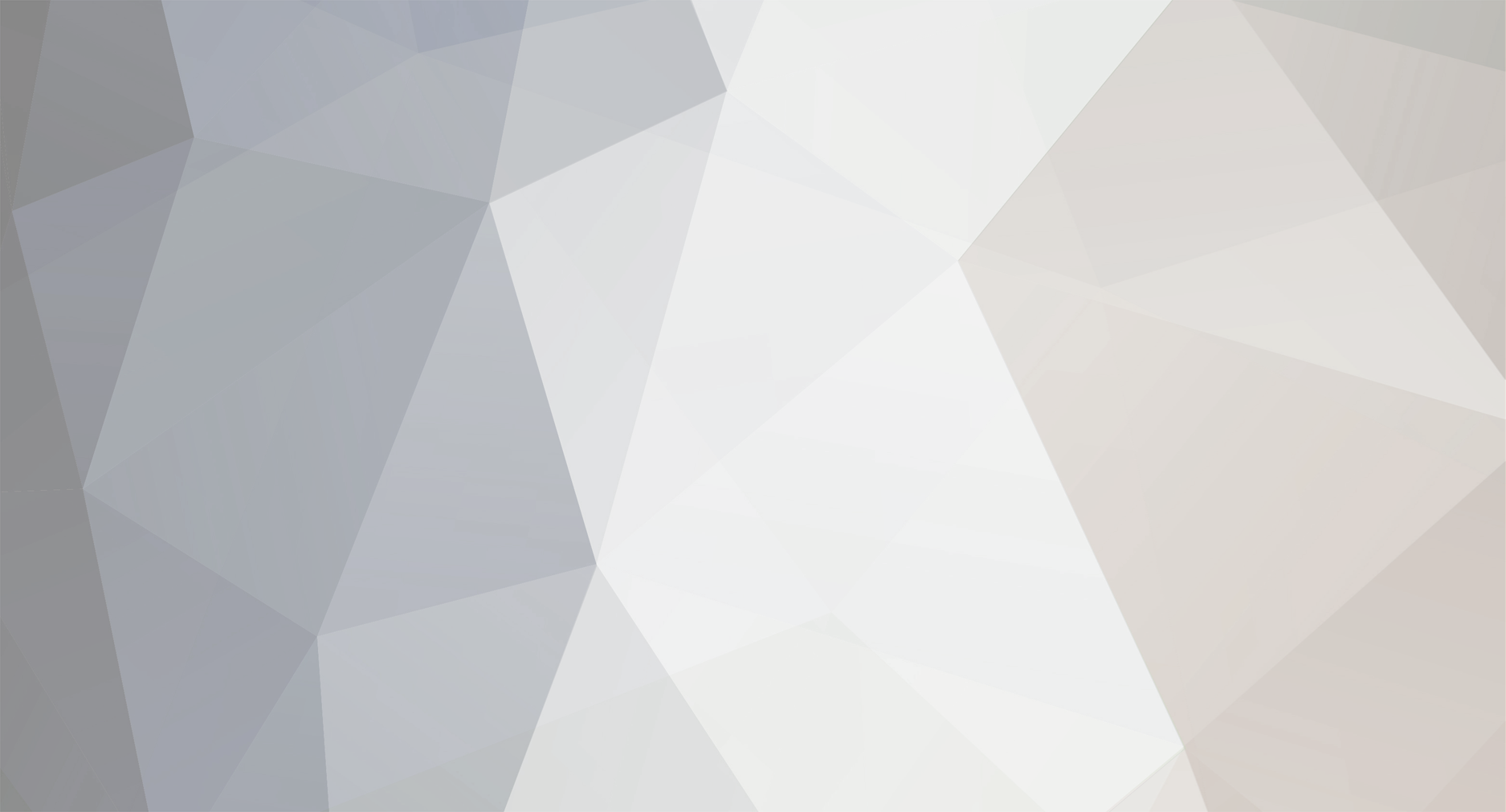
Thruster87
Members-
Posts
655 -
Joined
-
Last visited
-
Days Won
2
Content Type
Profiles
Forums
Gallery
Downloads
Blogs
Events
Store
Aircraft
Resources
Tutorials
Articles
Classifieds
Movies
Books
Community Map
Quizzes
Videos Directory
Everything posted by Thruster87
-
Magazine arrived today a lot thicker than usual, but a lot of adds.LSA registration may turn out to be a headache for some .Including me Cheers T87
-
A new oath holds pretty well; but... when it is become old, and frayed out, and damaged by a dozen annual retryings of its remains, it ceases to be serviceable; any little strain will snap it. ~Mark Twain cheers T87
-
How much difference is there in the operation of the idle stage [fitted in a 3300A] once it has been drilled out to 1.6mm ?? and what is the approx number of turns from stop are you setting the idle screw? I'm still working on getting the temps OK thru out the range Cheers T87
-
Old Bar Ferris Wheel Incident
Thruster87 replied to aaron roberts's topic in Aircraft Incidents and Accidents
The reason 4130 tubing is used that it does not require heat treatment to maintain its strength [if proper joint design /gussets are used], only stress relieving if doing long continues welding which induces too much heat imput. cheers T87 -
Engineering advice
Thruster87 replied to fly_tornado's topic in Aircraft Building and Design Discussion
You can use a AN bolt of the correct DIA, then drill it in a lathe to make a drill bush.Just did one to replace a DC4 bathtub fitting [outer wing attach point] Cheers -
DID i hear correctly, the reporter says the pilot thought it was a contaminated fuel line????
-
The following is a discussion on Metal vs Composite aircraft constuction; I don't run down composite structures, I just debate how appropriate they are when the full life-cycle of an aircraft structure is considered. There are some direct operating costs that can be saved by producing aircraft structures with composites, and the first owner will probably realize these benefits. My world revolves around the airframes that are still flying after 30 years (40, 50, 60, 70, even) and they've changed hands dozens of times. It's a very different perspective. The argument that a well controlled factory can produce a superior aircraft is not in question. I'd agree with that. It's the continued airworthiness costs that are my concern. A de-lamination zone in a CF spar - scrap the wing. Find corrosion on the web of an aluminum spar - clean/replace/reinforce and it's on its way. Once the composite airframe design becomes the norm, then aircraft will not live as long as they did with metallic airframes. The utility, economy, and accessibility of general aviation is something that we take for granted today. Making airframes cost 5x more and last 1/2 as long will be detrimental to the industry as a whole. Sparweb ""A de-lamination zone in a CF spar - scrap the wing. "" Then why would you have a repair schedule from some manufacturers for a 100 to 1 scarf joint to take out the damaged area. Your statement does not fly. B.E. blakmax (Aeronautics) 30 Nov 11 4:02 I am not so sure that composites are so susceptible to being scrapped for minor damage as suggested by Steven. Many repair methods are available for composite structures including adhesive bonding and mechanical fastening. My main concern