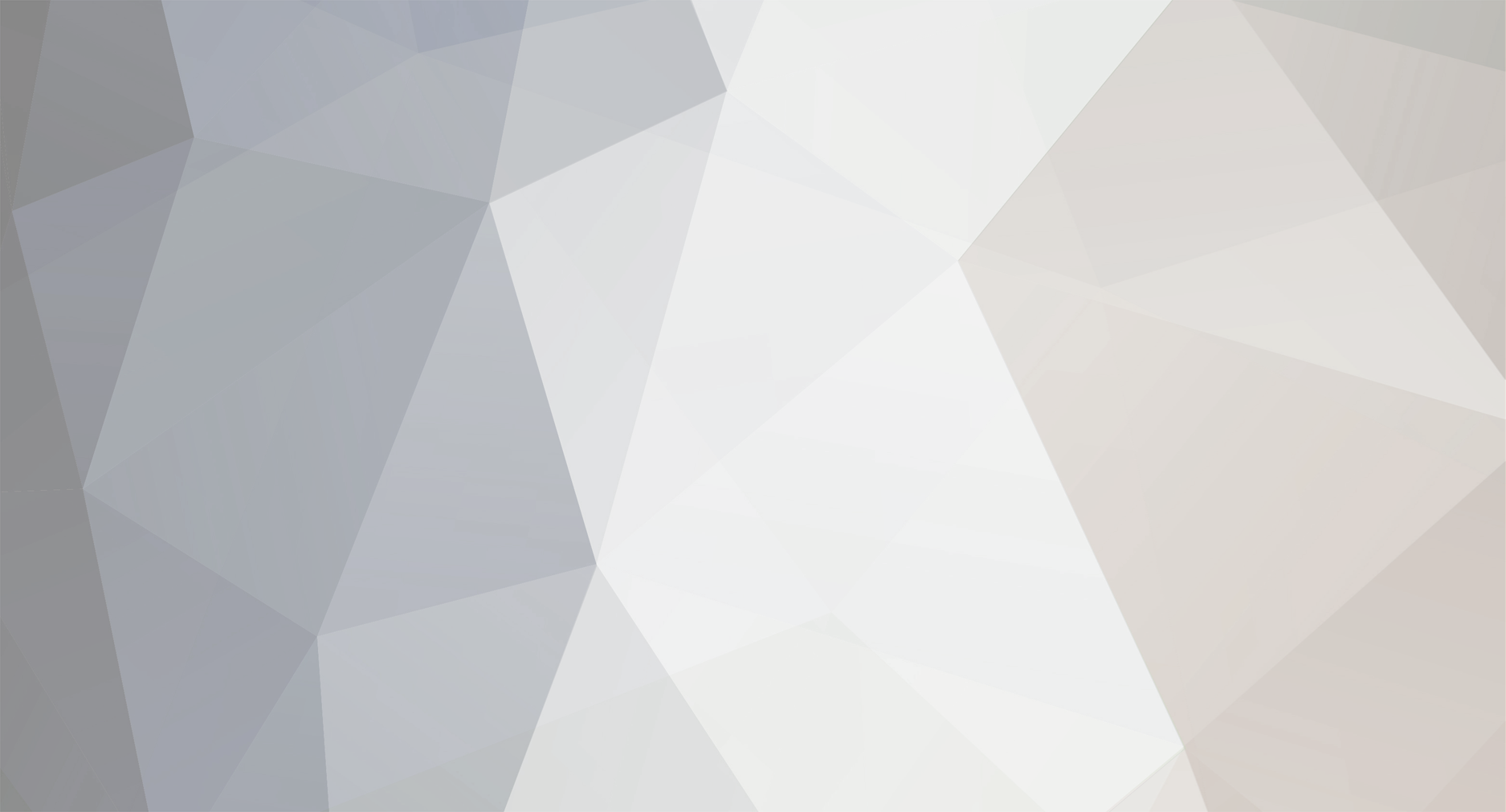
Markdun
Members-
Posts
357 -
Joined
-
Last visited
-
Days Won
4
Content Type
Profiles
Forums
Gallery
Downloads
Blogs
Events
Store
Aircraft
Resources
Tutorials
Articles
Classifieds
Movies
Books
Community Map
Quizzes
Videos Directory
Everything posted by Markdun
-
I forgot to mention. Laminations are used because wood shrinks and expands with changes in moisture content, and this doesn’t occur evenly. Laminating makes the plank/propeller dimensionally stable with changes in moisture content. Length wise, along the grain, wood moves little ~1% or so. Radially (imagine a line from the centre of the tree going outwards horizontally) ~5% or so. Tangentially (also horizontal, but parallel to the growth rings ~ 8-10%. This is why many timber boards twist cup and split. Of-course, some timber’s are pretty dimensional stable with moisture content, eg western red cedar, and this is why this wood is often used in windows and boat building despite being soft (it’s also toxic and doesn’t rot). And if you purchase radially sawn timber (the yanks call it ‘quarter sawn’) as you ought to for aircraft, then you minimise twisting, cupping and splitting, but you don’t get rid of it; laminating does. Also laminating overcomes small defects, like knots, gum pockets, grain misdirection etc.
