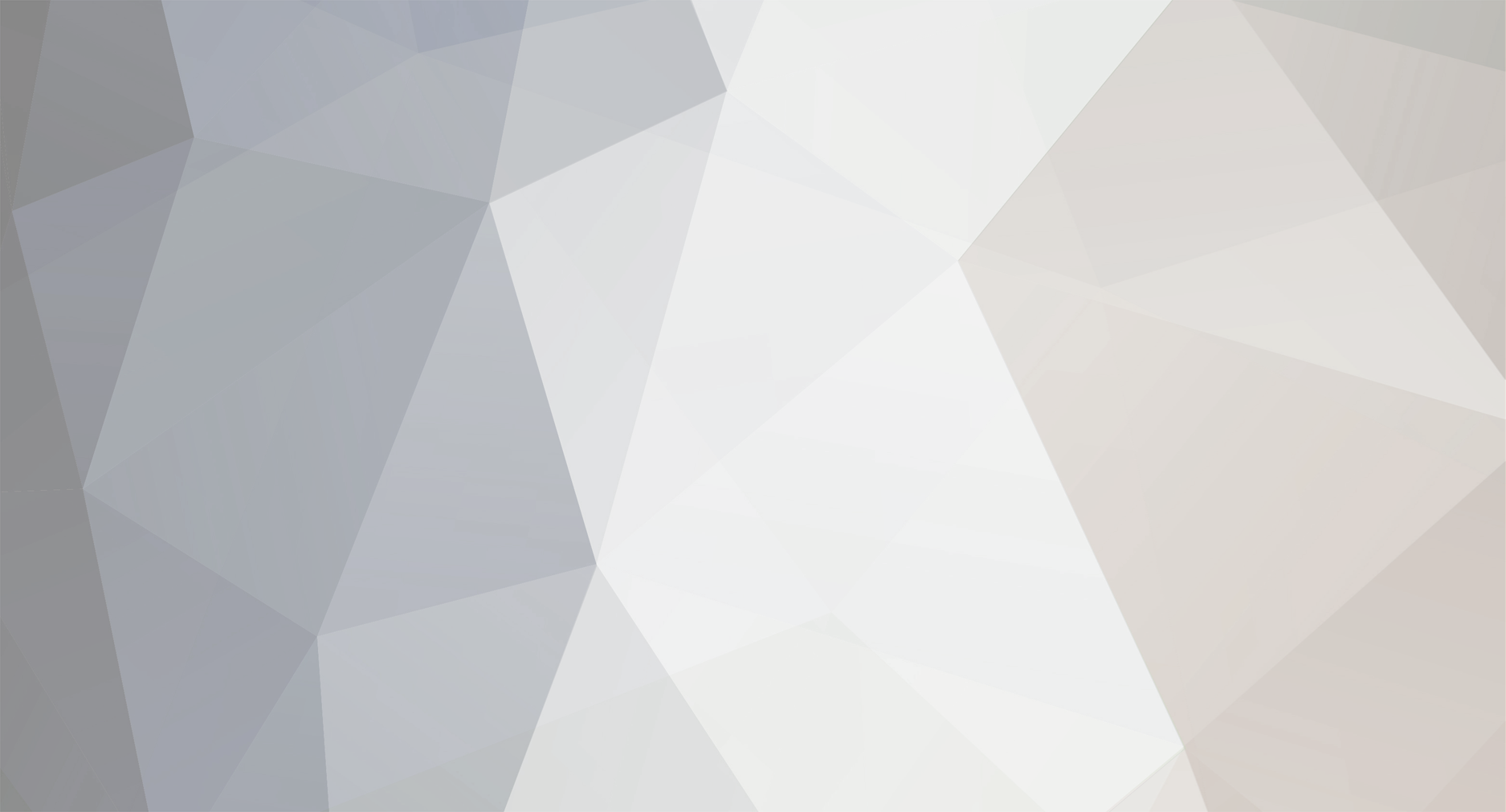
duncan_rtfm
-
Posts
78 -
Joined
-
Last visited
Content Type
Profiles
Forums
Gallery
Downloads
Blogs
Events
Store
Aircraft
Resources
Tutorials
Articles
Classifieds
Movies
Books
Community Map
Quizzes
Videos Directory
Everything posted by duncan_rtfm
-
-
During SEQ's lockdown I've been champing at the bit, because I have been waiting for a wood delivery to carry on work on the Fleabike. So, with nothing else to do, I have designed a new plane - this time a fully enclosed single seater.
I've decided to build it with the cedar strip canoe method. I have watched a huge number of Youtube videos of people building strip canoes, and it all looks reasonably straightforward. However, all the online builders are working from plans, and don't have to make any design decisions.
My first design decision is how far to extend the front "keel". It has to accommodate a 225mm diameter ring (to allow air into the engine compartment, and to provide for the prop shaft). I don't actually know how to build this.
This is what I've come up with so far...
I'll build the fuselage in three sections. The green section is a fairly straightforward "canoe". The yellow section is a single piece cowl/engine covering. And the orange section (as you can see) comprises the roof and the turtledeck
Do I run a keel along the entire length of the green section? And the yellow? Or do I do this for all three sections?
Are there any canoe builders on this forum who might be able to help with this?
Regards,
Duncan
-
OK - the Fleabike fuselage is complete, windshield added and all sanded down. Any suggestion regarding how to paint the Bike?
I have some 117 fairing additive for West system, and I thought I might roll that on, sand it back and paint with West + pigment (white). I'm leaving the control panels, seat, seatback (i.e. the upper central spine) natural wood, but painting the rest.
Is there a better way?
-
Question:
After wasting about an hour (and two cups of coffee) on the laptop searching for suitable fuel drain plugs, not a single manufacturer/distributor cares to specify the diameter of the thread going into the fuel tank. It seems I am looking for a 1/8" NPT, but I need to know what size hole I need to cut into my tank to accommodate this. Any ideas?
Duncan