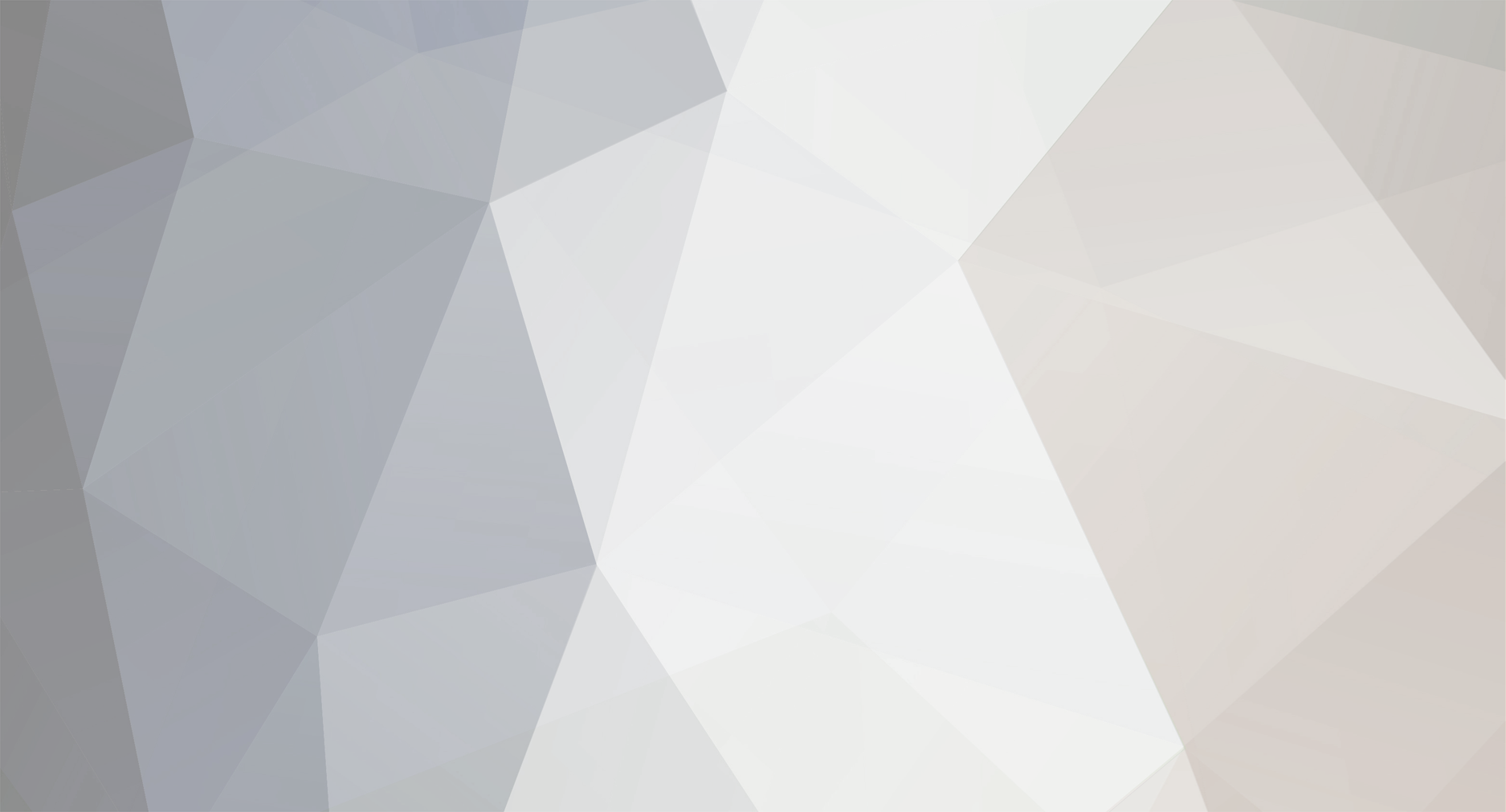
Oscar
Members-
Posts
2,485 -
Joined
-
Last visited
-
Days Won
67
Content Type
Profiles
Forums
Gallery
Downloads
Blogs
Events
Store
Aircraft
Resources
Tutorials
Articles
Classifieds
Movies
Books
Community Map
Quizzes
Videos Directory
Everything posted by Oscar
-
Brumby Signs with Chinese Aviation Giant
Oscar replied to Motif's topic in AUS/NZ General Discussion
GW: if you have better knowledge than a CASA accredited Test Pilot and the Aero-engineer responsible for the certification of, amongst others, the Gazelle, Jabiru LSA55 through to 160, Sunbird Seeker, AND the FAA Light Aircraft Division Chief Test Pilot, I salute you. -
Brumby Signs with Chinese Aviation Giant
Oscar replied to Motif's topic in AUS/NZ General Discussion
You are talking VGs. IF they are installed correctly - and that is subject to proper flight testing - theycan be bloody good. BUT: do not be deceived that they can just be chucked on and will work as expected. The Sunbird Seeker with properly-installed VGs, was reported by the FAA 'Light Aircraft Division' test p[ilot, to be 'perhaps the best stalling behavious aircraft I have ever tested - and the FAA should consult with (Dafydd Llewellyn, who did that work) to derive specifications for VG installs (paraphrased). The implicit message there was: even the FAA does not know how to best use VGs - go talk to someone who does. Now here's the evidence: When the FAA test pilot came out to run the Seeker through its paces, it showed a serious wing drop at extreme crossed-control stall. Contrary to the test flying results. Sunbird got back to Dafydd Llewellyn. It transpired that Sunbird had re-painted that aircraft, removing the VGs to do the re-paint for the job, and had re-installed one of them around 1/2" out of position. It happened to be a critical one. With all VGs in correct position, the Seeker can be flown at just above the stall speed, level, at nearly 20 degrees of yaw angle, quite happily. I have flown that test aircraft, and even to me as a novice power pilot, it was incredibly easy to control in attitudes that one would not hope to contemplate in most aircraft. It was designed to do Power Line Inspections with a forward-facing camera, at low speed and very low altitude: the job normally done by Helicopters. It succeeded in that - having only NOT the ability to hover. This is NOT a rant against VGs: they are marvelous aids to low-speed control PROVIDED that they are correctly installed, and they do not detract from cruise speed.. BUT: if incorrectly installed, they can produce a result that they hold control down to an airspeed below which separation is abrupt and violent. You need to take into account not only the wing spanwise airflow to ensure that the centre section stalls before the ailerons, but also that the downwash from the centre section does not affect the elevator authority. -
This is a MOST important and cogent point (my bolding). BOTH Jabiru AND CAMit hold (or for CAMit, held) Production Certificates issued by CASA, in their own right as companies. While CAMit operated purely as a contractor to Jabiru, it was not required to hold its own Production Certificate: Jabiru had the sole responsibility for its engines. However, when CAMit started production of parts and engines in its own right, it required a Production Certificate in its own right. Several years ago now, the Jabiru N.A. dealer made a public comment that it was entirely CAMit's responsibility for the quality of Jabiru engines. This was entirely incorrect, and CAMit came out with perhaps the first public statement ( as far as I can remember) of the facts as to where its responsibility - and for that matter, control - of the QA/QC issues, lay. It was a detailed response and pointed out a number of components for which it had NO responsibility, including