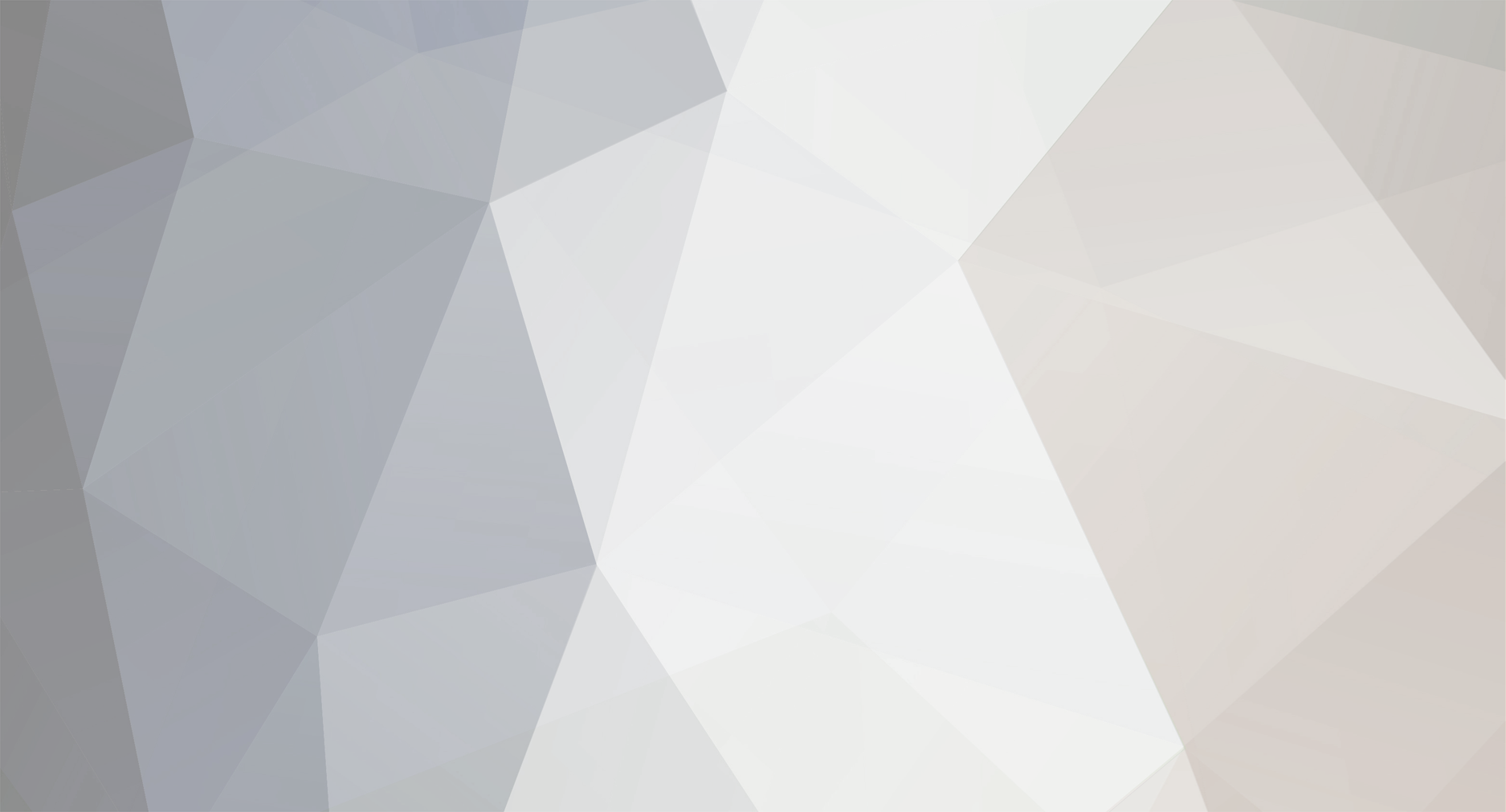
Bob Llewellyn
-
Posts
558 -
Joined
-
Last visited
-
Days Won
5
Content Type
Profiles
Forums
Gallery
Downloads
Blogs
Events
Store
Aircraft
Resources
Tutorials
Articles
Classifieds
Movies
Books
Community Map
Quizzes
Videos Directory
Posts posted by Bob Llewellyn
-
-
I wonder how much of the Jabiru cooling story is told by the pressure field around the cooling outlet(s)? Given the std jab cowl outlet location, even between two "identical" Jabs, a slight difference in wing static incidence or control surface rigging could produce a substantial change in outlet zone static pressure; as could a small change in climb speed or climb weight. Moving the outlet rearwards on a Glassair definitely improves things...Faster flying aircraft seem to suit the Jab motor. Prop load perhaps? There IS a bit of baiting goes on It's not pleasant for those who are getting a good run out of their engines and don't get much exposure to serious discussion. Quite a few ring me privately. Camit are making a serious attempt to improve a product that is significant in the field, and should be supported. There are NO fit and forget aero engines. Know and look after your engine and you go along way to making your own luck. Nev"Faster flying aircraft" are also low drag, so one would not expect large static pressure fields near the front.
Perhaps the simple solution is to cut the noseleg off all Jabirus?
Is Thruster.... is good!
There is no accident in the position of the Hawker Sea Fury cowl outlets, ditto the Douglas Skyraider, Thorp T-18, P-51 Mustang, DH Mosquito... whereas the early US GA cowl with a hole at the back on the bottom for the hot air to fall out, has very little to recommend it.
