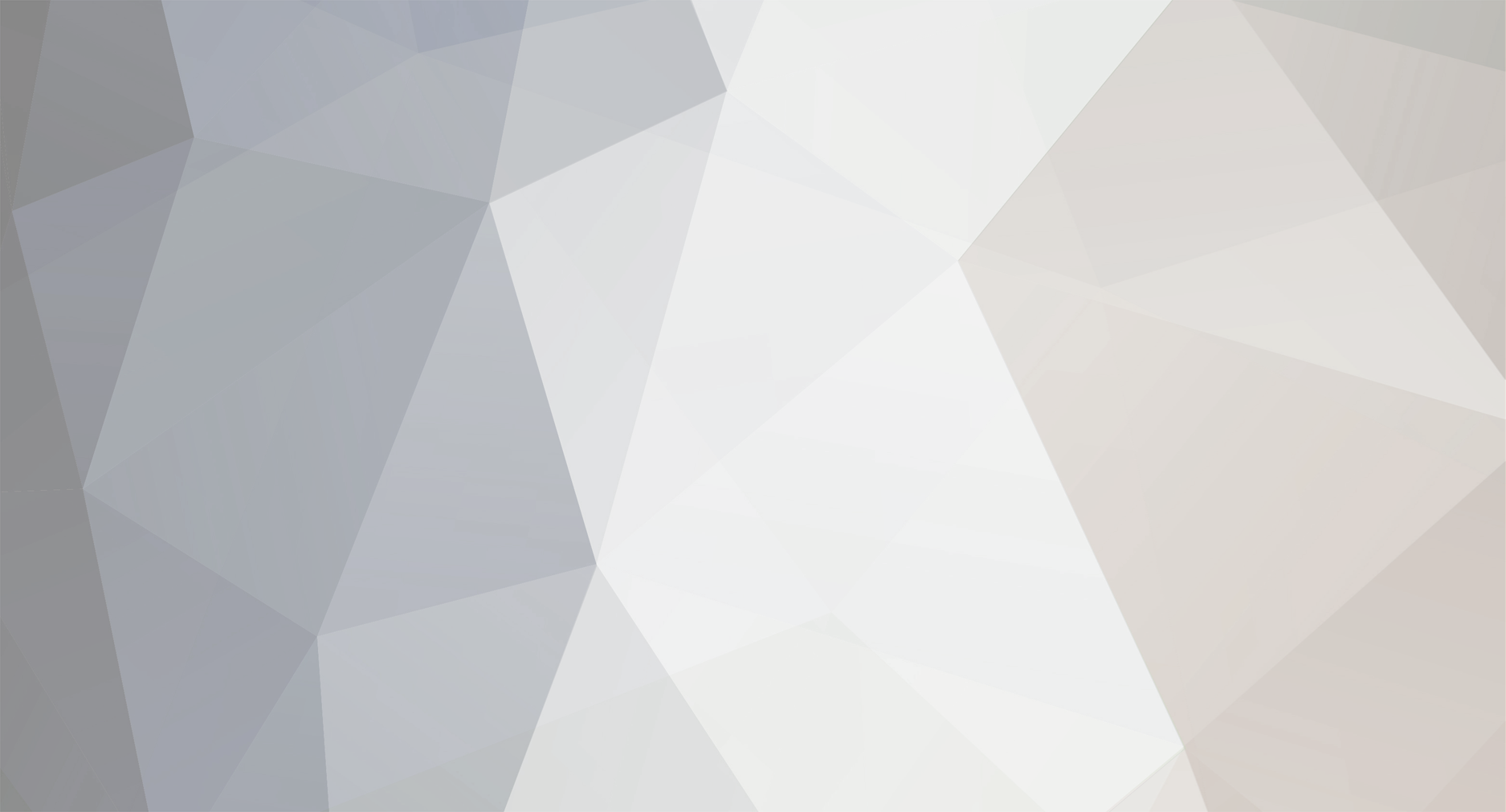
JabSP6
Members-
Posts
146 -
Joined
-
Last visited
Content Type
Profiles
Forums
Gallery
Downloads
Blogs
Events
Store
Aircraft
Resources
Tutorials
Articles
Classifieds
Movies
Books
Community Map
Quizzes
Videos Directory
Everything posted by JabSP6
-
OME , John I have a similar device fitted to my Jab 3300. I don't have to top up oil between 25hr services since fitting this device. You can make them out of different material. I have used Stainless Steel and Aluminium but you could also use fibreglass. It sits on top of the motor so the intake to the separator is right at the breather on the dipstick. The separator is mounted so that it slopes slightly back to the dipstick. Any oil that is separated during flight is then gravity fed back into the motor. I found several people were concerned about water/moisture being trapped in the canister and re entering the motor. I made mine out of Aluminium which allows for the engine heat to stay in the separator longer (heat soak on shut down) eliminating the chance of moisture in the oil. You also must ensure you have your operating oil temp above 85 degrees which will also help reduce moisture in the oil. I don't know how to attach a drawing on this post but if you PM me with your email details i can forward the plans to build one to you. Then you might be able to post it for everyone to see. Cheers Andrew
-
Gregv This is a bit of a long shot but i did hear that early on some of the bing carbies fitted to 6 cylinder engines had an intermittant problem with fuel starvation at full power. The root cause was the size of the opening in the needle/seat. The 4 cylinders didn't require quite as much flow as the 6 cylinder so was never an issue until they fitted the 4 cylinder needle/Seat to the 6 cylinder. They ended up checking the size of the opening and found by replacing the original needle/seat with a slightly bigger seat which allowed the fuel bowl to refill slightly quicker the problem was solved. It also came up as an intermittant hesitation/missfire and only happened in certain conditions, ie temp humidity etc. I don't want to lead you up the wrong path here but may be worth a look. Not sure what the original size should be but an example would be something like 2mm hole in the seat - 4 cylinder and 2.4 mm hole in the seat - 6 cylinder. This is not the right size but Jabiru would be able to give you the correct size hole. It was something that one of the blokes at Jab told me to check when i first bought my SP6 so they know about it. Andrew
-
FP It would be good to see how Clamar gets on with the floats on a J230. Any pics would be good Andrew
-
Thirsty To answer the question, No i haven't. When the valve broke i stripped the motor and sent the crank, rods, and camshaft to be tested which i believe jabiru sent to Archerfield. I also sent the engine cases into Jabiru to be bolted together and the alignment and clearances for the main bearings were checked. A new set of main bearings were fitted and Jabiru gave the cases the thumbs up. All the O rings around the Dowels were replaced but the dowels were kept. This was the recomendation from Jabiru when i rebuilt the motor. Now Jabiru give you the option of running bigger (7/16") through bolts but to do this you have to change the dowels and also drill out the mounting holes of the Barrels to accept the bigger thread. These new bigger through bolts are still only machined but should be better than the standard 3/8" bolts. The main reason i have chosen to stick with the 3/8' Rolled threads is that you don't have to strip the entire engine to replace them and will be a straight forward job that the majority of us will be able to perform without the worry of machining engine cases. One very important thing i did find out before i reassembled the engine was that none of the engine components are Balanced. I had the Crankshaft with the flywheel and propshaft extension bolted on balanced at 3000 RPM. Also the rods and the piston and gudgeons balanced. The results were quite incredible. Now the engine idles, revs and cruises quite smoothly compared to before the rebuild. Regards Andrew
-
Clamar Glad to see you found a suitable aircraft. What did you end up buying? Andrew
-
