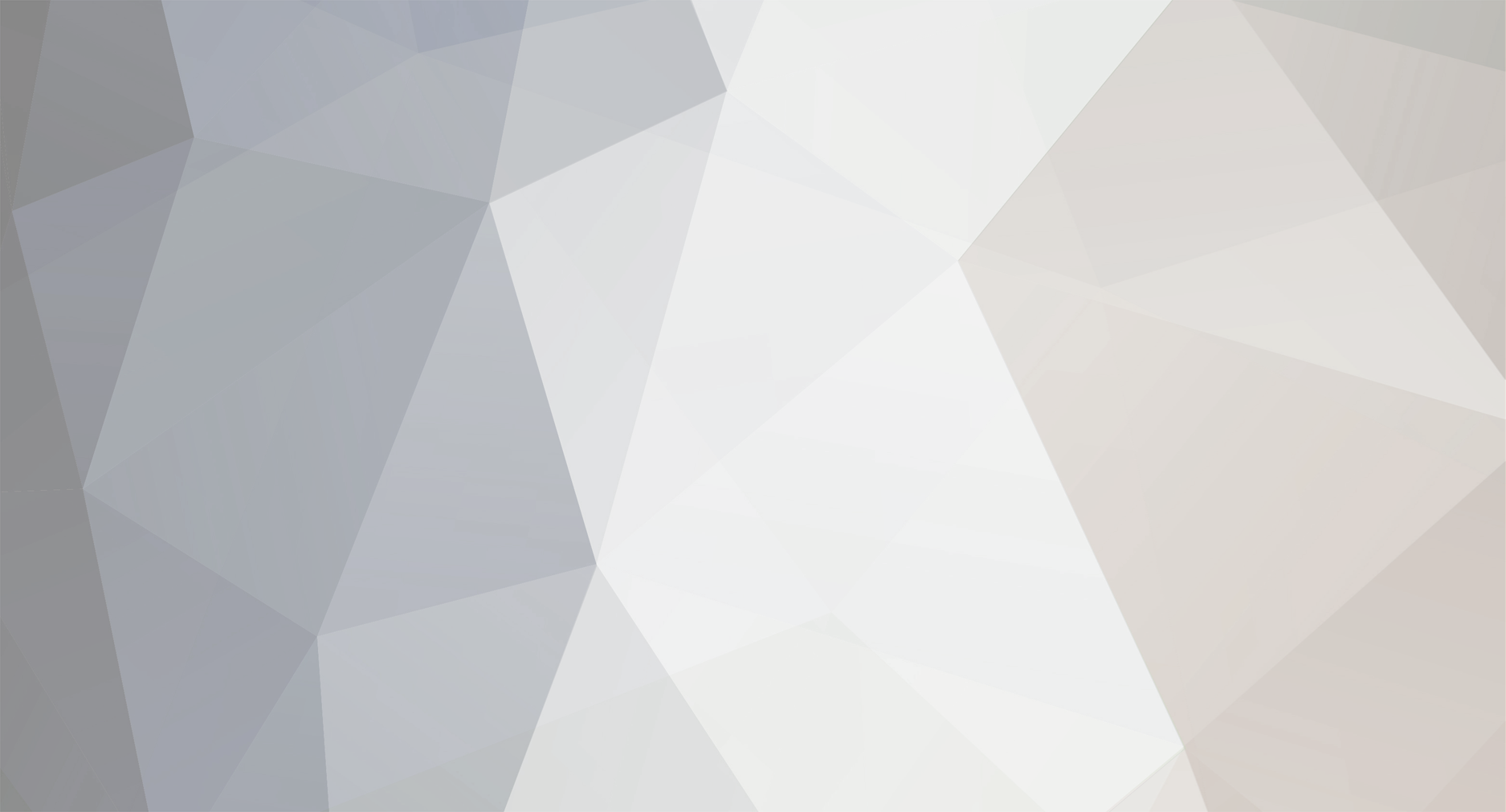
Markdun
Members-
Posts
357 -
Joined
-
Last visited
-
Days Won
4
Content Type
Profiles
Forums
Gallery
Downloads
Blogs
Events
Store
Aircraft
Resources
Tutorials
Articles
Classifieds
Movies
Books
Community Map
Quizzes
Videos Directory
Everything posted by Markdun
-
Obviously they don’t ascribe to the notion of ‘don’t look up’. And I suppose there wouldn’t be much left of 3.5t 12m catamaran dropped from 500’... obviously it would all be still there on accordance with the laws of thermodynamics, but in small pieces according to entropy. How do gliders get away with dumping ballast, &/or lighter than air aircraft?