-
Spacey, that’s an excellent idea. My Jim Maupin designed Carbon Dragon had lots of wood-cf composite construction. The wing main spars (full cantilever wing 44’ wing span) had caps of spruce and carbon fibre. The spruce was in the shape of a ‘U’ that tapered towards the wing tips. The carbon was ‘tows’; a specified number went full length and then there was progressive less full length. You had to make a jig for the carbon to roll off a roll, down through an epoxy bath, up to be squeezed to get rid of excess resin, then along the length of the spar cap. The wing ribs were also made with 1/4x1/4” spruce strips with a 3/32” groove routed down the centre (another jig), and carbon tows were laminated into that groove (similar jigging as for the wing spar caps). These made exceptionally light and very rigid and tough wing ribs. CF has good compression strength, unlike Kevlar, but in most work the compression forces are handled by the resin. But this is why cf laminations are very stiff, again unlike the floppy nature of Kevlar laminations. The problem with cf is that with such a low modulus of elasticity it bends only a very little and then fails completely.....it’s brittle. The combination with wood as a composite in the Carbon Dragon seemed to work well. However, Kevlar was the main tension load bearing material from the wing spar (and anti drag) attachment points to the fuselage. Back to prop building, the question would be what are you trying to achieve by laminating cf between the wood? It would make it much stiffer, which could make the prop more efficient, but it would also make it less resilient and perhaps less forgiving to engine power pulses say. I’d also give a warning from my experience...cf is not easy on tools...if you intend to do any shaping, cutting, sanding etc...good luck.
-
Skip, in sailing boats there’s a saying you can’t have a boat that is fast, cheap and with lots of room below. You can have any two features but not all three. I think aeroplanes are similar...we can’t have it all. Perhaps it’s time, as we all are getting older, to compromise on speed, but keep comfort etc. As per ‘Flying for fun’, spending more time getting there is, might deliver more fun! I hadn’t heard all that about the Europa....it always looked like a nice aeroplane.
-
Skip, I’m thinking a Europa...stall speed maybe a tad more than 30 though. And if you get some long wings you can switch the iron thermal off. Negative is low wing, but then I own a Corby which is such a hoot to fly....what’s wrong with 115 kts?
-
My comments about my experience flying gliders was based on flying in NZ. I agree with Mike’s comments about the GFA...strictly rule based, not safety conscious. I stopped after a check flight with an instructor in strong winds and heavy turbulent sink who was pissed I didn’t landed short instead of putting brakes away to risk a long landing among other gliders and people. He hopped out, pushed the tail through the 25kt wind, the rudder jibing savagely as you would expect, and with the rudder cable exiting the aircraft....an oversized or improperly swaged Nicopress sleeve gave way, and of-course, that glider was unairworthy both before and after this! This was the last straw for me. That club were discouraging of any family attending, particularly children, and expected everyone to attend a full day or not at all. I’m not surprised at all that the GFA has declining membership....they certainly weren’t fun to fly with for me.....a stark contrast to the people of Wellington Gliding Club in NZ based at Paraparaumu aerodrome.....and I’m an Australian and was only in NZ for a job for a few years!
-
Thanks....I also recall that the guy who landed the Boeing convertible soft-top in Hawaii was also a former glider pilot...but not completely sure on that one. Anyway, I would advise all people interested in flying to do some gliding; it’s not only good for flying skills & knowledge, it’s also good for your hearing and your soul. In gliding I learnt about and experienced incipient spins; we spun and had to recover; we did EFATO releases and flew circuits from 200’agl; we always did co-ordinated turns, including close to the ground; we climbed in weak narrow thermals frequently dropping that inboard wing and picking it up with rudder not aileron; we did outlandings which weren’t emergencies; we scared trampers and sheep ridge soaring in the mountains; we flew super smooth wave to 15,000’; we were towed through extremely rough rotor losing and regaining site of the tug in seconds; my kids often got to ride in the back seat of the Cub tow plane; we coastal ridge soared in westerlies below 800’ for ages; we flew with 10 or more gliders in the same thermal; we did aero tows, winch launches, car tow launches, and rubber band launches off the side of a hill with the hang-glider guys....flying for fun at its very best!