pistons, valves and valve train components: it was required to use, under operation to Jabiru's Production Certificate, components supplied to it BY Jabiru for the assembly of engines. In the case of raw materials - for example, the 4140 steel used in crankshafts, cams, rocker gear, or the billet alloy used for crankcases, heads etc. that CAMit produced, the material had to be sourced from companies that had 'Release Grade' QA/QC of their own. You don't get that from your local OneSteel store. You have to buy in quantities dictated by the manufacturer. There are some suppliers that deal in smaller quantities - e.g. in Australia, Performance Metals is one that will sell 'cut' quantities of Release Grade material complete with the requisite Release Certificate. Aviall ( a Boeing company) is another for aerospace manufactured components. They have to charge for the paperwork associated with selling those with Release Certificates - and it isn't cheap. For example: I have some Blackhawk rotor-blade connecting bolts, ex- BAE. MS20008-18. I think, Grade 13 quality, in Release Grade. They are 1/2" diameter, fine thread, just less than 2" in length. They are available in single quantity from a number of Aerospace suppliers, at around $250 a pop..yes, that is Two Hundred and Fifty $$. With a properly-designed link, you could lift a fully-laden B-double with one of them. Bought Release Grade Cherrymax rivets lately? 1/8" x 1/4" pull, about $2.25 each. You can buy a plastic box of 100 3.2mm x 6mm pull pop rivets from Bunnings et al for about $7. As a Manufacturer, you have to record not just the details of the material used, but in which product you have used them - and keep those records safe. If a Jabiru crankshaft - for example - fails through a metallurgical fault (I don't believe any have), then it is possible for Jabiru (through CAMit's records, of which presumably Jabiru has a copy) to identify ALL the crankshafts produced from that batch of material, which engines they were installed in, and initiate a recall. We see the same basic control mechanisms in operation every day, when there is for example, a recall on a batch of packaged small goods sold by a Woolies or Coles. That is QC in action. As a society, we not only EXPECT, but DEMAND, that level of protection. I have no problem with that: I will be bloody annoyed if the packet of sausages I buy from a supermarket contains fragments of glass that kill me. But: that packet of sausages was probably one of many thousand sold nationally every damn day. And, it contained a (probably disgusting, though I don't want to know) melee of ingredients, most of which had NOT been subject to QC inspection. Now, think about the situation of an aircraft, or aircraft engine, manufacturer with a production run on the hundreds, or perhaps low thousands, over maybe 25 years. With literally hundreds of components - ALL of which had to be measured, recorded. Have you ever looked closely at your Jabiru (or other) engine? You will find inscribed marks identifying a lot of the major components: the crankcase, the shaft, each head etc. I will guarantee that I can take a head off my engine and it can be traced back to the batch of material from which it was made - and from there, it can be traced forwards to any engine that had a head from that batch incorporated. That is the QC that you get from the requirements placed on the manufacturer. As an example of how this works: when Rotax issued SB's on its crankshafts, it identified the engine serial numbers affected. That was no wild guess - it was a result of the recording of materials, processing etc. And it affected thousands of engines. The QC back-up that you fly behind, every flight, is not accidental - it is mandated. And the cost of that level of protection has to be included in the manufacturer's costs of production. The requirements of that apply to every manufacturer. CAMit, with some 160 CAE-badged engines produced, had to meet the same standards as Rotax, with over 50,000 (aero) engines produced..And CAMit had to be able to prove the same QA /QC for engine #1.
