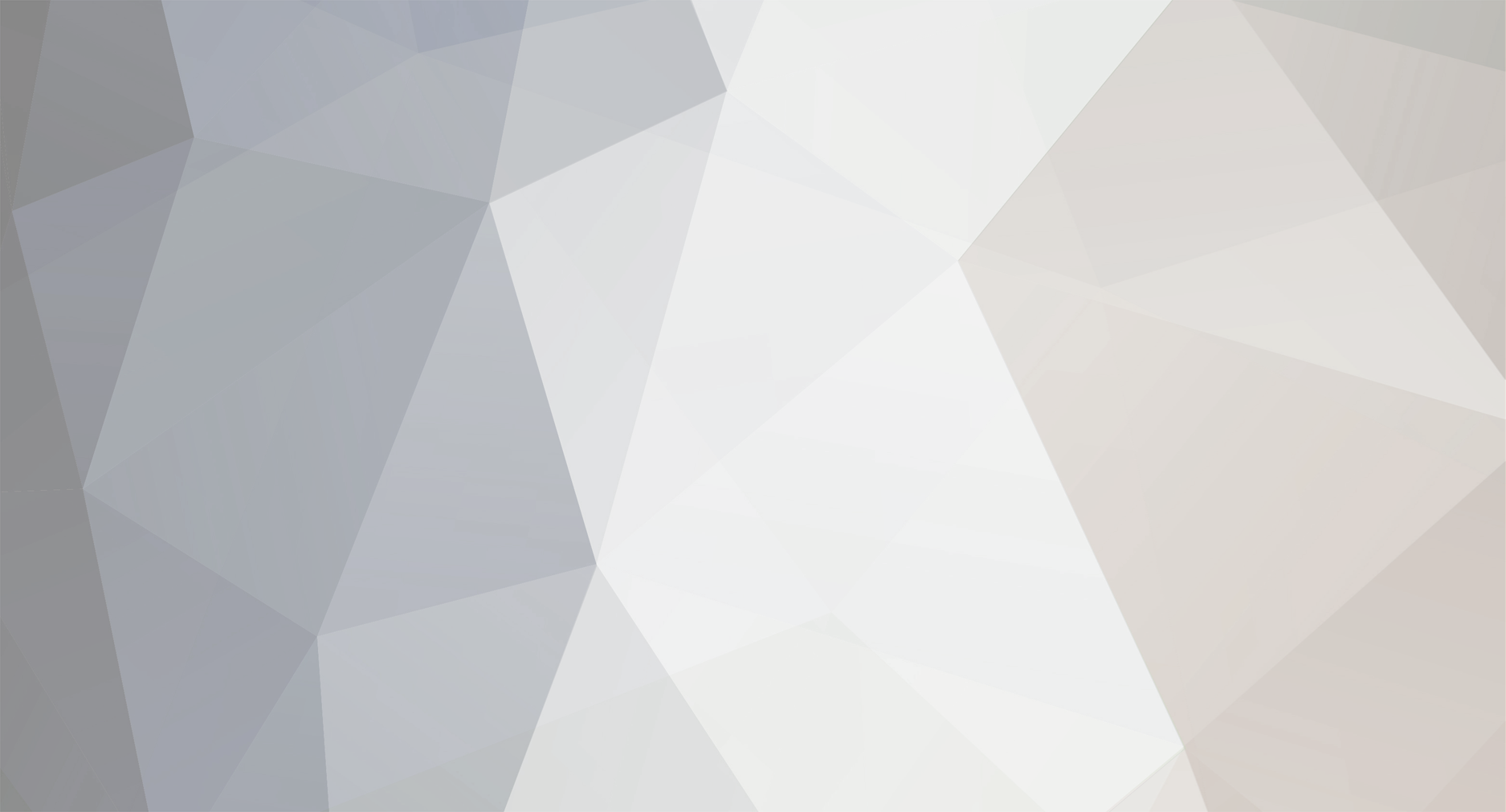
Ian
-
Posts
431 -
Joined
-
Last visited
-
Days Won
8
Content Type
Profiles
Forums
Gallery
Downloads
Blogs
Events
Store
Aircraft
Resources
Tutorials
Articles
Classifieds
Movies
Books
Community Map
Quizzes
Posts posted by Ian
-
-
This file didn't appear to attach however it shows a mechanism to reduce the degree of delamination which epoxy often suffers. Hydroxymethylated_resorcinol_coupling_agent_for_en.pdfHydroxymethylated_resorcinol_coupling_agent_for_en.pdf
-
Sorry for the long post but while you may have studied forestry you didn't study engineering. 😉
The key here is repeatable research rather than belief and proclamations from on high. Epoxy glues are fantastic however they shouldn't be used blindly and their limitations should be well understood, especially when using them in things which can cause you harm.