Guys As i have said earlier I don't take any of your comments negatively. They are all constructive the way i see, to arrive at the most desirable goal, and that is making these motor as safe as possible. I agree Nev that we should be focusing on the cause of the problem which is why when i broke an exhaust valve off, the first thing i did after the rebuild was to fit the MGL EGT & CHT sensors to every cylinder. It was only then that i realised that i was running too hot and too lean. I didn't jump up and down complaining to Jabiru that the motor was no good. I found the cause and rectified the problem. I improved the airflow to the heads, fitted fine finned heads, added in some ceramic coating, which together reduced head temps dramatically. I then richened up the mixtures but as a secondary measure i also installed 1 piece valves and fitted the K Liner Inserts so that no mater what happened to the motor in the future i should not be left in a situation where a valve head could break off. We have all found issues with these Through Bolts so i figured the best thing to do here to help with the safety and reliability of the motor is to eliminate the problem with the Rolled Thread alternative which was suggested by you all on the forum. I will carry out testing on the bolts so this info can be passed on to all including Rod so if anyone out there can help out with a contact for the straight pull test that Turboplanner has suggested i will forward some bolts. I will also carry out the test procedure that i have done to see how they compare and let you know. I am a firm believer of trying to improve if a problem has been identified rather than turn a blind eye and wait for it to eventually happen to me. Regards Andrew
-
Gerard I have fitted the K Liner inserts to my fine finned heads on my J3300 solid lifter motor. The original standard guides had shown signs of excessive wear after as little as 100 hrs on 2 separate occassions. I have now done just over 150 hrs since the last overhaul where i fitted the inserts and all is looking good. From all the reports i have received, including from the engine reconditioner that installed them for me, i should easily get 1000 hrs out of the K liner inserts. He has suggested just for piece of mind to replace them when the 1000hr overhaul is due but we will measure them up to see what wear there is. My heads still have the oil feed pipe going from the block to the heads and this still works as per normal in my application. Later model Hydraulic lifter motors with the hollow push rods and drilled rockers no longer use the oil feed pipe to the head. Regards Andrew
-
Turboplanner I welcome all comments especially the ones that raise question because that is the whole point of this forum. To use the vast wealth of knowledge that is available within this group to come up with the best solution. As i have said i am only new to the aviation industry and respect the opinions of those who have alot more expertise than i do in this field. The way i initially tested the old standard bolt was i made up a jig that replicated the engine case and barrels. I fitted a nut to either end of the thread and then slowly applied tension to them to see whether they would achieve a particular tension. Some made it to the required 30ft/lb and some wouldn't even do that. My understanding of the failures is similar to Thirsty's. The threads are not holding the required tension (especially when thermal expansion could increase this load) and therfore allow movement of the through bolts ultimately ending in the bolt failure. I think a straight pull test will definately indicate the strength of the bolt itself which i would expect to be higher than the standard bolt simply because we are using Grade 8 instead of Grade 5 and also the Rolled process. I will seek out somewhere to have this test performed so if anyone can help out with this please PM me so we can share the results with everyone. I have a good friend that spent 5 years working at Camet assembling these motors and he has said that it was quite normal to be tensioning up a set of barrels and find the nuts would not reach the specified tension and they would replace the nut and bolt and go again. They were not allowed to change things because they were supplying a product to the Jabiru specifications. So i believe (like many of you do) that by improving the strength of the thread in both the Nut (ARP nuts have done) and the studs (Rolled threads will do) this should put an end to the problems once and for all. I will get some testing done to confirm this and see how it all turns out. Regards Andrew
-