-
I also agree with Nev and Bruce. Gliders are conventional aircraft. As regards landing, I’ve only flown gliders with one wheel and a tail skid, and landing is as per conventional for any tail dragger; fly a conventional circuit, control glide slope with spoiler/brakes or side slip, using the spoiler/brakes/side slip like you would with a throttle, except you can’t do a go around, or like a dead stick landing in a powered aircraft. Cross wind landing is by crabbing not wing down....wing down risks a ground loop from touching a wing tip on the ground. Most gliders will also pull up fast, say if that fence is coming up too fast, by doing a wheeler landing, applying wheel brakes if you have them and pushing the stick forward to rub the forward under fuselage in front of the wheel on the grass. They also pull up faster if you keep the undercarriage retracted. I’ve assumed you understand the difference between nose wheel and tail dragger aircraft in that the centre of mass in a nose wheel aircraft is forward of the main wheels, and so when the mains touch the runway on landing the nose drops and this reduces the AoA on the wings, reducing lift. On a tail dragger the opposite happens, so if you land with airspeed above stall, the tendency is for the nose to pitch up, increasing the AoA, and you will balloon back into the air. There are also considerations about how spoilers/brakes affect stalling. The gliding club I belonged to regularly had landing ‘competitions’. We would put a row of toi toi (pampas grass) across tge runway to simulate a fence. The winner was the person who went clear over the row of pampas grass and pulled up closest to them. One time a young bloke came in with the club Blanik, real slow, brakes in, pulled up over the pampas and then snapped the brakes out. The glider immediately stalled about 1.2m above the ‘runway’ with almost no forward speed, coming to a stop about two plane lengths from the pampas fence.....a hard landing, but easily the shortest. The CFI disqualified him.
-
Contemplating how I could install a remote transponder in my Corby (definitely no room on the panel for a transponder) with it being controlled by my MGL Xtreme EFIS. Seems there are plenty of cheap Garmin XTR33 around. You would think manufacturers would publish their RS232 protocols but alas, no. The MGL setup is for a Sanden remote transponder, so it has the functionality. Has anyone either worked out the protocols or built a multiplexer/converter?
-
ADS-B Could We End Up Against A Similar Situation?
Markdun replied to jackc's topic in AUS/NZ General Discussion
I’ve said before flying small aeroplanes is inherently dangerous, and it always grates whenever I hear Ra-Aus rabbiting on about how safe it is. (And they’d probably get more growth in membership if they emphasised the danger instead of carping about safety...that is, if you’re one of those fools who want endless growth). Overcoming and dealing with the danger is to me, one of the fundamental joys of flying my own plane. And that is why it erks me substantially when I’m treated like a child by Ra-Australia or CASA when they compel me to use some commercial certified person to check or do the work on my bird, with that being pot luck whether the job is done properly. If it’s me that does it wrong, I’ve got one person to blame. Of-course the most dangerous sport of them all is lawn bowls, but I don’t hear of any moves that they should undertake more training, particularly human factors, nor get a permission note from a doctor when they turn 75 because they might lie about their health, nor a trained and certified maintenance engineer to tend their lawns and equipment. And the most dangerous thing we ever use is a bed; while matron might do a daily inspection, my guess is many users of beds fail to do the simplest, ‘am I safe’ check or lodge a sleep plan before embarking on 8 hours, despite this being the most likely place we will die. -
ADS-B Could We End Up Against A Similar Situation?
Markdun replied to jackc's topic in AUS/NZ General Discussion
Except for your first sentence, I agree with you Spacey. My ‘but’, is your view of ‘most’ unfair. I agree the policy objective should be the least worst. And from the point of view of an individual injured due to gross negligence, the Kiwi system is unfair, like you say. But how unfair is our system, where billions of dollars each year are wasted on lawyers and insurance companies (which could go to the injured), while many injured go completely uncompensated. I was a secondary school teacher in the early 1980s and one of my year 10 students was run over by some unlicensed youths in an unregistered car. He suffered two seriously broken legs and a smashed hip with life long disabilities ensuing. No third party insurance, and the wrong-doers had no income, no assets, and no future. He got nothing, except a life long disability. How unfair is that? I’d add, if there was ‘gross negligence’, and I’m not up on whether that has a specific legal meaning, it would seem it would also be common law ‘criminal negligence’, which is defined the same as the tort of negligence, except a jury finds the negligence so bad (gross?) it warrants a criminal penalty such as term of imprisonment. The big negative of the NZ system is there is less incentive for hazard makers to be careful. We found it not uncommon to find a big hole in the footpath or road with just a couple of 200l empty drums thrown in and a witches hat...no signs, lights or barriers...but hey, it does make oneself more careful of other idiots. Can’t someone tell me off for being off topic now? I’ve been getting high oil pressure alerts in my Jab powered Cygnet. Does this indicate oil pressure unit is failing or that the PRV is playing up?? -
ADS-B Could We End Up Against A Similar Situation?
