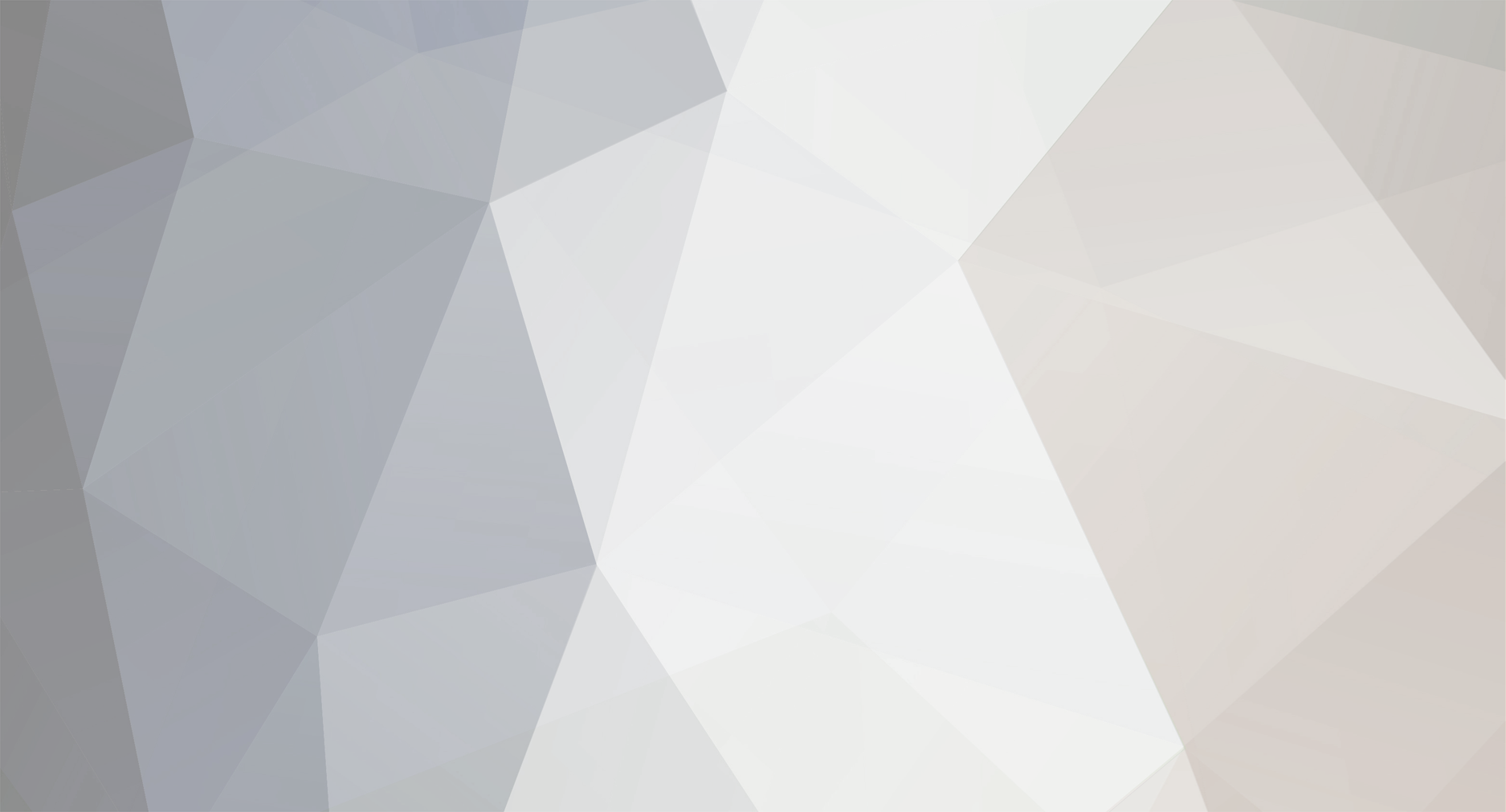
skippydiesel
Members-
Posts
6,752 -
Joined
-
Last visited
-
Days Won
69
Information
-
Aircraft
ATEC Zephyr, Sonex Legacy (A)
-
Location
The Oaks
-
Country
Australia
Recent Profile Visitors
14,898 profile views
skippydiesel's Achievements

Well-known member (3/3)
-
My system is for a Rotax 912ULS; If you would like, I can send photos of my interpretation of the Rotax boost pump, with non return by-pass circuit - all a mixture of automotive & aircraft fittings.😈
-
skippydiesel started following Rotax 912 coolant radiator and Fuel fittings
-
Sorry 440032, I am about to "throw a spanner" in your advice. When I was doing my Sonex fuel reticulation (30L wing tanks & central 40L header) all connected by aluminium pipe & AN fittings, I found that to get what I wanted to do the job I had to purchase from both Aircraft AND Automotive AN suppliers, There was never a problem with compatibility , because I made sure I got the correct bits. My suppliers were: https://www.asapspares.com.au/ https://www.aaestore.com.au/ https://aeroflowperformance.com/catalogue-2024 Between the three suppliers listed I almost always got the part(s) I wanted, when wanted. Aeroflow have an an amazing range, usually but not always, cheaper than the aircraft parts supply people. Take the time to familiarise yourself with how the catalogue woks, some "stuff" is in categories that you may not at first recognise. If you don't already have the pipe cutting, bending & flaring tools, be sure to shop around - the cheap ones will, with a bit of practise & care, do the job, leave the expensive stuff to the dedicated multi kit builder and professionals. Making consistent well formed flairs, bends without flattening/kinks, is a skill, take time to practise until you get it right - I found using a little spray lithium grease helped in most situations and be sure to deburr before flaring.😈
-
Did a little research(better than faulty memory) - Think I probably had a Barbour jacket & over trousers. Good in UK summer, okay in light, short duration rain - bloody awful in heavy rain, winter cold, sleet, etc😈
-
Oh well, cant get satisfaction every time, "said the actress to the bishop"😈
- 34 replies
-
- 2
-
-
Very clever - the kit comes with a a 25 MM ID hose adapter - not so many joins after all. "........don't understand about having different radiators for aircraft with different performances....." Its not a question of me not understanding that coolant radiators must be specified for diffrent engine sizes/applications, etc, its wondering why your kit supplier sees fit to not use the Rotax OM Radiator, that has been developed for the engine and what seems to be satisfactory in a host of aircraft from low/slow to high speed, pushers and tractors. Nothing sinister or argumentative , just curious 😈
- 34 replies
-
- 1
-
-
It will be very clever, if you have managed to go from Rotax to Setrab, without some form of reducer. My guess, a minimum of two extra joins, over that for a hose Rotax to Rotax.😈
- 34 replies
-
All good BurnieM. A very long time ago, I spent 5 years in the UK. My transport, for much of this time, was a Triumph 650. I had leather boots & gloves, the latest (at the time ) in all weather motorcycle gear - Berber/Burberry/Barba(?) heavy waxed over jacket & trouser. Open face helmet, traditional googles and leather face mask. Despite all sorts of strategies - newspaper under jacket (s), 2 pairs of trousers, wool & cotton socks, oversized rubber kitchen gloves over leather bike gloves, plastic bags over feet - I FROZE!!. The UK was/is a cold wet place - There were times I had difficulty opening my hands, after an extended winter ride. No amount of Dubbin seemed to keep by feet & hands dry, even the rubber over gloves/bags only had limited benefit. There is no doubt that I am a "lizard", much prefer heat to cold, so forgive my rejection of your, well considered, cold weather strategy - no offence intended😈
