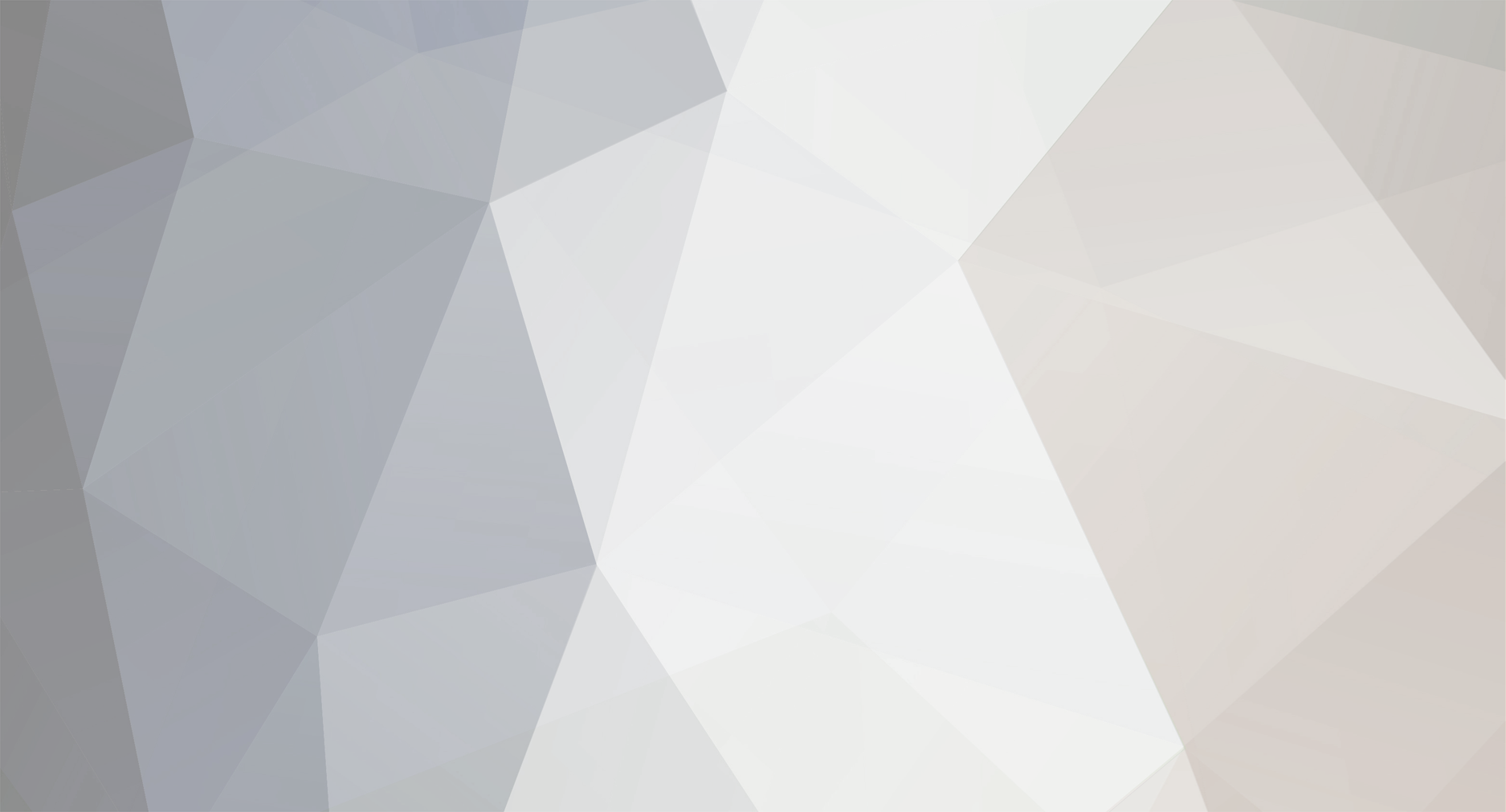
Markdun
Members-
Posts
357 -
Joined
-
Last visited
-
Days Won
4
Content Type
Profiles
Forums
Gallery
Downloads
Blogs
Events
Store
Aircraft
Resources
Tutorials
Articles
Classifieds
Movies
Books
Community Map
Quizzes
Videos Directory
Everything posted by Markdun
-
Hey Spacey, that’s really true. I was just telling Glen the other day that I did a prop strike after landing a Minimax on car track at a mate’s property near Cootsmundra. Thought I’d wash off a bit of speed (I’m really just taxing so just jogging speed) by running one of the wheels into the longish grass and she went up, just clipped the prop on the dirt, and then back down on the tail wheel... several hours later a broken crankshaft (1/2 VW conversion).. Brendan, that’s showing a good deal of confidence that you are always going to have a good place to land. Good attitude to have. Just don’t assume it’s the aerodrome in your flight plan. I have a rule I only fly over terrain I feel comfortable I can do an OK landing, ie. one I can walk away from, as opposed to a ‘good landing’ which is defined as one that the plane can fly again. The other big negative of tailwheelers is that any maintenance in the cockpit is s royal pain... drop a screw or washer and it rolls down into the tail with the empty beer cans. Everything is on a slope, You need a special hatch down the back to clean out all that stuff every 5 years or so.... amazing what you find.... spectacles, old paper ERSA, handheld gps, spanners, sockets & other tools you accused your sons of nicking, toilet paper etc c etc. it’s like discovering that 5th dimension where all those things you had a minute ago but can’t find now go; that mountain of lost socks, nuts and screws, mobile phone chargers that defied the first law of thermodynamics and just disappeared.
