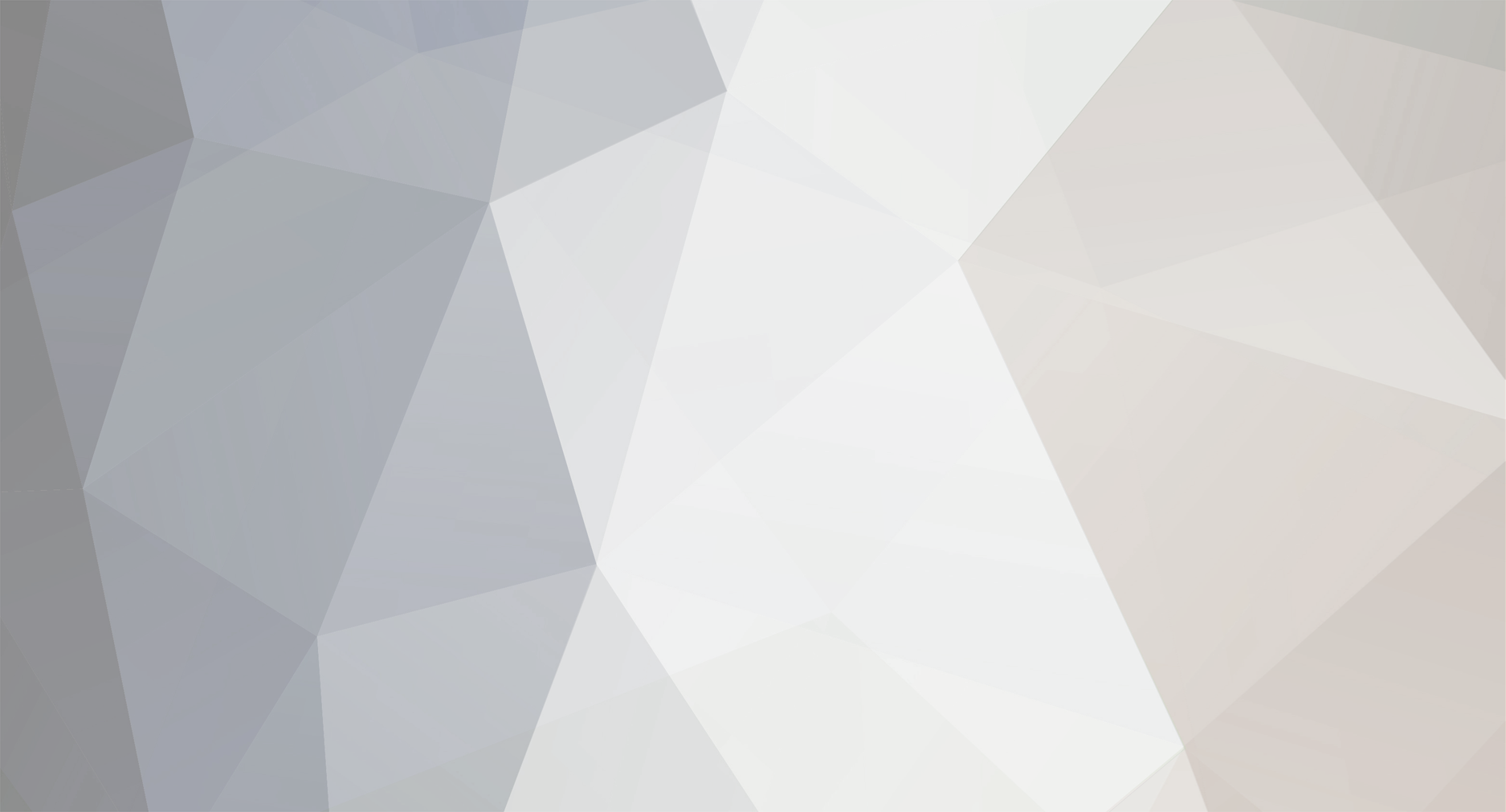
Bob Llewellyn
-
Posts
558 -
Joined
-
Last visited
-
Days Won
5
Content Type
Profiles
Forums
Gallery
Downloads
Blogs
Events
Store
Aircraft
Resources
Tutorials
Articles
Classifieds
Movies
Books
Community Map
Quizzes
Posts posted by Bob Llewellyn
-
-
mmf, it's been a long time since I read the book... but I still find the idea of mishandling the engine in order to stay aloft, mildly horrifying. Wasn't it actually ice forming on a gauze stone filter or something?Yes read the book and flew the same aircraft. Don't know about richening it up to make it backfire. If you opened the throttle too much on start up THAT will cause a backfire but that is a LEAN start. The start us done on the primer solenoid which is a fixed flow if you hold the switch down continuously. Backfiring damages the carburettor as it is a four chamber affair, with diaphragms. The carb anti ice was from the engine heat but may have been augmented with alcohol ?? NevI have had icing in a Thruster, and I was pretty disgusted at that... flying along a bit of low-altitude wave, and a wisp of cloud started to form around me, out of the blue... then the trusty ring-a-ding began to splutter. Sawed the throttle and left the cloud...