Markdun replied to jackc's topic in AUS/NZ General Discussion
Yes. In my view the NZ system is far, far superior. An injured person doesn’t have to prove someone was at fault, or run the risk a defendant was bankrupt, unemployed with no assets....everyone is compensated. No third party compulsory insurance for cars, no wasted money on useless lawyers or for profit insurance companies. The NZ accident compensation system has got some problems for sure, but nothing like we have here. One of the problems here is that judges are human and feel, as they should, for the situation of some poor fool, like the quadriplegic from diving into the sand at Bondi breaking his neck, and then look to where the person can get some money....local government or someone with insurance! Understandable, but crazy. -
ADS-B Could We End Up Against A Similar Situation?
Markdun replied to jackc's topic in AUS/NZ General Discussion
Turbo, see below. Insurance is different...often it seems insurance companies assume liability and pay when they shouldn’t....and just pass the costs on to customers. And sometimes this gets confused with legal liability. Australia: Civil liability for personal harm - dangerous recreational activity and obvious risk 05 June 2013 by Ross Donaldson Colin Biggers & Paisley In brief - Court decision gives recreational and adventure operators more guidance A student learning to fly a light aircraft is engaging in a "dangerous recreational activity". A crash landing is an "obvious risk" of that activity in the context of civil liability legislative provisions. Legislative reform provides more protection to recreational and adventure businesses A body of law continues to develop to define and exclude from recovery from damages persons who are injured when participating in certain recreational or adventure activities. This has been the consequence of legislative reform seeking to provide more protection to operators of those recreational and adventure businesses. Emergency landing of light aircraft causes harm to student pilot In the District Court of NSW ( Campbell v Hay [2013] NSWDC 11), the plaintiff, Noel Campbell, a student pilot, sued Rodney Hay, a pilot instructor, arising out of injuries he sustained when participating in a flying lesson. During the course of the lesson, the aircraft engine stopped and Hay took over its controls and undertook a forced landing, resulting in Campbell sustaining injury. Briefly the background of this incident is that about 45 minutes into the flight engine vibrations were encountered. On increasing the aircraft's revolutions, the vibrations apparently disappeared. A short time after this it was said vibrations returned but the engine commenced to run well for about a minute. Hay took control of the aircraft, applied full power and took other steps, but the engine subsequently failed. Hay put the aircraft into a gliding mode, allegedly attempting to restart the engine and undertook an emergency landing into a bush gully. Hay was an experienced pilot who had had been involved in a number of emergency landings over his career. Student pilot claims that instructor's management of aircraft was negligent Hay's negligent conduct alleged by Campbell focused on his management of the aircraft, leading up to and including the engine failure, and his decision in regard to managing and landing the aircraft in this period. The aircraft engine experienced roughness shortly before it failed. Expert evidence was led in favour of Campbell to suggest that on encountering engine difficulties, a decision should have been made to seek the nearest available landing area, rather than proceed with his original course and then having to deal with the consequences of the engine ultimately failing. Pilot instructor found negligent but argues that risk of injury was obvious The trial judge found that Hay had not exercised reasonable care by not ensuring that the aircraft was flown towards an appropriate landing strip immediately after the second set of vibrations started and by his decision to continue to fly towards Katoomba. Hay was found negligent as the pilot instructor, but he argued that the activity was a dangerous recreational activity, the risk of injury was an obvious risk and Campbell was precluded from recovering. Civil liability provisions provide some protection In NSW, pursuant to the Civil Liability Act (NSW) 2002 (the Act), a person injured whilst participating in a dangerous recreational activity and as a result of the injury arising from a risk that is an obvious risk is barred from recovering damages from another person, notwithstanding that other person may have been negligent. Those provisions offer powerful protection to operators of businesses which offer such activities. (For more information please see our earlier article A user's guide to the Civil Liability Act 2002 (NSW).) The public policy behind this legislation is to prevent placing the burden of civil claims on operators of such activities, when society perceives that these activities are inherently dangerous and bring with them an obvious risk of injury or death. Risk that would have been obvious to a reasonable person Section 5L of the Act requires a number of steps to be determined before a bar operates to exclude recovery. Those steps must be that the court finds that the activity is a dangerous recreational activity, which under Section 5K means a recreational activity that involves a significant risk of physical harm and that the harm suffered is an obvious risk as defined by Section 5F, being "a risk that, in the circumstances, would have been obvious to a reasonable person in the position of that person". Section 5F provides that an obvious risk includes a risk that is patent or a matter of common knowledge and can be a risk even if it has a low probability of occurring. Obvious risk as defined under Victorian law In Victoria, there is no equivalent of Section 5L of the Act. That is, there is no statutory bar to a claim in negligence if it is established that the activity involves