I'm not saying that resorcinol is an easy glue to use, it's harder than epoxy to use however used correctly creates a better bond.
1 hour ago, Markdun said:I definitely don’t agree with the view that resorcinol is a better glue than epoxy; but a lot depends on the epoxy- there are hundreds of different sorts of epoxy,
I know that there are a lot of opinions in this area however the rigorous studies all point to poor bonding qualities with timber when exposed to moisture. While there are lots of different epoxy formulations chemically they're very similar and the bonding results are the same. Happy for you to demonstrate the error of my ways however I haven't come across any testing programs where epoxy bonds in wood exposed to testing have survived standard de-lamination testing methodologies except where a primer such as resorcinol is used on the wood surface.
Epoxy is gap filling, easy to use and readily available. You just need to be very careful when using it as a bonding agent for timber, especially in harsh environmental conditions.
Attached is the appendix of Classic Boat which provides a professional boat builders opinion, also attached another study which tested both wet and dry wood failure on four different glue types including epoxy. In the conclusion epoxy actually bond more effectively to acetylated wood, but not unmodified wood.
QuoteOn the other hand, only the RF gave good wet bonds bonds to the acetylated wood. Modification to make the wood less polar improved the wet performance of the epoxy adhesive.
Starts with the following quote which is relevant for anyone considering using epoxy for externally exposed structural purposes.
QuoteEpoxy adhesives can develop bonds to wood that are as strong as the wood itself, but only if the bonds remain dry. Once exposed to repeated water soaking and severe stresses from drying, epoxy bonds delaminate and fail to meet requirements for structural wood adhesives intended for exterior exposure.
3 hours ago, Markdun said:It’s incorrect that resorcinol is used in the manufacture of plywood, marine or otherwise.
Resorcinol Formaldehyde can be set at room temperature or can be heat set. Phenol Formaldehyde PF is a very similar adhesive to RF and is often mixed with RF to create RPF adhesives which can also set at room temperature. Australian Standards specifies Type A adhesives for marine ply, both RF and PF are classed as Type A. RF is more reactive than PF and in some cases will bond with timbers more successfully than PF. The main reason to use PF rather than RF is price. RF is more expensive hence its limited use in this role. Actually RF is classed as a phenolic compound, it just has more reactive groups enabling lower temperature reactions.
3 hours ago, Markdun said:It’s not worth ply manufacturers to stuff around changing glues.... they are nearly all the same. The difference between marine ply and others are that in marine ply the veneers are the same thickness and the sheet will bend the same when stressed lengthways or sideways. ‘Structural grades’ may have lower quality veneers and/or achieve the same bending length vs widthways by having inner veneers thicker.
The main reason for changing glues is price and ease of use. This page give a good overview
https://www.matildaveneer.com.au/stuck-on-you-plywood-glue-bonds/
Type A (A-Bond)
This is the strongest bond and is also waterproof. It’s produced from a phenol formaldehyde resin that is set under heat and pressure. The result is a permanent bond that can be exposed to heat, cold or wet conditions for a long time without deteriorating. This glue bond is used for structural, exterior and marine plywoods.Type B (B-Bond)
Less durable than Type A, a Type B glue bond is waterproof but will deteriorate after several years being exposed continuously to weather. It is usually produced from a Melamine-urea-formaldehyde (MUF) resin. Plywood with a B-Bond is best used in situations of limited weather exposure, e.g. exterior doorskins and concrete formwork.Type C (C-Bond)
This glue bond can only withstand occasional exposure to dampness and as such is most suitable for general internal uses. It should not be used for structural applications or wet/damp areas. This glue bond is usually produced from urea formaldehyde (UF) resin.Type D (D-Bond)
Similar to Type C, Type D is also made from urea formaldehyde (UF) resin. D-Bond Plywood is best suited to internal uses where it is completely protected from wetness or dampness. It should never be used for structural applications.3 hours ago, Markdun said:Any comment about Australian timber being stronger is just coddswallop. We have over 500 species of eucalypts and other hardwoods and around 100 or so species of softwoods/conifers. The variability between species and even within species is enormous. Like epoxy, when it comes to timber its horses for courses. If one wants to generalise one could say that the softwoods/conifers (gymnosperms) have stronger wood because in general the wood cells are longer and have overlapping tapered ends (toilet paper), compared to the hardwoods (angiosperms) where the wood cells/fibres are more like cylinders (the Australian newspaper). But it ‘all depends’.