-
I think it was Bell Helmets who used the advertising slogan: 'if you have a $20 head, wear a $20 helmet'. I agree with Bex: you get what you paid for, and if you paid cheaply for something to help you do a specific job efficiently and it does that job, then you have recouped your investment. If you buy say an Ozito 9" circular saw that says on the box: 'for light duty only' and expect to rip hardwood sleepers down with it, then you are a fool. I had a much-loved Metabo variable-speed 125mm angle grinder, that I used almost every damn day, because I do a lot of metalwork. Expensive: over $400 to replace. I never used it as intended (including running a 9" 40-grit sander disc); when I had worn out three armatures and then when I could not get a fourth replacement, I went ballistic on Metabo's Australian distributor's a8se. The Metabo rep. listened to me and said - calmly - 'well sir, it is over 14 years old, and we are only legally required to have spares for five years.'. Exit Stage Right, embarrassed... What has this to do with CAMit? It has to do with the underlying ethical basis of the manufacturer. If an aero engine fails in flight, the consequences could - have - been fatal. 'Safety is our highest Priority' is perhaps the most debased phrase used in recent times by every manufacturer of ANYTHING when a failure results in a fatality. FFS, look at Samsung: washing machines catching fire, phones exploding... Apple: batteries exploding. VW: fatal shutdowns of engines. GM: fatal consequences of a known dodgy ignition switch. Takata: air-bags. Ford: Explorers rolling over, and famously, Pinto's frying their occupants in a rear-ender. Earlier Holden Commodores tearing apart in accidents.. The deaths just from domestic appliances / defective motor vehicles, makes the entire Aviation industry look like a side-show. For many, many companies: 'Safety is Our Highest Priority' is so obviously a monstrous piece of hypocrisy, trotted out when things go pear-shaped. If they are producing say, electric drills - 99.9% of failures do not result in anything more than customer frustration.. If you are manufacturing aero engines, you KNOW that a failure may kill people. You can put the usual warnings on the boxes and in the User Manuals: hell, Rotax used to ship 503s and I think 582s with an explicit statement on the carton 'Not for use in Aircraft'.. Let's not kid ourselves: that was NOT intended as a restriction in the interests of safety, it was intended as an 'out' in the case of legal repercussions from failure. CAMit - a very, very 'boutique' manufacturer in terms of its market presence - took its responsibilities to its customers seriously. Its CAE engines had all of the QC and testing and recording done to certification standard. When a CAE engine had a problem - due to the failure of an oil-cooler hose having been used that failed (which is an installation problem,. not an engine problem), CAMit rebuilt that engine for the owner at the parts cost. The failed hose that allowed the oil to be pumped out, was sourced from an Asian supplier from a country I will not name due to Bex's sensitivity to mention of the source. It is oh, so easy to criticise a company for failing to be commercially successful because it placed its ethical considerations ahead of its commercial interest. For those - and Bex - you are one - who take the view that commercial success is the sine qua non of good business: how about you jump off the North Col of the Matterhorn relying on rope that has the best profit ratio to cost? Or would you actually choose the best QUALITY rope available?
