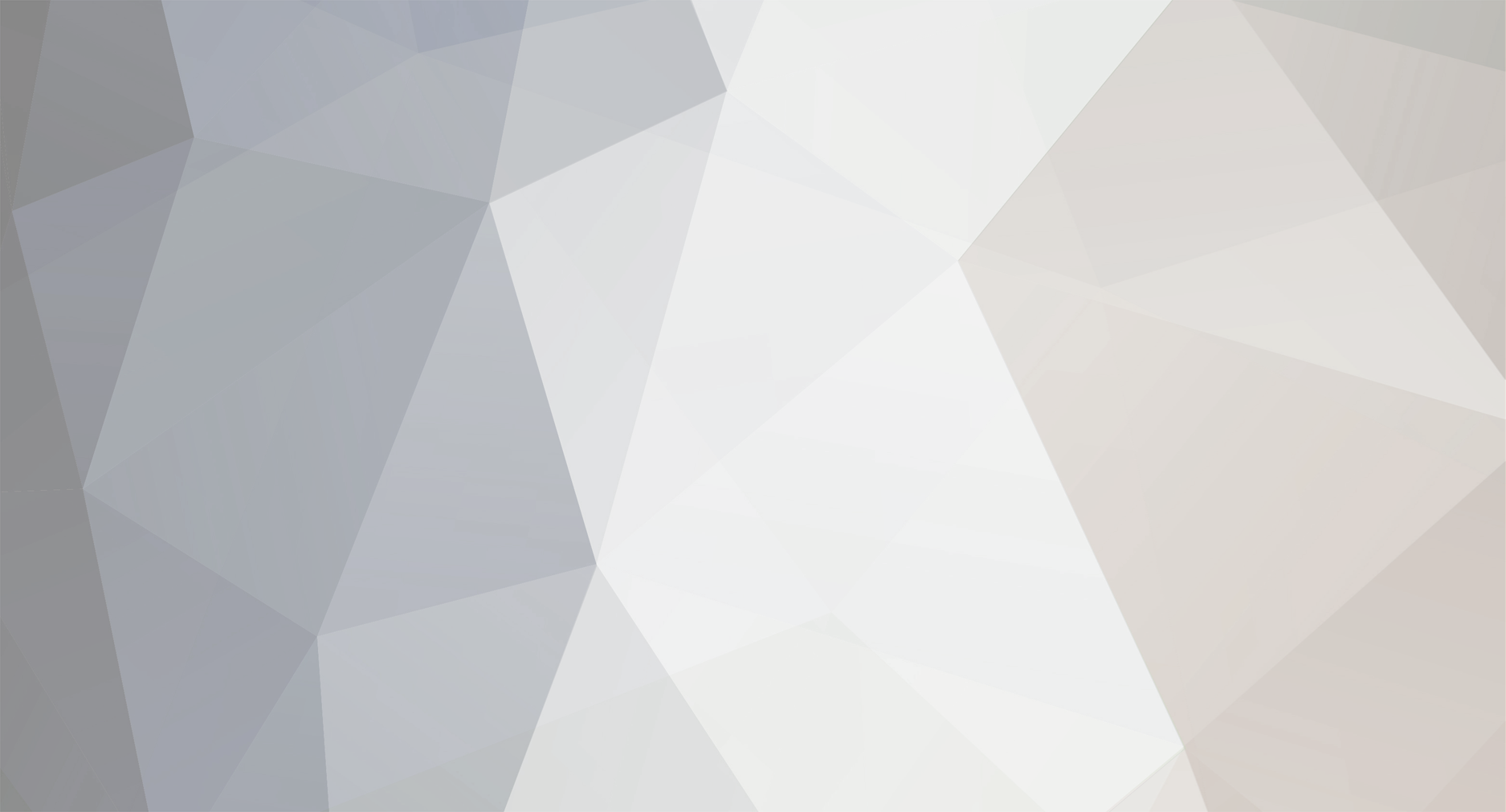
Markdun
Members-
Posts
357 -
Joined
-
Last visited
-
Days Won
4
Content Type
Profiles
Forums
Gallery
Downloads
Blogs
Events
Store
Aircraft
Resources
Tutorials
Articles
Classifieds
Movies
Books
Community Map
Quizzes
Videos Directory
Everything posted by Markdun
-
Was it a meteorite? Brings to my mind when I was sailing from the Percy Is to Great Keppel a few years back and at 3am I saw what I thought was a red parachute flare. I was about to radio in a relay mayday except the red flare appeared to accelerate over me along with a sonic boom and roaring noise heading south east where it disappeared. Definitely was not an hallucination as it was a typical dead flat inside the reef QLD sail, so no need for the coloured dreams scopolamine patches.