Australian structural hardwood timbers are significantly stronger on average than softwoods and hardwood species used in the northern hemisphere, using standards methods of testing strength which is measure in force per unit area. I'll list a few of the accepted timber strengths.
Grey Ironbark Modulus of Rupture 185MPa
Spotted Gum Modulus of Rupture 142MPa
Rose Gum Modulus of Rupture 119MPa
Hoop Pine MoR 90MPa
Norway Spruce MoR 63.0MPa
Sitka Spruce MoR 70.0MPa
Radiata Pine MoR 81.MPa
I could go on but you get the drift. Happy for you to add your own figure with published Module of Rupture figures.
You can also get an idea of the timber strengths from the following link which shows European glulam beam strength vs Australia standard strengths https://ash.com.au/blog/gl-au-nz-vs-europe/ . The main reason for the difference is the fundamental difference in strength of the base material, Australian hardwoods being stronger lead to significantly higher engineered wood ratings.
In fact there is growing interest internationally in using Eucalypts originally grown for pulp, for engineered wood due to its high strength. The main species grown in this manner is Eucalyptus Globulus which is also known as southern blue gum. An articles on this are below.
https://www.ncbi.nlm.nih.gov/pmc/articles/PMC7078706/
I suspect that you've become confused by the concept of strength to weight ratio which is a related concept, which is relevant to airplanes but is a derived measurement based upon strength in MPa. Aluminium is not as strong as steel as it has and ultimate tensile strength of 90MPa in the unalloyed form and up to 690 MPa with special heat treated alloys whereas special steels have a UTS of up to 2690. However on a strength for weight basis they're pretty equivalent.
But the point which is missed is that you can make a propeller from ironbark which is thinner and more efficient than one made from spruce while still retaining the strength properties in tension which is where most failures occur. Due to the increased Modulus of elasticity the propeller can also maintain greater stiffness with a thinner section. In fact based on the figures above you can have a stiffer propeller with half the thickness.
-
2
-
-
6 hours ago, Bruce Tuncks said:
Thanks Ian... You have got me wondering , all my life I reckoned that resourcinol was inferior to epoxy because of its lack of gap-filling properties, but as you say, in glued laminations, this should not be a problem.
I'd like your comments about the Australian ww2 Mosquito bombers. My understanding was that they were not built well enough to cope with non-gap-filling glues.
Epoxy was only invented after ww2 I also think.
Resorcinol penetrates and chemically bonds with the wood, this is one of the things which makes it's bond so durable. Very early Mosquito's were built with casein and later versions with urea formaldehyde. https://en.wikipedia.org/wiki/De_Havilland_Mosquito#Fuselage . Problems were found (often due to loss of aircraft) when these aircraft were deployed in tropical environments.
Urea Formaldehyde while strong is not as weatherproof as resorcinol. My understanding is that later Mosquitos and some of the Australian Mosquitos were built with resorcinol which mitigated many of these issues. Not saying that the build quality was high on the Australian planes but the glue was better.
-
I noticed a few people recommending epoxy as a lamination glue, there are better glues, epoxy has a poor record compared to other glues in relation to resisting de-lamination and glue-line failure. About all it has going for it is that its easy to use. Epoxy is good with fibreglass and carbon fibre but not wood. I'd be wary of a plane build with epoxy.