is that many OEMs would use resin injection to "repair' a delamination. I have yet to see realistic tests which demonstrate a restoration of strength and restoration of fatigue properties after resin injection. I HAVE seen(old)data which showed that injection repair of impact damage reduced the fatigue life of a 24 ply composite by 2/3rds compared to leaving the damage alone. However I am also not a fan of scarf repairs as suggested by BE, especially at a scarf ratio of 1/100. Suppose you have a structure which is 0.25 inches thick. If a scarf of 1/100 is applied then the scarf will be 25 inches long, on both sides of the defect, giving a 50 inch repair. I can't see any DER approving a process to remove 50 inches of good material. Now my expertise is mainly in metal bonding, and if Steven's metal aircraft were bonded using appropriate design methods and valid processes, they would last even longer than the alternate mechanically fastened method. Regards Max SparWeb (Aerospace) 2 Dec 11 15:24 What can I say? The backrooms of numerous repair shops are stocked with plastic airplane wings they can't fix. They need OEM engineering support for repairs because the scope of damage exceeds the MM limits. They wait and wait because the queue is very long. The work could be done, but the approved procedure, drawings, materials, processes all need detailed evaluation and documentation before the wing can be airworthy again. I have been whacked by FAR 25/23/27/29.613 enough times to be wary of composites. Maybe I'm just unlucky, but the airframe types I've been dealing with don't use materials in Mil-Hdbk-17. No data, then no proof, so no approval. Since I am not the OEM, I don't have the proprietary data on hand to back up analysis of a repair. To get it would cost as much as a new wing. To develop the data would cost more than a new wing. The client buys a new wing. I'm not talking about dropped screwdrivers, either. Everybody reading this thread knows you can find that kind of repair in the Maintenance Manuals of any aircraft. I'm talking about hangar rash that cracks the LE. Birds nests in the landing gear well. Fuel seepage. Disposition after a lightning strike. All the fun stuff that happens to airplanes in their lifetimes. That doesn't get written up in the MM because every case will be different. Nobody can cope with these repairs unless they have access to coupon strength/humidity/temperature test data. As I said, that belongs to the people who developed it for the type certificate. To make statements that "it's easy" means you either you work for an OEM, have a deal with one to license the data, or acquired the data by "other" means... and I'll leave it at that. Steven Fahey, CET berkshire (Aeronautics) 2 Dec 11 22:44 Sparweb. I agree with you. When I shut down my repair station I had 11 plastic wings from various manufacturers that were unrepairable because the repairs needed were outside the scope and detail of the maintenance manual (We burned them.), and it was cheaper to buy a new wing than engineer a repair. Another thing driving this was the customer who very often felt that a new wing would just be better than one that was fixed. Right now in the USA there is one manufacturer of plastic single engine land aircraft, who is charging far more than cost for engineering expertise for relativly simple repairs that are