-
True - the Transavia Airtruk and Pawnee Brave 400 and Fletcher FU-24-400 all have a payload greater than 50% of the takeoff weight. So now we know what efficient aeroplanes look like!Depressing picture of just how inefficient the whole thing is when you analyse what you are up against. Structural reality is that total payload will never be better than empty weight Total load inc fuel will be about 40% of AUW, generally .. You don't have to build a truck to take 6 times it's normal weight. Nev -
The system was an "open throat" wind tunnel with no flow straighteners*, which is a form that has done quite a lot of useful work in comparative analysis.Not to get too far off topic but someone posted a youtube video on this forum showing a bloke holding different aircraft parts over a fan on a desk.The part was connected to a scale and it's drag was read off of the scale.I have been unable to find this video again, if anyone knows?
What I found really interesting (besides the simple test setup) was that an aerodynamically designed part was many times more efficient even though it was many times larger than say a wire cable or something quite small...
*Though the massive tip vortices from a typical desk fan give me the shudders...
This became a major issue for Lanchester - the drag need be no more than the friction drag; but everybody was jumping on "form drag" and ignoring the subdivision of drag sources - and is demonstrated very well in the Cd for a teardrop body of length:diameter 3:1; the Cd is ~3% of the maximum sectional area. Compare this to the ~25% of the Cherokee fuselage. Taylor's Mini-Imp fuselage should have approached 0.05 (5%), or 1/5th as draggy as a Cherokee fuse. Truly we need to think outside the box (and inside the fish? DH Mosquito supposedly had fish input to the fuse...)
-
The problem is the issue of forced convergence - FEM works well with essentially two-dimensional plates of limited number; and even in such cases, the algorithms have to have a predetermined "fudge factor" to garauntee that they converge (I've had some glorious non-convergences reported from Inventor...). As soom as the program takes over the meshing, the model becomes mathematically unstable; if forced in a pro-stability direction, it becomes inaccurate. Chaos theory shows that a large accumulation of small inaccuracies gives wildly variable results from the one dataset.Following on from their CATIA CAD package, French Company Dassault Systemes produced Solidworks specifically for the Aerospace Industry although it was quickly adopted into other major branches of manufacturing. Solidworks incorporates very sophisticated computational fluid dynamics (CFD) and finite element analysis (FEA) capabilities. Commonly referred to as 'simulation and visualisation' they allow you to 'see' the effects of fluid flow and application of stress over and on the surfaces and members of a structure. The software can also generate a complete stress analysis for the individual members and the entire structure.There are other packages with similar capabilites, Autodesk's Inventor has add-ons for both.As for which to choose, a lot depends on which CAD platform(s) you are most familiar with. AutoCAD people will tell you that Inventor is the only way to go, realists with a handle on future trends are likely to start with, or learn, Solidworks. The essential difference is how the software goes about defining the model, AutoCAD is a geometric system and Solidworks is parametric although AutoCAD (and Inventor) now has a parametric design constraint tool. For the most part you don't need to know how the model is defined until you get into very complex solutions. Parametrics comes into its own when you want to change something you did near the beginning of the model and you want all associated members/items to change in a similar proportion, to remain 'linked' with the first item, for example.
Most former NASA and Boeing engineers seem to favour Rhinoceros (Rhino), a NURBS-based geometric modelling package and it has FEA and a Grasshopper Components plug-in for CFD and files can be converted to Solidworks format to use those features if required. Many other engineering softwares will do the engineering calcs for you too - Tekla Structures (formerly X steel), Graitec Advance Steel etc, they are very expensive but you may know someone who has a seat.
The main thing to keep in mind is that although (most) models from one format can be imported and exported from one package to another they lose their interactivity and so will not be 'live' within that other package, they will just be a simple solid or surface. In that case migrating from parametric to geometric is not so much of a problem because the solid can reasonably easily be rebuilt in AutoCAD for example, but if you take a geometrically developed solid into a parametric package it's just a reference solid and rebuilding it to make it 'live' (interactive with other parts of the model), means starting again.
How much of a hurry are you in? For those who are competent in any 3D CAD package you can follow a tutorial and be able to do the basics in Solidworks in a couple of weeks but will only be slightly proficient in about three months and competent in twelve months. After a decade you'll still be learning - I'm talking full-time here ... Many people start their CAD work at school or college with AutoCAD and therefore the learning curve will be much quicker for them in Autodesk's Inventor but you still won't be able to do the clever stuff for a long while.
The other consideration is cost. If you get yourself registered for something in the Engineering field at TAFE or Uni, for example, you can download limited functionality student versions of most of them, which stay activated for three years or so, and the extent of functionality is sufficient for most private purposes, quite enough to design an LSA for example. Once you go to the professional level you'll have spent enough on software to buy a brand new LSA ...
The pro versions basic costs (excl add-ons and in USD) - Solidworks about $12K, Inventor $8-12K depending on the re-seller and it includes AutoCAD, Rhino/flamingo is the cheapest and best value for beginners at about $1K plus a few hundred for the add-ons, Tekla is about $35K and Advance is about $10-15K.