an obvious risk, but the statutory provisions in Part X of the Wrongs Act (1958) seek to codify some of the common law as it relates to claims in negligence, including the awareness of the risk. For example, sections 53 -55 require a court to assume the claimant had knowledge of an obvious risk, if a defence of voluntary assumption of risk is pleaded (reversing the onus of proof on this issue). Obvious risk is similarly defined as in the NSW legislation. A claimant cannot recover if the injury arises from the materialisation of an inherent risk of an activity. An inherent risk is defined to be something that cannot be avoided by the exercise of reasonable care. Sporting clubs and adventure activity businesses need liability insurance These provisions are the product of the tort reform following the so-called insurance crisis after the collapse of HIH Insurance. It was perceived that there was an inability of sporting clubs and operators of more risky activities to obtain liability insurance. The definition of a "recreational" activity or services in the context of claims for damages for personal harm has also gained importance by virtue of the Australian Consumer Law and state fair trading legislation which permits operators to exclude certain terms, implied by legislation into a contract for the supply of recreational services, if certain express warnings are given to a participant. What is a dangerous recreational activity? In Campbell v Hay the Court had no difficulty finding that flying lessons in a light aircraft is a recreational activity. The question was whether this was a dangerous recreational activity within the meaning of the legislation. It must involve a significant risk of physical harm ( Section 5K). The trial judge took guidance from enunciation of relevant principles by the NSW Court of Appeal decision of Jaber v Rockdale City Council [2008] NSWCA 98 to answer this question. Jaber involved a person injured from diving into shallow water. The standard to be applied lies somewhere between identifying a trivial risk and one that is likely to occur, with reference to both the risk and the physical harm likely. An activity involving a significant risk of sustaining insignificant physical harm (described as a sprained ankle or a minor scratch to the leg) could not necessarily be regarded as a dangerous recreational activity. The risk of physical harm must be significant, while the risk of it occurring may be low or unlikely, but not trivial. A significant risk must be somewhere between the likelihood being trivial and one that is likely to occur. Risk of accident when flying a light aircraft not trivial or remote The court held flying lessons were a dangerous recreational activity. The risk of something going wrong in an aircraft, off the ground with a single engine was obvious. An aircraft in difficulty needed to be landed. The aircraft could get into difficulty for a number of reasons: pilot incapacity, pilot error, engine failure, and other mechanical problems. The likelihood of risk of injury was not trivial. In assessing whether this was a dangerous recreational activity, the court was inclined to inform itself and make its own assessment based on its own knowledge and experience. However, Hay did lead evidence, including statistical evidence of the number of accidents involving light aircraft, including injuries and fatalities. It is obvious, as common experience would suggest, that the risk of accident when flying a light aircraft was not trivial or remote. Crash landing is an obvious risk of flying In regard to whether the injury had an obvious risk, the court considered that as a matter of knowledge and common sense there is a risk of injury if Hay was negligent. A failure to manage or operate the aircraft in a reasonable manner could eventuate in a forced landing or a crash. This was sufficient to satisfy the definition of "obvious risk" in Section 5F of the Act, notwithstanding the low probability of the risk of harm occurring. Despite a finding of the instructor's negligence, Hay was barred from recovering damages. An obvious risk is not always obvious, despite the activity being dangerous Showing that a dangerous recreational activity has an obvious risk is not as easy as it might seem. A decision of the District Court of NSW in Harris v Perisher Blue Pty Limited [2011] NSWDC 172 illustrates the point. The trial judge had no difficulty concluding that snow skiing at the Perisher ski resort in the Snowy Mountains was a "dangerous recreational activity", but the circumstances giving rise to the injury were not caused by an "obvious" risk. In that case Harris sued the operator of the resort as a result of injuries he sustained when participating in a beginners' lesson. He failed to negotiate a ditch located towards the bottom of the beginners' slope. The ditch was not considered simply a product of the normal undulation and unevenness of a ski slope, but constituted something more significant and unexpected. The court found that the risk of harm, i.e. skiing into this ditch was not "a result of a materialisation of an obvious risk of a dangerous recreational activity". Harris was not barred from recovering pursuant to Section 5L(1) of the Act. That finding was not interfered with on appeal, although the appeal focused on more fundamental, breach of duty and causation issues (see Perisher Blue Pty Limited v Harris [2013] NSWCA 38). Of course, having overcome that threshold, Harris was still required to prove that the resort operator acted negligently to recover damages. (For more information about this case please see our earlier article District Court finds non-delegable duty of school during skiing excursion.) Recreational and adventure activity operators are getting the protection they need The decision in Campbell v Hay adds to the body of law regarding the civil liability of operators of recreational and adventure activities to customers who suffer injury or death. Operators and their insurers can take some comfort (and perhaps protection) with