outside the somewhat limited scope of his repair manual, just to ensure that damaged aircraft are totaled out instead of being repaired. B.E. The good engineer does not need to memorize every formula; he just needs to know where he can find them when he needs them. Old professor thruthefence (Aerospace) 3 Dec 11 13:29 "Designing repairs" has become a profit center for the oem's, "plastic or otherwise. Had a "plastic" aircraft attempt to taxi with the tail tie down still attached, damaging the attach point. The repair (and associated paperwork) cost thousands of dollars to acquire. At the time of the incident, the type was in the field for years. You can't convince me that that this hasn't happened before. If so, and the data was approved, why wasn't the repair scheme added to the maintenance manual? Because all you have to do is double click a file, and send an invoice for $1500.00, and the end user has to pony up the money. Cha-Ching!!!
-
Old Bar Ferris Wheel Incident
Thruster87 replied to aaron roberts's topic in Aircraft Incidents and Accidents
If you are considering building/buying any aircraft due diligence is your first port of call.Look a little deeper then the advertising.I personally found with the kit aircraft I built, it needed extra bits and pieces [a thicker canopy, phosphor bronze bushes , nylon bushes and a bit of extra angle here and there etc].I was able to use my past experience as a LAME to plan on future maintenance and try to anticipate issues within reason.If you are unsure go and talk to your friendy LAME, L2 and have them go over it.It does make a difference especially if they have a good unstanding of the type/model.Cheers -
http://freedom4um.com/cgi-bin/readart.cgi?ArtNum=133255
-
I found it cheaper to modify an already registered boat trailer[able to carry a 6m boat] Then put slide in and out main wheel supports for just about any track width just aft of the trailer wheels and tail in first by using the boat winch attached to the tail skid/tie down/etc.The length between the main gear and nose is adjusted by sliding the trailer axle via the spring u-bolts.I only carried the fuselage and then the wings separately to the airfield on the craddle siting on topof the trailer in the pic. Hope this gives some sparks to designing yours .Cheers T87
-
Maybe if you look a little deeper. Cheers [used to take these fairings of to do inspections, when I worked for Qantas]
-
All the ones of accident damaged aircraft [not flying race cars] that I've come across, the occurrence of unzipping rivet lines is not common.There is a lot more tearing taking place of the parent material .These aircraft I'm referring to are salvage [some world war 2] from around the world and rebuilt if viable at HARS. Bit of an example of the Qantas bottle explosion below. Cheers
-
A father buys a lie detector robot that slaps you when you lie. He decides to test it out on his son at supper. Father asks his son; "where were you last night" Son relpies; "I was at the library" *robot slaps son* "ok I was at a friends house" "Doing what?" asked the father. "Watching a movie." says son. "What movie?" asks father "Toy story." robot slaps son "ok it was porn!" cried the son. Father yells; "What? When I was your age I didnt know what porn was" robot slaps the father, The mother laughs and says "he certainly is your son." robot slaps the mother...