-
Brumby Signs with Chinese Aviation Giant
Oscar replied to Motif's topic in AUS/NZ General Discussion
As a matter of interest: can anybody tell me how many aircraft Bumby have sold here sine the Chinese acquisition? -
Bex, Jab. found the fault, re-machined the pistons, and (twice, AFAIK) re-built the engines they had in stock to try to fix the problem: the first time, to replace the pistons with correctly-centred circlip grooves with pistons they had had re-machined to concentricity., the second, to replace the damn circlips that were no longer adequately tensioned on the new, larger diameter grooves. I won't bother to go into the fine details; you can read between the lines in the Jab. service bulletin regarding circlip installation. I can only assume that the contract price for the pistons did NOT include a guarantee of QC. I don't believe Jabiru looked at a sample piston from its Chinese supplier without examining that it met specifications and then blindly ordered 5,000 of them. Jabiru does not have the calibre of measuring equipment that CAMit had: laser-table measurement in a climate-controlled room. Jabiru relied on the QC of its supplier - and that was faulty. CAMit measured EVERY component it made before releasing it to assembly.. That adds a significant cost to the production cycle. Jabiru did not contract CAMit to measure those pistons; they were supplied to CAMit to install. Scale of operation makes economy of non-measurement viable. I believe that Briggs and Stratton simply assemble every engine they produce, run them on a test cycle before releasing them and simply scrap any that d0 not measure up. It does NOT measure every component: cheaper to throw away the duds than worry about ensuring that each part of each engine was good before it was assembled.. Rotax fairly recently mandated a crankshaft replacement for thousands of its 912s. You claim I always bag Chinese manufacture. That shows to me that you don't read all of my posts: I have quite a bit of Chinese-manufactured tools etc. in my workshop, and many of them give good service, but I do NOT expect them to be of the quality of the Metabo, Fein, Festo, older AEG, Stahlwille, Snap-On, Moore and Wright, Mitutoyo, Minimax, Starret, Smart and Brown, Makita, Elu, Robland etc. tools I have. And I accept that I pay two-three-four times for those, than for the Chinese tools I also have. I will happily buy Chinese-manufactured tools to do a specific job and accept that a few of them won't cut the mustard. I buy the expensive stuff to do long-time/high precision service, because I know I will be using them in 10 - 20 years on.. I don't expect a cheap tool to do that duty. For example, I recently bought a Chinese light-duty air-hammer for $35 to drive flush solid rivets, made up the drive tool necessary for the actual job, and if it does the one job I need it to, it will be value for money given that anything for that job from Aircraft Spruce costs over $250. I can't foresee recouping the investment of $250 for a small, one-time job. And - it is doing a fine job so far - a bit crude but with careful attention to use, as good as the 'real thing'.. The difference between a $40k engine from Rotax and a $10k engine from the Happy Joy Luck Engune Factory, is at least in real terms: reliability due to QC. And - you need to pick the right Rotax:.. Quality is NOT unilaterally geographically centred. The entire UK motor vehicle (including motorcycles) went belly up because they were producing CRAP. Including from Rolls-Royce down. Yet, the UK was at the same time, manufacturing Gardner diesel engines - there were none better from anywhere in the world, and Smart and Brown Lathes, only bettered by Schaublin.. When it's good, from China, it's definitely world-class; when it's bad, it's just plain bad. Not 'Chinese' Bad, just, BAD. BMW have produced some vehicles that quite possibly make the Cherry look quite reasonable. HOWEVER: when you are flying over tiger country and the engine plays dead ants, will you be happy to say: 'oh well, it was cheap, mea culpa for buying it?' And that's why CAMit's dedication to quality, would be an investment you would happily have paid, if your nearest and dearest is in the RHS.
