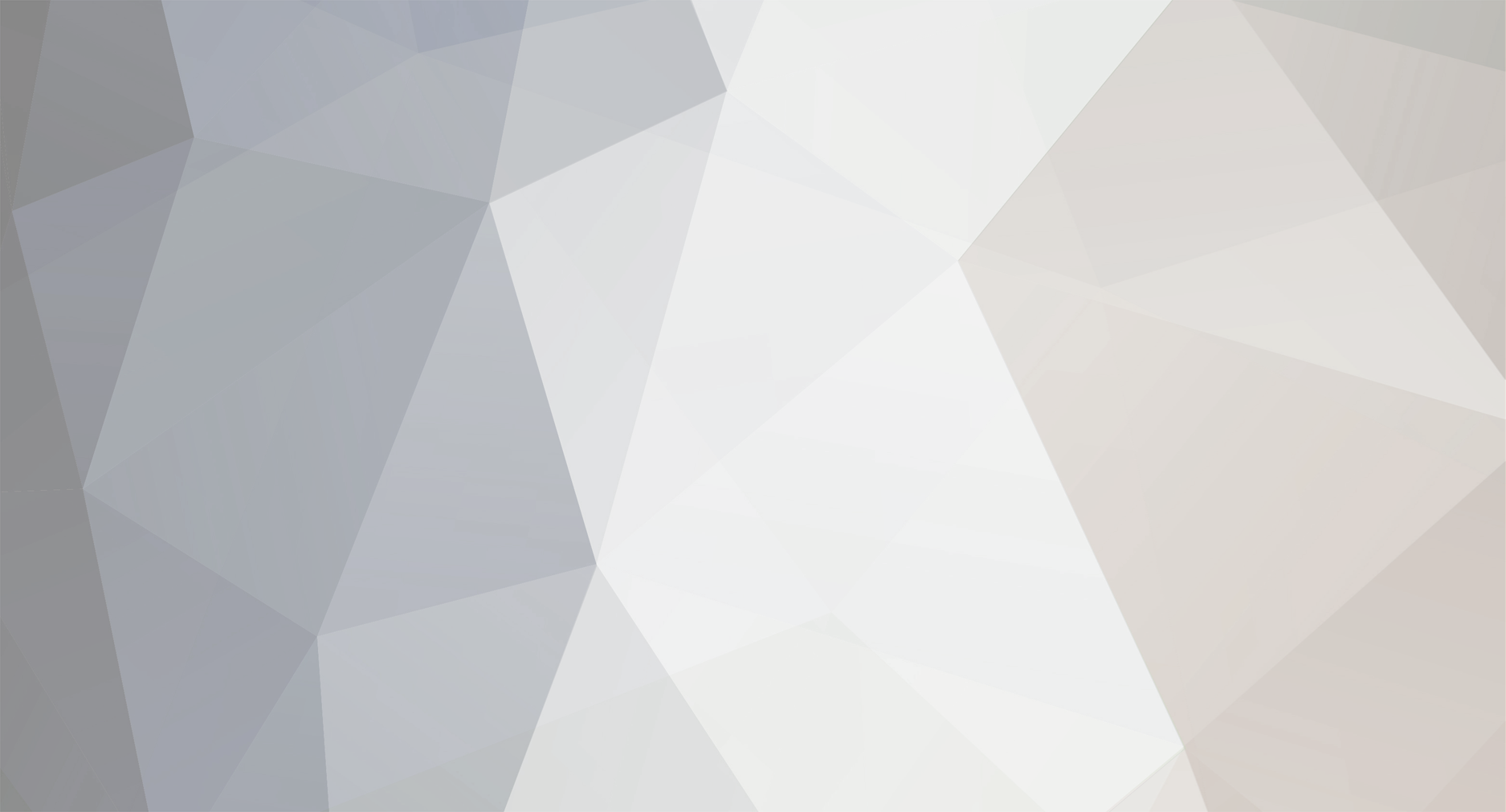
Icarus
Members-
Posts
147 -
Joined
-
Last visited
Content Type
Profiles
Forums
Gallery
Downloads
Blogs
Events
Store
Aircraft
Resources
Tutorials
Articles
Classifieds
Movies
Books
Community Map
Quizzes
Videos Directory
Everything posted by Icarus
-
DEREK Can certainly service a car. Have an old Hiace work van purchased 15 years ago 110,000 ks., Now has 501000 ks . has been in a mechanics shop once for a new exhaust and they Fxxxed that up!!!! Am about to remove and rebuild a ej 20 turbo from a forrester after an timing belt idler pulley failed due probably from not being replaced at 100k service with previous owner. Have restored old valiant including rebuilding everything, steering, suspension, brakes, engine, auto transmission, bodywork etc always fixing something Fix computers when needed and have radio/electronics as a hobby Partner wants a BRS and I would prefer it to. This probably rules out a JAB Would prefer 4 seats . looked at the Sling 4 at Evans Head Fly in ,very nice. New VENTURA from ICP [savannah manufacturer] looks Good too Brendan
-
Geoff 13 My partner is not convinced building and flying an aircraft is a good idea.. He is not helping my cause, evidence or not. I agree. I have confidence I can build and maintain an aircraft. There are many online resources to help guide and I have 2 LAME friends/customers to ask advice. I disagree. If its in use, it shows a whole lot. My assumption , based on the premise that I would not pay anybody a cent who thought they could maintain my aircraft like that. I am not bagging RAA. I am bagging the maintainer of that aircraft if it is flying. Have a good look I will leave the last smart arse remark alone.
-
I Have a LAME friend who says RAA is full of death traps. Told my mrs that I should not build an aircraft because its too dangerous to maintain yourself Pics like this make it hard to argue. Aircraft like this do nothing but harm to the hobby/pastime and make it harder for everyone who wants to build and .maintain their own aircraft. 24 reg so probably owner is L2 Makes me cranky
-
Emergency Landing Liverpool Golf Course
Icarus replied to Cosmick's topic in Aircraft Incidents and Accidents
How long does it take to toot a horn? If there a people in the way would you not find 2 seconds to push a button to save their lives? -
Emergency Landing Liverpool Golf Course
Icarus replied to Cosmick's topic in Aircraft Incidents and Accidents
Those bicycle air horns work well. I had one on a mtn bike. wonder if they would burst at altitude If landing on busy golf course , probably should try to approach from the hole end. They will see you coming then. -
Emergency Landing Liverpool Golf Course
Icarus replied to Cosmick's topic in Aircraft Incidents and Accidents
yep. can buy from a safety shop. maybe even Bunnings. this would be a good idea for crowded beach landings too. I recall a story not long ago where a child was killed and others injured during an emergency landing on a beach somewhere. a $15 air horn may have been the difference. I will definitely have one in or installed in my aircraft when I build it. might be handy to move stubborn wildlife on strips too -
Emergency Landing Liverpool Golf Course
Icarus replied to Cosmick's topic in Aircraft Incidents and Accidents