-
Earnest K Gann, richening up to get a backfire to clear the ice before it stopped the engine... every few minutes...If ice forms in the carburettor besides losing flow you don't have a functioning carb. The coldest part is where the fuel is vaporising. and downstream of it. (Butterfly and low speed system, depends on design) Nev -
....and here's the one I wasn't going to put up today... the sub-helical twist with tapered tips and a tad more advance... shows that efficiency and thrust don't go hand-in-hand...Hi,Props are really a bit of an art, aren't they? They don't seem to make sense...Duncan
-
No worries... That's because you're not mad enoughGood on you Bob for helping Duncan. This stuff fascinates me, doesn't mean I fully understand it, but the physic is really interesting.... it rots your brain... makes you think politicians are silly and the media is shallow...
-
2
-
-
The certification requirement is that an energy input sufficient to raise the air temperature 50C, is sufficient to control icing. It's not actually a function of energy input; it's a function of lifting the temp out of the zone in which icing can occur. If you fly in marginal icing in VFR conditions (been there), holding an electric cigarette lighter under the slide often helps. But if you're ever caught in serious icing, the Rotax electric system is useless.Not really. There are a lot of 912s flying round with zero carb heat and/or electric/coolant heated jackets on the manifold downstream of the butterfly. The aim being not to heat the air but just to melt ice off the manifold wall which of course needs far fewer kW and does not significantly change the air inlet temperature.The Merlin - which normally fought day VFR - used a water-heated butterfly... with a 1,200hp heater...
-
1
-
-
Getting back to the constant chord versions, here's what happens when you reduce the root advance and increase the tip advance... it's getting a lot more useable, although the first part of the takeoff will still be pretty lethargic.Hi,Props are really a bit of an art, aren't they? They don't seem to make sense...Duncan
This is probably it for today, but we still have to look at effects of spinner size, tapered tips on the reduced-twist form, changing the thickness distribution, optimising the twist distribution, fine-tuning the chord distribution, and fine-tuning the taper (or planform)....
-
Now find attached, the effects of tapering the outboard 1/3 of the blade, from 4" to 3"...Hi,Props are really a bit of an art, aren't they? They don't seem to make sense...Duncan
-
wonder if it's varnish or coking on top piston rings? If so, too hot... good case for silicon based oil!Engines shouldn't be "tight" on shutdown. Have compression but not be stiff. Something is wrong when that happens unless a very new engine, where it might be excused for a while. Nev -
Because most of the information on modern cylinder bore treatments is proprietary (and secret!), it's hard to justify the reliability; and doing it in the backyard does not garauntee good results. Lycoming brought out a "cheap" training donk with steel bores and chromed rings, which has the same prob. as Jabiru (some model of O-320, from memory...).The system appears well-engineered, but is a patch on a bad design. Why not line the steel barrels with Nikasil and use appropriate rings?The lesson is, don't stop flying for more than a weekend. Ever...