-
Folks: with all due respect for the importance of ethical and sociological aspects of where this thread has gone: what relevance does it have to the fact of CAMit shutting down? CAMit was Ian Bent, and it had very, very good support from everyone who had dealings with it. I happen to know that Ian's family was 100% supportive and trying to keep it in business; can we just look beyond the 'three degrees of family separation' stuff for the moment? I have already had indications from Jabiru owners that with CAMit gone, they will bail out (financially speaking) from their Jabs. They love the airframe but don't have faith in the new Jab. engine as a future powerplant. I don't have a better rationale for this than they have seen CAMit as the ultimate security for their flying; and I am inclined to share that perspective. I personally won't be looking to Jabiru's Chinese engine as a replacement - I'll rebuild my own Jab/CAMit hybrid as long as I can find reliable parts.
- 287 replies
-
- 12
-
-
-
-
The Petrel landing gear retract restraint system is crap; it won't hold fully up under normal manoeuvering loads. However, Petrel's own POH says if there are gear problems, land with gear up on the grass in preference to trying a landing with suspect gear safety on bitumen. You have a better chance of dumping it on the grass, than landing on water if the gear retract system is not working properly - and if the gas strut that is the primary uphold is failing, a less than perfect water landing will break the aircraft and sink it. http://www.16right.com/MessageBoard/Queens%20Lake%20IMG_7520.jpg
-
Rotec does not -AFAIK - have a CASA Production Certificate. CASA does not hand those out with Cornflakes packets. If you are happy to go with Experimental, not a problem, but if you want to train, fly into CTA, put your aircraft on the line for hire - you need a certificated /certified engine.
-
Off topic - but: if it's a Chinese compressor, the two areas to check are the valve 'petals' in the compressor head and the head bolts. Typically, Chinese stuff is actually good design and manufacture, let down by some bugger in the manufacturing plant trying to save a few cents by substituting crap parts. I will happily buy Chinese stuff but expect to have to work out where the 'weakest link' is and fix it - and then, I get good performance at the home handyman level. Have to admit that, for close-tolerance work, I don't go near Chinese: my mechanics tools are mostly Stahlwille and Snap-on, my measuring tools are .Mitutoyo, Starret and Moore and Wright. Good tools are a joy to work with.
-
Mark: quite correct for the physical parts, but you need to factor in that the QA systems must meet standards ( ASTM or certification mandated) - for Jabiru certificated engines (mostly the 2200C), to be acceptable. For aero engines (or airframe parts, for that matter), the QA is quite extensive, starting with the release certificates for the raw materials. If I had a copy of the CAM files for - say - Jabiru rods, I could take it to my local CAM-capable workshop. and they could make up a part that was in every physically measurable respect, identical to OEM. BUT: it would not be an acceptable part unless it could prove the total QA chain. If I substituted it in my engine and the engine failed and there was a crash which left third-party injuries - my insurance would (correctly) refuse me coverage. It's precisely this reason that - for instance - you do not substitute AN bolts with allegedly equal-spec bolts from Bunnings (which I am sure you would never do!). Example: I have a 'Proudly Australian Made' air compressor - Peerless brand. They don't mention that it has a Chinese-sourced compressor.. Ran less than 20 hours before being unable to deliver more than around 35 psi. Went looking for the problem: the 1/4" UNC head bolts - marked as Grade 8 - pulled their threads at around 4 ft/lb. Cheese quality. Replaced them with reliable Grade 8s torqued to about 12t/lbs and immediately it went to 110 psi no problems. Have several thousand hours on it now with no problems.
-
Nev - didn't 'Grumpy' (Don Garlits, IF I remember properly) run a drag engine with liquid sodium cooling in a virtually solid block about 30 years ago? Solid is ok for 6 seconds or so...Not really enough time to get you to turn-back, even with a vertical climb...