Out of bound is whit stakes with black top Red stakes = lateral water hazard. 5 options if ball enters. 1. Play ball from inside hazard 2. Play another ball from the spot where the original ball was played 3. drop a ball on a line formed by hole and hazard entry point, as far back from entry point as you like no nearer hole 4 . drop within 2 club lengths of hazard entry point no nearer hole 5. Drop within 2 club lenghths on a point opposite side of hazard and equidistant from hole all except 1. incur a shot penalty. In the case of the aircraft in the water. If a player decides he can play the ball from in the water hazard and the aircraft was obstructing the players stance / swing there would be no relief . [no free drop] This is because there is no relief from immovable obstructions in water hazards. there would be relief anywhere else on the course. [ ie free drop ] If the player with reasonable help could move the aircraft to play his shot ,he could treat the aircraft as a movable obstruction ,move it play the ball. no penalty -
Bank Angle ...... Load Factor ..... Stall Speed ....30°.... ...... .. 1,15 G ..... 1,07 .....45° ............ 1,41 G ..... 1,19 .....60° ...... ... 2 G ...... 1,41 ......75,5° ......... 4 G ...... 2 Thank s Frank and Extralight. I was confusing load factor with stall speed. You can see how this might happen looking at the table I copied above. So the stall speed in my example : 50 kn level stall speed . Stall speed at level turn 45* bank angle =50kn x 1.19 = 59.5kn Thanks for the corrections Brendan
-
Greetings. Can some one confirm my theory of what is happening in the previously posted video please? 1. The aircraft is decelerated to approximately 25 kn above level stall speed . say 50kn level stall . 2. the 45 * turn brings the stall speed up by x 1.41 so approximately 70 knot stall in 45 * level turn. 3. the inside wing is now about 3kn above stall speed ,the outside wing about 7kn above stall speed. 4. The overuse of left rudder now causes yaw left, reducing left wing speed to below stall speed. 5. The right wing is still above stall speed and flying. over we go. Thanks Brendan
-
Apparently , recently there was a spate of thefts from rural properties in my area. The thieves used drones to scope out the property for people at home and layout. They then went in and filled up the owners wheelie bins with stolen goods and wheeled them away. The drones were seen by neighbours as they flew over their properties . one solution may be to build a rf scrambler to disable the control signal to drone. However I believe building or possessing such a device is illegal.
-
For those that have not seen this video yet. Before the comments about Darwin almost gets another etc. Think about how easily this can happen . you cant see the prop from the side. your mind is pre -occupied with everything else going on. your exited about the impending flight, whats that noise? in the background now?? oh yeah the engine sound a bit off , hows the fuel!!!, oops forgot about the prop. Should there be some sort of cage around the prop?
-
+1 for ferrite the wires. also maybe the headset cable Also if the switch to the lights is physically close to your vhf radio , may be worth a try to move it [the switch] further over on the dash ,along with the wiring as far from the radio and coax as possible. Not sure how that will go as far as LSA compliance however. ensure all grounds are good including battery to frame /common /bus
