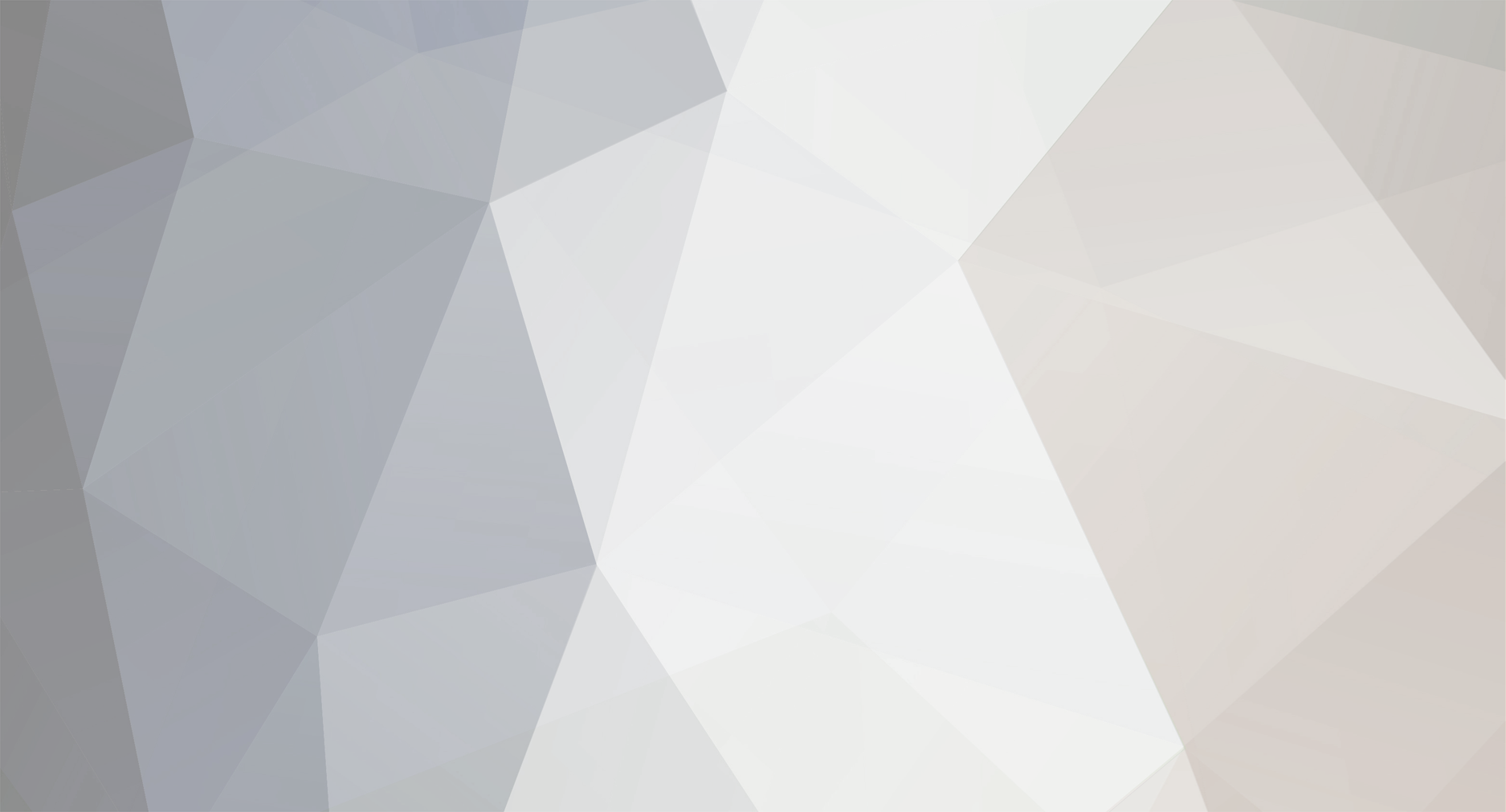
powerandpassion
Members-
Posts
2 -
Joined
-
Last visited
Information
-
Aircraft
Hawker Demon
-
Location
Melbourne
-
Country
Australia
Recent Profile Visitors
51 profile views
powerandpassion's Achievements
-
Bruce, to clarify, QM was used for fixed pitch propellors, not Mosquito props, which were aluminium. Australian timber for Mosquito production that was used was Coachwood veneer for British Standard V3 ply. Other timbers like Mountain Ash for high strength structural reinforcing and Bollywood as a balsa alternative were examined, but ultimately Canadian spruce and Ecuadorian balsa used, as substitution would have called for dimensional changes for which there was ‘no time’ for in 1942-3. The ‘issue’ with Australian Mosquito production were delays consequent to poor glueing practice at wing subcontractor GM Pagewood. Once this was discovered deHavillands embedded their inspectors at Pagewood to resolve the issue, but existing wings already mated to Beale Piano factory made fuselages had to be recalled and rectified, and by the time this was resolved the Pacific War had moved on, and the government, anxious to preserve budget, cut back production. Postwar, dH glued up timber fuselaged Vampire jets with no issues. Resorcinol type glues (Beetle) were used on both designs, so the early casein based glues subject to microbial attack were not the issue. Poor gluing practice at Pagewood was put down to the GM ethos of speed in assembly, poor joint preparation and poor ‘glue habits’, ie, not following instructions, probably from a workforce used to putting together metal fabrications. GM Pagewood did assemble dH Tiger Moths successfully, but these were structurally steel tube framed fuselages with timber spar wings, probably more forgiving than something meant to travel at 600km/h with two 1,000 HP engines strapped on, like a Mosquito wing. If you want to start a conspiracy theory, GM was the owner of North American Aviation, (NAA) which made the B-25 Mitchell twin engined aircraft, which might have been considered a competitor to the Mosquito. NAA did licence the P-51 Mustang fighter and later Sabre Jet to Commonwealth Aircraft Corporation, so perhaps some slick haired NAA salesman ‘encouraged’ poor glueing in Pagewood, but this would be unlikely.
-
Apologies for bringing up this old thread, but a fascinating discussion. I feel as if I have gone down to the cellar and brought out a fine old bottle of wine, worth uncorking ! My interest is in 1930’s era timber propellors, as an example, fixed pitch propellors used on the Hawker Australian Demon, 500 HP RR Kestrel engine, used by the RAAF from 1935 to 1943. These propellors were originally supplied from the UK in Honduran Mahogony, by the 30’s representing the best possible material, and all were coated with doped Irish linen to create a moisture barrier, with brass leading