-
Find attached the effects of increasing the advance by 10", with no other change. Stay tuned...Hi,Props are really a bit of an art, aren't they? They don't seem to make sense...Duncan
-
It adds bending moment. It adds a lot of root bending moment. Any effective tip device does. The winglets on one of the Cessna twins - 421 mebbe? - drop the fatigue life to ~1/4 of the life without winglets.There has been some discussion recently about the work of Hoerner. One thing that Hoerner lends his name to is the wing tip used in some aircraft, including recreational aircraft.Chris Heintz (one of the CH701's designers) illustrates it like this:[ATTACH=full]28668[/ATTACH]
If the Hoerner wing tip works as illustrated, you get something (in this case, wingspan) for nothing. However, that is 20th century technology, started by much earlier by Hoerner and adopted by Heintz/Tedesco in the 1980s on the Zenith aircraft.
Heintz claims that the Hoerner wing tip expanded the wing by 100-200 mm (per wing):
[ATTACH=full]28670[/ATTACH]
Lately, there are other wing tip designs found on RA-Aus style aircraft. One is advertised by a supporter of this forum, the Nynja. Here, the wing tip device is an upswept one:
[ATTACH=full]28669[/ATTACH]
One wonders what would be the best wing tip for 19-xxx high wing plane? Any thoughts??
The Hoerner tip produces less bending moment than a winglet, and less benefit than a winglet; if you want the benefit of higher aspect ratio, build a bigger wing. There are far better places to improve most aeroplanes than the structurally arduous wingspan extension.
Airliners use winglets for hangarage reasons, not because they're better than a span increase.
-
1
-
-
They're fair cows... the physics is NOT as simple as it looks. I've spent a lot of time developing prop analysis tools (and, I'm pleased to say, I've won an argument with Hartzell about the performance of one of their own props!)... Anyway, once you've got a set of charts showing the effects of various geometry changes, you'll have a better idea of how to pick one, at least..Hi,Props are really a bit of an art, aren't they? They don't seem to make sense...Duncan
-
Hi,Very kind of you to offer to help.
The engine red lines at 3600 rpm, and is fitted with a 1.6 to 1 PSRU. Engine is rated at 50hp max.
Does this help?
Duncan
Sorry I was distracted, and only ran one prop - I normally start with a constant-chord helical twist, and it's in the attachment. I should be able to run a couple more tomorrow, and a couple more the next day - by which time you may be shopping for a variable pitch prop that'll hold its blades!!Hi,Very kind of you to offer to help.The engine red lines at 3600 rpm, and is fitted with a 1.6 to 1 PSRU. Engine is rated at 50hp max.
Does this help?
Duncan
Cheers, Bob.
-
Next time you get into a dogfight, you might be sorry... 3~4% can be the difference between victory and defeat!A few years back I had my hot exhaust squirting into the mouths of a pair of exhaust augmenters (based on 1942 NACA research). They worked well, sucking cooling air past the engine and making a measurable difference to climb performance. The penalty was black muck over the wing root and $1070 dollars for an ANR headset.I removed the augmentors. The 3-4% extra efficiency was not worth the damned noise. -
Good question. At a guess - and it's just a guess - the spat is far enough below the cowl outlet for the effect to be small.I wonder of anybody has ever looked at the CHTs on a Jab with the front wheel spat vs no spat.For reference, the DC-3 fuselage was found to increase the nacelle (engine) drag by ~11% or so... and those engines weren't terribly close to the fuselage!
-
sure thing - I'll have a go later tonight, after I've welded myself to the scenery (or set fire to my overalls!) and convinced the kid to sleep :o)Hi,Very kind of you to offer to help.The engine red lines at 3600 rpm, and is fitted with a 1.6 to 1 PSRU. Engine is rated at 50hp max.
Does this help?
Duncan
-
1
-
-
The deal with fixed pitch props is that they have a pretty limited speed range; it can be extended by having the inboard part of the blades stalled at low fowards speed, but this requires either a bigger donk (Spitfire 1 is an example) or a very long takeoff roll! Even the humble Piper Cherokee, which barely manages twice its stall speed at high cruise, was offered with a "climb" and a "cruise" prop.HiI estimate the MAUW will be in the region of 560lbs (256kg). Valley Engineering supplied a prop with the engine, but to be honest, I don’t know what its specs are, besides being two-bladed, 5ft diam, wooden. In X-Plane, I’m using a 2.5ft radius 2 blade with the following specs:I’m not much of a prop person, and I was planning on getting someone who knows what he’s talking about to select a prop for me (or confirm the V.E. supplied prop is OK) closer to the time.
