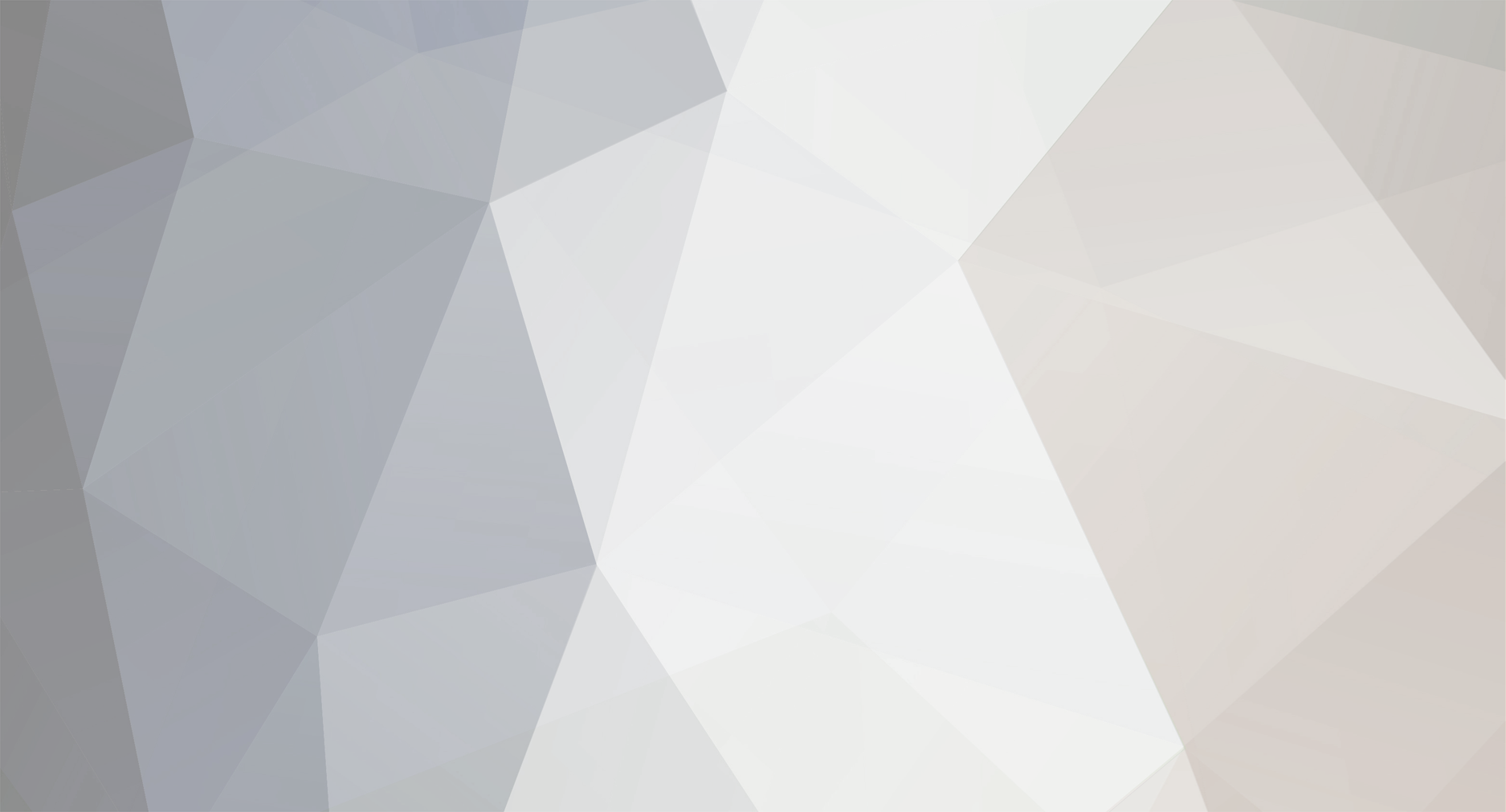
chevy
-
Posts
17 -
Joined
-
Last visited
-
Days Won
1
chevy's Achievements

chevy replied to ave8rr's topic in Aircraft Incidents and Accidents
chevy replied to ave8rr's topic in Aircraft Incidents and Accidents
chevy replied to ave8rr's topic in Aircraft Incidents and Accidents