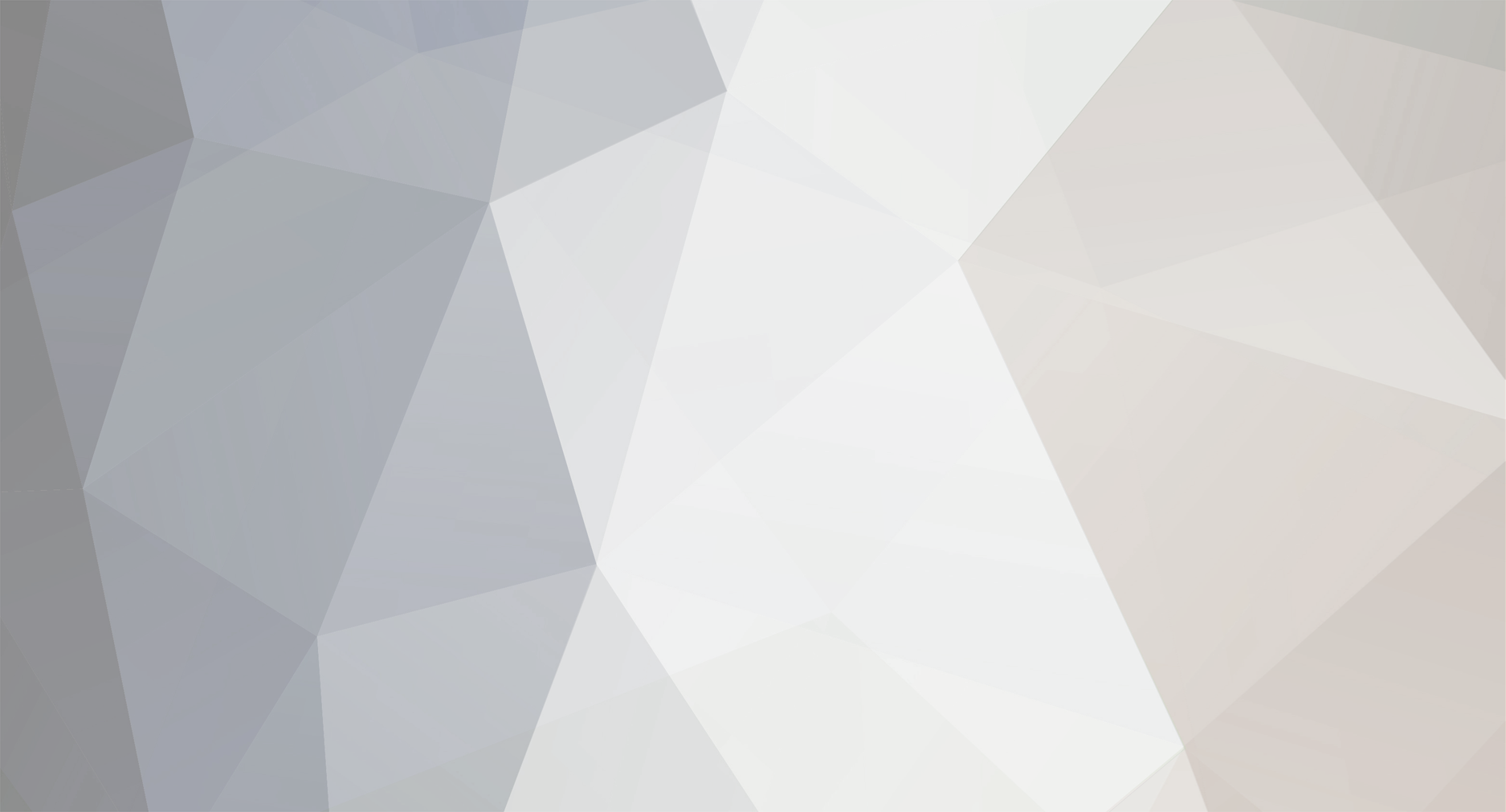
damkia
-
Posts
605 -
Joined
-
Last visited
-
Days Won
3
damkia replied to 68volksy's topic in AUS/NZ General Discussion
damkia replied to motzartmerv's topic in Aircraft Incidents and Accidents
damkia replied to a topic in AUS/NZ General Discussion
damkia replied to motzartmerv's topic in Aircraft Incidents and Accidents
damkia replied to motzartmerv's topic in Aircraft Incidents and Accidents
damkia replied to motzartmerv's topic in Aircraft Incidents and Accidents
damkia replied to motzartmerv's topic in Aircraft Incidents and Accidents
damkia replied to motzartmerv's topic in Aircraft Incidents and Accidents
damkia replied to motzartmerv's topic in Aircraft Incidents and Accidents
damkia replied to motzartmerv's topic in Aircraft Incidents and Accidents
damkia replied to motzartmerv's topic in Aircraft Incidents and Accidents