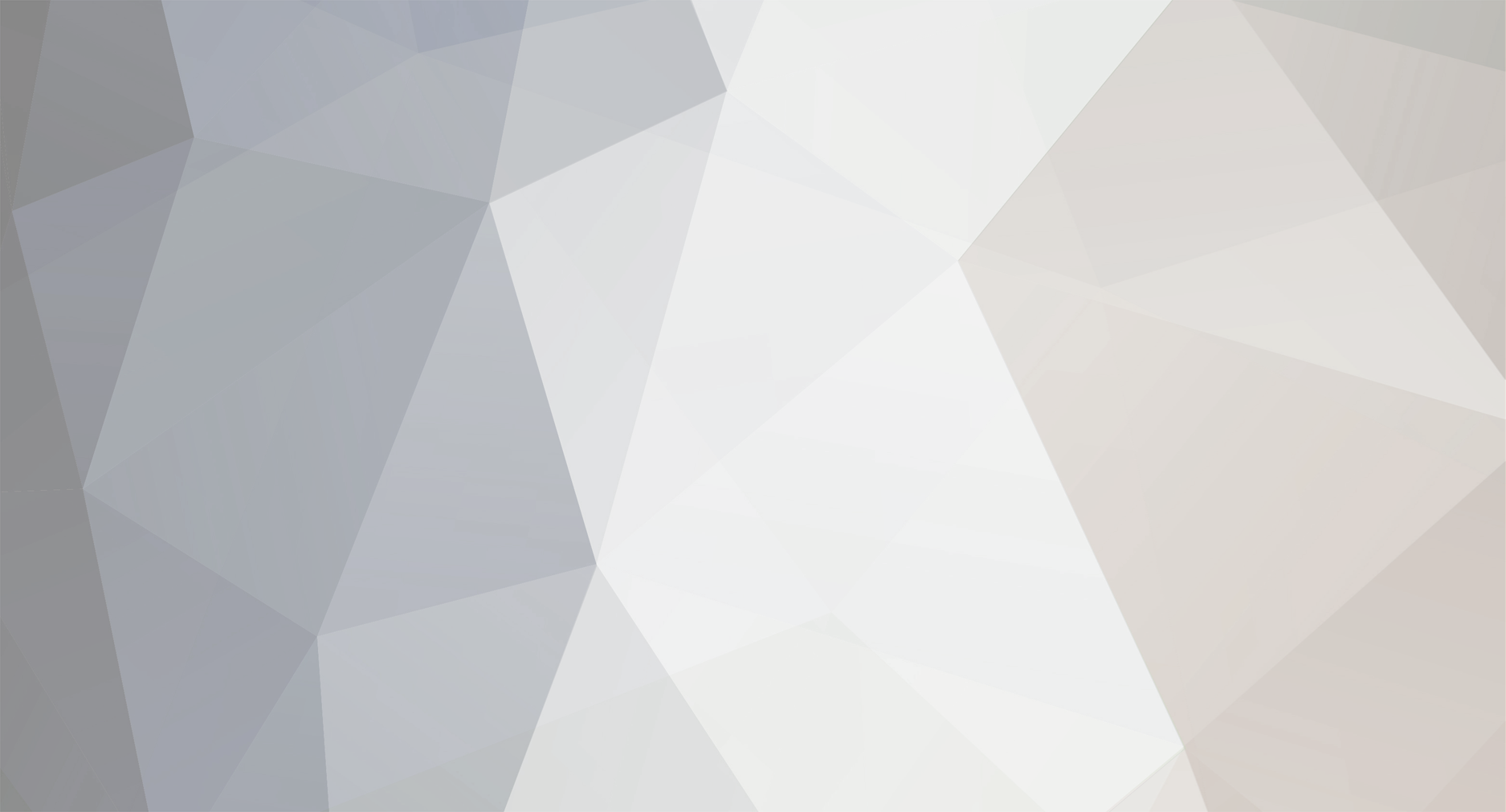
Bob Llewellyn
Members-
Posts
558 -
Joined
-
Last visited
-
Days Won
5
Content Type
Profiles
Forums
Gallery
Downloads
Blogs
Events
Store
Aircraft
Resources
Tutorials
Articles
Classifieds
Movies
Books
Community Map
Quizzes
Videos Directory
Everything posted by Bob Llewellyn
-
pish tish, when ya pull the flap lever, you just have it move the whole wing fowards a foot or so! (304.8mm for those in the current century); offsets the pitching moment, increases the stability. It may be a structural challenge... The NACA modification of the F2-F (Buffalo; my memory was in error ie not the F4-F tests), fitted with a full-span 2H single-slotted flaps with both slot-lip and in-flap plain ailerons, gave acceptable handling at an overall dCl up to 0.88, at low speed / flight idle; higher dCls were accompanied by pitch instability and a tendency to flick roll as a stall warning, though the 1943 military test pilots had no trouble handling it... In essence, the F2 tests showed a need for powered controls, artificial force feedback, and fly by wire. But with these minor issues addressed, there is no reason that a 1,000 hp single seat recreational aeroplane to a military design standard could not routinely achieve overall Clmaxes in excess of, say, 3.0. As the KR2 has an excess seat / load capacity, there is no reason it could not be converted to fly-by-wire, using off-the-shelf servos and an industrial controller implementation of a PC for stability/feedback issues. And as the 912/914 is bulletproof (they say), fit a 914 with a microsquirt programmable fuel injector, and nitrous oxide injection into the eye of the turbocharger compressor wheel (about 5lb/minute should give about 220HP WOT). Extend the main legs a bit so the 84" propellor needed clears the ground (it IS a taildragger, of course?), and Bob (no relation) zyouruncle...
-
NACA Technical Note 808 shows the two-dimensional lift coefficient of 23012 with a single 0.3c Fowler flap at 40 degrees deflection, as 3.3 compared to the naked section at 1.52; I think the same data is plotted out in Abbot & Von Doenhoff. This equates to a dCl of ~1.78; at KR-2 reynolds numbers and planform, the maximum practicable root Clmax (unflapped) will be about 1.4 If one assumes ~65% span flaps, with a bit of effective taper, then the fowler in question has the potential to just about double the Clmax (the inner 65% span carries about 80% of the load, giving an overall dCl of 1.78 x 0.8 = 1.42). This would give 1/1.42, or a ~30% reduction in Vs. NACA Report 723 shows 230XX in three thicknesses, with a moderately undeveloped 40% chord double-slooted flap pack. There is more information therein than meets the eye, as 23012 is a leading-edge staller, whereas 23030 is definitely a trailing-edge staller (23021 changes with Re, but may be considered TE staller for small a/c purposes). In that Report, 