-
Which books for middle aged newbie
Icarus replied to RDavies's topic in Student Pilot & Further Learning
Not a paper book ,however I enjoyed them. Will probably read them a couple more times http://www.flybetter.com.au/ Casa has some publications worth reading too http://vfrg.casa.gov.au/ to start with. Dont forget the very good tutorials linked from this site. http://www.recreationalflying.com/tutorials/ also look at you tube videos. plenty of good safety videos and instructional videos there. Who reads paper books now anyway? -
I see , so the pistons are designed for a water cooled engine , the air cooled jabs are running too hot for the pistons to effectively dissipate enough heat at times? The oil squirters cant hurt . Are the turbos oil cooled only.? do they suffer from oil coking ?
-
Me : I guess a hot crown could start detonation , but why did it get too hot? . Cant dissipate enough heat? is that a design/ engineering issue? or a symptom of an overheating top end? Too lean? hot plugs? detonation from hot heads or too low octane ? An engine running normally, as you know ,should not melt or heat damage the piston crown. A detonating engine can heat the piston to melting point. hot carbon deposits on a crown can cause pre ignition. Monitoring EGT and CHT can give warning that detonation is happening and time to reduce load. hopefully in time to save the engine from near total destruction. http://www.acl.com.au/web/acl00056.nsf/a7d23b8ace0d7e31ca2560d3001fb663/014b681fc66eeab44a2563c6002578c5?OpenDocument
-
Overheating heads can cause post ignition detonation. Post ignition detonation creates a multitude of problems: Heating of valves and pistons to very high temperatures, particularly at sharp edges like valve head corners and piston tops at the perimeter. These high temps can then cause pre ignition detonation. Both types of detonation put high heat and massive strain on all engine parts. This includes: high impact type pressure on piston top through to bottom end and into crankshaft.. this is then transferred to main bearings which are in the crank case, trying to break it apart. The head is also now being forced in the opposite direction at much higher force than normal. Are your through bolts strong enough? Bolt heads Flat on the clamped surfaces? Hot Head? The exhaust valve can overheat and swell in the guide, or break the head off or stick in the guide then the piston finishes the ex head off. Also the seat can warp and or chip and allow hot gasses to flow past the valve head burning the stem and then fracturing the ex valve seat can drop out if the head is overheated and expands and the interference fit is not tight enough. tops of pistons especially at the top edge can be destroyed etc etc Too lean a fuel mixture can create too much heat ,followed by pre ignition detonation The point of all this is that poor fuel or fuel with too low octane rating can cause detonation as well. Creating all the same problems as above and any others I missed. So Jabiru often claims poor fuel, some owners claim poor quality control , while others claim overheating heads as the cause. Some say poor fuel distribution causes lean condition. My opinion is that the issues are probably a mix of one or any combination of these factors. Interestingly Jabiru now appear to provide full exhaust and cylinder head temperature monitoring on all cylinders as standard. Possibly urged by CASA A school jab I was in recently, had dropped an exhaust valve and I believe it was only run on avgas. My actual experience with jabiru engines is exactly 0. and my opinions are based on hours and hours of reading on the subject . http://www.experimentalaircraft.info/articles/aircraft-engines-detonation.php http://www.contactmagazine.com/Issue54/EngineBasics.html
