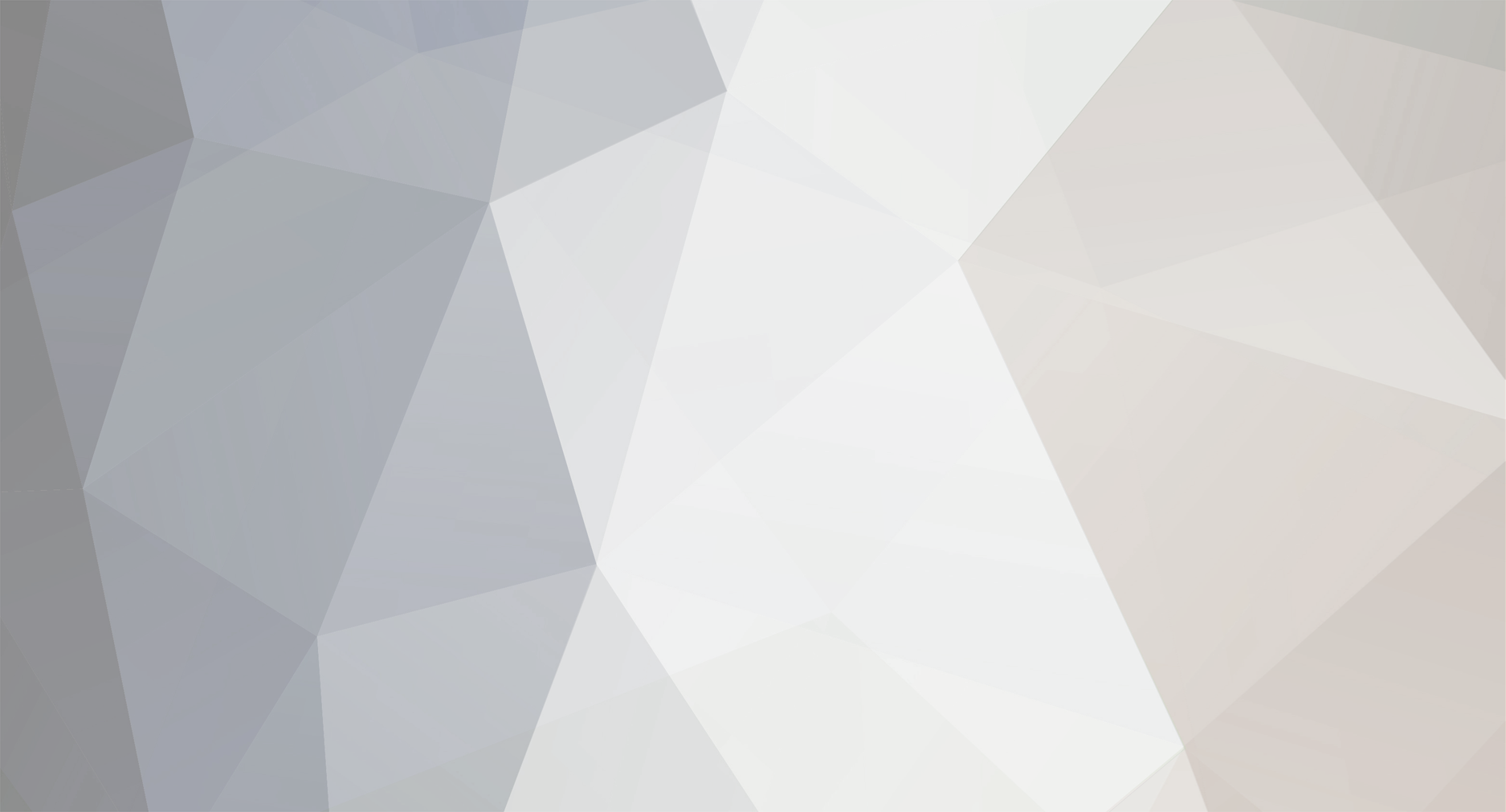
aro
Members-
Posts
1,027 -
Joined
-
Last visited
-
Days Won
11
Content Type
Profiles
Forums
Gallery
Downloads
Blogs
Events
Store
Aircraft
Resources
Tutorials
Articles
Classifieds
Movies
Books
Community Map
Quizzes
Videos Directory
Everything posted by aro
-
ATSB report into light aircraft engine failures
aro replied to fly_tornado's topic in Aircraft Incidents and Accidents
It's also a fact that more people have died after Rotax engine failures than Jabiru. It might even be true. Without actually looking in detail at the numbers - which we are trying to do - you can't be sure. Just because you are aware of more Jabiru failures, or heard it at the airport, or read about Jabiru failures on the internet doesn't make it true. Personally I know about more Rotax failures (also I believe unreported) than Jabiru but one person's personal knowledge is just an anecdote. You have to look at the numbers - and not just for numbers that support what you are trying to prove. You need to spend more time looking for numbers that might refute it. The old "I've never had an engine failure and they were not the engine's fault anyway" routine. This is why you need to look carefully at the numbers and work out what should be included and what shouldn't. Are maintenance related failures excluded from the Jabiru figures? Should Jabiru get any credit for eliminating any possibility of a balance tube problem? (Or all carb synchronization related problems for that matter?) I normally fly a Rotax but have no issues flying in a Jabiru. I would be far more reluctant to fly in a piston twin - I think PA-31s have killed more people due to engine failure in Australia than Jabirus. -
ATSB report into light aircraft engine failures
aro replied to fly_tornado's topic in Aircraft Incidents and Accidents
That was my initial impression, but working from the numbers in the report I get about the same results. The important point to note is that it is only working from the failures classified as "high risk" by the ATSB - 6% of the total failures. I don't buy the numbers calculated for FTFs though - if the high risk failure rate is 4 in 400,000 hours, to get 1 every 3 years a FTF would need to do 30,000 hrs/year. If you have 60 FTFs averaging 1000 hrs/year you would expect a high risk failure every 2 years across all FTFs, If the failure rate for private owners is 1 in about 2000 years, if you have 2000 owners you can expect to see someone have a high risk failure every year. Then you have to ask the questions: "How does it compare to other engines" and "Is that acceptable". The biggest problem with these figures is that the number of high risk failures is too low for the figures to be accurate. Change the classification of one entry and it makes a big difference to the result. -
ATSB report into light aircraft engine failures
aro replied to fly_tornado's topic in Aircraft Incidents and Accidents
Interesting report. I have a few concerns about some of the statistics. I would like more explanation of why they limited the GA study to <800 kg MTOW and the effect this might have had. Superficially it seems reasonable to compare similar aircraft, but if you are comparing engine reliability MTOW is not necessarily the best way to select your population. You would be better to try to get aircraft involved in similar operations. 