If you use X-Plane, you might want to grab a copy of the model and fly it. Feedback invited, of course.
You can find the model here:
Because of the thick shank, most wooden props are stalled near the blade roots at low speed, which contributes to the perceived vibrations and poor cooling flow; but the reduced anti-rotational "lift" of the blades allows the engine to develop more power early in the TO run.
The classic helical twist prop shape - c.f. Fred Weick - is very much of the "extend the speed range by stalling the shank" school. From this aspect, use of a smaller diameter prop gives a higher static speed through the prop, so for the same speed ratio, the smaller prop has a higher top speed.
If you let me know the prop RPM at the engine's full power, I can run you a couple of performance curve estimates (they will vary with twist distribution and planform, but not hugely).
-
Dafydd became an aeronautical engineer about a century ago, and worked in aviation businesses, for DCA, and as a consultant... I've worked professionally in the design area for the last 12 years. In the CAR 35 game, one has to become an expert on the job(s) at hand, so I've learned fluid dynamics, FEA, metallurgy etc on the fly - doing a bit of electrical engineering back in 1988 and 1992 helped, but maths, physics, and materials science at high school has been fundamental.Just curious ... do you guys (Bob, Daffyd, HIC and DJP) know all this stuff about aerodynamics, FEA, CFD etc from working professionally in aviation or just researched it out of interest? I'm a structural engineer with a working knowledge of FEA (and it's pitfalls), and I'm also building assembling an aircraft, but have nowhere near enough knowledge to tackle the design of one. I find all this discussion very interesting, if only to make me realise how little I know about the subject. Downloaded a pdf copy of Hoerner last night for some light reading!rgmwaI recomment to you, very strongly, the NACA reports on the web (cranfield site); there's a lot of practical experimentation up to the end of WW2... there's a weakness in the airfoil data, as they were in love with their variable density tunnel, and a bit short on appreciating how much extra turbulence exaggerates the Clmax of laminar or otherwise poor low Reynold's Number sections; and the RAeS (Lock etc)had a much better grasp of propellors; but things like surface finish, wing planform effects, undercarriage drag, and practical stability are all there... and how to correctly baffle a Continental (ignored by Cessna!), etc etc
-
That's a big speed range - how much should it weigh, and what are you using for a prop?Gentlemen,I have been working at this design for a few years now, progressing from rough sketches of improbable concepts, to what I now have - via Raymer, Roncz, Whitney and others. And lots of help from experienced friends and designers.Lately, I have discovered X-Plane as a great visual concept tool, and have been using it as a sanity check on my design formulae. Interestingly, I've discovered that there are very few design concepts which satisfy both the spreadsheets/formulae and X-Plane. What I now have ticks all the design boxes I can find, AND flies brilliantly in X-Plane. I'm a happy camper.
Proposed specs:
Seating: Single seat
Power: 50hp Valley Engineering twin (116lbs, including redrive, full oil, starter etc)
Configuration: Tractor, tandem wing (larger wing in front), tricycle undercarriage
Performance: Stall 43kts, Max S&L 135kts
Controls: Elevators/ailerons on both wings, flaps on both wings
Construction: Glassfibre/3-D Core foam sandwich
Current status:
I am putting the finishing touches to the plug (completing the wing recesses), and will hopefully be doing final prep for the molds within a week or so.
Regards,
Duncan
-
1
-
-
I think it was a Hawker specialty - I believe they machined tricky multi-spigotted tube ends, which were rivetted into place. It avoided de-heat-treating the structure by welding, gave spaceframe structural efficiencies, and made them rather faster to repair from battle damage.[ATTACH=full]28035[/ATTACH]Yes, I do know that Hurricanes are bolted frames. From http://www.spitfiresocietyeastern.org.uk/form 51.html:
"In a hangar adjacent to the airstrip three Hurricanes are concurrently being progressed to airworthy status. G-HRLI belongs to Hugh Taylor and saw RAF service as V7497, construction number 41H-136172, built in 1940 by Hawker Aircraft Limited. The aircraft was shot down over Kent in August 1940. All Hurricane airframe components are joined together using bolts."
Does anyone know how Shorts / Fairey fastened their polygonal stainless steel tube structures?