-
Sorry, correction. The fact is ‘Brown horses eat more than white horses in Australia’.
-
Now you guys should get some experience. I’ve about 1500 hours total time and probably a bit over 30 hours on nose ploughers. I admit I don’t have a lot of experience on nose ploughers. But it is just plain untrue, wrong, incorrect that tail draggers have poor fwd vision. My Cygnet SF2A with the tail on the ground has far better fwd vision than the Jabiru, the Tecnam Bravo, a Cessna 150 & caravan all with their nose wheel on the ground. I admit the Corby has less fwd vision with its tail on the ground than the Jab..... pretty much the same as the Tecnam (nosewheel down). Further the tail draggers (at least the ones I’ve flown) lift the tail within 20m from the start of a take-off roll, and all the tailwheelers I’ve flown with tailwheel up have had better fwd vision than any nose plougher I’ve flown with its nosewheel down. And then there’s what happens when the nose plougher rotates & lifts it’s nosewheel....pretty much no fwd vision along the airstrip ....& that’s at speed. The opposite happens for the tail dragger...as you speed up better vision. I’d much rather run into the pothole going slow than hit the unseen wombat at speed. In the air the LG is pretty irrelevant to vision, except I note the Tecnam Bravo & the Cessna caravan suffer from astronaut complex in having a ginormous panel for all those fancy screens and switches and thingos which block the view for normal sized people. In short, ‘some taildraggers’ have poor fwd vision when taxiing slowly with the tail on the ground... but not all. I’d also say that in attempting to land short in a paddock (say from an engine failure)...an outlanding, the vision fwd on the Jabiru landing slightly tail down is no better than the Corby. Don’t get me wrong, I’m not anti nose ploughers... I’ve just got one... the Jab200. As I’ve said before it’s probably pilot experience and currency which is more important. Two big differences: first the wheel base is much longer in a taildragger. As such the pitching moment is much less when you roll over a bump or indentation. Second, a quick perusal of the RAA-aus incidents shows many a nose plougher damaged from the nosewheel digging in during an outlanding. It may well be the same logic of the fact that brown horses eat less than white horses in Australia (its true!), but I don’t think so.
-
Don’t know the stats & I wouldn’t disagree. Might be different for operations flying out of and into a paddock compared to a bitumen runway. I would hazard a guess it will to a far greater extent depend on the pilot’s experience and currency. I’m more than comfy flying a nosewheel off a paved runway.... I’d even admit it feels easier than a tail wheel aircraft. But on the grass and mud & ruts...? I’ve been doing some fast taxies with the J200 and I find it a bit of a challenge.... compared to my tailgdraggers. No light tap dancing on the rudder pedals to keep it straight like the tail draggers... more like heavy pushing steering a rugby scrum... that is until the nose wheel comes up.
-
Nah. Just take the tail wheel off, ie convert to a tail skid. Only issue you may occasionally have to hop out to re-aim the aircraft. Had to do this at Temora once to line up for T/O on the grass. But yes, bitumen certainly is tough on tail wheels, particularly the shopping trolley brand.