800 kg MTOW excludes all C172 and PA28, so you probably exclude most of the GA training fleet, while Jabiru do a lot of training hours. The only common GA training aircraft that seems to be included is the C152 (and the Tomahawk, if you consider it a common training aircraft). I don't know which way that would skew the statistics. You also exclude some common amateur built aircraft e.g. RV-7 and RV-8 (although not RV-6 or RV-9). I think you can work out average aircraft hours/year from failures per aircraft and failures per 10,000 hours. If I did my maths right it comes to: Jabiru: 52 Rotax: 30 Lycoming: 40 Jabiru utilization is significantly higher (75% higher than Rotax, 30% higher than Lycoming) which again suggests to me that the operations may not be directly comparable. The report states: It should be noted that when comparing the VH and RAAus occurrences in Figure 5, there is always the possibility that reporting rates for engine failure or malfunction occurrences may differ between VH and RAAus communities. However, it seems unlikely that this would bias any manufacturer in particular. Figure 6, however, shows that there is something significantly different about reporting of Jabiru failures. Jabiru engine failure reports seem to have much more detail. The quality of the reports is different enough that I think you can no longer assume that the Jabiru numbers can be directly compared to other manufacturers. It seems possible that if details of the failure are more likely to be reported, failures themselves might also be more likely to be reported. It looks like Jabiru reports are about 50% more likely to include detailed information about the failure. Does this mean that failures are also 50% more likely to be reported? Or maybe reports with insufficient information are a similar percentage of actual failures, which would mean that Jabiru failures are about twice as likely to be reported. It's all guesswork until you can explain why the Jabiru numbers in figure 6 are so different. Some sort of verification needs to be done to make sure that you are comparing apples with apples. Overall I'm disappointed in the lack of analysis of the figures. I think you can conclude from the report that there are some common failures with Jabiru and MAYBE they fail more often than other engines - but exactly how often it's hard to say. It would be interesting if they had used the FAA methodology discussed in a previous thread, where a number of failures was deduced based on the number of accidents. That would have been an interesting way to cross check numbers. -
Fundamentally, no. Because, from the first page of the Installation Manual: "This Installation manual for ROTAX aircraft engines should only be used a a general guide for the installation of ROTAX engines into airframes. It does not represent an instruction for the installation of a ROTAX aircraft engine in a specific type of airframe or airplane." "This Installation Manual shall in no event be used without fully complying with the specific instructions and/or requirements of the manufacturer of an airframe or airplane." Most of the sections also have a note that the airframe manufacturer is responsible for ensuring that the installation will perform correctly. The airframe manufacturer is responsible for the performance of the engine in the airframe, and the airframe manufacturer installation instructions absolutely override the Rotax instructions. If you want to modify the airframe, even if it is to better conform with the Rotax installation manual, you need to follow the correct processes for a modification to the aircraft.