-
The guys operating the big Helios had the call. They were wanting to generate more income in off-fire season ‘downtime’. In their view it was a rule intentionally made to prevent Helios competing with existing fixed wing and road transport freight haulers. There is an insurance issue as well.... if anything goes wrong with a helio lift the first item on the checklist is ‘release the cargo’.
-
CASA probably wouldn’t allow freight. I tried to hire one of the firefighting helicopters to lift an 11m x 6m, 3.5 tonne sailing catamaran from my front yard in Canberra to Batemans Bay. Cheaper and potentially less hassle than a wide load permit with police escort etc. Guys operating the helio said it would be easy except for the requirement that any and every public road we flew over had to be closed to prevent the risk of the load falling on a car. So it was the wide load permit with 3 escort vehicles, plus two police escort vehicles, 100 pages detailing traffic management plans for every intersection and breakdown pullovers every 20km etc etc rtc etc and 5 months for a bureaucrat to approve. The actual move took 6 hours (yard to floating boat); & police not interested in the approved 100 page plan (fuck that, we will just do it this way, ie drive down on the wrong side of the King’s Hwy with our lights flashing and try to keep up with us). A dirigible would have been far better.
-
So no progress on ‘no molecules’, just a vacuum? ....far less dense than H2 gas & not flammable. Easy to adjust buoyancy by pumping stronger vacuum to go up and letting atmos gases in to go down. Issue is finding open cell rigid foam that is of sufficiently low density and compressive strength to withstand vacuum, or alternatively a carbon fibre egg-shell type structure.
-
Fuel flow sender/sensor options
Markdun replied to trailer's topic in Instruments, Radios and Electronics
Me too. With fuel I’m ultra-conservative; none of this laissez faire lefty progressive nonsense. On a delivery flight from Northam WA to the ‘East’ with the aircraft picked up from one of the worst LAME in the country who only fixed the reported fuel leak after I got the Avgas shower from the leaking fuel pooling in the wing and then emerging from the wing root when you opened the cockpit door. With that fixed we then flew to Kalgoorwhere I spent full day to redo numerous other non-fixes including reconnecting one wing tanks fuel level sensor... connector corroded off. Next leg was a long one to Forrest following the railway. Every 20 minutes I recalculated fuel used and remaining from fuel tank level gauges, fuel flow meter (JPI) which we hadn’t calibrated, and estimated from engine performance data in the POH; each confirming each other...a tight cocked hat if you like and understand old fashioned navigation. The owner in the right seat was amused. This helped me in deciding whether to land at one of the railway landing strips every 80nm, head south to the coast and highway, or continue on to Forrest. We departed full at 100litres, I’d planned on landing with 20 (or 15 if headwinds arrived); my 3 calcs at the last railway emergency landing strip estimated 25l would remain, and the bowser at Forrest confirmed 30 was remaining. BTW the JPI was quite accurate despite the unmetered Rotax return fuel line to one of the wing tanks. -
Fuel flow sender/sensor options
Markdun replied to trailer's topic in Instruments, Radios and Electronics
Biggles that’s the averaging or smoothing algorithm the display uses. In my Corby I have both the MGL and the old Navman wired up to the same old Navman FF sensor. Both displays get the wobbles, but different wobbles, when the electric Facet pump is on & neither give info on the averaging methodology they use. There is also fluctuation with the carb float bowl needle and seat opening and closing, most significantly at idle. In a lot of respects the display of FF to+/- 0.05 lph ie to 0.1lph is a misleading distraction. -
Fuel flow sender/sensor options
Markdun replied to trailer's topic in Instruments, Radios and Electronics
I use fuel flow data for three main purposes: first, as a power setting...I find rpm pretty hopeless as an indicator of power as it’s too dependent on vertical speed (noting that fuel flow will increase a tad when you put the nose down & rpm increases with no change in throttle position; second, for calculating fuel remaining (which is cross checked to fuel level, either visual sight or fuel level sender); third, as a check on full power fuel flow at WOT during climb out. I find that once you have calibrated the fuel flow sender they are very accurate, even on Rotax with a fuel return line. But that’s the issue... calibration is a RPIA & can take a while. On my Corby I have an old ‘Navman’ sensor connected to an MGL XTREME EFIS/EMS. This was a dream to calibrate as the Corby’s fuel tank is 40l and easily measured with a dip stick. Fuel remaining cross check is to a resistive float fuel level sensor. Cost of the sensor was zero as I liberated it from a yacht. It has an axial turbine which allows fuel to flow even if the turbine seizes. Most accurate when mounted vertically with fuel flowing