23012 had a max dCl of 1.9+; 23030 had ~2.67. As it's the upper rear wing section curvature that is most affected by the flap local suction (thus leading to greater circulation etc), the 23030 data should read across to a thinner aft-cambered TE stalling section, like USAF 35B. On the same basis as the Fowler considered above, the stall speed comes down to 59% of the flapless value - viola!. A conservative aerodynamicist would regard this pasting of the 23030 dCl onto any old rear-loaded airfoil as an optomistic guess, as much because of the retrospectively known vagueness in the NACA correlations between excessive tunnel turbulence and effective reynolds number, as because of the paucity of data on short-bubble behaviour of 23030 (which should greatly affect the translatability of the data to 6-digit sections). It is of note that the 6-digit data published in Abbot & von Doenhoff predates the discovery - by Hoerner - of the VD tunnel's vast excess of turbulence; so the 6-digit Clmaxes given in A&vD are optomistic at least. So - can we get a 40% reduction in Vs, or not? Well, NACA WR L310 - which is subsequent to the 40% double-slotted tests - shows that minor changes in the fore flap - aft flap relationship can give a dCl variation - on a 0.3c flap pack - of 0.56. As this research was based directly on the 0.4c double slotted flap pack, it is reasonable to assume that the 0.4c pack could be improved by as much as 0.3 (dCl) by similar tweaking; which is larger than the various tunnel errors discussed previously, and suggests that the previous generalisation about wide applicability of the 23030 data is defensible. But wait, there's more! An ace lurks up the sleeve, in the form of some data - reported I think in Hoerner's "Fluid Dynamic Lift" - showing a remarkable benefit from a downturned flap TE on a slotted flap. Or perhaps not remarkable - if a plain flappette gives even a 50% improvement on flap nose suction (i.e. local dCl of ~0.6), then the knock-on effect should give a very similar magnitude of benefit to the whole wing / flap pack assembly - i.e. a 50% improvement in overall wing dCl. But is the idea of an overall Clmax of >4 the ramblings of a madman? Schrenk's tests on blown fat airfoils got to a Clmax of well over 5 (from memory). If we regard the rear flappette as increasing the nose suction of the rear flap, which in turn increases the nose suction of the front flap, creating a boundary layer control equivalent to a wing with a suction slot at the TE, it becomes apparent that the overall wing circulation behaviour of a highly flapped wing should be very comparable to that of a 'forced' boundary layer wing. It is of note that the airliners of today, which might be expected to be designed to later data than the published NACA work, are in fact using flap packs that are linear developments of the NACA work, and not very much different at all.