-
1
-
-
Sounds good - speaking as a speed freak (who flies Thrusters...), reducing the outlet area as a nozzle should give a bit of "thrust", provided you don't increase the positive pressure field around the inlet. Anyway, reducing the cooling flow certainly reduces the cooling drag.Bob years ago you got me thinking about this issue. Any low-wing can dump engine cooling air into the low-pressure zone above the wing leading edge. Mine does and the heads run so cool that I have been incrementally reducing the inlet area. -
Oh yes, GIGO always applies; but when an FEM of a thin-shelled circular tube under torsion loading produces a steadily increasing plate shear around 360 deg, with a step back to minimum, and claims that the solution is correct, and the inputs and reactions are appropriately distributed, the algorithm(s) are called into question... the same model worked well in bending, but not torsion...Similarly with manual calculation, garbage in, garbage out. I'm no expert in the FEA area but from what I have experienced the quality of the output depends significantly on the way the model is built. And, also similar to manual calcs, forming an estimation of the expected result will quickly alert you to unreliable output. I reckon a week or two of modelling and optimising (or re-modelling) beats the hell out of a year of manual calculations.Ain't that the truth ...
Sure, I wasn't saying the bulge was a result of any software's intervention, just stating that the software's CFD visualisation of it shows how that solution works.
The ability to crunch numbers is certainly faster than, say, the Douglas design office; but the equations are no different - and for the proponents of "more complex is more accurate", chaos theory is hard to argue with.
Certainly the graphics give a clear repesentation.
I am averse to neither FEA, or modelling; I use FEA regularly, and have developed quite a few mathematical models in my time; but doing so has made me very cautious of the extrapolative ability of complex models, and acutely conscious of the shortcomings of FEA when applied to structures. As these same shortcomings are increased by at least 2 orders when applied to fluid modelling, even by the heat transferrance analogy, I don't trust aerodynamic FEM very far at all.
For those who like it, feel free to use it. My understanding of an engineer is one who appreciates, and can compensate for, the uncertainties of reality. For me, fluid FEM (other than perhaps simple elemental models) introduces more uncertainty than it removes - just because it shows expected results does not mean that it is correct!
-
Well, yes, as them isobars are inextricably linked to local velocities and so - at high speeds - compressibility, yes. However, I was positing that the isobar distribution need not be so gradual if the flow speed is well below compressibility shock initiation...... and isobars at the centre of swept wings .... -
djp, it was a hangar discussion during morning tea at a small Aus aircraft factory; the bloke was a (visiting) honours graduate in Eng. Aero from some major Aus university, and he'd been expanding his FEM / FEA experience whilst - I think - visiting the US. At the time he spoke, he said that there were a couple of prototypes entering construction, and the "real" reason was primarily to resolve the FEM issue.First I have heard about it but perhaps it was on the UK side? We had 200 or so people working on design and structural analysis of the JSF in Australia and I'd think I would've heard about something like that. The project certainly went overboard on FEM and I agree that many people don't know enough to question the output.He would've said that a very long time ago. Gee, that was even before my time and I can remember being excited when the mainframe computer expanded to 34 Kb. Physics hasn't changed but the capability to solve equations representative of the physics certainly has.Bearing in mind that this probably represented the views of the FEM people he had been working with at the time, I can't say how big the FEM disagreement was in terms of the overall project, or how it was eventually resolved.
From foggy memory, compressibility in the flap shroud had something to do with it...
hrmmm... are you familiar with R&M 2375 (the "King Cobra" flight tests in pursuit of laminar flow?) Hoerner's world tour (so to speak) of sphere tests of major wind tunnels is also quite revealing.
Perhaps it is simply my mathematical unsophistication, but I am as yet unaware of how to repeatedly solve large systems of simultaneous equations without "forcing". The concepts of fluid flow modelling that I have dabbled in, have all required either sweeping simpifying assumptions or VAST numbers of equations... even Brownian motion does not equate to the small scale turbulance found in nature, and the subject of turbulent vortex size range influence on local surface pressure gradients at the difficult Re of 3,000,000 ~ 7,000,000 makes too many unknowns for the variables.
Camit engines - anyone got one?
in Jabiru
Posted