-
It is/was an (alleged) problem with VW cars. A woman was killed when rear-ended by a truck on the freeway. The truck driver said that her car suddenly slowed down and he couldn't avoid it. Following the accident, many VW drivers came forward and said that they had also experienced their cars suddenly losing power and slowing dangerously in traffic. VW issued a recall of automatic models, however the crash vehicle was a manual. VW claim the problem doesn't affect manuals, but many of the people claiming to have experienced the problem also had manuals. It is only relevant because it is a very similar risk scenario - alleged engine faults that can/have result in death. Similar questions arise about manufacturer liability, whether authorities should force more action from the manufacturer, whether VWs do suffer this type of break down more often than other vehicles etc. or whether the publicity has prompted VW owners to come forward.
-
It's none of those things - it is a number used to calculate the number of engine failures starting from the number of accidents or fatal accidents. The FAA are saying in that document that data about engine failures is unreliable because many are not reported. So when they are required to assess risk they calculate a number of engine failures based on the number of accidents or fatal accidents. Publicity about an engine's unreliability is likely to result in more reports. Since there is so much publicity about Jabiru, failures are far more likely to be reported - it is human nature. Look at the VW sudden deceleration problem - how many additional people reported problems once it hit the news? I fly from an airfield with a busy Jabiru school. I have not heard of any Jabiru failures. I have heard talk of 2 Lycoming/Continental failures/power loss in flight, plus a newly installed Lycoming making metal that meant the engine had to be replaced. None of these appear in the ATSB list I extracted. Many failures go unreported. Numbers are unreliable. The best numbers probably come from using the FAA methodology and using 10x the number of accidents. The number of fatal accidents is too low to be useful. Actually I do recall one Jabiru failure. It failed after an oil line wasn't installed properly after maintenance. The Lycoming failure reminded me, it failed after a fuel line was not installed properly after maintenance. Were either reported? I don't know. There's another interesting number: 3 of 4 engine failures that I know of occurred after maintenance. The other was a brand new Cessna, according to the rumour. All engines fail. You need a statistician to tell you whether one engine fails more than another and what the risk is. I strongly doubt that CASA have had any rigorous statistics done on these numbers.
-
CASA seem to have done a poor job of quoting and perhaps understanding FAA criteria. For example the 1 in 10,000 hour engine failures is not a limit, it is the assumed rate of engine failures (in fact, greater than 1 in 10,000 hours).
-
That depends what you want to measure. If you want to know the risk of an aeroplane landing on someone, total events is the important number. If you want to know where CASA should spend their time and money, events is also the important number (or maybe the number of fatalities). E.g. there is no point in spending time and money on Gipsy engines, even if they prove to be much less reliable per hour than Lycoming - because they don't do enough hours (relative to Lycoming) to be a problem worth looking into. Although CASA sometimes seem to have a problem with this concept e.g. the AD recently issued against an aircraft last manufactured in 1929...