-
This is not a short-answer question! But here goes: It depends on whether the suction side of the aileron is effective - or not. Most are not. The Thrusters (and Drifters), which have a very effective "hydraulic break" to trigger separation over the suction side of the (full span) ailerons, have strong adverse yaw with any use of ailerons. The few Thrusters in the world that have tried to droop the ailerons as flaperons, have found that the adverse yaw is not noticeably worse than standard. Mind you, at 20~30 kts on the runway*, it is possible to steer the standard aeroplanes - in the anti-roll direction - with secondary effects of aileron! They also have the glide angle of a well-fired brick.... *Mostly noticed on bitumen; the response lag on grass is large enough that the control deflections have generally been changed before a swing is noticed. The Cessna 402, which - quite deliberately I suspect - does not achieve suction on either aileron surface, does not have enough aileron power in the engine-out situation; hence Microdynamics VGs, to restore the suction on top of the downgoing aileron. IF the control surface (flaileron?) has a semi-circular leading edge, AND the diameter is slightly greater than the depth of the wing adjoining it - that is, the top & bottom of the aileron (undeflected) stand a little "proud" of the wing surface lines, AND the gap is sealed or VERY small, then the suction side will be effective at up to ~15 degrees downwards deflection. For part-span ailerons, this ties in very well with the 2:1 differential Fred Weick's NACA research program found, ie upwards movement should be twice downwards movement for maximum effectiveness / minimum adverse yaw (with plain ailerons). As mentioned in previous post, droop them very far and they go through separation at some point, which changes the force/deflection* curve, control power, and adverse yaw - for the worse. *The pilot input force vs control deflection - force has to increase with deflection at close to constant rate at any given speed, for certification. The NACA Wildcat (F4-F I think, not FM-2 or their Buffalo) fitted with full-span slotted flap with an aileron in the outer flap, achieved excellent controllability and a quite worthwhile reduction in stall speed. This would not be a minor modification to most aeroplanes... From what I have seen of Van's aerodynamics, and Ed (Kreuger?)'s, I expect that they are using a suction-side-ineffective control surface, which avoids a change with part-deflection separation (since it's always separated!), at the expenses of less effectiveness* and slightly greater cruise drag. It also makes aileron flutter in cruise far less likely, which is why Cessna have stuck rigidly to the formula since pre-WW2. *The change in lift coefficient / change in drag coefficient with control deflection is greater for a suction effective surface; I am not saying that the RV-12 will have inadequate aileron authority, but it could have the authority with less drag! So - simple plain flaperons can be made to work - without huge R&D - if they're full-span and suction-ineffective; but they don't increase the Clmax / drop the stall speed much (10% can be had). Slotted flaps and plain, undrooped, ailerons will give a lower stall speed (up to 20% typ.) and better L/D, if the flap shroud is properly shaped; and, if the aileron is suction-effective & differential, less adverse yaw and lower cruise drag. Slotted ailerons with anti-balance tabs (or pro-balance, as the force-deflection curve requires), and Fowler flaps give a better low-speed L/D, higher Clmax (lower stall speed - as much as 40%) than either of the above, with admirable force-deflection curves. BoeingBus do not fit all those fancy control surfaces to their wings for no reason. RVs traditionally have bags of power, and so the Cessna-style ailerons are just fine for them. Given the running cost of most recreational aeroplanes is governed by the engine, I personally favour the slightly more sophisticated (complex, costly, versatile, efficient) solution of slotted flaps and suction-effective differential ailerons.
-
I have an EA-81 in the shed - I prefer the EA 81 to the R80 (I assume we're talking BMW R80?), because the torque pulses are half the size if at the same power / revs... and the EA-81 is water-cooled, which makes it easier to get low cooling drag. I expect the EA-81 to be very reliable if I get the installation right, and the best value for money for a two-seater.