If your only interest is to experiment a bit and see what difference a few changes make to the performance of a basic aircraft form you could have a play around with X-plane. It's quite a different concept, you download the (free) software and produce an aircraft model of your own design - or choose from thousands of online models - and change the basic model by dragging 'handles' until you have what you want. Then you define the engine power and type(s) and various other parameters and go and fly the plane in the simulator. Then go back into the model, change it and fly it again and compare the difference.
The thing to remember with X-plane is that although the software makes a very nice rendered image of your plane for you to fly, the rendered image isn't fully representative of the plane you fly in the simulator because you are flying the parameters you input, not the model, so if you don't define the flaps accurately the performance won't reflect the flaps you may think you have, if you get me. Also, disregard a lot of what X-plane indicates about stall characteristics, it doesn't cope well with anything other than simple stall behaviour. Disclaimer - I've only played a little with X-plane so others know much more about it than I do, but some pretty experienced and successful designers speak well of it (for specific purposes) and use it as a matter of course to test their new design progress.
Below are some images, the first three are examples of CAD FEA, the first showing the stress on a wheel as it would be when loaded with the weight of a car, stress on operating turbine wheels, a loaded chassis showing the point of greatest deflection. The rest are CAD CFD showing pressure distributions, the last one is probably something close to what you are looking for, and demonstrates why modern airliners have the bulge below the wing centre-section and have been able to reduce the size of the fillets as a result. Co-incidentally a very handy space for the gear and systems stowage as well - note how evenly spaced are the isobars.
[ATTACH]28023[/ATTACH] [ATTACH]28024[/ATTACH] [ATTACH]28025[/ATTACH] [ATTACH]28026[/ATTACH] [ATTACH]28027[/ATTACH] [ATTACH]28028[/ATTACH] [ATTACH]28031[/ATTACH] [ATTACH]28029[/ATTACH][ATTACH]28030[/ATTACH]
FEM is a tool, that translates reality into 2-D triangular plates with imaginary thickness, and averages the properties as if the plates were rectangular. It gives very precise answers, but the accuracy is suspect in all but fairly simple structural models with intelligent - not automated - control of the meshing. Computer programmers neither understand this, nor care.
It is my understanding that the Joint Strike Fighter FEM teams entered an intractible dispute, and they had to build two extra prototypes to resolve the FEM disgreements (back about 2006/7).
Hoerner himself states that there is no credible method for predicting laminar to turbulent transition around a 3-D shape, and the physics haven't changed...
-
the 7.1lb (last) drag term in the example is for wing parasitic plus tail parasitic, not just tail!Induced Drag is estimated as wing area (S) x 1.2 x Cl (lift coefficient) squared / (PI x A(spect Ratio)) for a constant chord wing (square tips) of AR 5 ~ 8ish; 1.1 x Cl / (PI x A) for a straight tapered wing in the same aspect ratio range; and Cl / (PI x A) for an elliptical wing - but forget that one, unless you like snap rolls as stall warnings...You calculate your Cl at any speed from: Lift = 0.5 x rho (air density) x V squared x (S(wing area) x Cl), rearranging for Cl. Assume your maximum Cl (unflapped) will be ~1.45, and you won't be far wrong at all. Forget the "this airfoil section gets 1.8!" claims, those are not figures for 3-dimensional wings, OR at real Reynolds numbers, OR in typical air.Your fuselage drag coefficient will be in the range ~0.25 (Cherokee style) to ~0.15 (Sonerai), ignoring cooling drag, based upon the maximum cross-sectional area from in front; calculated from Drag = 0.5 rho x V squared x max cross sectional area x Cd (say 0.2 to start with).
Cooling drag depends a lot on what's inside the cowl, but a good starting point is (imperial units): (5 + 5 x number of cyls) x 0.025 x 0.5 rho x V squared in feet/second. Most GA aeroplanes do worse than this.
U/C, faired and spatted, will typically be 0.4 x frontal area (i.e. max section from in front) x 0.5 rho x V squared.
The wing and tail surface parasitic drag will be ~0.008 x projected area (plan, in the case of wing & HS) x 0.5 rho x V squared.
Calculate thussly the total drag at, say, 40kt; 50kt; up to 120kt by 10 kt increments. The lift remains the weight of the aeroplane, so you have the L/D at each speed. This gives you the (unpowered) sink rate at each speed, which - multiplied by the weight - gives you the (thrust) power required for level flight.
Whack that lot into a spreadsheet, and it'll be within a bull's roar; which will give you a fair idea of the performance effects of different configurations.
In the next day or so I'll try to post some general guidance on propellor performance. Have fun!
ps an eg: With an 800lb aeroplane, AR = 6, constant chord wings, 80 sq. ft, at 50kt: Cl = 1.18; induced drag = 70 lb; assume 6 sq.ft frontal area, fuse drag = 10.2 lb; a 4 cyl donk drag = 5.3 lb; two 5.00 x 5s on springlegs in spats etc drag = 4lb; with 24 sq ft of tail, drag = 7.1lb
total = 96.6 lb drag; L/D = 8.28; DHP = 14.8
Assuming a prop efficiency of 55% (4-stroke, direct drive), this requires 27shp for level flight at this speed; with a 45 hp donk, the ROC would be 410 fpm. Check against real aeroplanes...
Good night.