-
Found the knocking culprit. The main shaft that rotates in the plastic bushed aluminium pillow blocks bolted to the firewall. Rotates smoothly but there is about 1mm end float so the whole front wheel assembly (except for the pillow blocks bolted to the firewall) will go up and down 1mm as load is applied and removed which happens when the nose comes down after you hit a bump. With a fast taxi I couldn’t notice it.... mainly because the whole plane rattles. I’m still trying real hard to understand why ppl prefer noise wheelers instead of conventional.
-
65kg on the nose wheel and 300kgs on the mains puts the CoG in a pretty good spot, though was a bit more overall than i would have liked. I don’t have the pre-flood W&B. If I did then I can figure how much mud I haven’t washed out, or whether it’s the Rotec LCH. Probably have to go 75kg to make it too nose heavy if I recall my CoG calcs correctly. I can’t see how you could put any of nosewheel in backwards.
-
Thanks. So no noise is too be expected from taxiing over bumpy ground. Its all new & I assembled as per the manual. I'll go over it again. There is a bit over 65kg there when the tanks are empty so the NW does carry a decent load. My airstrip is pretty good bump wise. The wombats seem to prefer drier spots; the wallabies just dig up the orchid tubers... tiny holes. Its the effing pigs. But the big problem ATM is too many soft muddy spots for a nose wheel aircraft. If the La Nina keeps up I just may have to stay with the conventional undercarriage aircraft in my hanger.
-
Ehhhh? When I did the conversion to nose wheel the instructor said to me as we were slowing down and about to turn off the runway (bitumen) that 'its ok for you to lower the nose wheel to the ground gently now'. So if a nose wheel isn't for taxiing what exactly is its function; perhaps the same as a rubber duck?
-
Many poo poo ‘Evidure’ because it has solvents which theoretically reduces its waterproofing properties. However I’ve used it to coat entire wing structures with good results, but then these aeroplanes haven’t been sunk in floods. For a prop, I’d guess it’s not so good because you want to build a reasonable thickness of hard epoxy on the outside surface to resist nicks and chipping. Indeed some like the WEST guys suggest the main benefit of a light glass cloth and epoxy on the outside is that the cloth guarantees a reasonable minimum thickness of epoxy to prevent moisture absorption. But then you have the risk of delamination of the cloth.
-
Ian, most of what you say in that latest post I would agree with. My point is there are several factors and the best, strongest etc all depends. From a structure & weight point of view, including moment of inertia, I’d build props from western red cedar: it’s stiff, light & dimensionally stable, glues well and that’s why it’s common in lightweight boat construction. However, it’s soft and dings easily, which can be partially fixed by coating/encapsulating, but in my view this would preclude it for props, just as soft radiata is crap for furniture (unless you like dents). But I’ve gone to a composite ground adjustable prop for the Jabiru and have the two props for the Corby: one made from Eucalyptus delegatensis 60”x46”; & a second one from Auricaria cunninghamii (58x47.5”). Both have similar weights profile and thickness; the hoop pine slightly lighter and the alpine ash slightly stiffer. The ash one pulled me along in cruise at 110kts @3100rpm burning 14.5lph, around 1500fpm climb at WOT. Really a ‘climb prop’. Haven’t got around to installing the hoop pine one yet as having too much fun with the Corby as it is, but it’s intended to give me 115-120kts cruise.
-
Bruce, casein is made from bovine milk protein a monomer which is polymerised to a polymer. The simplest technique is warming the milk with an acid which makes the milk curdle. The curds are dried and formed into shape. So, I would guess it would denature with heat or be consumed by microbes. But it would not remember and return to being milk. Next time your offspring produces a baby and it up-chucks its milk feed, go collect it to make casein glue or milk plastic buttons. And if that doesn’t get you some attention you could see about collecting the kids urine to make a urea based polymer, but that requires formaldehyde. You could make some plastic jewellery? Yenn, I don’t think it works quite like that. From the ‘get go’ the carbon and wood will share the loads. The issue is whether the greater stretch in the timber as load is applied will cause delamination. Sometimes carbon fibres are mixed with Kevlar. The carbon gives the laminate an exceedingly stiff but brittle characteristic. The Kevlar on the other hand yields more easily and combined with carbon reduces the negative of carbon in not being able to absorb sudden loads and the negative of Kevlar in not being very stiff. The wood carbon mix does much the same. The other thing is that carbon epoxy is much better at handling compression loads. So a 6mm square rib member with a 2mm square carbon insert on one side gives 32mm2 area of wood and 4mm2 of carbon. If the part is a beam with the lifting force away from carbon insert the tension side will be handled by the wood and the carbon would handle the compression load There’s also practical factors like a 2mm x 2mm carbon bar may be sufficient for a wing rib, but will it have sufficient surface area for a glue join or to attach fabric or plywood to? Rot in timber structures is really only an issue if you don’t manage moisture content. Spruce, balsa, radiata pine, & many of the eucalypts all have terrible resistance to rot if you let moisture in. Don’t. Encapsulate it all in epoxy and polyurethane. Nicks in props should be fixed. If you see water ingress as inevitable, try using western red cedar, Huon pine or cypress pine which are full of toxins and resist rot.
