities towards RAAus aircraft; so the current official position on RAAus' authority to bully manufacturers is in a state of flux. If you want more background data, read the ICAO Airworthiness Manual; the Morris Report; HORSCOTTS; the Air Navigation Act 1920; the Air Navigation Regulations; the Civil Aviation Act 1988; ANO 95:10; ANO 95:25; CAO 95:55; the Civil Aviation Regulations 1988 et seq; the Civil Aviation Safety Regulations (such as they are); AMROBA's submissions to the current Minister for Aviation; and the upcoming White Paper on Aviation.Its unreasonable to expect everyone to call Darren or for Darren to answer all those calls . So if you have some information that warrants a statement like this, why not put the information here for all to see.Or, for the cutting edge info on the mystery, 'phone the man on the cutting edge - Darren. Alternately, let the man work, and expect much clarification within the next 6 months.
-
1
-
2
-
-
Anout 10-12 years ago, the FAA said "we do not ensure airworthiness. We ensure that procedures have been followed, that have been shown to deliver airworthiness"... CASA is trying to follow this precept. Now, merely improving the airworthiness of your aircraft is irrelevant to them; if you don't use their specified procedures, you are evil and BAD!!! (nothing personal, just so you knowYep I do have a 19 plane. But its really hard for me to accept that improving the cooling could be illegal.I have all 4 CHT's being measured and I've dropped them 15 degrees or so. Why on earth would they want to stop you doing this?-
1
-
-
RD 250 with 10mm overbore, burned itself in Brisbane after i stuck a 400 donk in it; GS 450, pistons burned out by crap fuel outside Sydney, GSX 400, the bike tried to hump a semi trailer; SV 650, I was the 8th? of 22 prangs that day on the crap mastic surface in Canungra; GpZ 900R project awaiting my attention... for about ten years now...
-
My main gripe is that fatigue is an unread, burned, and buried book to all the blade designs that I know of. Many have an arbitrary "service life", but on inspection are full of lousy structural design - e.g. "fail deadly" philosophy, unnecessary stress raisers, poor choice or juxtaposition of materials; and the class operational limitations do nothing to promote ongoing airworthiness - rather, they seem designed to promote darwinian selection.Gyro's handle turbulence well but use a lot of fuel if you want to go somewhere. Some have design faults that rule them out. Note this post sat for a week so is a bit out of date.NevThe other point on modern gyrocopters, is that almost all are based on Benson's entry into the US search for an airforce pilot retrieval flying vehicle (that would fit in a Phantom glovebox, and allow downed pilots to fly out to the Tonkin Gulf). It was meant for a service life of 30 minutes; to be flown by a highly trained pilot; and to not land. True to this heritage, and quite unlike Cierva's later creations, gyros cannot land or takeoff vertically; have very limited speed ranges; and offer naff all pilot protection in event of a prang.
I'd be willing to give a Pitcairn a long, hard look...
-
My understanding is that it's all about the interatomic bonds - no, stay with me - "natural" and "synthetic" oils are all based on carbon-carbon structures, with hydrogen around the edges. The three basic stable carbon, um, "backbone" structures are called Paraffinic, Aromatic, and Napthenic. Crude oils contain different blends of these, and some crudes take longer to disintegrate than others - e.g. Pennsylvanian oil stocks were aromatic/napthene rich, and so both stayed slimier for longer as oils, and made higher octane petrols, than early Russian stocks.Guys, VERY old thread, most admitted its a poor way to gather data, firstly small sample size then differing opinions on what is considered standard operational maintenance or an engine failure.Theres some more current threads going giving Jabiru a hard time over engine problems - maybe with justification.Re oils, getting off topic and as many are run in LSA which cant vary from Jabiru information.
There is work being done to use other Aeroshell aviation oil in Jabiru engines with good results, engines have run big hours on this oil and will soon be torn down and inspected before recommendation changes. Not all good for engines with 100+ hrs. on them.