the court adopting a broad interpretation of the legislation. Injuries to be expected of such activities should not be compensable. At first glance one might think that embarking upon a course of flying lessons, an activity involving sophisticated and well maintained machines operated by highly trained people, would not constitute a dangerous recreational activity, but the court's reasoning is sound. Yet there will continue to be argument in future as to whether these statutory provisions will apply to many novel activities. Participants in adventure activities cannot expect to be protected from all harm In the field of recreational and adventure activities and the liability of operators, and prior to these more modern legislative reforms, the courts have grappled with the need to recognise that there must be a trade-off between the experience a recreational or adventure activity offers, (excitement, exertion, exhilaration, fear, challenge), as against the risk that an injury may be sustained. Participants cannot expect to have these experiences (which are as much emotional as they are physical) yet be "wrapped in cotton wool" and protected from all injury. A balance must be struck, ensuring that operators provide a relatively safe experience, but not necessarily risk or injury free. (Most people participate in organised sport on that understanding.) Alternatively, operators can provide a very risky activity but with full disclosure and acknowledgment of those risks with accompanying waivers and exclusions - for example, perhaps, in the case of parachuting and motor racing. Even a low risk of significant harm makes a recreational activity dangerous Where the recreational or adventure activity may cause an injury that is not trivial, even if there is a low probability of it occurring, it can be considered a dangerous recreational activity. Similar findings have been made about diverse activities including snow skiing and shooting kangaroos by spotlight, although participating in touch rugby was found not to be and an organised gym class, or whale watching from a boat were held not to involve the supply of recreational services. Providers of dangerous recreational activities failing to exercise reasonable care Injured persons remain permitted to recover loss and damage involving dangerous recreational activities where the eventuality of the risk of harm is not obvious, and the operator has failed to exercise reasonable care. Examples of the application of these principles for recreational operators could include a horse trail ride operator providing a defective saddle strap which breaks and a patron falls, or a scuba dive operator placing divers in a powerful current, having failed to interpret the tide charts properly. In these examples, a reasonable person may not have expected the eventuality of the harm, and but for the operator's negligence, the injury would not have occurred. Content and scope of risk warnings considered in Action Paintball case On the 13 May 2013 the NSW Court of Appeal delivered a judgment in Action Paintball Games Pty Ltd (in liquidation) v Barker [2013] NSWCA 128 which included a consideration of the content and scope of risk warnings to be given to participants of recreational activities. Under section 5M of the Act no duty of care is owed if a risk warning was given regarding a recreational activity. The plaintiff was 10 years old at the time when she participated in a laser tag game in open bushland occupied by Action Paintball. The plaintiff tripped on a tree root and suffered injury. She was awarded damages in the District Court. The Court of Appeal found that a general warning given by Action Paintball that there were a lot of sticks and obstacles in the way and to not run at full speed was a sufficient warning of the risk to engage section 5M, and the plaintiff could not recover damages. Operators of recreational activities can take some comfort in the court adopting a pragmatic, rather than restrictive approach to the requirements of section 5M. Ross Donaldson [email protected] General liability Colin Biggers & Paisley -
ADS-B Could We End Up Against A Similar Situation?
Markdun replied to jackc's topic in AUS/NZ General Discussion
Turbo, what you say sounds more like USA law. You may not realise, but Australia is actually a different country, with different laws. The ability of a surviving family to sue a deceased person’s estate is quite complicated here. A mother who saw her 5 yo son run over and squashed to death by a concrete truck is entitled to nothing, unless she can prove she suffered psychological damage ‘nervous shock’. But the point I have made before is just as relevant, the amendments to Australian States’ and territories’ tort law statutes, specifically excludes liability when a person voluntarily engages in an activity that is an inherently dangerous recreational activity such as pony club, rugby league or flying light recreational aircraft. A family of a person killed, who was voluntarily engaged in flying recreational aircraft...which is inherently dangerous, would have no case. NZ is even better....there, negligence tort liability is mostly abolished through their universal no-fault Accident Compensation Scheme, that insures everyone injured is compensated....just the lawyers don’t get their fees. Go read the current version of the NSW Civil Liability Act; I think you will be surprised. -
ADS-B Could We End Up Against A Similar Situation?
Markdun replied to jackc's topic in AUS/NZ General Discussion
Yenn, Don and I were once asked by Canberra ATC to identify ourselves as we were flying east from Murrumbateman towards Canberra. He was in his VP2 and I was in a Minimax.....probably around 4500’. They could have only picked us up by their primary radar....and they had no idea of our height. I’m also told that primary radar (Mt Majura) at Canberra also picks up trucks on the Federal Hwy...and that one truck was nearly targeted with a missile when a US president was visiting. -
ADS-B Could We End Up Against A Similar Situation?