-
Nev, the best drag engines I know of made in Aus. are produced by Phil O'Brien - a 1600 cc drag-bike engine that makes around 1000 hp, I believe!. It's all billet and CNC manufactured. Typically last a complete season without re-build.. As you would know, the critical factor in a split crankcase is reliability of the main bearing bore tunnel. Two factors important: the first being compression under assembly load, the second being any lateral movement between halves. The standard Jab. assembly uses Loctite as a sealant - and requires (amongst other things) an assembly technique of precise timing and close control of ambient conditions. I've watched Jab. engines being assembled at CAMit, and it takes two well-trained people to get it right. Jab. engine design uses hollow dowels between the cases, the through-bolts run inside the dowels. The CAE engine uses the through-bolts as the dowels. The difference being: cumulative differentials are one order for the CAE engine, two orders for Jabiru engines. I can verify from personal experience that the CAMit tolerances were sufficiently close that you could not assemble a CAE engine if ALL components were not at the same ambient temp.
-
When Rod Stiff first looked at casting as a process (and tried it with the 1600 engine), the Australian alloy casting industry could not meet quality standards. The only Aerospace capable foundry - CAC - had shut up shop. Only very recently has another foundry capable of aerospace-quality started up in Australia. CAMit's position was, that the amount of machining needed on a crankcase for a cast product necessitated a similar investment in machinery, and given the reject rate of castings for sumps being experienced, it was commercially better to utilise that machinery to produce reliable crankcases than to have to throw away dud castings. Why would Rod have ceased production of the 1600 engine after 65 or so examples if it had been successful? I can show those interested a 1600 crankcase that is utterly useless post-machining, due to the casting problems. In order to meet the requirements for a training-capable aircraft, the early Jab. 2200 engines had to be certificated; Jabiru (like Rotax at the time) chose to go with JAR22h. The J2200C engine was certificated to the same standard as the Rotax 912A ( I think it was - the first 912 series, 80 hp.) Certification required QA standards and a manufacturer's Production Certificate issued by the National Authority responsible for implementation of the International standard - CASA. Jabiru did not hold a PC for casting and no Australian facility could have filled that gap.
-
Quite, quite incorrect. In an surface-to air transfer situation with forced air induction giving high airspeed, a rough ( i.e. cast) surface will produce a deep laminar flow area and negate the rate of heat transfer. 'Eddy heat transfer' is a complete furphy in the case of surface-to-air heat transfer..
-
Since when was 3.6K the same as 4K?
-
4K rpm? Horsedung. But what would I know? - only had personal experience of the Buick and Packard Straight-8s. Haven't had a ride in the local Stutz Straight-8 Sedan, it could be a screamer for all I know.
-
My family owned a 1938 Straight 8 Buick in the 50's; engine no problem (other than its drinking problem; the only car I've every had that was thirstier was my XJ12, which could get as low as 4 mpg if given the berries.) I also owned a 1938 Packard straight-8 Hearse - and it went rather well; I used to drive it between Mittagong and Canberra and the look on other driver's faces when you passed them doing around 80 mph would have kept me in petrol if YouTube had been around.in those days. But the Packard was splash-feed poured big-ends and it ran several going up Red Hill with 13 (live!!!) Duntroon Cadets in the back, also at nearly 80 mph. It had been a good party, that evening. http://www.hearse.com/images/to_file/robers01.gif My mother once drove a Packard Straight-8 convertible between Geelong and Derrinalum and averaged 90 mph for the trip; her obnoxious passenger had to be hosed out of the left-hand seat at the end of the trip. With one rod per throw and a main every throw, the Jab. 8-cylinder was a long engine with a very light shaft. Twisting of both the shaft and the cam was always on the cards. You have to look at the necessary cylinder spacing for an air-cooled engine to appreciate why the Jab. went one main per single rod, and Jabs. have an excellent reputation for their bottom-end strength - shafts have never been an issue. But the 8 pushed that to the edge. If you don't understand why, then you don't understand the dynamics of an engine. Alfa Romeo in the '30's tackled that problem in the 8Cc 2900 by joining two supercharged fours in the middle, with two separate shafts and cams joined in the middle with the cams chain-driven at the middle. The famous 'Batmobile' Le Mans coupe was the first vehicle ever to make 200 mph down Mulsanne. A restored 8C coupe in South Africa blew a newly refurbished 4.2 E-type into the weeds in the early 60's. Alfa Romeo 8C 2900B Le Mans Berlinetta (Chassis 412033 - 2010 Goodwood Festival of Speed) High Resolution Image The Straw Boater hat worn by one of the 'Batmobile' drivers at Le Mans was, I believe, conceived as a bit of a joke..