Maj As you mentioned, this has been discussed several times before and i have taken all this info on board and decided to find an Australian Company to source the components for us. This is a well know company and produces rolled threads in many different sizes and has their own specialised machines that do Quality Assurance Testing of the threads which will pick up any problems such as the things Facehunter has rightly mentioned. Turboplanner. I plan on having these bolts tested to see what tension either the bolts fail or the nuts fail. The old standard components have been tested and have failed anywhere from 28ft/lb to 35ft/lb. Some ARP 10mm metric studs the same length have been tested and failed just under 60ft/lb. I will let you know what we get out of these studs once i receive them. I also plan on taking a set into Rod to see if he is at all interested in the idea and will pass on the supplier details if he is. Hope this helps and will keep you posted. Regards Andrew
-
JR Mobile. Alliance Fasteners are saying that they will be up to 3 times the strength of the machined thread. The standard Bolts are only grade 5 4140 where as the rolled threads will also be using grade 8 4140 round bar. Facehunter/ Thirsty The Standard Long through bolts are just 10mm round bar with the ends machined down and a the 3/8" UNF thread on either end. The Short bolts have a 10 x 1.5mm thread on the case side and 3/8" UNF on the Barrel side. They are made at Camet on a CnC lath so, NO they are not a rolled thread. The new 12 point nuts (ARP) are a Rolled Thread. That is why i thought it would be better to have both the bolt and nut rolled thread also to improve the contact between the nut and bolt in the thread. When I first went searching for companies that could roll threads in the size required i couldn't locate any in Australia that had 3/8" UNF dies. I contacted ARP to supply but they wanted up around $500 for the set and had to be specially made and imported from USA. TJ actually imported the dies in to do this job for me at his cost. When i asked the factory why they under cut the section of bolt before the thread instead of leaving it at 10mm all the way to the thread and having a small radius just before the thread the only response i got was to improve the strength of the bolt??? I'm no engineer but i don't understand the logic in this. Anyway. Moving on. From what i understand the cases are dowelled and the bolt does not play any part in aligning the cases. It simply clamps them together. I know of 10mm bar with metric threads being used with no undercut section to clamp the cases together and it works. The only thing that had to be done was the holes in the barrels had to be drilled out slightly to give clearance for the slightly bigger thread. (10mm instead of 3/8") I believe that the reason Jabiru have not used rolled thread is exactly as you say Thirsty, COST. They can be turned out on a CNC quite cheaply in Bundy which would help keep the overall cost of the engine down. I, on the other hand, don't mind paying a bit extra for a few components to have an overall superior product. Its all about improving the reliability for me. Regards Andrew
-
Good news Forumites. Finally i have been able to source an alternative to the standard Machined Thread Engine Through Bolts supplied by Jabiru. To go along with the ARP Nuts (rolled thread) that are supplied now as the fix for the failing through bolt (machined thread) issues we all know about, i have spoken at length with a manufacturer in Western Australia and he has imported in the correct thread dies to be able to manufacture a complete set of new Rolled Thread Through Bolts. There are 10 long studs and 4 short studs to make up a complete set. They are made out of 4140 round bar and will have a much higher strength due to the rolling process than the standard 4140 machined threads that are the only option out there at the moment. He is producing the first 10 sets for me tomorrow and will hopefully post them over to me early next week. They will be the slightly longer length so that you will still have a couple of threads protruding out of the new 12 point ARP nuts. The cost of these sets are currently around the $120 mark plus postage which is a great price. The more orders he recieves the cheaper he will be able to manufacture them for as he can buy in more material at a bulk discount. For those of you that are in need of replacing the engine through bolt and would like a set to match the new ARP nuts i have included the manufacturers details and you can deal straight with the Director of the Company. TL Adlard - 0430135816 Alliance Fasteners 8 Coolibah Way Bibra Lake Perth, WA 6163 I must stress that i have no interest in this company and i am not interested in becoming a supplier of these bolts but i thought that i would pass on the information for those of you who would like to eliminate the potential of the through bolts failing once and for all. I am not the first to use the rolled thread through bolts and, as i have always tried to do, i am just trying to find ways to improve the reliability of this jabiru motor. I hope this can be of help to you and if you have any questions just ask. Regards Andrew