-
That document gives a methodology to estimate the number of engine failure events from the number of fatal accidents. although I'm not convinced by it since the relative performance of the aircraft influences so heavily. I went back to the ATSB database and queried the last 10 years of engine failure related fatal accidents. The numbers: Lycoming or Continental: 4 Rotax: 3 Jabiru: 1 VW: 1 Auto: 1 Gipsy: 1 Which using the methodology (multiply by 100 and divide by 10 years) gives estimated engine failure event rate of: Lycoming/Continental 40 / year Rotax: 30 / year Jabiru/VW/Auto/Gypsy Major each 10 / year. I would say these figures are rubbish due to the low number of data points. Also Lycoming/Continental figures are definitely influenced by the higher performance of the aircraft they are installed in - but this does reflect the real risk. Rotax vs Jabiru is interesting although would be greatly influenced by 1 accident either way. 10 x the number of accidents might give better figures but I don't have the time at the moment.
-
That's not a benchmark on failure rate, its a way of estimating failure rate from accident data. It is saying the numbers for engine power loss and shutdown are unreliable, and provides a way to estimate them from accident data - which is considered more reliable. According to that document, historically engine power loss/shutdown frequency is greater than 1 in 10,000 flight hours (doesn't specify how much greater). Their estimate of power loss/shutdown frequency is Number of accidents x 10 or Number of fatal accidents x 100. So it doesn't provide any actual benchmark. However, it does provide a way to estimate the number of engine failures across each engine type: the number of accidents x 10. The number of fatal accidents is probably too low use reliably. However there have been a number of fatal engine failure accidents behind Lycomings and Rotax, so using this methodology would suggest that those engines have a failure rate much higher than Jabiru.
-
That's my point - without knowing the variation you can't conclude anything. The number on it's own is meaningless.
-
The number seems unlikely to have doubled in 1 year. If there is a trend over several years you would look at it, but you can't conclude anything from those 2 figures. That's when statistics come in - you plug in the numbers over several years, and statistics can tell you how likely it is that this number is produced by chance. If it is unlikely to be produced by chance, then you need to start looking for causes.
-
What FAA benchmark were they referring to? Assuming there is such a benchmark, there are still 2 problems: 1) What if other engines e.g. 2 stroke Rotax, VW conversion etc. also don't meet the FAA benchmark? 2) How long does it take to demonstrate that you do meet the benchmark? This is what I was saying might take 5-10 years of figures to produce valid statistics. When numbers are low, you get a natural variation in figures. Just the other day on the news they were saying that this year 14 people have drowned on beaches this year when the equivalent figure last year was 7. Have the people responsible for beach safety made some big change that is causing people to drown, or more likely, is it just a particularly unlucky year?
-
And that may be very difficult without good data on what triggered the restrictions. CASA have painted themselves into a corner where lifting the restrictions might be very difficult. They have to either: - Come up with some metric for Jabiru to reach to justify lifting the restrictions. This will have to be something that Jabiru didn't previously measure up to, that other engines DID, where Jabiru can demonstrate a change. This is essentially what people have been asking for when asking for justification for the restrictions - a measure to meet to have them lifted or - Demonstrate that the rate of engine failures has decreased statistically. Given the low number of occurrences overall, and the fact that you need statistics over over a reasonable lifetime in a range of operations, it will probably take 5-10 years to get statistically valid data. These statistics would obviously also have to be a measure where Jabiru failed and other engines passed. CASA might have a problem where they can't produce a trigger for lifting the restrictions without providing evidence that the restrictions were not justified i.e. other engines must also pass the same test. A note on statistics: Statistics is more than a count of occurrences or even a set of data. Statistics is a set of tools to tell you whether you can draw reliable conclusions from your data. If you have data with the number of Jabiru failures and the number of other engine failures, the science of statistics can tell you whether you have enough data to draw a conclusion and how reliable that conclusion is. I haven't seen anything like this produced. I have my doubts whether CASA actually employ anyone with statistics qualifications.
-
The problem is that people don't look at the actual risk. They look at what other people guess is the risk. If you look at the actual incidents of people killed on the ground, it is clear that the most risk comes from: 1) Cargo flights 2) Small jets 3) Large jets 4) Military jets 5) Medium turboprop Not necessarily in that order, but these are the aircraft that appear most in accidents where bystanders are killed on the ground. Single engine piston barely appear on the list - even when they crash into urban areas. It's not really surprising if you look at it objectively - the danger comes from speed+mass, and fuel carried.