edges. Old photos show Demons left in the open with canvas propellor covers, if not hangared. From 1928 all RAF aircraft were decreed to be made from metal, the great airship projects R100 and R101 were funded by HM government to allow aircraft manufacturers the stimulus to tool up for metal construction and retrain their carpenter workforce to metal fitting. The driver was the extension of aircraft service life by moving away from the destructive shrink-swell cycle of wood. In 1940 Australia was forced, from lack of UK supply, to make it’s own propellors, selecting Queensland Maple after exhaustive testing as the best material. Most antique Australian propellors that remain are QM, very rarely do you see a Honduran Mahogony example in a museum. The shrink-swell cycle was revisited in the 1940’s with Australian Mosquito production, when the CSIR subjected Mosquito wings to climate tests, from Townsville to Fisherman’s Bend, to resolve structural analysis. These CSIR reports make interesting reading : I would only hangar a Mosquito where good coffee and laneway art can be found, or otherwise a humidity managed hangar elsewhere, if longevity is an issue. For the Demon, the clamping plate was aluminium on a nickel chromium alloy hub, so the hypothesis is that the OEM figured a performance benefit from this arrangement, perhaps related to crush? I have not done a hardness test on the aluminium relative to the doped hub, but an old Demon prop I have shows no crush or fretting on the doped hub face. I figure the old timers had tens of thousands of hours of practical experience, and there is always a reason for something. The hub bolts are hollow, and I understand this was one method of ensuring even heat treatment, whereas a solid bolt might have a tough case and softer core, or uneven performance. It seems like the hub, bolts and prop were a system, with careful and complimentary material selection, aided by simple habit of avoiding moisture or condensation in hangaring or picketing. The Ferrodo discs were used with Aluminium Fairey Reed type fixed pitch propellors on Avro Ansons, I see, so far, no evidence of their use for timber props. Fixed pitch timber props made it from 100HP to 1,000HP application, and beyond with various fine veneered and compressed designs, particularly German Jablo types, protected by bakelite type finishes. The issue with Queensland Maple is most of it was clear felled in the 50’s and 60’s to create dairying land in Queensland, and what remains of native stands is now locked away in national parks. Only a limited volume of what might be cut, if at all, will present as even grained, consistent material suitable for propellor making. It is all a rapidly receding art, with generational knowledge lost as ‘old men die and libraries burn’. One benefit of the internet is to post, share and accidentally record information, in forums like these.