-
Wide Bay Australia International Airshow! (2011)
JabSP6 replied to Tomo's topic in Trips/Events/Seats
Hey Tommo Living in Bundy i will obviously be there also. It would be good to catch up will all the people that frequent this site. Look forward to seeing you all there. Andrew -
Chris After the rebuild i did have to ajust the pitch of the prop to reduce the RPM back to the recommended range. I was seeing 3550 RPM straight and level flat out. I now see just under 3300 RPM straight and level. When in cruise at around 2850 RPM i now see just under 20 lt/hr. I'm happy to have a chat if you PM me with your details Andrew
-
John It was a pleasure to spend time with you last weekend and i hope that i can share some of the things i have found to help improve our motor. I am only too happy to talk about anything that we can do to improve these potentially great motors which is why i started this thread. I am home most weekends and would love to hear if anyone else has had some good results from improving something with this motor no mater what they have done. Safe and Happy Flying. Andrew PS. John. I haven't forgotten the discs. Still waiting on them. Will send them as soon as i receive them.
-
Darren The jabiru is a fantastic plane for the price and i would recomend one to anyone as long as you get it set up right. Good cooling for the heads and not running too lean. I have done several things to get low head temps and with 150 hrs on it i am very happy with the results. Send me a pm with you details and i will discuss further. Andrew
-
Deadstick I haven't laid eyes on the new manifold yet mate but a good source at the factory tells me that they are still not seeing even EGT's across the board with this new manifold. This is why they have not released them yet. In fact they are now experimenting with a cross in the inlet manifold which has been documented on other jab sites to try to improve the spread in conjunction with the new manifold. They are trying different lengths and different positions to come up with a fix. We will have to wait and see i guess. Cheers SP6
-
Vev This is the info i was looking for. Thankyou. Can you just clear up 2 things for me please. I am looking at the diagram of the Bing Carby in the Service Bulletin JSB 018-1. You are suggesting to drill out the emulision tube to 3mm, Is this what is shown as the atomiser? You also suggest to drill out the air hole to 3/16", Is this the air density sense port? Sorry for being a pain but i just want to make sure i have it right before i carry out this modification. Once i have this info right in my head i will do this mod on the weekend and will report results on this thread. At the moment at cruise i have a difference of around 90 degress C but averaging around the 680 degrees C area. Wide open throttle gives an average of around 40 Degrees C lower. Wags
-
Nick That is the bulletin i have seen. I was just wondering if there is any way of contacting the company that does the mod to find out exactly was is done. Hopefully if we can try this mod and it works it will help solve a lot of issues and then we can work on tuning the carby to get the optimal power and ecconomy with nice even EGT's across all cylinders. Wags
-
I was just reading a forum where in France you can send your carby to a company and they modify the Emullsion Tube by drilling it out and this supposedly improves the fuel atomisation which in turn is supposed to improve the EGT spread. They swear by it and it only costs around $40 Aus plus freight. I know a few people in Aus have mentioned this and i was wondering if anyone has tried this and can shed some light on exactly what is done. A diagram of the location of the emmulsion tube and a drill size would be much appreciated. I had heard of drilling out the choke jet located in the bowl to improve cold starting, but i don't have this problem. Very interested to hear if anyone has done this mod and verified the results. I can also verify that Jabiru are now also trialling the cross in the air box to improve the EGT spread with their new inlet manifold. Hopefully they will come up with a solution that will cure this problem for all jab motors no matter what version engine or type of plane they are in. Wags
-