-
1
-
-
Induced Drag is estimated as wing area (S) x 1.2 x Cl (lift coefficient) squared / (PI x A(spect Ratio)) for a constant chord wing (square tips) of AR 5 ~ 8ish; 1.1 x Cl / (PI x A) for a straight tapered wing in the same aspect ratio range; and Cl / (PI x A) for an elliptical wing - but forget that one, unless you like snap rolls as stall warnings...Is there any software out there that would allow you to simulate such a thing?I mean, I'm reasonably competent with maths and physics, but at this stage I'm..... well... like a dog in a forest not knowing which tree to pee on!You've given some good advice, but I don't know where to start to apply it all.
Maybe an aircraft design package exists to allow me to come up with some on-paper numbers?
Thanks,
Gimballock.
You calculate your Cl at any speed from: Lift = 0.5 x rho (air density) x V squared x (S(wing area) x Cl), rearranging for Cl. Assume your maximum Cl (unflapped) will be ~1.45, and you won't be far wrong at all. Forget the "this airfoil section gets 1.8!" claims, those are not figures for 3-dimensional wings, OR at real Reynolds numbers, OR in typical air.
Your fuselage drag coefficient will be in the range ~0.25 (Cherokee style) to ~0.15 (Sonerai), ignoring cooling drag, based upon the maximum cross-sectional area from in front; calculated from Drag = 0.5 rho x V squared x max cross sectional area x Cd (say 0.2 to start with).
Cooling drag depends a lot on what's inside the cowl, but a good starting point is (imperial units): (5 + 5 x number of cyls) x 0.025 x 0.5 rho x V squared in feet/second. Most GA aeroplanes do worse than this.
U/C, faired and spatted, will typically be 0.4 x frontal area (i.e. max section from in front) x 0.5 rho x V squared.
The wing and tail surface parasitic drag will be ~0.008 x projected area (plan, in the case of wing & HS) x 0.5 rho x V squared.
Calculate thussly the total drag at, say, 40kt; 50kt; up to 120kt by 10 kt increments. The lift remains the weight of the aeroplane, so you have the L/D at each speed. This gives you the (unpowered) sink rate at each speed, which - multiplied by the weight - gives you the (thrust) power required for level flight.
Whack that lot into a spreadsheet, and it'll be within a bull's roar; which will give you a fair idea of the performance effects of different configurations.
In the next day or so I'll try to post some general guidance on propellor performance. Have fun!
ps an eg: With an 800lb aeroplane, AR = 6, constant chord wings, 80 sq. ft, at 50kt: Cl = 1.18; induced drag = 70 lb; assume 6 sq.ft frontal area, fuse drag = 10.2 lb; a 4 cyl donk drag = 5.3 lb; two 5.00 x 5s on springlegs in spats etc drag = 4lb; with 24 sq ft of tail, drag = 7.1lb
total = 96.6 lb drag; L/D = 8.28; DHP = 14.8
Assuming a prop efficiency of 55% (4-stroke, direct drive), this requires 27shp for level flight at this speed; with a 45 hp donk, the ROC would be 410 fpm. Check against real aeroplanes...
-
1
-
-
A useful starting point for design estimations is that, in incompressible flow (ie well subsonic) for a very fair fuselage with elliptical wings:All fixed-wing aircraft obey essentially the same basic physical principles; their performance is defined fundamentally by their wing loading, wing aspect ratio, equivalent flat-plate drag area, and power loading. Or if you prefer, span loading, flat-plate area and power loading. Without those numbers, it's not possible to predict the performance. So you need to make a better "first guess" than your description, before anybody will be able to come up with any numbers. A good starting point is the required stall speed; with this and the weight, the wing area can be estimated.Most aircraft with a power loading of 10 lbs per horsepower or slightly above, manage to cruise at about 2.5 times the flaps-retracted stall speed. A higher power to weight ratio will allow maybe 3 times the stall speed; this is about the practical achievable range. An extreme WW2 fighter type might get to a TAS of 4 times the sea-level stall speed, at its optimum altitude. Jet airliners get high true airspeeds by flying so high that they are cruising not much above their minimum drag speed. Polishing the thing and getting close to an "ideal" aerodynamic form does not change this speed relationship very much; but it can reduce the fuel consumption. So the "ultimate" sexy shape actually has less effect on performance than is popularly imagined.The drag breakdown analysis allows you to estimate the equivalent flat-plate drag area (the hypothetical area of a flat plate pushed into the air and subjected to the full dynamic pressure, 0.5 x the air density x the speed squared). Hoerner* is indeed the "bible" for this, but how to use the result to estimate performance needs a bit more; a useful guide to both realistic actual drag data and how to put it together to estimate various aspects of performance, is "The Design of The Aeroplane" Author Darrol Stinton, ISBN 0-632-01877-1; it's quite readable, even if you don't follow the mathematics.
*you won't find Hoerner in your local library; it was published only by the author, so it's a very rare book. Aviation professionals and university libraries are likely sources.
Below the critical Mach number (about M = 0.6), Drag can be represented by two parts, namely the "parasitic" drag, which increases in proportion to the square of the speed; and the "induced" drag, which is basically due to the fact that, because the wing pushes air downwards in order to support the aircraft, it is always flying somewhat "uphill".
It decreases in proportion to the fourth power of the speed. At the speed for minimum drag, half the drag is parasitic, and half is "induced" drag. This normally occurs at around 1.2 to 1.4 times the flaps-retracted stall speed. This idealisation is varied a little by the fact that the parasitic drag of the wing can change somewhat erratically, if it experiences a significant amount of laminar flow over portion of its operating range; however the literature on "laminar airfoils" is not too realistic in the real world.