-
So Ian you know just how much engineering is involved in a forestry degree do you? Obviously not. And I might add ignoring the human element (the skill required to affect a good resorcinol joint) and assuming little variability in timber physical characteristics of published mean values is not uncommon. To be clear, balsa wood is not very strong (layman’s term) but is an exceptionally good timber for lightweight structures. It too has high variability in stiffness, strength and density. Ditto for spruce. Even in bolts, a high MPa bolt maybe not ‘better’ than a lower yield bolt that is more malleable and resilient to repeated bending/loads. It all depends on what you need. And yes there are various Type A to C or D bonds in plywood, but in my experience even in Bunnings, they are all type A. Even some crappy interior lining ply I bought had type A bond. I’ve absolutely no idea of what species of timber you refer to as ‘ironbark’. Most likely it covers several species, quite divergent botanically and in physical properties, so who knows what? As I’ve said before, I and others, have crafted workable props from E.delegatensis (Alpine Ash) that is light (meaning less density if you select your planks carefully), and reasonably dimensionally stable with changes in moisture content (radially and tangentially) & hard & strong enough. A closely related species E.viminalis can have similar physical properties, but the timber of some trees of this species when milled are completely useless for any structural purpose. B. marginata, an Australian hardwood, is also totally useless for any structural purposes. I would not use any of the eucalyptus species in a wing spar, but I would and have used Douglas fir (close grained radially sawn), hoop pine, and I have even used clear close grained radially sawn radiata pine in tail spars. Although I have used eucalyptus as spar caps (tension and compression parts) in large roofing beams. I’ve never used, nor have I heard of anyone else using, ‘ironbark’ for props. My inclination is that that timber probably would be better suited for building stumps, wharf piles, or the edges of snow skis. So we disagree. i don’t really care. Resorcinol glue has its place in history, just as casein glue derived from bovine milk proteins was a technological advance providing a waterproof glue that enabled the Vikings to expand their empire via boats. It may still have its place, but is limited. As for timber, I’d suggest readers look to what is available and make informed decisions on it. As another contributor noted the presence of knots, the orientation of the grain, growth ring spacing etc and the individual density of each plank are likely to be as important or more so than the species. As an aside, I did wonder about worrying about delamination with high moisture content wood. Are we talking about timber props made from unseasoned timber or timber not fully encapsulated in a waterproof polymer like epoxy and polyurethane, & this subject to dimensional changes with moisture content changes?
-
I’m restoring a flood damaged (ex-Lismore) J200. Pretty close to flying stage, but I’m not used to those nose wheel thingos, particularly on a bumpy grass strips. Seems to be quite a bit of knocking up there whenever I taxi fast over bumpy ground. In my tailwheel aircraft I don’t even notice the bumps and any noise from the tailwheel is past history behind me... not so with J200 & with the short distance between the training wheel and the mains, the hobby horsing is unsettling. It would be good to hear what is normal? I’m thinking it’s clunking from the rubber doughnut stops.... can’t see where else it could be coming from.