-
Consider installing a smoke system which you turn on in the circuit…that might make you more naked eye visible to others. Glen, the other thing with a passenger is to enlist their assistance in eyes out of the aircraft, because as we know, most ppl are doing pre-landing checks on downwind (distracted) & mainly concentrate on outside visual observation for other aircraft just before turning onto a circuit leg. Yeh I know that even that, as is all ‘see & avoid’, will be crap because the human eye/brain is just not effective in picking up ‘non-moving objects’ in the sky; ‘see & avoid’ fails at the ‘see’ because you just don’t see intercepting traffic. Raymarine and Lowrance also produce low power(digital) 360 degree 10nm radars which ought to pick up other boats/aircraft ~$3k. The radome is a cylinder about 50cm dia & 15cm high. They are normally bolted onto a yacht mast spreaders, but I’m sure you could fashion a streamlined fairing to mount above the fuselage in front of the vertical stabiliser.
-
VW based engines. Pros and cons from users?
Markdun replied to danny_galaga's topic in Engines and Props
Yes, VW conversions were notorious for icing, particularly at the lower ‘T’ join where the two sides came together at the rear bottom of the crankcase, as seen in the pic above. A simpler solution is to weld a thick steel tang (not stainless) to that T which bolts to one of the crankcase bolts. This conducts heat from the crankcase to the T. Oh, and also have a carb heat system. I flew behind a VW conversion like this for over 700 hours mostly in the southern tablelands of NSW and never once had to pull carb heat despite flying in icing conditions. Mark -
-
Why didn’t you go into class E, as you do have the SE2?
-
Many years ago I was asked to pay import duty on a box of parts (mostly AN bolts) from Aircraft Spruce clearly labeled ‘Aircraft parts’. I was initially told that because they were ‘bolts’, duty applied. After a bit of a whinge from me, ‘ the parcel is marked ‘Aircraft parts’ and that’s what they are so the duty is zero’ etc, including asking how I could formally have the decision reviewed, the duty ‘charge’ magically disappeared. I think the big part of the problem was that the courier was DHL and it was their ‘try on’ rather than customs as it was then. But to the present I thought that import duty has for the most part been abolished (except luxury cars etc) and in its place you pay GST, plus the shonky non-tax tax of Home Affairs (Customs) charging you a handling fee plus a fee for paying the GST (or something like that). So if you paid AUD$5,000 for that box including shipping, that would mean $500 GST plus the handling fee and fee for paying the GST, so $750 would be about right.???
-
Thanks Glen. When I’m next asked for any medical conditions I suffer from I’ll add ‘inept’ along with ‘intolerance’. -:)
-
ADSB Grant Skyecho 2 etc
Markdun replied to Kyle Communications's topic in AUS/NZ General Discussion
That doesn’t seem correct. When ADSB was first being introduced the RpT industry (Q &V) were prepared to pay Airservices for all aircraft to have ADSB out fitted for ‘free’ to the aircraft owner on the basis it would save them more money in fuel savings particularly at regional airports, ie based on then using ADSB ‘in’ to avoid recreational and charter aircraft etc. The recreational side of aviation like GFA and RA-Aus were apoplectic with rage that this would herald in Big Brother and every RA-Aus flight would end with 3 AFP vehicles a CASA inspector and the arrest of the RA-Aus pilot on terrorism charges to be tried in a secret Star chamber court. The GFA has concerns that no glider could thenforce ever climb a thermal because of the mass of the battery to power the ADSB device. Oh, how times have changed. But I’m happy to concede that perhaps RPTs didnt fit ADSB in because without the surety that all aircraft have it, what’s the point? I fitted the SE2 after having the shit scared out of me by a heavy military helicopter travelling in the opposite direction to me at my altitude while I was downwind 1000’agl in class G airspace. We missed by about 250m. They weren’t on the area Frequency. My subsequent follow up communication with them indicated they rely solely on ‘see & avoid’, ie roulette, but ‘usually have the ADSB turned on’. And the SE2 has been fantastic for avoiding them since. -
I shouldn’t be so obtuse. The SE2 is well known for failing LEDs. I’ve had one replaced on warranty. This one I know of the GPS LED is blank, that’s equivalent to green. Any thoughts on an inductive passive GPS antenna for it, say built into a mount?