-
- 3
-
-
One of two caribou has arrived at Albion Park today to become part of the HARS fleet [ATTACH]12477[/ATTACH]
-
Has anyone adjusted the timing on the 3300 solid lifter to the folowing: Note that late-model 3300 engines The new part has been indexed to give 20° BTDC for spark timing instead of the original 25°. These are engraved with "20° BTDC". This change was made to improve the engine‟s tolerance to lower-grade fuel and it is recommended (but not mandatory) that the new part be fitted to 3300 engines at full overhaul
-
Continuing with the debate [lifted from the WEB] 1) There IS no "glaze"! That's a polished surface. Call it "final machining" done by the last set of rings. It's a wonderfully smooth surface of a certain size. Microscopically, it looks like this: | | | | | | | | 2) If you run a hone through it, lightly or heavily, you rough it up, and create low spots. It then looks like this: \ \ / / \ \ / / \ \ Until it "runs in" to a new bigger size that looks like this: | | | | | | | | | | 3) Your new rings, and your piston, must get the surface smooth again, by wearing down the high spots (what is left of the old polished surface - NOT a "glaze" -to the level of the low spots. This results in a) accelerated wear of all engine parts, due to the "grinding compound" effect of the metal being worn off as your cyinder is ground to the oversize of the bottom of the wear spots - as well as the GCE of the abrasive residue which will inevitably be left in the low spots - at the bottom of the grooves created by the unnecessary hone. b) A final (after break-in) size of the cylinder being larger, the piston being smaller, and the ring gaps being larger once this unnecessary abuse of your surfaces has been completed. I've told you that the reason I stopped honing polished bores, and using cast-iron rings on rering jobs was because the SAE research report found that identical engines treated both ways, and then run for a fairly long interval after reassembly showed that: a) The "deglazed engines" showed lower compression and significantly greater wear upon being dissassembled and examined than those which were not "deglazed." b) The "deglazed" engines oil consumption was higher during the so-called "breakin" period than that of the others, and continued to be higher throughout the virtual service life. (These were test bed engines.) c) Periodic compression checks revealed that at all stages, the compression on the deglazes engines was lower. Furthermore, I've also said that I've built many engines since that day in 1969, and I've never had a problem with bad ring sealing, poor compression, or oil burning on any engine I've done since that time - although I did have some troubles of this sort with engines I DID "deglaze" before that. And finally: there is no such thing as "deglazing." Honing is a final process used to take the boring bar marks down to a smoother (smoother, not smooth) surface after machining. The machinist purposely bores slightly oversize, to allow for the metal the hone is going to take out, and hones to a slight oversize, to allow for the metal that is inevitably going to be lost as the piston and rings take out the high spots left by the hone.