Interested in your ideas on Sport Plus from Aeroshell Bob
However, all natural oils are blends, so some proportion of them (as lubrication oils) breaks down rapidly, and some proportion lasts well. They also have a high vapour pressure, which is not favourable from a foaming aspect.
Synthetic oils contain a much more limited range of constituents - although the forms they do contain are also found in nature - which gives an aging curve more like a plateau and cliff, than a bumpy final descent. In fact, if the steel components are cool enough, synthetics can last a remarkably long time. They also have lower vapour pressures than natural oils.
So much for carbon. Silicon acts like carbon (in a chemical and micro-structural sense), but it's bond strength is higher. So, silicon-backbone oils last longer st the same temps, or the same time at higher temps; and, being synthesised, can offer the same shape aging curve as synthetic carbon-based oils, to a higher temperature for a longer time. The vapour pressure is also quite low (vapour pressure is not the only determinate of foaming behaviour, but it's the basic one).
Shell say "AeroShell Oil Sport Plus 4 is made up of a blend incorporating synthetic technology and high performance additives to help provide long lasting protection.". This says to me, that Aeroshell Sport is a synthetic carbon-based stock, probably with added napthenes separated from natural oils, and some added methyl silicon. It is therefore a bit cheaper to make than straight methyl silicon, does not last as long as straight methyl silicon, and has a higher vapour pressure than methyl silicon. The fact that Shell see fit to advertise a detergent ingredient to clean up carbon deposits shows clearly that the oil is designed to break down; and begs the question, what are the side effects of the disintegrating "detergent action" molecules as the oil ages?
Conclusion: Shell have given up, and added a bit of extra methyl silicon to a good grade of car oil, because cars aren't run at WOT / full power for 5 minutes at a time, every drive. It's probably better than the competition, but it's in a lower class - i.e. carbon based - than straight methyl silicon.
CAVEAT: I do not know that AMSOIL is straight methyl silicon, but I DO know that the AMSOIL 2-stroke product, run in Rotax 501/503/505s back in the early 80s, resulted in carbon-free piston rings, very pale ash on the piston crown and head, and a film of oil - NOT black carbon - in the exhaust ports.
If I find a vendor of an oil that performs as methyl silicon did under NACA test, and costs less than a gonad, I'll tell the world. In the meantime, any oil with an HP additive - for gearboxes - almost certainly has methyl silicon in it, and is therefore a better oil than one without methyl silicon. (Note that gear oils without HP additives, may be assumed to NOT have methyl silicon).
-
5
-
-
I wouldn't get into a gyro for less money than I could retire on, unless designed by me
... or a recently manufactured Cierva, which ain't likely. Anyway, the BD-5J Bond used is pretty compact when folded...
Thanks Nev & rgmwa, that sounds depressingly realistic - or realistically depressing? But surely you have a wish list...?
-
Welcome Bob,Good luck with TOSG, I will be a part of it.... Wait a minute, I already am!
Pud
yes indeed... oh, the secretary got sidetracked with creating some new letterheaded paper, but I'll be sending receipts as soon as I kick myself
-
Sorry, I'm writing like it's a conversation. Ok - as oils get hotter, they get runnier. Methyl Silicone stays unrunny to higher temperatures than parafin, or "mineral", oils. So, all other things being equal, in a hot location the Methyl Silicone will be slimier. But all things ain't equal! Under high pressures - like a rocker driving a valve - the local viscosity of any oil gets much higher; Methyl Silicone has ~1.6 times the pressure viscosity coefficient of parafin oils. So, under pressure, Methyl Silicone will be slimier.I have read this post a few times but cannot make sense of it. Obviously I have had a mini-stroke and need to have a Bex and a lie down. Does it read 'right' to others out there? Will check in tomorrow for responses and abuse.It follows that, in a hot cylinder head, Methyl Silicone oil will have far better "lubricity" (sliminess) than oil squeezed out of the ground & refined - i.e. paraffinic oils.