-
I think my SE2 has the GPS accuracy indication correct. When it’s first turned on its one green and two reds on the LEDs and once it’s going ‘properly’ its 2 greens and a blank for the GPS led.
-
Tidy Corby Starlet. 450 hours TTIS airframe. Restored 2018 & re-engined with a fully overhauled Jabiru 2200 with 150 hours now. Absolute joy to fly. MGL EFIS/EMS, mech back-up ASI, G meter, fuel flow, Becker VHF. Easy cruise at 110KIAS and climb rate 1500-2000fpm; stall around 32-34KIAS. Will only sell to good home. She needs someone to fly her more often than I do. I will consider delivery.
-
The trouble with those numbers on torque is that what you are seeing is variation from other variables, which are unrelated to bolt tension which torque is merely a proxy for. I doubt the head cap screws are the same alloy as the cylinders and the variation are probably more to do with varying electrolysis / corrosion of the threads of the cap screws in the cylinder. Most likely the lower head screw has less corrosion and moves easiest. FWIW I think the purpose of head bolt tension checks is to assess whether there is recession, except perhaps a check at 5-10 hours after the head has been replaced. As such I think it is better to do head bolt tension checks far less frequently than specified in the maintenance manual, and to do the torquing properly, ie dynamic by backing off and then re-torquing. And given how easy it is to pop off the head on the Jab to have a squiz, why not do that at 300 hours?
-
ADSB Grant Skyecho 2 etc
Markdun replied to Kyle Communications's topic in AUS/NZ General Discussion
A couple of years back I asked ATC when I was 25nm east of Canberra at 4500asl. They had nothing from the SE2, but I was visible with the Mode C xpndr. We also checked whether Musk’s satellites could pick up the SE2 (my brother as the global lead ADSB engineer as he was then, had direct feed from the satellite system) and it didn’t, even with us fiddling with orientation to maximise emissions towards the satellites. That’s the consequence of the low 25w power of the SE2. I really don’t understand what ‘calibration’ an installer does, or is this another bureaucratic totally meaningless word like ‘committed to’ & ‘take seriously’? -
Just saying, all the comments about this new form of anarchists might not apply to this defendant as it was only the prosecution’s assertion. We have the debacle in Sydney that the police invented a ‘fact’ that an ambulance was blocked crossing the Sydney Hbr Bridge by a protester and this resulted in her being remanded despite it having no foundation. Is that possible in QLD? Also laws theoretically apply to all ppl, citizen or not. I say ‘theoretically’ because whether someone is prosecuted often depends on their gender, skin colour, social standing etc etc etc. So I’m not so big on responsibility to the state. however, my whinge is big corporations paying zero or very little tax still demanding the protection of our laws and courts to enforce commercial contracts & protect their interests and their owners liability is ‘limited’. That said, I agree with all the comments about the dip shit ‘sovereign citizens’ & the RWNJ ‘freedumbers’.