-
A few things. Jabirus now come standard with Dynon 7" Flight DEK D 180 glass panel with full EGT CHT temp monitoring for all cylinders. The 750kg MTOW {South Africa and some here} in the 230/430 at least is due to the Fact that the aircraft was designed with an extra 10% safety Buffer built in. on top of the normal ultimate load factor. This info was from Rod Stiff himself. My TIF was at Lismore on a 30* day. We landed downwind aprox 3 knots over hot tarmac in a J170 . I now understand what F L O A T I N G a landing means. That long runway got shorter ,,,and shorter .........
-
Pipistrel Virus pulls chute
Icarus replied to fly_tornado's topic in Aircraft Incidents and Accidents
I was speaking to the Cirrus sales rep at Lismore a couple weeks ago. He was adamant that the cirrus can be recovered from a spin . You just had to be shown how. It wont recover in one turn therefore wont meet FAR spin recovery certification. Here is a story from a CFI who recovered from a spin, I have no reason to doubt its validity. http://studentpilot.com/interact/forum/showthread.php?39859-Unintentional-spin-in-a-Cirrus It seems that the design of the wings that make them harder to stall/spin , also make them slower to recover from a spin. here is an interview with one of the design engineers. http://www.kineticlearning.com/pilots_world/safety/06_05/article_06_03.html and the Cirrus logic http://whycirrus.com/engineering/stall-spin.aspx It appears at first to me, that they were not prepared to change the wing design to get it to recover in one turn, the same design that helps prevent spins in the first place. So the catch was : recover in one turn and easier to enter a spin, or harder to enter spin and slower or possibly no recovery and use a chute. and one more : http://www.aopa.org/News-and-Video/All-News/2003/February/1/Spinning-In -
Just so we are clear. In no way am I advocating or implying the aircraft should be flown to or above maximum g. Just trying to give shafs some numbers to go off so he can see that the bumps are not near the aircraft limits
-
http://www.recreationalflying.com/tutorials/regulations/ASTM_F2245-07_Airplanes.pdf I believe this document is one of the standards accepted by CASA as a standard for LSA Page 4 has info on structure and loads. I read it as a safety factor of 1.5 is applied unless otherwise set out in the list . Have a look and see what you think. eg a 600kg aircraft designed for + 4g - 2g 600kg x 4 g= 2400kg x ultimate load safety factor of 1.5 = 2400 x 1.5 = 3600kg so the aircraft needs to be tested to be able to withstand 3600 kg for 3 seconds? not sure if the list containing the special load factors also gets multiplied by 4g ie push pull control system joints. at 4g would experience say 10kg of force x 3.3 = 33kg so those joints would need to be designed to withstand 33kg rather than 10kg x 1.5 = 15kg ?