-
...more or less. A plain, sealed or extremely small gap aileron may be expected to separate from the top surface at not more than 15 degrees downward deflection (and from the lower surface at 20~25 degrees upwards). If your ailerons normally work in the range 10deg down / 20 deg up (differential), then adding a droop of even 10 deg to both will substantially change the adverse yaw effect, in a worse direction when you grab a lot of aileron (eg mechanical turbulence...). If you change the drive geometry, you can largely eliminate this change; but it's likely the force/deflection curve for the controls will reverse near neutral, either with the ailerons drooped or up. Not a simple exercise, unless you don't give a hoot for Certifiable control behaviour. Also, the benefit is small. An analysis of an LSA pre-prototype design, with plain flaps from 13% to 60% span (from C-line), and plain ailerons fron 60% to 90% span, showed that deflecting a 20% chord flap down 15 degrees gave a 10.5% reduction in stall speed; subsequently drooping the (20% chord) ailerons by 15 degrees gave an additional 1.7% reduction in stall speed - hardly value for money. This is because the spanwise lift distribution approaches elliptical* at high lift, even if the wing does not, so the outer bits are not doing much lifting - mainly reducing drag by holding the tip vortices apart! The wing analysed was treated as almost constant chord (constant but with cropped tips), of aspect ratio just over 6, and no twist. A tapered wing would get marginally less benefit from drooping ailerons. *Ignoring NACA TN606, which everybody else does anyway...
-
Stall speed must be measured, normally using a pivotting pitot on a stalk out in front of the aeroplane, a trailing cone static, and a calibrated ASI. With regard to knocking a few knots off, as djpacro said, money will do it... for starters, how does it stall? Does it stop being able to be held wings-level with conventional use of controls, or does the stick reach the back stop, or is there an "uncontrollable pitch-down"? If option one, VGs in front of the ailerons should do the trick. If option two, VGs on the bottom of the tailplane may well drop the stall speed. In either case, the stall behaviour may change radically, though with VGs ahead of the ailerons it's unlikely to kill you. If the stall is an uncontrollable pitch down, it's worth wool-tufting the wings to see where it's initially separating. If it's a trailing edge stalling airfoil - such as anything laminar / 6-digit, or Clark y / USAF 35 / 4 digit, judicious placement of VGs on the wing should drop the stall speed and keep the handling acceptable. This kind of approach is acceptable for homebuilt / experimental or 95:10, where you don't have to go off and do a full spin matrix to prove that whatever you've done has made the spin recovery no worse. It's expensive if you do... mind you, there is no reason that a cautious and thoughtful approach should be expected to make spin recovery any harder! I would strenuously advise against extending the span of the wings; I was asked to analyse such an approach once (actually, I was asked to ok it!); but the increase in bending moment from even a small tip extension is very large, and the KR-2 centre section is not easy to beef up without increasing the carrythrough spar depth.
-
Metallurgy... it's a fair simplification to say that there are two general approaches to fatigue resistance when it comes to selecting an alloy for a highly-stressed structural part; the more time-hallowed stems from the work of Griffith and Orowan, and is to use a material with a large elongation after reaching yield stress. The AN fasteners fall in this category, as demonstrated by their ability to bend 180 degrees around their own diameter. The idea is that the material will locally yield at the tip of a microcrack, and the crack will not propogate. It seems to work. The other approach is to use an alloy / heat treament state with a very high strength, and so (if ferrous) a high fatigue limit; NAS aerospace bolts fall into this group, as do most cap screws. In all (ferrous / ferrous alloy) fasteners, the high strength comes from Martensite (a form of iron carbide), which also has a high intrinsic resistance to disintegration of the basic repeating structure in the atomic lattice. In other words, it is tough on a micro scale, as well as very strong on a macro scale. The high strength also gives the option of pre-tensioning such to avoid cyclic loads in the fastener, and so avoid any potential for fatigue. It's simply a matter of engineering. The issue of thread bearing is more of shear transferance between the fastened parts; where a light-drive fit with only shank enclosed allows a continuous transition from the mode of frictive traction between the faying surfaces to the mode of bearing on the shank and shear in the bolt, substituting shank bearing area for threaded bearing area obviously requires the fastened parts to slip over each other before significant shear transferance into the bolt. After the first occurrence, the bolt mean stress is excessive, and a frictive assymetric preload exists. If such high load events recur, chafing and/or bolt fatigue failure are not far away. Re "aircraft quality", I have also had the dubious pleasure of seeing a (released) box of 7/16" AN bolts, new, of which about half did not fall within the dimensional limits of the milspec... eccentric heads, oval shanks, varying shank diameters. As they were made to order, and cost about $16 per bolt, no-one was very happy about it.