-
Talking about engines that have been standing around for a long period of time, the discussion followed on to the need to hone or not [bore 4041 rings cast iron as per the Jabiru engines] after a top end inspection,especially on low time engines. Found the following WEB debate intersting : I was once in attendance at an Auto Mechanics course at Technical College, dancing thru the hoops for a degree in Industrial Ed. One topic we kicked to death in there was the subject of honing and ridge reaming cylinders. It all came about when the instructor greeted us one morning with the news that you should *never* hone cylinders except to finish a bore job, and that it's *pointless* to ream ridges, unless you need to get the piston out. (Cars) What an uproar! Most of us had had a fair amount of experience with engines, and we were pretty incensed. You *have* to "deglaze," or the rings will never seat! You *have* to deridge, or the new rings will hit the ridge and break on the first stroke! Everybody knows that! Well, our instructor, who was a pretty savvy guy, knocked the wind out of the sails of the more scientifically inclined among us with one move: he handed out some reprints of actual SAE test results involving deglazing/not deglazing rering jobs, and ditto for ridge reams. It seemed that the compression test figures after 10000 miles were *better* by far for the unhoned engines. Also the increases in piston clearance were less, as was the bore wear, and - get this - they also showed *significantly* less bearing wear. How come? Well, it seems that when you scuff up a perfectly good smooth cylinder with a rude sort of carborundum device, you are in fact only putting scratches on it, giving us a new, larger diameter at their base - sort of like root and pitch diameters in a nut, say. And when you put it back together, the new rings and this rough surface proceed to grind each other down until smoothness is re-attained. By this time, needless to say, you have larger ring gaps, due to more ring wear, and more piston clearance, since the cylinder has been taken down now to the base diameter of the honing scratches. And the valuable metal so removed has been converted into grinding compound circulating in your oil, so you have also reduced the size of your piston, and contributed significantly to wear of all the other parts as well, from rocker bearings to cam bearings to timing chain rollers to rods and mains. Proven. Scientifically demonstrated in an actual SAE sponsored research project. But you gotta *deglaze* or the rings will never seat, correct? Well, yes and no, Chet. Although it is true that *chrome* rings are so hard and smooth that it can take from a long time to forever for the cylinder to wear them to perfect fit, this is *not* the case for Cast Iron rings. In fact, that's the secret. Chrome rings only in rough (honed) bores. And hone bores only when you have to, ie as the final "finish" of a bore job. Since the boring bar tool in effect runs a screw thread down the bore in its journey toward the land of largerness, it is necessary to do a final "polish" with a somewhat cruder tool - the hone. This is the *only* reason to put a hone in a cylinder. And when it's done, the machinist has purposely left some extra meat in there for the hone to finish to final diameter. And the final diameter is a tad small as well, in anticipation of the initially rapid wear that is inevitable as the new rings and the scratchy bore get acquainted. This is also the reason for very careful cleaning of said bores before assembly, and for very frequent oil and filter changes, until the motor has stopped manufacturing grinding compound during the break-in process.
-
Read this article http://www.ch601.org/resources/riveted_joints_by_chris_heintz.htm Cheers
-
Most kit A/C structures are only static load tested [how many of them have actually been calcaulated by a Aeronautical Engineer]then it basically goes on flying hrs. It is only when there are accidents /incidences/etc that things may appear and highlight issues not foreseen during design.I don't know of any new aircraft design [commercial] that has not been modified later. Even Aeronautical Engineers designing new A/C cannot calculate all the different forces that come into play.I suppose one has to work it out for oneself what standards you are prepared to put up with.It will be interesting to see how deep these investigations will go as the accident appears not to be caused by a structural failure.The following is the RAA requirement for new kit A/C designs Aircraft of Australian Design . If the aircraft type is of Australian design, a satisfactory history of operation of one prototype plus one identical copy for periods of 200 and 100 hours will provide and acceptable basis for application for approval of the kit for the aircraft type. The second aircraft may be factory or privately built. However no more than two aircraft of the type may be built by a factory following application for approval until approval of the kit has been completed.
-
Totally agree Nev.I don't know if the top & side panels are stressed.There is a formula to work out the number of extra pop rivets or larger Dia that are needed compared to solids and work [sample testing] done by members on the Matronics site found a great deal of difference just using A4 pops [a lot stronger] rather then A3 and the way the heads peeled of or not.[the quality /consistency of the pops has a big bearing ] I believe they used Avex pops made in England . A very intersting read http://www.ch601.org/resources/riveted_joints_by_chris_heintz.htm cheers
-
What in heavens name are you going on about turbo.One moment you are saying NOT to analyse then in the same breath you analyse the reasons the rivets are shearing [maybe you do or don't have the technical background to understand aircraft structures or is there another agender].All I'm saying is riveted joints in aviation should NOT unzip for what ever reason.If they do unzip you need to ask why. That's how we improve safety. Cheers
-
Rivet line unzipping like that, still does not seem OK to me for what ever reason.Is there a structures sheety on the forums who would care to comment. Cheers