upwards. Sensor is plastic, but I had it for 700 hours in the Cygnet without any issues. It is still working well. On the Cygnet I have a Red Cube. I did have the Navman but when I converted from Vw to Jabiru the Navman couldn’t deal with the electrical voltage spikes from the Jab voltage regulator. But then neither did the Red Cube which I purchased on eBay for a good price. Problem was fixed by installing a Powermate VR. The Red Cube works... cant say It’s really any better than the old Navman. Again it feeds data to an MGL XTREME. Fuel remaining is cross checked with a visual fuel level. On the J200 I have a Flowscan sensor which came with the aircraft and which was submerged in floodwater for several weeks. It too works well but I’m struggling with calibration.... again mainly due to electrical interference from the Jabiru voltage regulator. It is cross checked to the Jabiru ‘fuel level’ sensors (sight gauge, mech gauge & electrical level), which in my limited experience are all total crap. This also makes calibration really difficult. I’m thinking it’s going to take quite a lot of flying to get the fuel flow sensor in this aircraft calibrated accurately. With less than 10 hours in this aircraft it’s still ‘work in progress’. I also have a non-turbine FF sensor in my boat...it a Lowrance. I’m not a big fan. The range of fuel flow is from zero to 8lph? but mostly around 2.5-3.5lph...it just doesn’t like that...& it cost heaps, often reads zero until you give it as tap. It connects via Ethernet. If I was looking for a sensor I’d be scanning eBay. For new .I would probably give the MGL plastic one a try, but that would be an experiment. -
Any news on Wedderburn aircraft accident 26/12/22.
Markdun replied to Geoff_H's topic in Aircraft Incidents and Accidents
Bruce, the thing is people are people; they make mistakes and forget things, underestimate risks, get sucked in to confirmation bias. etc etc. The consequences when flying are more severe. Crash a 1800kg car with a well designed steel cockpit protection at 80kph & you have an excellent chance of surviving. Keeping in mind the kinetic energy to dissipate in a crash is 1/2mv**2, and compare that to crashing a 600kg aircraft made out of aluminium foil or sticks and paper at 120kph or more... you have less chance. In my youth I did a fair bit of rock climbing & thought that was pretty safe. Then I did a season of mountaineering and found, unlike rock climbing, you really had to trade off protection for speed (to the top) to (a) successfully climb the peak; & (b) to avoid the bigger risk of warm afternoon ice avalanches killing you on descent. I lost one friend on Mt Aspiring...avalanche on ascent.... something that you really cannot mitigate against except by not doing it. And then a few months ago a kid in my son’s TAFE class was killed abseiling because he simply clipped onto a rope that wasn’t tied on, despite checks and second person checks. I stand by my earlier statement that flying light aeroplanes is inherently dangerous; it is misleading and dishonest to represent it as a ‘safe’ recreational activity as Ra-aus do (& really why else do they carp on and on about safety if it was safe?); & we should accept that and learn to live or die with it, not ignore it, but always have it mind. -
VW based engines. Pros and cons from users?
Markdun replied to danny_galaga's topic in Engines and Props
I’ll chime in here agreeing with Don and Roger. I have a bit over 900 hours behind a 1/2VW and a very simple 1835cc conversion. The pros are that they are cheap and easy to work on; they work and get you flying. The cons are the poor power to weight ratio, and the required ‘tinkering’. The 1835 was lucky to produce 55hp (proponents claimed 64hp.... perhaps hp is a unit like the gallon which in the US is a lot smaller than everywhere else?). I did a valve lap and replaced the piston rings at around 500 hrs. It was an ultra simple conversion: home made heat shrink hub; std vw crank, a single ignition from a vertex ignition bunged into the std distributor drive ( made an interesting cowl bulge); a Bing CV32 carb from a BMW R80 boxer; & a small 5A Honda charging coil with PM rotor bolted to the rear. The only issue was the prop to hub flange which delivered me to the canola paddocks twice. The half VW gave me more woes, but this was more to do with my experiential learning and then belief I could plonk the Minimax (Vso=20kts) just about anywhere for an outlanding, which I did. This included an EFATO at <100’ from a broken head bolt (lesson: in sub-zero temps warm up engine for longer); broken rocker shaft bolt (dont use really old bolts); broken crankshaft 2 hours after a prop strike (yeh, yeh....how effing stupid was that). and an intermittent ignition coil fault that nearly delivered me into the wilds of the Deua R (don’t mount ignition coil on top of s very vibrating engine). In hindsight I’d do it all again. I converted my Corby from VW to Jabiru mainly because Id already done a VW to Jabiru conversion on the Cygnet and was very happy with the extra power and lower weight of the Jab. -
Any news on Wedderburn aircraft accident 26/12/22.