-
I have never suggested you (Zenith et al) are wrong, only that the approach is somewhat unconventional. I like unconventional, especially when it works. Despite this I am not a fan of "reinventing the wheel" for no apparent gain. I still wonder at the choice, given the diffrent viscosities of oil & coolant (water) and I assume the Setrab heat exchanger has been optimised for oil (it looks like an oil cooler). In addition, the Rotax 9 coolant system will have 25 mm OD hose connections , so at some point reducers will have to be fitted to get down to the Setrab inlet/outlet dimensions - added weight, more joins ????😈
- 34 replies
-
- 1
-
-
From another Forum: An Australian pilot : " I used battery powered Ororo branded socks for a while but found them uncomfortably narrow on the foot and tight around the calves. Over the last few years I’ve used stick on toe warmers available at most pharmacies. I find them to be effective" https://www.chemistwarehouse.com.au/buy/83839/hot-hands-toasti-toe-warmers-5-pairs At $7.00, I think I should give them a try😈
-
Speculation: For Rotax 9 powered aircraft, high / low / rotating, the Rotax radiator is the norm - Your dual purpose oil/coolant, the exception. Nothing wrong with that of course😈
- 34 replies
-
- 1
-
-
- 34 replies
-
- 1
-
-
I didnt not suggest using an oil cooler, for a coolant radiator, would not work, only that it may not be the best design for the job. Oil coolers usually ; Are of heavier construction, than needed for coolant - in aircraft all unnecessary weight is usually avoided Have smaller ID inlet/outlet pipes - this may result in the need for pipe reducers, more weight & complexity When perfectly satisfactory dedicated Radiators & Oil Coolers are available, I wonder why you or is it the kit supplier, would choose to do this??😈
- 34 replies
-
Yes - as I acknowledged BUT how effective is the Setrab in BOTH roles??? Seems to me that if an oil cooler can be used as a coolant radiator, then this would be common practise - last time I looked its not. I would like to know the technical reasons why not.????? I am sure there are Forum members who would be fare more qualified to debate this than me😈
- 34 replies
-
There seems to be a small confusion in this thread between Radiators & Oil Coolers. Radiator - Name commonly use for coolant heat exchanger Oil Cooler - Name commonly used for - you guessed it, oil heat exchanger. In both cases they are air/liquid heat exchangers (there are liquid/liquid heat exchangers). Many similarities however, their design differences tend to reflect liquid viscosity and expected temperature & pressure ranges. Not saying that the one heat exchanger design, could not be used for oil or coolant, however I have never seen this and I would suggest that the targeted liquid is more likly to be efficiently cooled eg Danny-G's Setrab example looks to me to be an Oil Cooler., while Rodgerc's is a Coolant Radiator😈
- 34 replies
-
Thanks Thruster however its the calves & feet that are cold not my upper body, head and hands. IF THEY WORK the socks (which brand?) will be the perfect , well targeted, cost effective, solution😈