Markdun replied to jackc's topic in AUS/NZ General Discussion
The biggest risk to me from flying where I do are military heavy rotor wing aircraft flying at or below circuit height over my airstrip in what are regular trips for some commodore from Nowra to Canberra and back. They don’t monitor the area frequency (in my case Canberra approach east), nor do they have their own radar turned on. My correspondence with them was to the effect they use ‘see and avoid’ and that’s what they are going to keep doing, and they declined my invitation to land, have a coffee and discuss how we could better maintain safe separation. Of-course, the military are exempt from CASA and ASA rules. I’ve ended up buying a SkyEcho because most of the time they do have their ADSB turned on. It still scares the bejesus out of me after having a blackhawke fly by me (<300m) in and slightly below my altitude on a downwind to land. It also scares me when Canberra approach ‘clear’ inward bound aircraft to Canberra in Class G airspace from Lake Bathurst at 4500’, when controlled airspace at that altitude, doesn’t begin 10nm further in towards Canberra. I always get tge feeling those guys think ATC has the responsibility to avoid conflicting paths from the time they are advised they are cleared and not when they leave Class G....maybe I’m wrong on that. -
Yenn, you can cut/grind the back off the TinyTach to expose the battery. Replace with a cr2032, and recover with a small section of old canopy lexan/acrylic and a few screws, or just goop. Like new from the front. Don showed me this. Cutting off the back will also allow the water therein, to drain out....much quicker than Glenn’s suggestion of evaporating the ingested water off, particularly if you take the plane up and do several cycles of spins 🙂 On the rpm reading, my TinyTach also had a two stroke default, ie. on pulse per revolution, not a four-stroke that has 1 pulse per two revolutions. To avoid the resetting to two stroke giving half the rpm, I had the sensor wire wrapped around two HT wires from the same magneto, to produce 1 pulse per revolution. I’m thinking your problem is your maths, not the TinyTach, unless you wrapped the sensor around the HT lead from a coil to a distributor.....do change the battery —- it’s not hard.
-
Walrus, I was a bit taken aback when I had to ‘apply’ for an MMSI number for a yacht AIS (a slow maritime ADSB type system) and had to photocopy my 40year old, washed in saltwater a few times, radio operators certificate, to prove my qualification....to the very same Cth department that issued me the certificate! The CASA system for an ADSB hexadecimal number is much better. And yes,similar stupid rules say you can’t have expired flares on board, or EPIRBs past the extreme conservative battery life expiry date. Still, I keep at least 4 on my boat and two in my aircraft. If the shit hits the fan, I want the lights to really and truly light up at the AMSA emergency incident room in Canberra, rather than having them think, ‘yet another false alarm’ to check out.
-
Haa! I once did a review of the Radcoms Act. Found that around 90% of GA aircraft were non-compliant in not having an ‘apparatus licence’ for VHF radiocoms; and small boats were far more compliant with only 60% failing to have an apparatus licence for their vhf radios. It cost the SMA heaps more in not enforcing the rules than revenue from licence fees. My recommendation was to abolish the requirement, including the radio operators’ licence rests for both aircraft and boats....at least for vhf.
-
I agree Jack. On motor vehicle standards the relevant regulations or statute or code requires the owners or operators of the vehicles to meet the appropriate standards. I would think a purchaser of a caravan that was sold as meeting the appropriate standard but which in fact did not, would have a good basis in contract law to sue for damages etc. I think you will find that the Registrars of Motor Vehicles in each State also has the discretionary power to require the owner/operator to get a certificate or report from a professional engineer that their vehicle meets that standard. Here in the ACT that discretion is used to require registered operators of lpg powered vehicles to get a certificate of compliance for the lpg system every year. Of-course, if a vehicle doesn’t meet the standard and the non-compliance results in damage to others, the owner/operator (as opposed to the driver) could be liable legally. This stems from tort law, which would ask, did the defendant owe a duty of care to the plaintiff, if yes, what was the standard of care that was owed to the plaintiff, was that standard breached, and then what were the damages caused by that breach. But this does NOT apply to Ra-Aus aircraft because, firstly, as an inherently dangerous activity, there is no duty of care owed to participants (due to tort law reform). Secondly, if there was a duty owed (but there is not to other participants....so think about that....a duty would be owed to GA and RPT pilots and passengers, and people on the ground), tge ‘appropriate standard would not be CASA standards (eg.CoA) because they expressly do NOT meet the standard and are exempt (if operated under Ra-Australia)...the standard would be Ra-Aus standards. Which of-course, brings us back full circle to that circular argument that if an aircraft/pilot do not meet the Ra-Australia ‘standard’, they are not exempt from CASA rules. Putting aside tge question about jurisdiction of Ra-Aus to discipline members for non-compliance, a proper court has an obligation to make laws work even when they are stupid. I could give you an example I had when I uncovered that thousands of Crown leases in Canberra were issued contrary to law which expressly forbid the Minister issuing these leases....the deals involved land redevelopment, and failure of both Liberal and Labor governments to charge hundred of millions of dollars for redevelopment rights on public land. Others might call it corrupt, but I can’t comment. The unlawful acts were by Ministers or their delegates, not recipients. The owner of a local airport, among many others, was one of the beneficiaries of this publicly funded largesse. In a strict legal sense,because the leases were issued by the Ministers contrary to the law, they were invalid ‘ab initio’, as opposed to being capable of being invalidated by court hearing. Therefore, all the current leases, bought by unsuspecting families were also invalid. My legal team said there was no question about this, but they said every court in the land would find whatever way the could to prevent our success because of turmoil it would create.