Markdun replied to Geoff_H's topic in Aircraft Incidents and Accidents
Mmmm. I’m not flying to Wedderburn, but my airstrip south of Tarago is 745m long has trees, large..ish, on both sides 30-40m distance (15-20m from airstrip centreline) which gives reasonable clearance. It is oriented for the prevailing NW & SE winds. In most cross wind situations the wind diverts to run down or up the runway, or it is effectively calm, once you are below the tree canopy. The thing is you have to prepare for the windshear as you descend (or ascend) through a very short zone of turbulent air. I generally add 5-10kts, and this means one generally has excess energy to dissipate once below the tree height on landing (& you land long), or on T/O you remain ‘tween the trees for longer to accelerate resisting the urge to get away from the trees. I feel comfortable T/O & landing the Cygnet in 20kt x-wind, but by golly I wouldn’t try it in the Corby or the Jabiru despite their tiny wing spans. I’m just saying trees are not always bad. Any Pax, like sons’ latest girlfriends, need warning that landing looks daunting, particularly when you fly sideways to descend rapidly to get below the trees. -
Any news on Wedderburn aircraft accident 26/12/22.
Markdun replied to Geoff_H's topic in Aircraft Incidents and Accidents
Injury rates are pretty extreme for horse based recreation (for ppl & the horses), but lawn bowls and golf are the most deadly. I think those of us involved in recreational aviation do it a disservice by perpetuating the lie that it’s a safe past-time. Ra-aus would get heaps more members if they stressed the dangers of flying, that after each flight the great achievement felt by the pilot in cheating death etc etc, rather than, if you check these boxes it’s all very safe. -
Any news on Wedderburn aircraft accident 26/12/22.
Markdun replied to Geoff_H's topic in Aircraft Incidents and Accidents
I’m told the aircraft attempted a downwind landing, bounced/wobbled several times and then powered up for a go-around with a very low turn. My interlocutor said the pilots held licences & were very experienced with heavy aircraft. How accurate this info is, I don’t know, but it comes from an owner of an aircraft at Weddernurn. -
Trailer, if you need a needle and seat you can buy them from Jabiru snd probably Munich Motorcycles. The Jabiru Gen 3 Overhaul Manual describes how to remove the old seat and install a new one. But my understanding that is mostly done as a modification for the 3300 to increase the the diameter of the hole in the seat to increase fuel flow to the bowl. It’s more common to just replace the needle ... it has a ‘rubber’ tip and these can degrade. I am assuming you are referring to the needle and seat that controls the level of fuel in the float bowl and not the ‘needle jet’ and needle that controls the fuel flow from the bowl to the intake plenum at cruise settings.
-
Crash at Caiguna today 16/12/22.
Markdun replied to Markdun's topic in Aircraft Incidents and Accidents
Prior -
Crash at Caiguna today 16/12/22.
Markdun replied to Markdun's topic in Aircraft Incidents and Accidents
Onetrack the source for the Cessna comment was according to some news outlets, the WA Police; ATSB then corrected this with the media. I think that’s excusable. -
Crash at Caiguna today 16/12/22.
Markdun replied to Markdun's topic in Aircraft Incidents and Accidents
ABC says a fatality. Do I post the 3 pics I have of the engine when it was at Caiguna yesterday? -
Crash at Caiguna today 16/12/22.
Markdun replied to Markdun's topic in Aircraft Incidents and Accidents
Thanks. I’ll pass that on to a matter who was at the airstrip early this morning. -
Just heard that a ‘light plane crashed at Caiguna this morning. Don’t know any details or if anyone was injured but police are going to attend. Yesterday two Jabirus (a 55 and a J160) landed at Caiguna. The 55 had a list of woes, including main earth cable to engine sawn apart by flywheel, prop had lost 15cm of fibreglass sheathing on one one blade (the tip), and a substantial oil leak on the starboard side enough to oil up the windscreen. It was a ferrying job west to east. This morning wind was 20kts with a large cross wind component and early in the morning it was raining. I’m assuming the crash was most probably one of these aircraft. The strip is 1300m x 30m and just been refurbished.
-
Most calls aren’t ‘5nm SE, 4500’, they are ‘over the chook farm’, or ‘training area, 4500’, which is just dandy if your are unfamiliar with the airfield. Again in boating GPS derived Lat,Long in degrees & minutes has de facto become the standard for position reporting; no more 15nm NE of South Solitary. Only problem is many boaters (& coastal ‘marine rescue’) seem to think giving minutes of Lat & Lon to 4 decimal places is necessary. Are we drifting from the topic? I’d like to know if RFguy has written the code yet for a software upgrade for Dynon, MGL EFISes with ADS-B in or OzRunways etc that will provide proximity/safe separation info and warnings?