All this is also affected by the propeller; firstly by the aerodynamic efficiency of the propeller, and also by the increase in drag of parts of the aircraft immersed in the slipstream. Most simple performance estimates make a fairly crude assumption about the likely propeller efficiency, and are often optimistic because of that. In an aircraft that cruises at less than 100 knots or so, the propeller efficiency can be surprisingly low. Again, Stinton gives some useful rules of thumb.
1) The total drag is least when the parasitic and induced drag are equal (as Dafydd mentioned);
2) The minimum sink speed occurs when the induced drag is 3 times the parasitic drag;
3) The best L/D speed is 1.315 times the minimum sink speed.
It's virtually impossible to do better than these, as they are a result of the basic physics. Note that (2) predicts that soaring aeroplanes should have high aspect ratio wings to minimise induced drag, and (3) demands that transport aeroplanes fly at less than twice their stall speed for good efficiency. (3) also means that high speed ratios require huge power.
In a small powered aeroplane it'll be virtually impossible to achieve a speed where the induced drag becomes 3 times the parasite drag, as the Reynolds number range makes it a great challenge to avoid premature separated flow from the fuselage.
-
Reports 485, 518, and 522 tell almost everything about light aeroplane undercarriage. 518 covers spats and faired struts vs "pants".What's the theory behind `pressure recovery' spats, or wheel pants as the US guys like to call them?rgmwaThe theory behind any form of streamlining comes back to Lanchester (1892); any body of "icthyoid" shape (i.e. fishlike) owes all of its drag to skin friction. Which is to say, if separation (and compressibility, but Lanchester didn't know about that) is avoided, only friction drag remains. All of this stuff about "form drag" is simply a way of combining typical friction plus separation in a way that avoids the computational complexities that CAD so neatly deals with.
Incidentally, fish don't use much fairing to avoid interference drag (sharks and whales do...); but air has 14 times the kinematic viscosity of water, so it's much less critical once you're out of the sticky stuff and underwater...
Such highly successful small "racing" aeroplanes as the Miles series and early Lockheeds used "pants" as a structurally simple way of fairing the U/C legs, brakes, wheels and tyres all at once. The drag reduction was substantial. The reduction in directional stability was also substantial, but as everyone was used to directionally unstabke fighters, who cared? It's worth looking at the 1930's european development of small racing aeroplanes, e.g. the French Deutch de la Muerthe Trophy racers ~ 20ft wingspan, 240~350hp, averaging ~ 380kph (207 kts) over two races of 1,000 km each in the one day (in 1934).
The main drag from typical spats comes from the airflow within, and how it leaves the spat. Putting closing doors on the bottom of a spat reaps dividends, and provided they're not made of Unobtanium, it's safe to land with the gear "up"
...
-
There's a NACA report - a series on undercarriage - which looks at spats, leg fairings, pants, and finer points of fillets and geometry - when I reboot my desktop I'll post the number...After spending a couple of months building fairings around my fat 600X6 tyres I finally got to do some proper tests today, flying extended squares at 4000' with and without the spats.In the least impressive test, while cruising at 2900rpm fuel consumption dropped 8.95% and speed increased 6%.I never particularly liked the look of those ugly big wheel pants, but they work.
-
1
-
-
As soon as the air next to a surface begins slowing down, it creates an "adverse pressure gradient". Seperation is imminent. If a low wing is rigged with a small positive incidence, such that at cruise the fuselage centreline is aligned with the airflow, an anti-interference fillet has to grow in radius as it moves aft; and normally, the rear edge of the fillet has to turn up - see also Grumman 4-seat lighties, which twist the root of the flap/TE up.My understanding is that intersecting angles less than 90 degrees should have a fillet to reduce drag whereas intersecting angles greater than 90 degrees don't need it. LaurieYou can also live without fillets if you place a VG at or just ahead of the LE to energise the junction airflow. The cat can be skun many ways; but air dinna like flowing around solid bodies at high speed...
-
Eagles... NO sense of humour...I've often come across them when flying gliders; they'll often join a gaggle of thermalling gliders and show us all up. They consider themselves to be the rightful owners of the sky, and they'll compete with a thermalling glider, just to show who's the best. I've had one stay with me to cloudbase, at 7000 feet. I've only seen one attack a glider once - and that was because it came up behind him in a thermal and bumped him (at about 5 knots relative speed) - quite inadvertently, but the eagle was not amused.-
1
-
-
Didn't Hawker use bolted tubes in the Fury, Hart, Hind, Hurricane ?I carried out the structural testing of the Xair Hawk (H/Hanuman elswhere) for the UK section S approval and I fly one. You would be surprised at the loads an apparently simple bolted tube airframe can actually handle. They are also easily repairable unlike welded tube or composite airframes.Some checks you can carry out to compare the two:-If you get a chance, have a look at both airframes in the nude with no covers.
Check out the way the various tube ends are terminated and bolted.
Grab hold the prop (near the spinner of course!) and try to move it sideways.
Push and pull on the horizontal tail planes and look at the fabric on top the fuselage.
You should notice distinct differences between the two aircraft.
A personal opinion - the Skyranger does exactly what it says on the tin, but the Xair is a stronger build which will handle turbulence better.
Ref comments above, the Xair undercarriage is very robust and will handle "firm" arrivals with no problems. It will also take a lot more than 80 hp, I have flown 912 and D-Motor versions with 90+ hp and they were both very good, the D-Motor being even better due to the much lighter installation.