The gold standard for wood glue is resorcinol, it is the glue recommended in most plane building standards and is also in the Australian Standards for commercial exterior glumlam glues. Basically moisture penetration weakens the epoxy-wood bond permanently even after drying. Is your prop likely to ever get a stone chip and then get rained on or fly through a shower? Resorcinol is the glue used in marine ply and was also used in WW2 to fix the Mosquito delamination issues in tropical environments. One thing to note is that resorcinol doesn't have gap filling properties and requires a relatively high clamping pressure which shouldn't be a problem when making propeller glulam blanks. Some isocynanate and PU glue also have good results however results vary across manufacturers and formulations.
A lot of research has been done in this area I've attached one paper and the text from it is below. The research was looking at gluing acetylated wood, however the control was un-treated wood and the text relating to epoxy is pretty damming. An example of a primer is a resorcinol primer applied to the wood surface which chemically bonds with the wood surface and achieves a strong bond with the epoxy.
QuoteEpoxy bonds to wood are generally strong when tested in a dry condition, but they weaken drastically when subjected to water saturation and drying. If primers are used to increase adhesion, epoxy bonds can withstand
exterior environments. Poor exterior performance is probably caused by inadequate wetting and limited penetration of high molecular-weight adhesives into the wood. Epoxy-polyamide ( EP ) adhesive was diluted with 10% butyl glycidyl ether in an effort to increase its penetration, which helped somewhat. After examining failed bonds under the microscope, it was evident that the adhesive penetration was poor. Not only was there poor adhesion to the wood, as evidenced by failures in adhesion to the wood, but some cohesive failures were evident. Although the adhesive did bond well to the untreated controls, it was still negatively affected by the level of acetylation. as indicated by lowered dry shear strengths and wood failures (Table 1). Wet shear strengths were very low and wood failure was non-existent (Table 2). The lowered polarity of the acetylated wood probably contributed to the poorer wetting and penetration, hence the bond strengths, as the level of acetylation increased.
Australian woods are significantly stronger than their northern hemisphere counterparts, for example ironbark has a tensile strength about 2x that of english oak (famous for it's strength) however they are difficult to glue, however this strength provides the ability to create a thin strong prop which is appealing. Again resorcinol glue appears to be about the best adhesive in this regard according to research done by the Queensland Government which is about the only Government agency actively doing research in this area which is a pity as from an engineering perspective these timber have great structural potential.
Also if you're going to the trouble of building a propeller you can use the wonders of computer software to get an optimal design for a particular speed and generate a cad file and have a machine carve your blank. I think that I generated this using https://web.mit.edu/drela/Public/web/qprop/ but it was a while ago. Unless you have thousands of HP big paddle shaped things are far from optimal, thinner designs with an airfoil that goes towards a point will provide a significantly better outcome. Below is an airfoil generated to provide optimal thrust at about 160 knots with about 180 hp.
-
1
-
-
It is easy to see trends in small information samples. Especially when change is forced.
https://www.atsb.gov.au/publications/2018/ar-2018-058/
On top of this a number of aircraft engines are so marginal in the first place any change may push particular products over the edge.
That being said I'd personally prefer to see ethanol free mogas made available by default at airports and adapt the airframe fleet. All other options are going to be costly as fuel companies will want to both maintain margins and recoup costs of a new product in a declining market. Also in regional airports the opportunity to have infrastructure that caters to both planes and cars might ensure that the fuel at least remains fresh.
-
1
-
-
The only way to make this work is a hard drop dead date.
- Planes which can run on available fuels will transition.
- Planes which can't will sell at a discount reflecting the cost of modifications STC etc.
- Companies will develop replacement fuels as the current market will disappear.
-
2
-
9 hours ago, Old Koreelah said:
after several phases of modifying my Jodel Babe it started looking a little like his amazing AR-5
After watching his video on wheel pants I'm noting the flush sides on your wheel pants and the design of the engine cooling
-
1
-
-
I might have to buy a copy to take on my holidays as a bit of light reading.
He died a few years ago and also designed the AR-6 https://en.wikipedia.org/wiki/Arnold_AR-6
According the the video he also built the Amsoil Racer so if anyone wants to go fast efficiently he's worth paying attention to.
-
1
-
-
On 06/07/2022 at 7:36 AM, Geoff_H said:
It's just a thought, my design process has always been, "what can we do different" then suggest even stupid ideas then examine possible implementation of the stupid idea.