Mark I have a 3300 that had a similar thing happen after I had a service done. It was winter and luckily for us the temps rarely get below 10 Degrees C. The motor ran perfectly the day before with the same OAT. We had changed the spark plugs from the Irridium back to standard plugs and every morning after start up the motor used to give a cough when trying to advance the throttle quickly. This would continue for about 5 mins until the engine warmed up. After a week of this I changed the plugs back to Irridium ones and the problem dissappeared. Since then i have found that by monitoring each cylinder head temp and exhaust temp my fuel mixtures were on the lean side. I have richened both the needle jet and the main jet by one size. Motor now starts first time every time no matter what the outside temp and has never given any sign of hesitation. Just something to think about with the spark plugs. I would firstly try carby heat as others have suggested and then look at the carby jetting. Wags
-
Andy The first thing i did when I discovered the differences in CHT's was to swap the position of the sensors to make sure the Temp was in fact correct for that head and not follow the sensor indicating a sensor fault. All was good to my surprise. No matter which position I fitted the sensors the CHT's always remaind the same for the head. As all i'm trying to do is reduce the temp as much as possible and even them all out i'm not that worried if all sensors are not exactly calibrated perfectly. One thing is for sure. I have managed to reduce the head temps on my 3300 from averaging 160 - 170c at WOT and 140 - 150c at cruise to a much more pleasing 115c at WOT and 105c at cruise (average). If these actual figures are 5c hotter or lower doesn't really matter to me. The main thing is i have reduced and been able to even out the temps by fitting sensors to each cylinder and modifying the air flow to each head, and hopefully do what this thread was all about. "Help improve the reliability of the 6 cylinder Jab". Wags
-
Deadstick. I was also amazed at the hugh difference in the CHT's and the EGT's once I fitted the MGL sensors. I have spent countless hours changing the path for the air to cool the heads to achieve consistant CHT temps. I too saw temps above 700C with the standard jetting of 185 needle jet and 255 main jet. To get my EGT's below 700C on cruise i fitted a 190 neddle jet. I also had to increase the main jet to a 260 so that a WOT the temps were lower than at cruise. This seems to be working well with only a minor increase in fuel usage. My EGT's now average around 680C at cruise and 650C at WOT. I believe this is why there are so many problems with overheating. People can only see the CHT of cyl 6 and no EGT's. In my situation cyl 6 was the coolest but I also had 60 - 70 C difference in CHT temps. Wags
-
Trevoratbay. I would be only too happy to chat about all the different things i have done to reduce the cyl head temps. I live in Bundy so would be easy enough to catch up maybe at Hervey Bay. Send me a PM with you phone number and email and we can organise something. Wags.
-
Hi Trevoratbay. The cooler you can get your head temps the better mate. I have fitted an MGL gauge with 6 cht sensors and 6 egt sensors. All reports i have read and experienced myself suggests that no 6 cyl is NOT the hottest cyl. In my SP6 no 3 was about 20-25 degrees hotter and No 4 about 15-20 degrees hotter than no 6. Since fitting the sensors i have spent countless hours modifying the airflow in and out of the engine bay and around the barrels to finally achieve fairly consistant temps across all 6 cyl's. Flying out to work this morning the cht's averaged 120 degress give or take 5 degrees on full power climbout and then cruising at 4500ft my temps reduced to an average of 105 degrees. Before i fitted the MGL gauge my standard cht gauge used to read 140 on climb out and 125 at cruise which i thought was all good until i found that no 3 was 20 - 25 degrees hotter. If you get time i would suggest moving your sensor around to check all cylinders especially no 3 & 4. The biggest killer of these Jab engines is high head temps which causes premature valve guide wear and rocker bush wear, also can cause problems with the valves. Keep a close eye on temps and the lower you can get them the more reliable your motor will become. Wags.
-
Jack Anything is possible. The Jabiru Factory is at the airport and a quick phone call to them would be able to secure a time to show you around. They are very accommodating in this aspect. The engines are made at Camit which is an engineering firm in bundy on the East side of town right near the Bundy Rum Factory. This would top off the day to go thru the rum distillery after visiting the Engine shop and Jabiru. I live in Bundy and if i'm in town when you are coming i would be pleased to show you around. Andrew