-
Yes. ‘See and avoid’ is total bullshit. The only planes you see are the one moving with respect to your aircraft, ie. these are the ones that are not on collision course. In other words you automatically will avoid the planes you see., so in that sense the planes you see you will avoid. The ones you don’t see, i.e. the ones not moving in relation to you, are the ones you won’t avoid, but need to. On the boat the only way you tell if you are not on a collision course with another moving boat or a stationary object like a rock is to take a bearing; if the bearing remains constant over time you’re going to crash. It still requires you to see the non-moving (with respect your vehicle) object in the first place and have time to assess it. But in the air, IMV, ‘see & avoid’ is simply relying on the low probability of a collision as others have said earlier.
-
It all depends. My main motivator in getting and using the SkyEcho was to avoid heavy military Rotary aircraft at circuit altitude & below over my airstrip. I missed one by several hundred metres on downwind on one day; they didn’t respond to my radio call and subsequent correspondence with the military was that they just use ‘see & avoid’ in class G. So yes, I currently use ADSB for in circuit at my place.... but at Goulburn, no, because most aircraft don’t have it turned on or installed (you would think training aircraft would have ADSB out wouldn’t you?).
-
In the boating world the ADSB equivalent is AIS, albeit it’s only two dimensions and the velocities are an order of magnitude less than aircraft. That said, away from congested waters like Sydney, I’ve found the AIS system fantastic. I can program my GPS/chartplotter to give me a warning if another boat is predicted to intercept my predicted position by a certain distance (say 1nm) or time. While the data from other boats does include its velocity and the first derivative (rate of turn), I’m pretty sure it just predicts the intercept based on current position and velocity( course over ground and SOG). Further the data from other boats includes their MMSI number which enables you to call that boat’s bridge by DSC on the VHF radio. If they don’t respond you can up the urgency and initiate an alarm on the bridge. In my experience ships respond... I call them, give my position via bearing and distance and ask if they see me on their radar... they never do. Generally, I advise them I will change course to pass them port to port, and on a couple of occasions they have volunteered to speed up or slow down to give me greater clearance... this in more confined coral reefed waters. But it’s bloody useless in Sydney..... it’s just distracting noise.... there are so many potential conflicts the system just can’t cope. I think the same might apply to ADSB in aircraft. In the circuit forget it.... too much else going on. But on a cross country being notified of any traffic likely to come within say 3nm or 1000’ vertically, or a specified time, would be very handy. It’sa pity our VHF radios are so dumb and can’t use the ICAO number allocated to each ADSB transponder to call the other aircraft via a DSC channel. And there is the problem that many aircraft monitor the incorrect frequency. Where I’m located the class G airspace ‘area frequency’ is the same as ‘Canberra approach east’. My neighbour with an autogyro only monitors 126.7 on the advice of his CFI in Wollongong and is resolute in not giving a broadcast on, or listening, to the area frequency because he thinks he’ll get into trouble with ATC. We both operate out of uncharted private airstrips. BTW, organising an in air rendezvous with ADSB is amazingly easy and a little bit scary.
-
Did you know there was a three engined 747?
Markdun replied to red750's topic in US/Canada General Discussion
Ohh, I thought they were just carrying a spare as one or more of the others were a little dodgy ‘on condition’. & isn’t that why they take an engineer ... to do the mechanicing en-route? On my yacht I carry a spare short engine and gearbox... but invariably it’s usually a small ancillary like a CDI ignition charger coil or trigger, or the friggen oil pressure sensor that fails. Stuart, the back of the J200 is for the galley and hammock? -
Did you know there was a three engined 747?
Markdun replied to red750's topic in US/Canada General Discussion
So if a 747 can carry a spare engine sound underneath (Making off field engine replacement possible?), do you reckon I could sling a spare Jabiru 3300 underneath the J200 for when....? -
Did you know there was a three engined 747?
Markdun replied to red750's topic in US/Canada General Discussion
Quite a while ago (>10 years) ATC at Sydney noticed a 747 taking off with only 3 engines working. They queried the pilots who responded that that engine hadnt been working for a month. It was, I think, a Chech republic company that we’re doing a once a week flight to Sydney.... very lightly loaded. Their approval was subsequently pulled. My source was a senior engineer with Airservices. So there was a de-facto 3 engined 747.