-
Builder Workshop
Bob Llewellyn replied to Staunch's topic in Aircraft Building and Design Discussion
Carol Richard's husband has built an RV or two, and did run a very introductory workshop at Cessnock some years ago. I believe they live on the airfield estate at Temora. Graeme Mudie, or whoever is currently active in the Sports Aircraft Owner's Group, should know most RVites in Australia (although SAOG is qld based). The SAAA has RVs coming out their ears, so they'd be worth a call/email... -
It's NOT a silly question, for this thread has revealed much of the many ways in which recreational pilots select an aeroplane. If the sole purpose was to define the ideal recreational aircraft, then yes, it'd be better done by negatives. Respondents have wished for more cruise speed, less landing speed, decent range and low initial and operating costs. Quite a few have recognised the benefits of the high-wing, strut braced layout, whilst a few at least have also recognised the field of view issue. So the answer seems to be, people would like a choice of a few speed/performance brackets, but all in low initial cost, low running cost, quick-build, and generally easy to get one's butt into the air. With a four-stroke engine... which points at LSA "certified"; CS-VLA is an acceptable standard under LSA in Australia, and meets or exceeds all requirements of ASTM 2245. The remaining question is, will the manufacturer(s) have the expertise to properly exercise "due diligence" in the certification?
-
There is a J-160 with a 912 running around, Approved under CAR 35 Engineering Order; I believe it's at Boonah now. I know of no other Approved J160/912...
-
The 532 was higher compression, not well suited to ULP; the 582 does the same job on lower octane fuel...
-
For GA, there are a stack of subcategories under Experimental. You are talking about experimental-amateur built. try experimental - private use, which is designed to allow one - and one only - of any new configuration to be kept airborne after testing. Note that CAO 95:55 only addresses experimental - amateur built. The issue is this - unless RAAus can demonstrate an exceptionally high risk is posed by your aircraft, they are causing you loss/damage in breach of the Administrative Decisions Judicial Review Act 1988. Take the mongrels to court.
-
It is. There are people in CASA and RAAus who don't understand experimental. The other point is this - BCAR(S) (CAP 482) allows demonstrating reliability by service history - see the Warp Drive / 912 combination. CASA has finally killed off the CAR 35s (by changing the regs), and the new regs are almost unworkable. CASA insist that someone else make the engineering assessment, but there's nobody left. Aviation WILL get safer, as modifications and non-standard repairs can no longer be approved. CASA has won, unless something political is done.
-
The RVs use NACA 23012, or a tad thicker; as did the later Austers, the Beech Bonanze, Grumman Wildcat.... the Starlet is NACA 43012A, or very close; they should be comparable
-
500000 jobs gone ... Media useless
Bob Llewellyn replied to DrZoos's topic in AUS/NZ General Discussion
Could be... I was in high school in the early '80s, and the small business model then assumed a selling price of twice the direct costs as the first estimate of the retail price; in 2000 I did a New Enterprise Incentive Scheme small business course, which assumed a selling price of the average of the competition's price plus a small bit for uniqueness (of whatever you were selling...). I think petrol pricing is perhaps the supreme example of "what the market will bear" pricing, with crippling nock-on effects. -
Hmmm, the RV4 is a bit of a hotrod by GA standards... less than 15lb/hp @ MTOW, less than 15lb/sq.ft ditto... The Starlet airfoil is an outstanding performer at low reynolds numbers (i.e. high Clmax); what power loading and wing loading are you running? If a Starlet has soggy low-speed climb performance, it's probably leakage from the canopy or premature wing root separation (the Piper TraumaHawk is a mongrel for these). Does yours have flaps?
-
I suspect he meant "CAS or IAS?".... in the "rudder during finals" thread (I think) there's a useful post on stall speed determination ...