Good approach to see. There's far too many people who don't ask fundamental questions for fear of looking stupid. Too many times I've left meetings to have people thank me for asking what "XXXX" meant and they've been involved with the project longer.
Or possibly there's something wrong with those who actually ask questions 😉
One of the features in the video below which I found interesting was the lack of effect of a spinner on the speed of the plane. The simple high pressure zone in front of a blocking leading edge is actually a somewhat efficient shape. This makes me think that trailing mechanisms tend to be more effective.
-
2
-
1
-
-
59 minutes ago, Geoff_H said:
That's why well designed heat exchangers are contra flow. Hot flows one direction through heat exchanger, cooling fluid the reverse.
I was wondering what the efficiency gains were and wikipedia just makes thing easy. https://en.wikipedia.org/wiki/Heat_exchanger#Flow_arrangement
-
1
-
-
2 minutes ago, facthunter said:
If your motor already has cooling issues don't even consider supercharging it.
Good advice. However if you can increase cooling efficacy it might be fun 😉 but more likely lots of heartache. The early turbo lycomings and continentals had lots of issues, and they are still prone to heat related issues. It's hard to get right.
Does anyone know what the sodium filled valves for the rotax cost?
https://www.rotax-owner.com/en/support-topmenu/40-uncategorised/658-si914030-914
-
1
-
-
I'd actually say that a supercharger is less desirable than a turbo for airplanes except for the back-pressure issue and you have some new issues. Turbo's operates very effectively at the reasonably constant loads that planes have compared to cars. The main reason that turbos have a reputation for more heat is simply because they can generate higher levels of boost and they run hot themselves.
I didn't mean to put you off, if you're aware of the issues you cater to them in your design and build.
More capacity is probably the simplest path to more power, however more power also increases heat load and it doesn't get you normalization at altitude.
Rotax has released sodium filled valves which might be a reasonable way to extract a bit more heat.
Also remember that as ambient density decreases, the required turbo size increases so size the turbo for your cruise altitude not sea level.
-
1
-
1
-
-
It's not only pressure drop. The air warms as it flows through the radiator, warm air cools less efficiently, so that back half of the radiator cools less efficiently, or you need to move the air through the radiator faster compared to a thin radiator which creates more drag.
But I do like the mosquito as a plane, it's an example of material design compromise where the design leveraged the properties of the material rather than simply building a wooden plane like a metal one.
Apparently this is a quote from Hermann Goring
'The British, who can afford aluminium better than we can, knock together a beautiful wooden aircraft that every piano factory over there is building, and they give it a speed which they have now increased yet again. What do you make of that? They have the geniuses and we have the nincompoops!'
-
2
-
-
20 hours ago, RFguy said:
Ian, what's your take on the ability for Skippy's exit flow radiator to work at anticipated ?
A problem with most small planes is the lack of space and it's even worse in the engine bay. You're making compromises simply to make things fit. Cooling is really hard to get right.
The aim is to accelerate the outflow as much as possible in the final duct recovering as much energy as possible. One of the things with these designs is that they tended to make the exit duct adjustable and not the inlet, higher pressure in the inlet duct makes the air spill around the intake so a static oversized inlet would appear to be OK. It's so difficult getting this right intially I'd be tempted to go down the variable geometry path as it would allow me to tune in flight rather than build 5 ducts before I found the best compromise.
The other thing which people have alluded to it that the cooling requirements in climb are different to those in cruise so with any static design you're either over-cooling in cruise or cooking in climb.
But it's another thing to build and another thing to manage in flight.
These pictures are from another forum it's worth noting that the mosquito's design opted for a very thick radiator even though it's less efficient simply to make it fit.
The P51
-
Turbos make engines more efficient by recovering energy from the exhaust gas however
- They increase the backpressure on the exhaust making valves hotter.
- They compress the intake charge making it hotter PV=nRT
- The turbine compressor blades transfer heat to the airflow as they're not 100% efficient
- You are generating more energy in a smaller space. This means more heat to dump
Essentially it increases the heat load on the engine requiring more cooling. You can mitigate some of these issues with an intercooler however temperature remains an issue. Things like sodium filled valves also help with heat removal.
-
1
-
2
-
On 02/07/2022 at 3:15 PM, Thruster88 said:
Renewed my class2 medical today. Learned a little bit about the current process. I am now confident self declared medicals will come for PPL license holders.