-
There is a lot of bull here. Public liability.....? I don’t think so. Who is the lawyer? In most States and territories in Australia tort law was modified about a decade ago, to expressly exclude dangerous recreational activities, like RA-Aus flying, from tort law proceedings. Negiligence and ‘duty of care’ just doesn’t apply, if the activity is inherently dangerous (which it is for light aircraft), if there is a notice warning to passengers/occupants etc, or if the student/participant signs a waiver, it just doesn’t apply. The only jurisdiction in Australia that didn’t implement these reforms is the A.C.T.. I doubt the Ra-Aus has any liability over the misdeeds of any LAMES or L2 maintenance people. The truth is that people accept liability themselves....as it should be. It’s only the I’ll-informed, or insurance companies with vested interests, that keep peddling the lie of organisations like the ra-Aus being liable for what their members do. In my view, the key issues are: what is the problem? eg. unairworthy aircraft causing injury or damage to third parties (ie. not the pilot or passenger); and what is the best way to address this problem, eg. Weight, speed, maxim7m number of passengers, system of competence for maintenance people, noting it’s not going to be perfect or foolproof. And the direction of the RA-Aus in just trying to replicate the old, failure laden, overly complex, model favoured by CASA to be buddies with ‘the industry’, doesn’t answer either of these questions. My evidence is that in my experience there are equal proportions of LAMES and L2s who I wouldn’t let touch my aircraft, as there are that are exceptionally skilled, experienced and competent aircraft maintenance personnel. In reality, the aircraft’s owner/operator makes the decision as to who he/she employs to maintain their aircraft (or do it themselves), irrespective of whether they are a LAME or L2...why not recognise this and give guidance on how to make this decision rather than perpetuate the untruth that all LAMES or L2s are competent because they jumped through some regulatory hoops?
-
Hot rear cylinder example Jabiru 3300A-2575 and plenums
Markdun replied to RFguy's topic in Engines and Props
Glen, I’ve a couple of new roller lifters at my hanger if you want to experiment with them....guaranteed empty of oil. I could also pull some pushrods....but I haven’t measured them. -
For glueing, I use the System Three one to one ratio glue.....the same as I use on my wing spars, ribs, and on structural beams on my 11m yacht. I’m told it’s the same as one of tge approved epoxies for certified aircraft....and good for gluing in high humidity (some epoxies aren’t). When cured it is only a tad harder than E.delegatensis and pretty resilient (ie. not brittle). For coating I just use a local Qld made epoxy that is fairly high modulus, ie. hard and waterproof, but will chip more. Some epoxies are softer (eg. BoteCote) which have characteristics more like lower density wood used in boatbuilding like WRC and are better in that use. I tried these softer types thinking they would be better for leading edge protection, along with Kevlar woven tape....not worth the effort. I now use hard epoxies for coating and prop tape for leading edge protection. If I was making the prop out of low density timber like hoop pine, now I’d probably use the single pot expanding urethane glue. Not as tough as epoxy, but the urethane glue joins are stronger than the wood if the wood is soft. Lots of laminated beams and plywood in my sloop held together with urethane, and it’s over 10 years in the water with a few thousand blue water ocean miles under its hulls....and no glue joins have failed.
-
Bruce, adding a 175x75x2.4 gal steel C beam to your wing spar will make your wing stronger, but I wouldn’t think that a good thing. The glass covering is mostly about ensuring a thickness of the coating for moisture and abrasion. I think the strength claims are marketing spin mainly. My guess is the glass will also increase the moment of inertia and diminish one of tge benefits of a wood prop. But its swings and roundabouts....I don’t think there’s much in it to worry about.