-
Best to look up the actual law, and it looks like QLD is quite a bit different to NSW. Below is QLD. So arguably, if you are flying unlawfully (without a BFR, no log book, with an expired ERSA, or in an unregistered aircraft, unlicensed) you could be done for manslaughter, and depending what ‘unlawful purpose’ means legally, murder. That’s not an easy question to answer. In 1775 a Miss Johnson contracted with a carriage maker (Holmans) to construct an elaborate carriage for her to tour the streets of London to drum up business for her very successful brothel. She took delivery of the carriage and refused to pay Holman (perhaps the gold leaf wasn’t thick enough or velvet soft enough?). Anyway the court rejected Holman’s case saying they would not give support to an unlawful and immoral contract. This precedent was watered down substantially by Australia’s High Court over whether a NT pastoralist had to pay a water bore driller’s invoice for bores drilled illegally which didn’t find any water. They said the pastoralist had to pay. But that’s civil, not criminal. However, in NSW some druggies invaded a Sydney house for robbery (unlawful purpose), were caught by the occupants who tied the two of them up, called the police, and while the police were on their way, gave them a bit of a whacking with a cane. Result was that the occupants were convicted of GBH, despite a statutory provision which purported to give them immunity (the reason was that once the robbers were tied up, they were no longer engaged in an unlawful purpose, they were prisoners). I think there is a lesson there re sequencing of actions. Anyway, a long winded way of saying flying unlicensed may not be an ‘unlawful purpose’ in itself as opposed to, for example, if you were stealing the plane. CRIMINAL CODE 1899 - SECT 302 murder 302 MURDER (aa) if death is caused by an act done, or omission made, with reckless indifference to human life; (b) if death is caused by means of an act done in the prosecution of an unlawful purpose, which act is of such a nature as to be likely to endanger human life; manslaughter 303 MANSLAUGHTER
-
Just refreshed my memory on NSW law on negligence (Civil Liability Act). I used the word ‘inherent’, it’s ‘obvious’ risk. Relevant provisions set out below. I think Qld is much the same. Oh, and when I said the tort reforms didn’t work, that was in respect of lowering insurance premiums; they definitely worked in limiting ppl’s rights to sue and insurance payouts and increasing insurance company profits. FWIW my view is we should have copied the NZ no fault accident compo scheme; it’s by no means without problems, but saves the country heaps in insurance and legal costs. Of-course, this doesn’t help the guy on criminal charges, nor the guy killed. Also think about the RA-aus insurance.... it really is limited to personal injury of ppl not engaged in flying or 3rd party property damage (power lines, fire started etc). DIVISION 4 - ASSUMPTION OF RISK 5F Meaning of "obvious risk" 5G Injured persons presumed to be aware of obvious risks 5H No proactive duty to warn of obvious risk 5I No liability for materialisation of inherent risk DIVISION 5 - RECREATIONAL ACTIVITIES 5J Application of Division 5K Definitions 5L No liability for harm suffered from obvious risks of dangerous recreational activities 5M No duty of care for recreational activity where risk warning 5N Waiver of contractual duty of care for recreational activities CIVIL LIABILITY ACT 2002 - SECT 5L No liability for harm suffered from obvious risks of dangerous recreational activities 5L NO LIABILITY FOR HARM SUFFERED FROM OBVIOUS RISKS OF DANGEROUS RECREATIONAL ACTIVITIES
-
Old Man Emu, your quote is consistent with the common law and Cth Criminal Code on criminal negligence with the exception that some of your previous comments on the the onus of proof is at odds that in a criminal trial the onus is always on the prosecution (well nearly always). ‘Criminal negligence’ is a common law crime in itself, and the elements of the offence are the same as the civil tort of negligence except that a jury has to conclude that the negligence was so bad it warrants a criminal conviction. Manslaughter by criminal negligence, as the judge pointed out, is slightly different in that the negligent act replaces the fault or intent element for manslaughter. Normally that requires an intention to cause the other person harm or recklessness. Again, some negligence is ok; it has to be so bad that a jury considers it warrants being a crime, & in sense of it ever got to a jury in my view the ‘pub test’ would sink the defendant. I would think in this case the defendant would have reasonable prospects to argue, with evidence, that failure to have licence or comply with the registration/maintenace rules were not, beyond reasonable doubt’, causative elements for the death. For example it would seem he had 10 years of safe operation and lots of other ‘compliant’ operators have crashed/rolled over on beaches. The strict liability issue will depend on the specifics of the legislation. But even there, the onus is on the prosecution to prove, & it would not be the first time that that charge of flying unlicensed was dismissed because CASA made a mistake. He may have had a PPL in the dark past and just not kept his logbook current or done a BFR and CASA lost the record of his PPL. I know I had to show the Communications Authority an old weathered paper marine radio operators certificate for HF because they lost the records. My dad won a court case against the ATO because he kept records of his corro with them, & they didn’t have records. A person I know successfully defended a ‘flying without a licence’ charge (pre-AUF days) because the charge sheet was signed by the wrong person. Duck-ups occur frequently and they nearly always benefit the defendant (better for 10 guilty to go free than gaol 1 innocent principle). Two further points. A dead person (or their estate) can’t sue for negligence. A wife, or friend might be able to sue, but only if they personally suffered a loss, such as a mental condition (nervous shock); loss of financial support (for say a defendant spouse or child); and for men when their wife is killed, the loss of housekeeping & consortium (sexual services) previously performed by his wife (I think this has changed recently). The other point is that amendments to negligence laws around 10 years ago as part of reforms to make insurance more affordable (it didn’t work) substantially reduced ppl’s ability to sue negligent doctors and operators providing recreational or inherently risky activities. Flying in light planes is well established as an inherently risky activity and the law makes it very difficult to make a case even if there is no warning placard or signed waiver (except in the ACT).