-
When I was flying gliders years ago, I used ONLY non-polarised glasses - Aviator style with Zeiss Umbral brown tint-lenses, from OPSM that made them up at a very reasonable price. Every serious glider pilot used them - because you spend up to 8 hours flying in the bright sunshine and they were the only lenses that didn't distort the ground colours and didn't leave you with eyes that felt like they'd been sandblasted. They were the German Navy tint for warships in WWII and highly-prized. For flying, I find the Aviator style the best - they didn't happen by accident.. That's all I have worn for about 50 years now... Bought a pair of Ray-Ban Aviators and had them changed over to the Zeiss Umbral lenses ( non-prescription) - very, very expensive - about $450 in FY 2000. Probably around $800 today; I don't want to think of the price for prescription ground glass Umbral lenses... The Bloody Ray-Bans dismantled in the frame after about 12 months, and I spent years sailing/racing yachts where glass lenses are extremely bad news for keeping your eyeballs intact.. When I started to re-learn flying a few years ago for Power flying after a long time away from flying anything - I found I could not read the instruments on the panel, my short-distance vision had deteriorated too much. Not good. When your Instructor asks you why you had not back-tracked to the airfield and you have to admit that you can't actually see the compass properly - other than as a round thing on the panel- it's a reality check. My long-distance acuity had also deteriorated, though I'd not realised that when driving /riding. So I went to an Optometrist and had my distance vision correction and close-vision correction checked and listed, then went to Zenni Optical and had a pair of dark-tint brown, a pair of light-tint brown and a pair of clear bi-focals made, in Aviator style, for around $15 each posted to here. And they are EXCELLENT quality, the frames are better-lasting than Ray-Bans and the lenses are very good. They are delivered to Aus. in about 15 days after ordering. However: I immediately had problems with my flare (or round-out, choose your terminology) height in a J160 - when I pulled up the nose, I lost sight of the runway ahead and had to judge by checking to the side - and the bi-focal transition makes that very, very hard. With familiarity with the change, it gets easier; I've had no problems with driving or riding the bike. I haven't tried transitional lenses, I worry that my judgement of closing distances will be distorted by the angle of view; with the bi-focals, you do know whether you're looking through the close-focus or distance prescription.
-
If that fit-up was done at the Jab. Factory, I saw it just before it was ready to fly - very, very nice job of building the RV-7, too, and the installation was looking excellent. He must have had it propped just right (and flown it with good sense), as there were potential issues with crankshaft harmonics and twisting over the long shaft. An RV7 isn't a lot of airplane to be hauled along with that much grunt and there should never have been much of a need to flog the thing too hard. I don't think they would have lasted well at all if flown by someone in an unsympathetic way or in a draggy aircraft. Too much (or too big in diameter) a prop. would have caused problems with the standard Jab. prop. hub but the RV7 can't carry - and doesn't need- a big prop AFAIK.. Cooling should not have been a huge issue; with the heads 'paired' as per the 2200, only the 3-5 and 4-6 heads would have had the exhaust ports alongside (as happens in the 3300 anyway) and while the head bolts do restrict the airflow down to the exhaust ports somewhat, that is workable with attention to the cooling set-up. With CAMit gone, there's no chance of getting a new replacement crankshaft (or even a crankcase) if they fail; AFAIK everything else was standard Jab. parts apart from the intake and exhaust runners, obviously - and could even have been bought up mostly to CAE specs with (very careful!) hand-drilling of the crankcase to accept the CAMit through-bolts, barrels and heads. CAMit could have even installed the piston-cooling jets in the crankcase.. Sadly, with CAMit gone, your mate had an engine that has to be considered 'no user-serviceable parts inside', so his aircraft is now an airframe with a thing out the front that is a dead engine walking... Good on him for having the courage to try a new engine, and it's great to hear he has had a good run with it. CAMit had the capability of supporting 'bespoke' variants, Jabiru does not. There is no Rotax equivalent, nor Ul power or d-motor, so it's Lycoming or Continental, and that's going to involve not just the raw cost of the engine but the mount, prop, cowl mods etc.
-
But fin area is entirely relevant to the airflow past it. In the CZ examples, there is no p--delta, the fin area works in ambient. That is NOT the case for (most) aero-engines.