-
Landing on crossing runways, basically the same distance to run, both go around. ATC were behind the situation and were not separating the aircraft at the critical time. There appears to have been little time for ATC to issue vectors and the aircraft were below minimum vector altitude. The instructions issued by the trainee were unclear and it seems misunderstood. The aircraft may not have got too close but that looks like good luck not good management. http://atsb.gov.au/publications/investigation_reports/2015/aair/ao-2015-084/
-
2 aircraft crossed paths when ATC did not intend it to happen. ATC didn't specifically separate them by altitude or track. One was at 4 mile final when the other was turning base 3.5 miles from the crossing runway. Then both aircraft go around. The only thing that separated them was big sky theory, and we know from experience that the sky is not so big in the vicinity of an airport. So this does look pretty serious to me. Way closer to an accident than we are supposed to get.
-
I think the 161 Warrior is probably the most common PA-28 in training now, and 140s are mostly in private hands. I don't see that I can separate to that level, but since we are interested in the engine not the operation it probably doesn't matter. I searched for Pa-28, C172, C152 engine failure or malfunction from 2007-2012 inclusive (6 years). I got about 160 records. It's a bit hard to interpret, many of the records don't give a reason for the malfunction or much detail on where the aircraft ended up. My counting came up with: * 70 incidents with a serious loss of engine power in the air. * 35 incidents where the aircraft ended up off runway (most off airport, some overran the end of the runway etc. after engine failure) * 24 incidents where a major engine component failed (cylinder, crankcase, valve, fuel pump, fuel controller etc). That's only the incidents where it is spelled out explicitly. However... it doesn't tell you much without the total hours to work out a failure rate. It does tell you that Jabiru engines are not the only engines that can and do fail. I will attempt to attach the data file for those who want to do their own analysis. The biggest problem with the Jabiru issue is that the RAA rules were developed when the engines in use were much less reliable and already assume that engines are unreliable. Unreliable engines is the reason we have a low maximum stall speed. Unreliable engines is the reason we have a low maximum weight. Unreliable engines is the reason we are limited to 1 passenger. Unreliable engines is the reason we are required to be able to glide clear of built up areas. Sure, restrict to GA Jabirus that do not have the same restrictions if it is believed that the engines are not up to certified standard. But I don't see the reason for additional restrictions when the assumption of an unreliable engine is at the heart of the rules we operate under. ATSBSearchResults (6).xlsx ATSBSearchResults (6).xlsx ATSBSearchResults (6).xlsx
-
I also searched for Cessna 172 specifically, there were about 50 Engine failure or malfunction reports in the last 5 years.
-
Just playing around with search on the ATSB site. Searching the last 5 years: Detailed Data Results You searched for: Date range: From 03 Jan 2011 to 02 Jan 2016 Location: All Occurrence Category: All Occurrence Type: Engine failure or malfunction Aircraft and Airspace: Manufacturer: Cessna Aircraft Company - All, Piper Aircraft Corp - All Injury Level: All The number of occurrences during this time period were: Total 334 Accidents 35 Incidents 247 Serious incidents 52 Number investigated by ATSB 25 334 reported engine failure or malfunctions in 5 years from Piper or Cessna aircraft. Any foreseeable danger there?
-
That doesn't tell you much, just refers you to sb-912-066 but from my reading sb-912-066 says if you have the new style cylinder heads, you need to change the instrument labels and temperature limits to match.
-
Missed a word: Anchorage did what they had to do to make the business >look< profitable It doesn't appear that they made any changes to the business, just some accounting number shuffling to produce a paper profit for valuation purposes.
-
Is that true? It seems remarkable that someone would buy a company without the unrestricted right to use the company name. Maybe it is true, but I would like to see a reference to support it.
-
It's important to note that Dick Smith the person hasn't been involved in the business since 1982... turning 10 million into 520 million was the private equity group that bought it from Woolworths. More than anything it illustrates why it may be unwise to use your name as a business brand that you might later sell...
-
1 square foot is 144 square inches, so 14.49 pounds per square inch is 2087 pounds per square foot. C172 wing loading is about 14 lb/square foot so we only need a difference in pressure of about 0.1 PSI or 0.7% at sea level.