-
I definitely don’t agree with the view that resorcinol is a better glue than epoxy; but a lot depends on the epoxy- there are hundreds of different sorts of epoxy, of widely difference strength and hardness as there is widely different additives/fillers. So it all depends. Timber boats are almost universally glued together with epoxy, including laminated veneers, double diagonal plywood, strip-plank, laminated beams. Similarly nearly all timber aircraft built now are out together with epoxy glues, including laminated wing spars, wing ribs etc etc. In most cases the glue join failure when subject to sheer or tension is of the wood fibres either side of the epoxy, not the epoxy itself. An epoxy glue used for a wood propeller should have a similar hardness as the timber used and use an appropriate filler, like cotton fibres. I’d suggest a System Three or T88, ir even Bote Coat ‘Poxy Glue’ with a 1:1 mix ratio (harder to get wrong). These glues can be used in high humidity, unlike some others, eg WEST’s. The one draw back off epoxy is that it not UV resistant. It’s incorrect that resorcinol is used in the manufacture of plywood, marine or otherwise. Almost exclusively used are thermosetting glues such as phenol formaldehyde. The veneers and glue are layered in a press and then subject to microwaves to set the glue. It’s not worth ply manufacturers to stuff around changing glues.... they are nearly all the same. The difference between marine ply and others are that in marine ply the veneers are the same thickness and the sheet will bend the same when stressed lengthways or sideways. ‘Structural grades’ may have lower quality veneers and/or achieve the same bending length vs widthways by having inner veneers thicker. Any comment about Australian timber being stronger is just coddswallop. We have over 500 species of eucalypts and other hardwoods and around 100 or so species of softwoods/conifers. The variability between species and even within species is enormous. Like epoxy, when it comes to timber its horses for courses. If one wants to generalise one could say that the softwoods/conifers (gymnosperms) have stronger wood because in general the wood cells are longer and have overlapping tapered ends (toilet paper), compared to the hardwoods (angiosperms) where the wood cells/fibres are more like cylinders (the Australian newspaper). But it ‘all depends’. I try to use E.delegatensis (Alpine ash) for props, but this comes with densities from 300kg/m3 to 900 kg/m3. Or one of our gymnosperms, like Aurucaria cunninghamii (hoop pine) which is a bit soft for a prop (not so with 3 coats of epoxy), but also highly variable in grain characteristics .... some samples I’ve seen you would not build a box with it. Some ‘Ironbark’ species might be exceptionally strong, but they are also exceptionally heavy, frequently with densities greater than 1000kg/m3, ie they sink in water. Sitka is not strong, but it is light and stiff, which makes it suitable for aircraft building. If you milled up a piece of ironbark to be of equivalent strength as spruce it would be lots smaller, probably a bit heavier, but it would be really bendy.... totally unsuitable. My experience has been in successfully building the Jim Maupin designed Carbon Dragon which was almost exclusively Sitka Spruce, with carbon fibre tows laminated into grooves milled in the Spruce (including the 6mm square wing rib stock which had a 2.5mm channel routed which was subsequently filled with carbon fibre and epoxy). I have also built the timber Minimax made from Hoop pine, Pinus radiata, Douglas fir and various types of plywood. I also have Cygnet I built in the 1990s with epoxy laminated Douglas fir wing spars and hoop pine geodesic lattice top and bottom of the wings. Now over 20 years and 1000 hours without an epoxy glue join failure. I have also refurbished a Corby Starlet with resorcinol glue joints. Several wing ribs and some plywood resorcinol joints had to be repaired (with epoxy). I also have built several boats; the latest an 11m ocean sailing catamaran: all critical glue joints are epoxy except the strip planks which are powalina, of similar density and strength as balsa. This is glued with the moisture cured polyurethane expanding foam glue. Some of my deck beams are from our rot resistant cypress pine glued with epoxy, but as this wood is extremely oily you must wash it with acetone before gluing. Mark. BSc(Forestry)
-
I’m new to this idea of a low fuel warning as there is such a device on the J200 I’m restoring, and I am inclined to heave it overboard. My current and past aeroplanes didn’t/don’t have one. You know how much fuel you put into the tanks; you then checked this by dipping the tanks; you have an indicator of fuel level from either a window or a fuel level sensor; you have calculated fuel remaining from fuel consumption multiplied by time (either estimated or via a fuel flow sensor). It seems to me the only scenario is that fuel has leaked out... which would have been picked up in your walk around or from your EMS fuel flow high alarm setting. Don’t get me wrong. I’m a total Nervous Nellie when it comes to fuel starvation. In an unfamiliar aircraft I flew from Kal to Forres, I calculated estimated fuel remaining every 20 minutes and compared that to my flight plan and adjusting fit the headwind. This was from fuel burn estimates using 3 sources of data: from estimated fuel burn; from the unknown calibration fuel flow computer; from the wing tank fuel level gauges (one of which I had to do a ‘Taranaki’ repair on because the LAME found it too difficult...& of-course that doofer repair remains 5 years on). Yeh, yeh, more work, a bit autistic, but it gave me something to do, other than tick off each railway airstrip we flew over while the owner held the stick. We landed with 35l actually remaining compared to my estimate of 28l, from 100l at Kal.