-
500000 jobs gone ... Media useless
Bob Llewellyn replied to DrZoos's topic in AUS/NZ General Discussion
I posit that Australia has changed from "fair market value" to "what the market will bear" pricing, during (mostly) the late '80s and '90s. I agree that returning to "fair market value" will result in reductions in various costs and wages. Is this thread arguing about changing "what the market willbear', or considering a return to "fair market value"? Note: "Fair market value" places the onus on the manufacturer / service provider to figure out the real costs; "what the market will bear" changes the onus from the manufacturer/provider (who really knows the costs) to the - dare I say gullible? - consumer, who knows what they can afford at that point in time. Whilst Adam Smith's dicta of wealth creation is satisfied in both cases, the "what the market will bear' is based upon mendacity or ignorance, whereas "fair market value" is based upon reality. -
500000 jobs gone ... Media useless
Bob Llewellyn replied to DrZoos's topic in AUS/NZ General Discussion
Antiquated ideas of economics - the notion that "Capital" owns the means of production, and "Labour" operates the machines, should have died by WW2. But Keynsian economics is geriatric too... civilisations collapse due to poor economics. Perhaps more history should be taught in school? -
My Thrusters ain't supercharged, and they manage The W-8 with C-85, or even O-200, appears a fairly - but not astoundingly - efficient package; but it has a very high utility as a personal aircraft; especially in the US, which is paved with runways. Adding a bit of extra power obviously makes them more STOL, but tends to increase the cruise speed and eat into the structural margins blah blah (who'd fit an IO-320 and cruise at 40% power, eh?). A Corby Starlet with a solid lifter J-2200 makes a pretty useful runabout for one, out of short hot-and-high strips... more so with the 3-piece wing and extra tankage, i suspect. The Buttercup looks very much Rundflug-inspired; I doubt the coupled slats/flap mechanism makes for easy approach control! Would it qualify as a "simple" aircraft under LSA / ASTM?
-
500000 jobs gone ... Media useless
Bob Llewellyn replied to DrZoos's topic in AUS/NZ General Discussion
I would observe that the vast majority of commentators here, are pointing their fingers at what they see as failures of the principle of a "fair go" - the issue that, if it is impossible to separate a "management salary plus incentive vs real value contributed by management" package, from greed, then there is something wrong with the package. Similarly, if the operations of an organisation with the function of pursuing the mutual benefit of all those involved in a business (i.e. a union) manifest no benefits but to the executive of said organisation, there is something wrong with the running of the organisation. The whole concept of a "fair go" implicitly considers society as a whole; these days, a significant proportion of Management executives appear to be professionally short-sighted to (a) the length of their contract, and (b) the performance indicators by which their renumeration is affected. Call it professional training in abandoning perspective. Our politicians seem to have it, too... the result is that the executives of an organisation are, unconsciously, making that organisation into a parasite upon society as a whole, rather than a symbiote. Unions are required, by definition, to be partisan to their membership; but that does not mean that they cannot recognise the interests of the rest of the industry in which their members work, or indeed society as a whole. Send not, therefore, to ask for whom the bell tolls. -
Ok, sounds good. I have a small concern over the Vb, or Vno; small slow aeroplanes tend to be able to achieve their Clmax in rare gusts, and the process of sticking bigger engines in (e.g. the Rotax 912 in the Kappa Sova, designed for a 503!) gives a 75% power cruise way over the rough air penetration speed. Thorpe & Van Grusven(?) get around this by low aspect ratios, and highish wing loadings; I expect the W8 did similar, but the W10 wing would be expected to have a steeper lift curve. Do they suggest a Vno or Vb? They're one of my favourite designs, but the W8 with small engine has a not-so-impressive speed range by modern standards, and is less than ideal out of 1,000ft grass strips at 3,000 ft density altitude :o(
-
Major LSA Ceases Sales and Production...
Bob Llewellyn replied to River's topic in AUS/NZ General Discussion
What about the "Angel Flight" mob? I don't see why RAAus couldn't participate... -
500000 jobs gone ... Media useless
Bob Llewellyn replied to DrZoos's topic in AUS/NZ General Discussion
Not detached from Geoff Dixon, though... -
500000 jobs gone ... Media useless
Bob Llewellyn replied to DrZoos's topic in AUS/NZ General Discussion
Ok, here goes; "Alan Joyce and... and... Sol... (grunts)... Sol.... Trujillo were... "NO! No, I can't do it. I suggest that the common thread is the short-term fiscal sleight of hand intrinsic in the Harvard School of Business management model (I know that the original Harvard model is way superseded, but the intrinsic confusion between the appearance of wealth and real worth remains entrenched in management pirates the world over...