-
On parts, there question is which parts. Lots of parts are common to both Gen3 & Gen4 but some major parts are not, like crankcase, cylinders, heads, pistons. Probably good if someone did a table, of what is, and isn’t. The other thing is, if Jab are not going to support providing parts, particularly consumables like distributor caps, bearings etc, then Jab should provide OEM specs and part numbers to assist ppl finding alternative sources.
-
This is what I use. I have them in two aircraft and over 200hrs with great results. Needs a 5V power supply. $30 https://www.ebay.com.au/itm/163191931141?mkcid=16&mkevt=1&mkrid=705-154756-20017-0&ssspo=xieIH1mFSHi&sssrc=2349624&ssuid=Shq9KlDPSE2&var=&widget_ver=artemis&media=MORE
-
I’d just like the Skyecho to output an RS232 wired connection so I can utilise the collision/proximity capability of my MGL EFIS.
-
KG thanks for the correction on Loctite 620. I’d add to Yenn’s comment that a top end o’ haul is not that difficult following the Jab material. If I was going to get someone else to do it I would make sure they give you completed engine build worksheets including the measurements and tolerances in the O’haul manual.
-
No I haven’t tried freeze and release. I just wrote ‘supaglue’ instead of cyanoacrylate. It’s whatever Jabiru use and the manual says its a Loctite product but it’s still cyanoacrylate, aka superglue. I tried heat as per the O’haul manual. BTW it was just 3 bolts and 2 dowels and all broken off before I got the engine. But even removing intact bolts it’s pretty much mandatory to use a new high quality hex driver with a long breaker bar, apply heat and ever so gradually increase the torque, and just at the point when you think the screw head will definitely shear off it moves...& then it’s easy. The dowels were relatively easy to remove as I was able to braze on a bolt to the 2-3mm extending out from the crankshaft and use that bolt to pull the dowel out. The flywheel bolts are now locked with Nordlick washers which I should should think will be easier to remove.
-
Nev, since I’ve made a jig to do the tunnel boring it’s not that bad. I’d do that many times in lieu of having to extract broken flywheel cap screws ... you have to drill them out with progressively larger tungsten bit drills and then chisel the remainder with 2mm wide hardened chisel being careful not to damage the crankshaft.
-
Splitting the case is probably 3-4 times the hours of work than a ‘top end’ overhaul. There’sa lot more measuring and you have to deal with the cam timing and distributor drives, the oil pump and flywheel. I’ve done two cases: both had fretted cases: one was removed from an aircraft because in retorquing the through bolts the crankshaft was pinched by the main bearings and seized. The other had no external signs of crankcase fretting and was due just for a 1000hr top-end overhaul, but when I did a torque test with new through bolts (mandatory replacement at 1000hrs) the crankshaft rotational friction exceeded the specs. Splitting the cases revealed light fretting as the cause but 3/5 main bearings were showing copper colour, ie. were worn excessively. It’s quite possible that at 1000 hours one might want to split the cases for a precautionary inspection.... but it’s a lot more work particularly if you have to machine the crankcase halves, but not that much more expensive in parts. Removing the flywheel is fraught if the cap screws are supaglued & more so if a cap screw (or dowel) is broken off before or during removal.... budget several days just for that. Dealing with fretted cases is not easy. Most engine shops can reface the halves but I couldn’t find any that could do the tunnel boring to the Jab specs. The main issue was the small size and tight tolerance of the camshaft tunnel. So I’m not really sure if splitting the cases at 1000hrs is worth it or not.... if you do, you will really get to know your motor. Mark
-
Nev, I’m being picky; water is still a ‘thing’.