-
Nev - it's not the source that's the likely Archilles heel for the Jab 'Chinese engine' - the Chinese can do excellent work, though their QA can be a bit iffy. But the Nanchangs, for a start, are bloody good aircraft and as hi-tech for the class as anything. Look at the number of fins on the Jab. Chinese heads: from the Ozkosh photos, I count 15. Look at the number of fins on a current Jab. (or CAMit) engine: from the Jab. website, I count 20. Cooling capacity is mandated by the area available to the airflow. My Series 1 heads - the first used on J2200 engines - has 15 fins. The first 2200 engines worked ok for a light aircraft, flown with good regard for engine management, on 100LL. Do the maths. If you are flying a 600 kg MTOW aircraft on a warm day on even 98 MON (more likely to have deteriorated to around 95 MON) to the same flight profile as would work for a 430 kg MTOW aircraft on 100 RON - what's the potential for detonation (let alone excessive chts.?.)
-
CAMit was fairly rapidly (in terms of the overall market, world-wide) developing its market. CAMit engines (and service) are very popular with the Sonex crowd - witness the OEM agreement with Sonex, who build their own VW conversions BUT were smart enough to recognise that there was significant demand for the Jabiru engines and in the CAMit engine they had access to something that was being enthusiastically received by Sonex builders as a great match to their high-quality airframes. And Sonex have, I believe, well in excess of 1000 airframe kits sold. If I didn't own a Jab., a Onex with the CAMit 3300 engine in it, would be an absolute hoot as deeply personal travel device (aka drill holes in the sky for the sheer thrill of it stuff..). The CAMit engine in the Bathawk was ASTM-certified (not sure of the details there, but Bathawk was prepared to put its 'manufacturer' status behind the CAMit engine). Bathawk doesn't have huge numbers of aircraft out there, but it is gaining a reputation as a damn useful workhorse in its area - even to the point of being armed! It performs much the same role as the Seabird Seeker (another excellent Australian product, sadly now lost to overseas interests.) It is easy to criticise CAMit for having been 'over-capitalised' for the market situation in which is found itself in the last few years, and I would agree that had Ian Bent been a ruthless businessman he would have contracted (in the sense of reduced, not put out to contract) his operation to fit the circumstances. Machines could have been shut down, or disposed of, staff could have been laid off or put on reduced hours. That's easy to say, looking in from the outside - though it didn't work for Chrysler Australia, Ford Australia, Holden... and those are companies with pretty damn ruthless cost management ethics. Anybody remember the UK car manufacturing industry? I read last week that Ford USA have shut down one plant that manufactures Mustangs.. I have personally spent some weeks in the CAMit factory, got to know a lot of the people there and I would have refused to be the person walking down the floor telling a bunch of terrific people which ones were no longer required. Being a decent bloke may not be alpha-level business practise, I accept, but some of us place a value on being able to go to sleep at night without dealing with the trip that we are going to shaft someone (and his family), the next day. Jabiru itself - as Rod Stiff and Sue Woods have stated - is running at minimal production and there have been some rumored problems there for airframe production as well in the last few weeks. Hopefully, those are unfounded rumors. As a Jabiru owner, I state once again that the airframe they have produced and the general level of service that they provide is something for which Australian aviation should be monumentally proud and supportive. However, I state for the record that I do NOT believe that 'the Chinese engine' will be a successful retro-fit into existing Jabs. It may well perform adequately in new Jabs. with an optimised installation, but for technical reasons to do with especially cooling capacity of a cast-finned engine, as a 'drop-in' change-over for older Jabs. it won't cut the mustard. That has NOTHING do do with the sourcing, it has to do with basic physics. If Jabiru offer it as a replacement with a complete FWF kit - more likely to work well. The CAE 'core replacement' engine was developed as a drop-in package. It would be ingenuous to say that it would not have been even better with a better installation set-up than Jab. provides as standard, but amongst other things, it provided better 'headroom' for CHTs due to better alloy. A lot of other detail features provided more confidence in your flying on a daily basis. The phrase 'a Faustian Bargain' is well understood. Nothing comes for nothing, and Jabiru moving to Chinese manufacture of its engines, may well prove to be just that. For all our sakes, I hope it won't, but hope springs eternal, while the CAMit engine was here-and-now delivering..
-
Orders not just THIS year: three years ago, the CAMit facility set-up to meet Jabiru's demand for 90 engines/month, was running at 10 engines/month. Jabiru orders in 2015, I think, for the second-half-year was for 10 in total.. Jabiru have been developing 'the Chinese engine' for four years now. Square THAT away with: we have always done our best to support Australian businesses. I can't.