Furthermore, when a parafin oil gets too hot, esp in the presence of iron (or steel), it breaks down, releasing carbon particles. These are the mongrels that cause piston ring sticking, and also cause incomplete valve closure as the valve stem tends to bind in the guide (generally also with the formation of lacquers from the disintegrating oil molecules).
Methyl Silicones do not start this until considerably hotter than their parafin equivalents.
Now, to my eye there is a considerable body of evidence that the valves themselves are generally of acceptable quality - they don't fall to pieces too often - and the valve springs don't turn to melted cheese. This only leaves valve stem binding due to lubricant failure - probably only intermittent, but it starts the valve seats burning - as the probable culprit.
As none of the materials used in the jab engines is, in fact, soluble in Methyl Silicone, I cannot see any credible argument against using a better lubricant, aside from that it would probably irritate Rod Stiff.
-
2
-
2
-
-
They ain't castings, they're machined from solid wrought bar/plate al...What on Erath does that mean? -
100LL is Iso-Octane (tri-methyl pentane, I forget the locations) with TEL added; ULP is parafins plus aromatics plus - for the high "octane" stuff - some unstable organo-metallic; the two would have fairly different time-temperature diagrams when burning, and one would reasonably expect the more complex blend to burn in several stages (even though it's all over in a few milliseconds, the rate of pressure rise is crucial to "smoothness', and has a bit to do with achieved TBO...foxy said: Ive found that she ran a little smoother when running on 98 octane fuel than when she was run on unleaded.That's in line with expectations. Lead is the best lubricant but it also fouls engines. -
Since the Jab heads were billet, last time I lookedI would further check the valves and castings of the cyl head by blocking off the open end with a piece of flat metal and rubber seal. Fit an air hose connection through the metal, turn on that air pressure full blast and listen for leaking air anywhere. Faint leaking out the intake and exhaust ports is ok, but elsewhere is cracked casting.-
1
-
-
Yes. Check out the NACA report. Jabirus do not have a massive habit of dropping valve heads, or valve springs going soggy, and the overpumping of the hydraulic lifters should have been solved for years (some solid lifter engines get valve leaks too). Ergo, the head lubricant is getting too hot / thin. The extra 50C or so the Methyl Silicon gives over any parafin, together with the reduced rate of 'cracking" of the oil, and the increased high-temp viscosity, all should tip the balance. Jabiru is not a research organisation, and their engine is not rocket surgery; and better lubrication (in both a hydrodynamic and a chemical stability sense) doesn't hurt an Otto-cycle engine.So Bob, no disrespect intended here, would you run that oil in a Jabiru engine? That oil get's no mention in their documents and manuals as far as I can tell. If you ran that oil and the engine blew up, who's fault would it be? (So far the only info using Google is from China!)ps I'd want to know a little more about the manufacturer, if the source was Chinese (have met some QC issues with aviation products from Chinese companies...)
-
Pulling a head is a "top overhaul", and Lyconental do not consider it to be a major overhaul - eg tops at 1000 hrs, 2000 hr TBO. Personally, after reading NACA technical Note 4161, I'd run AMSOIL (Alkyl Modified Silicone OIL) in any aircraft engine I could; massively better lubricant at higher temps and operating pressures.I'm looking forward to seeing how things pan out when there are a lot more replies.It looks like ruffasguts is getting quite good service out of them, but surely it shouldn't be necessary to pull the heads off every 100hrs to keep the things purring. I thought it was mainly hellies that had high maintenance?Good on him if he's got those hours out of them, but surely if the manufacturer claims 1000hrs between overhauls, one should not be expected to give a head-*** every 100hrs.
Yenns reply was interesting, in that he appears to have had few problems until he was unable to get avgas, maybe they run cooler in the head area with that fuel, and that gives the valves and rings an easier life.?
I sometimes wonder whether an additive like Redex upper cylinder lubricant in the fuel would be an advantage, and keep things a bit better lubricated, reducing friction heat?
Jabiru engine life times
in AUS/NZ General Discussion
Posted