I like your confidence however I wasn't particularly optimistic based upon the views of the working group. From a quick review the thrust of the working group was to harmonize with NZ standards as the best approach and develop new standards.
-
On 02/07/2022 at 4:54 PM, RFguy said:
I contest the statement that "High velocity airflow across the radiator is bad it equals lots of drag."
Rather than argue about this I'd point you toward the article that I linked to and the section on "Classification of drag" being divided into 3 categories.
- Skin friction drag of stream flow.
- Drag due to eddying arising from separation of a stream from a surface.
- Drag due to expansion losses without actual stream separation.
Points 2 and 3 are avoidable
Thus the ideal system will be designed to
- to avoid stream separation or severe expansions
- To reduce the stream velocity over the cooling surface, and
- to reduce the external surface to a minimum.
Even when following these principles it's hard to get the design right hence the design with maths and allow experienced people to fudge.
2 hours ago, Geoff_H said:It was all designed with mathematics, get the older guys to use experience to modify the maths. The measure extensively when commissioning and alter as needed. It was very empirical
-
1
-
1
-
I'm not sure cowling pressure per se is bad for cooling.
To create efficient low drag cooling you want small inlets and outlets and a large area of slow moving air across the radiator.
Essentially the reverse of the below.
http://hyperphysics.phy-astr.gsu.edu/hbase/imgmec/bernoul.gif
High velocity airflow across the radiator is bad it equals lots of drag.
Large thin radiators are more effective than smaller thicker radiators as the speed of the flow through the radiator can be lower for the same amount of cooling. Remember drag is proportional to v^2
Large inlets and outlets are bad (however you need them large enough to provide the requisite heat flow) and generally it's more effective throttling the outlet.
This means that the additional heat you add to the flow can do work (but not really at the velocities we've talking about) However it allows you to minimise drag.
WW2 was the epitome of radiator design as turbine engines made this field pretty much redundant. But there are some gems to be found in this area.
https://history.nasa.gov/SP-445/ch5-5.htm
https://reports.aerade.cranfield.ac.uk/bitstream/handle/1826.2/1425/arc-rm-1683.pdf
-
The energy content of 97 litres of fuel ~= 850 kW/h even at 30% efficiency that about 255kW/h at the prop. And the bonus is that as you use fuel you get lighter.
A nice BMS might be this one. https://www.ennoid.me/ It's open source so if you don't want to buy it you might be able to save yourself a few shekels by building it. It has individual temperature sensors and achieves balanced charging. It also is scalable using master/slave model with the main controller controlling a number of smaller pack based units.
-
17 hours ago, kasper said:
Lets just say they weigh the same for all practical purposes.
The easiest way to make this lighter would be to go on a diet. You're pushing the boundaries of the technologies, it sounds interesting good luck with it. Does your BMS monitor cell termperature?
If you get your estimated 2 hours with your setup how long would a charge take a between flights?
-
55 minutes ago, onetrack said:
Cape Bouvard Technologies, is trying to progress a "structural battery",
It doesn't really matter whether a current battery is structural or not, they're just heavy. Battery powered electric airplanes might be OK for short duration training flights or for people who want to tool around on the weekend flying circuits. They're less attractive as a form of A-B transport.
Batteries are heavy and the rate of improvement hasn't changed much in the last decade, cheaper yes, lighter no. One possibility for a battery would be a something like a lithium-air battery however there are significant issues to overcome prior to this becoming a thing. These issues may prove to be insurmountable, just look at fusion, conceptually easy in practice very difficult.
You might want to consider aluminium-air batteries however they're non rechargeable which mightn't fit with the attractive vision of just plugging the plane in for a few hours before flying off, and they're not cheap.
Another option for aircraft might be to resurrect the liquid salt reactor concept but while this is technically feasible in large transport airplanes I can't see many people waving flags to have flying reactors especially when we can't even get them built as a replacement for coal reactors.
As an aside the French have the greatest percentage of nuclear power, are a net electrical energy exporter, have some of the lowest greenhouse gas emissions in Europe and power which costs about half the cost of Germany. They've been demonstrating how to operating their reactors in a dispatchable manner even though they weren't designed for this role allowing them to dovetail nicely with solar and wind generation.