Nick
EI-ECK
-
Small horses.Indeed yet people running around claiming 100hp for Subaru EA81s with the same inherently flawed setup.Once upon a time I had an overpropped Rotax 503; would not get properly on the pipe at static (or, indeed, below about 25kts...). I fitted a 50mm PVC elbow and about 40cm of straight pipe to one carby; it jumped the chocks... we strangled it, and fitted another inlet runner to the second carby, and fired it up (tied to the scenery, elephants etc). Gutless. More gutless than with no runners. I angled the runner to the front carby, to separate the inlets. Very little change until I had it nearly in the prop, then it roared. So I threw away the plastic and got another prop...
-
1
-
-
It's a big enough deal that Heinkel made the wings on the He111 perpendicular to the fuselage surface, even at the expense of "gulling" the wings outboard, and faired the roots (See also Corsair...). Airliners put external mitres on their fuselages where the wingroots are (there is a compressibility reason as well, but the interference drag is still valid). Cessna stuck the wings on top of his smaller products, which neatly avoids any problems of interference from the wing supervelocity (higher speed air over the top). Thorp kept the PA-28 fuselage constant width to the wing TE, and added fillets reducing the thickness/chord of the root, thus reducing local supervelocity. Henry Millicer positioned the maximum width of the AirTourer at the wing TE. Vans start tapering their fuselages foward of the wing TE, and do not fit fillets, and did not offer any sort of radiused fairing on the earlier products (that I'm aware of); which gives the interesting characteristic that, if the propellor actually stops rotating in flight, at best L/D speed the separation from the wingroot/fuselage blankets the tailplane sufficiently that, if the CG is fowards - say, with an IO-320 driving a CS metal airscrew - there is insufficient elevator power to flare. (Any RV driver who thinks it's normal to not be able to three-point with the flaps out, or to need a blip of power to flare, has been demonstrating the point).So tell me, exactly how big a deal is intersection drag?Would it pay any decent dividends to design a plane where aerofoils/wings/etc join the fuselage at such a gradual rate so as to avoid nearly all intersection drag or is the payoff really not that much compared to the annoyances and overheads involved?Thanks.
Gimballock
Rutan stuck the fan on the butt end of his earlier designs, effectively vacuuming the interference wingroot area, and in any case the Vari-anythings have ample fillets and generously radiused fairing. The P-51 Mustang used fillets; so did the Bonanza. Aircraft that have gone to the trouble and expense of fillets or fairings include most WW2 fighters, most production low-wing GA aircraft post WW2, and most airliners post WW2 (look at the Super Connie!).
Provided you stay at a lift coefficient of less than 0.3~0.4, interference drag from the wing-fuselage junction will be insignificant if the fuselage incidence is appropriate for cruise. For a typical small aeroplane, the increased parasite and induced* drag during the takeoff-climb approaches the weight penalty of an extra passenger.
*Not only does the stagnant wake increase in area by 1~2% of the wing area (or 15~30% of total drag) at best L/D, but the irregularity caused in the spanwise lift distribution increases the induced drag measurably)
Consider the venerable Piper Cherokee; unspatted and in average paint, it'll get a best L/D of about 1:10 at ~65 knots. At 2,000lb, that equates to 40 (thrust) HP to stay up. Now, add 4.5* square feet of extra stagnant wake from putitative wingroot interference drag - a force of ~63lb if the wake be truly stagnant, but ~40lb is likely nearer the truth. So, an extra 8 DHP, or a 20% increase in the power required for level flight.
In climb terms, the cost is 132 fpm. If we assume that the Cherokee at 2,000lb will manage 832 fpm ROC sans interference drag, then the 132 fpm that would be lost, could be recovered by reducing the weight by177lb.
*Turbulent transition and interference separation both develop - spread - at ~15 degrees to the airflow; so on a 5' chord, if the inteference turbulence starts at the LE, it'll be about 1.34 ft out along the TE and 1.34' up the fuselage side, and oscillating to give an effective area around the square of this distance. Check wooltufting and smoke-trail wind tunnel pictures, there'll be enough on the web; or I can find you a couple of NACA report numbers.
To check the sanity of this, a fixed pitch propellor optimised for ~100kts cruise will do very well to exceed ~70% efficiency at 65kts; and, with an unspatted 6.00 x 6 hanging off the noseleg, propulsive efficiency would be less than 65%. As such a prop would also hold the engine revs back in slow climb, the available THP will be around
150 x 0.9 x 0.65 = 88 THP; less 40 to eliminate sink, leaves 48 THP to climb with, giving 790 fpm ROC at 2,000lb. So, the numbers are in the ballpark, and the fillets on the Cherokee are worth about 12 SHP in climb, or at least one passenger, or a lot of your fuel - or not operting out of a strip where you need the performance!
-
2
-
-
No worries!Thanks, Bob.That's about as comprehensive a response as I could have hoped for!You raise some very good and valid points that I will need to digest and ponder!
Stay tuned for further questions.
At this time, designing and building my own aircraft is pure science fiction/fantasy, but I'm always mulling over ideas for when the time is right.
Until then, I will struggle to get my piddley posterior off the ground by conventional means!
Thanks again,
Gimballock.