-
Can’t see the rationale of holding an RAA-Aus fly in at a security controlled airfield.
-
Don has heaps of experience in the Thruster and I would defer to his experience. For my part I was never able to comfortably and predictably land a Thruster to how I would have liked. The issue I think is that it has exceptionally high drag and there is just not much energy to convert from kinetic to generate lift without stalling at the lower airspeed (42kts say); you really do have to push the stick fwd quickly to avoid stalling of the engine quits, and any flare on landing is very short because it stops flying very quickly indeed. Brendan, it was a requirement when I first learned to fly that any student would need to read and be knowledgeable of the PoH before they hopped into the aircraft. At a BFR a few years back I had to put the instructor off a little while to give me time to: (1) read the PoH; & (2) familiarise myself with the aircraft and its controls (with the PoH in my hand); & then (3) do a quick daily inspection for myself. There was no problem with this, and in fact I think she was impressed that I did so. The plane was unfamiliar to me, and after the BFR she said she was more than happy to hire the aircraft out to me. Always read the PoH. Mark
-
Flying slow, on the bad side of the L/D curve
Markdun replied to Markdun's topic in Student Pilot & Further Learning
I always thought a ‘good landing’ is one where the pilot and passenger(s) can walk away after landing; and a ‘very good landing’ is one where the aeroplane can take-off again after the landing. -
Flying slow, on the bad side of the L/D curve
Markdun replied to Markdun's topic in Student Pilot & Further Learning
Yeh, OK. Perhaps its more how I like my plane trimmed and rigged. -
Flying slow, on the bad side of the L/D curve
Markdun replied to Markdun's topic in Student Pilot & Further Learning
No.... increased air speed, lift force on wing moves fwd etc. But in an aircraft with a 30hp motor, throttle position or power setting has v. little to do with speed, except on the ground. -
Flying slow, on the bad side of the L/D curve
Markdun replied to Markdun's topic in Student Pilot & Further Learning
Maybe the pitch forward needed to offset the pitch up from full thrust is built in for the Airbus so in case of EFATO, there’s no rush to push the stick fwd to avoid a stall like you have to do in a Thruster? Having built several engine out the front aircraft, I know that thrust line adjustments of the engine are usually needed in most aircraft builds to minimise throttle pitch effects, and this is true for low, mid and high wing aircraft. It all depends on the displacement of thrust from drag vertically. And you can make small adjustments with washers under the engine mounts (or failing that modify the engine mounting). It also depends on what the pilot finds acceptable. On my mid-wing Minimax I adjusted ad-nausea to the point where power changed pretty much affected rate of climb/decent but not AoA or speed. The Corby (low wing) tends to pitch up with the throttle over 100kts with its zero downthrust, as does the Cygnet (shoulder wing) despite its (from memory) 3 degree s of downthrust. -
Flying slow, on the bad side of the L/D curve
Markdun replied to Markdun's topic in Student Pilot & Further Learning
Airbus obviously need more washers on their upper engine mounts for more down thrust..... shouldn’t be big pitch change with power change. -
Flying slow, on the bad side of the L/D curve
Markdun replied to Markdun's topic in Student Pilot & Further Learning
OK, I’ll bite; why not fly on trim? On my Cygnet it’s a servo tab on the elevator with a Bowden cable control. And as Nev said, it’s also there for redundancy say for a broken elevator control wire (but I can’t see that happening) or the elevator control horn falling off from too much rust (it is down there in the tail which gets dragged through the creek and mud occasionally and more frequently the wet grass). As I said I’ve tried to fly a circuit on trim, but It’s bloody hard giving the pitch oscillations. -
Flying slow, on the bad side of the L/D curve
Markdun replied to Markdun's topic in Student Pilot & Further Learning
I’ve always thought flapping the controls (quick inputs) just adds drag (which can be a thing you want sometimes). Flapping the rudder definitely does add drag on a sail boat. The secondary effects of the rudder are pretty much immediate in my experience. I’ve flown many a model with just rudder (including aerobatics) or rudder and elevator; and I’ve practiced circuits with just rudder and elevator trim tab in the Cygnet (ie. hands off the stick). The issue there, for landing particularly is that when you move the elevator trim you get a cyclic pitch response... about 3 ups and downs before it settles down again.... so you would need a very long approach.