-
1
-
1
-
1
-
-
There's a nice picture on wikipedia of Carb formation
https://en.wikipedia.org/wiki/Carburetor_icing
There will be some pressure drop caused by long intakes but nothing compared the cooling caused by the venturi and part throttle configuration
-
On 22/06/2022 at 10:22 AM, jackc said:
One would’ve thought members from the coalface should’ve been included?
I agree however there are a number of factors at play here. Some of which appear to be self interest where conflict of interest should be declared.
At the very least there should be significant representation from aviation groups which should include.
- The PPL community
- The commercial industry
- The Gliding community
I struggle to see why there are so many AV med representatives, it is a well understood science and all of the representatives should understand them well. Two representatives should be more than sufficient.
Also the terms of reference should explicitly reference the international experience which should be the key driver for change.
If there hasn't been an increase in accidents related to self certification of medicals then the existing process would appear to provide little value. It should be up to the committee to justify how any additional process would add value.
-
1
-
1
-
The members of the committee are:
- Dr Anthony McArthy
- Dr Jeremy Robertson
- Dr Sara Souter
- Dr Priti Bhatt (Didn't attend)
- Dr Ian Hosegood
- Peter Antonenko
- Matt Bouttell
- John Raby (Didn't attend)
- Will Stamatopoulos (Didn't attend)
It is concerning that the current approach to the committee selection provides a degree of medical expertise with more that 50% representation, however there is not a similar representation by the flying community, the ATSB or people with the relevant mathematical skills to assess risk appropriately. For example even someone with a B Medical Mathematics would provide signficantly greater rigor to the process.
One of the key outcomes of studies into air safety is that the types of conditions identified by the specialist Aviation medical community rarely contribute to incidents involving pilot incapacitation. It is conceivable that providing advice to pilots in relation to food choices prior to flight would provide a greater benefit that the current regulatory process.
Make your own wooden prop
in Engines and Props
Posted
Apologies for joke in relation to forestry, I was trying to be funny but it may have missed the mark. I'm sure that structural analysis, material design analysis & testing etc is all part of the curriculum. However your formal training should make you appreciate the relevance of the research relating to epoxy-wood bonds.
In a related query I was recently pointed to Robert McGavin who works for DAF in Queensland recently wrote "Barriers to the Effective Adhesion of High-Density HardwoodTimbers for Glue-Laminated Beams in Australia" which is an interesting read if a bit sad from an adhesive point of view. If anyone ever has an adhesive related question he's probably the right person to chat with.
Resorcinol is a technically more difficult glue to use correctly which I alluded to, however there are also some PU and Isocyanate glue which also don't tend to exhibit the moisture related delamination issues which epoxy is prone to which are gap filling. From a propeller construction perspective it where the "joint" is simple from a topology perspective it makes sense to use the best adhesive. For a more complex joint where clamping pressure can't be applied epoxy might be the most suitable. However if the joint is simple, clamping pressure can be applied, and maximum durability and strength is required then in most cases resorcinol is a better choice. It also washes up in water which makes cleanup simple. Pretending that epoxy has obsoleted all other glues is somewhat misguided, not a golden hammer. What it comes down to is whether you'd feel safer buying a used wooden aircraft or boat built with epoxy or resorcinol especially if weather exposed. Resorcinol correctly applied has an outstanding record of maintaining a bond in difficult environment, epoxy not so much, but it is certainly easier for non-craftmen to apply and create something.
If you clicked on the links associated with the strength of the timbers involved you may have seen that Ironbark in this instance was grey ironbark or "Eucalyptus paniculata". Rather than write the full botanical name I thought that most people would find the term Ironbark simpler. In relation to making propellers out of ironbark I haven't heard of it being done either however there may be some aerodynamic advantages due to it's superior strength allowing the use of lower profiles.
In relation to your query about seasoned or unseasoned timber I suspect that this is a bit of a red herring. If you read the papers they all deal with seasoned timbers with specific moisture contents. The issue relates to moisture exposure post seasoning which impacts the adhesive performance across a variety of tests.
While internal framing can be fully shielded this protection can't be provided to propellers. Stone chips, rain etc and the exposed nature of propellers makes it likely that the timber will be exposed to moisture ingress as you can't control the weather when flying.