-
not unless you used a suck-through carby or injected into the eye of the compressor...What about 2-3 psi from a small turbo? would that help normalise the uneven mixture distribution?-
1
-
-
Or you could just stick two Rotax 462's on the wings, and have twin engined reliability!!!!JJ, that's useful. (incidentally, I've been keeping a quiet eye on SDS for about five years now,: I first noticed them when I was researching a possible EA81-powered project, and I've been consistently impressed with what they do.)Suggests to me that there are a few different paths that one could take, probably driven by what registration group one wants to fit in.As things stand, I suspect that the 'retain the carby and add supplementary fine-tuning by EFI' approach MAY be a way to get around having to use a certified engine - though that would need to be tested as a concept with CASA before embarking on a project to try it. IF it can be accommodated in the regs, I still think an option for 55 and 24-certified reg aircraft.
For 19-reg and VH-exp, a straight SDS system (and maybe clean up the pre-TB intake tract, it's pretty squashed for the Bing and early airboxes at least are not a pretty sight, to my eyes). I think I'd like some electrical supply redundancy, and I also think using a conventional alternator with conventional regulator (CAMit or Rotec) would be sensible. On that score, I like the CAMit one as it provides a bit of crankshaft damping and uses toothed belt, not v-belt.
A possible, I'd think, degree of redundancy for the SDS installation that wouldn't stuff things up could be to use a TBI unit rather than just a plain TB with a second system and a manual switch-over. Depending on the sort of flying one wants to do, I guess that could be a 'full-on' TBI set-up if you really feel the need for high-level performance from the back-up unit (you fly out of difficult sites etc.) or even, given that the SDS system is pretty damn reliable, something as simple and pretty cheap as a megasquirt with say dual injectors in a simple tube just before the plenum. Aftermarket TBI set-ups come in at around $2k all up, the megasquirt I think can be set up for about $1k. So, an SDS kit PLUS a redundant back-up set-up might come in around $6k; you'd probably want to be pretty well assured that you'd extend the real, attainable TBO by about double that of what people are typically getting now to look at it as cost-neutral.
So, I think, there are a number of options one could consider. The result of all of our ponderings here is, to me an indication that this whole area of getting better fuel mix into Jab engines is very much a work in progress and I am of the opinion that the potential of the CAMit engine to provide (we hope!) something worth adding some thousands of $$ worth of extra-quality fuel delivery gear onto is the reason that all of this consideration becomes worthwhile pursuing.
-
1
-
1
-
-
Good question. There are two separate (but overlapping) issues here; strength, and stiffness. Lurking in the background is longevity, or ongoing airworthiness, or fatigue - take your pick!Can anyone tell me which is more likely to give more strength per kg - carbon/glass fibre monocoque (like, say a sailplane or a Jabiru) or a tube steel construction with doped fabric or perhaps even a light fibreglass skin (like a nose cone pod on, say, a Drifter)?Just curious.Thanks.
Gimballock.
Because air is thin stuff, most of an aeroplane's structure is also thin, gathering dispersed loads (air pressures!) and feeding them into more major structural members. Apart from the most major of loaded elements (e.g. wingspar root attachment), the maximum strength of aeroplane structures is generally set by buckling; and buckling is a function of stiffness. For example, alloy steel has about three times the working strength of PH aluminium, and is about three times as dense - so, why not use very thin steel instead of thin aluminium? Buckling - because the aluminium bit will be three times thicker than the steel equivalent, it'll have ~27 times the buckling resistance (up to yield - but the working stresses are such that, in sheet and thin extrusions, an aluminium structure works out lighter than Chrome Moly).
The other stiffness issue is aeroelasticity, or "flutter" - if the airframe (or any bit of it in the breeze) is springy enough, it can interact with the airstream and resonate - the first sign of, say, aileron flutter is generally the instrument panel blurring because the shaking is so violent that you can't see; rapidly followed by either the aileron (if you're lucky), or the wing falling off.
Getting back to your specific question, rag does nothing in compression; which is to say, it contributes naff all to the overall strength/stiffness of a structure, though it's a lightweight way to catch small airloads and feed them into a skeletal structure. A steel tube skeleton - i.e. a fully triangulated spaceframe - is itself a very effective structure, and can be designed to be pretty efficient. However, combining the two gives less than optimal material usage. Welded 4130 (chrome-moly) spaceframes are ideal for engine mount frames and cabin structures (that have to feed lift truss loads, landing loads, and powerplant loads around the crew); they are less ideal for such things as tailplanes.
Glass/Epoxy is less efficient in sheet form than aluminium; and it's less efficient in beam form than steel. However, it's much much easier to arrange to have just the right amount where needed - whereas variable thickness aluminium skins are impracticable on light aeroplanes! Also, judicious usage of core materials (coremat, various foams) can make "sheet" structural elements in glass/epoxy look very competitive in stiffness/weight.
Compare the airframe weights, if you can get them, of the Lightwing and the early Jabiru (pre- Light Sports Aircraf category Jab LSA); the Jab structure is a tad smaller % of the MTOW, for an aircraft with much the same payload (i.e. 2 seats), a faster cruise, a similar stall, and more endurance. Both aeroplanes have enviable accident survivability records.
Carbon/epoxy is a clear winner in the stiffness/weight stakes for things like wingspars and D-boxes, but has low toughness and low lug effectiveness - it's very hard to get a light but reliable bolted or pinned connection, such as to an engine mount. Compare the airframe weights of unlimited sailplanes of today, to Blaniks and the wood, steel and rag generation (with the same payload).
If you're aiming at LSA, then a welded steel cabin structure, ditto engine mount, aluminium rear fuselage, glass/epoxy/foam tail surfaces, and a glass/epoxy/coremat/foam wing with aluminium struts is about the optimum for structural efficiency - but the joins between the sections better be well designed!
-
1
-
2
-
-
Obsolete before I wrote it!
-
Unless the air velocity is extreme, or some sort of resonance or interference exists, the air differential will be very small; fuel is much more sensitive to centrifugal force, partial vaporisation etc.Im checking individual injector adjustmentBUT, back to basics on this problem, are we just seeing fuel distribution problems or air distribution issues too, ie does the swirl effect amount of air headed to each pot or is it just buggering up fuel mist?If its just fuel then there should be no need to play with injectors individually?
It doesnt run a EGT feedback loop but can run loop on O2 sensor or maybe AFR
It is an add on and running 100% EFI is way simpler than trying to calibrate 3 fuel delivery systems. I do see the certification point though.
Keeping carb operational would be as simple as running regularly solely on carb system. This a reason why maybe Rotec TBI would be prefered, no bowl or gaskets to be concerned with. Also flow a bit better.
Re certification ......how do Rotax go about certifying their ECU injection system in 912 is? Did they have to get whole thing recertificated?
I see they are offering new software and intake plenums etc to owners, how does the system handle this kind of upgrade?
Whats their redundnacy arrangement?
Shows there must be some acceptance
SDS/Edge Performance do some slick EFI setups for these std 912 too
If there's enough fuel at 3 pots but the 4th is wrong, one needs to twiddle the 4th injector only...
Rotax, under the ASTM for LSA certification, satisfy themselves. Thierlet were the first, and possibly still only, people to get any National Airworthiness Authority to accept non-aviation electronics on a light aeroplane under any Design Standard requiring an independent umpire to be satisfied..., to the best of my knowledge...
-
Nope, not missing that. As I said about 3,000 posts ago, if one regards the EFI as an electronically calibrated high power jet - replacing the enrichment function of the needle - then the mythical complete EFI failure mode is to be fine at ~80% power or less (post #126). FMEA buddy; you'll learn to love itIf I find out where you are, you are going to get a slapping...Yer missing the essential point that trying to get the Bing on a Jaburi to give decent even mixture is a Sisyphean task - you think people haven't damn well been trying to do this for years?-
1
-
1
-
-
Aha! THAT's why you bought #0001 - you're not good with big numbers! I must say, I've long suspected it...David, I actually think that most of those problems have been - at least partially - addressed in this rambling discussion!. I don't have the knowledge or skills to know the numbers, but conceptually, I'd go about it this way:By test, find out the fuel delivery profile using the cd carby only that delivers more or less reliably about, say 90% of the fuel required on average to keep the engine reasonably happy at say 75% power. Set the carby up to do that; needle, jetting. Then add Dafydd's idea of an auto-rich solenoid that simply fools the carby into delivering more than required if in abnormal situation i.e. EFI failure. Perhaps also modify the existing 'choke' function on the carby to provide 'climb-rich' condition, that one simply pulls on at the start of the take-off run and leaves alone until throttling back to cruise climb.Then size the injectors adequately to provide all the additional individual pot supply in normal circumstances so that when everything is running happily, the added injector droplet size is an efficient fuel-air mixture. That is intended to mainly provide even fuel distribution to all pots at the best economy rate..
For electrical supply redundancy, I'd think a fairly small LiFePo4 battery could be plumbed in, utilising the more reliable charging functionality of the CAMit standard-type alternator that has much better protection from dangerous voltage spikes than the Jab style alternator. In fact, I don't think I'd be happy even running the EFI box from anything other than a well-regulated supply, for safety reasons, and certainly NOT any LiFePo4 type battery. Even quite a small (say around 1 kg, 8300 mh-hour HobbyKing battery) should, I'd think, give a decent amount of EFI-running capability - enough to get well along the way to a bug-out destination and set up a get-there height profile that assumes you may need to go back to carby-only power settings.
It would take some intelligent system design for both the fuel and electrical supply, but the beauty of the EFI supplementary is that once the EFI is programmed, it should be possible to apply the entire package to any Jab engine and the EFI will handle the different individual engine / operation characteristics.
Well, that's my theory... cue the dance of the effema angels-on-a-pinhead philosophers..
Most aircooled aero donks run stoichometric - i.e. the "correct" mixture (nominally 14.2~14.7:1) - up to ~85% power, then progressively richen up to ~12:1 at 100%. The main slide needle in Bings (both by shape & position) controls this enrichment. If you re-needled your Bing to give stoichometric all the way up, then EFI failure should only affect you on takeoff/climb; and you'd kinda notice the rev drop!
-
1
-
-
then she must be happy!!!!!They must give them to my wife too, she does that thing when whatever pops into her mind comes out her mouth. -
I put it to you that we feel we do not get full value for our tax dollar; how reasonable this is, I am not sure - though there is a lot of froth and bubble about corruption and inefficiencies, in terms of GDP it seems a trifling amount. I think the lack of meaningful public consultation, even more than the opacity, turns most of our tax into a grudge cost.I think we expect our pollies to do things when a catastrophe strikes. That's the way we have become. It appears we want it without paying very much (or nothing) as well. This post was stuck in the system since yesterday. Just picked it up now. Nev
Intersection drag
in Aircraft Building and Design Discussion
Posted