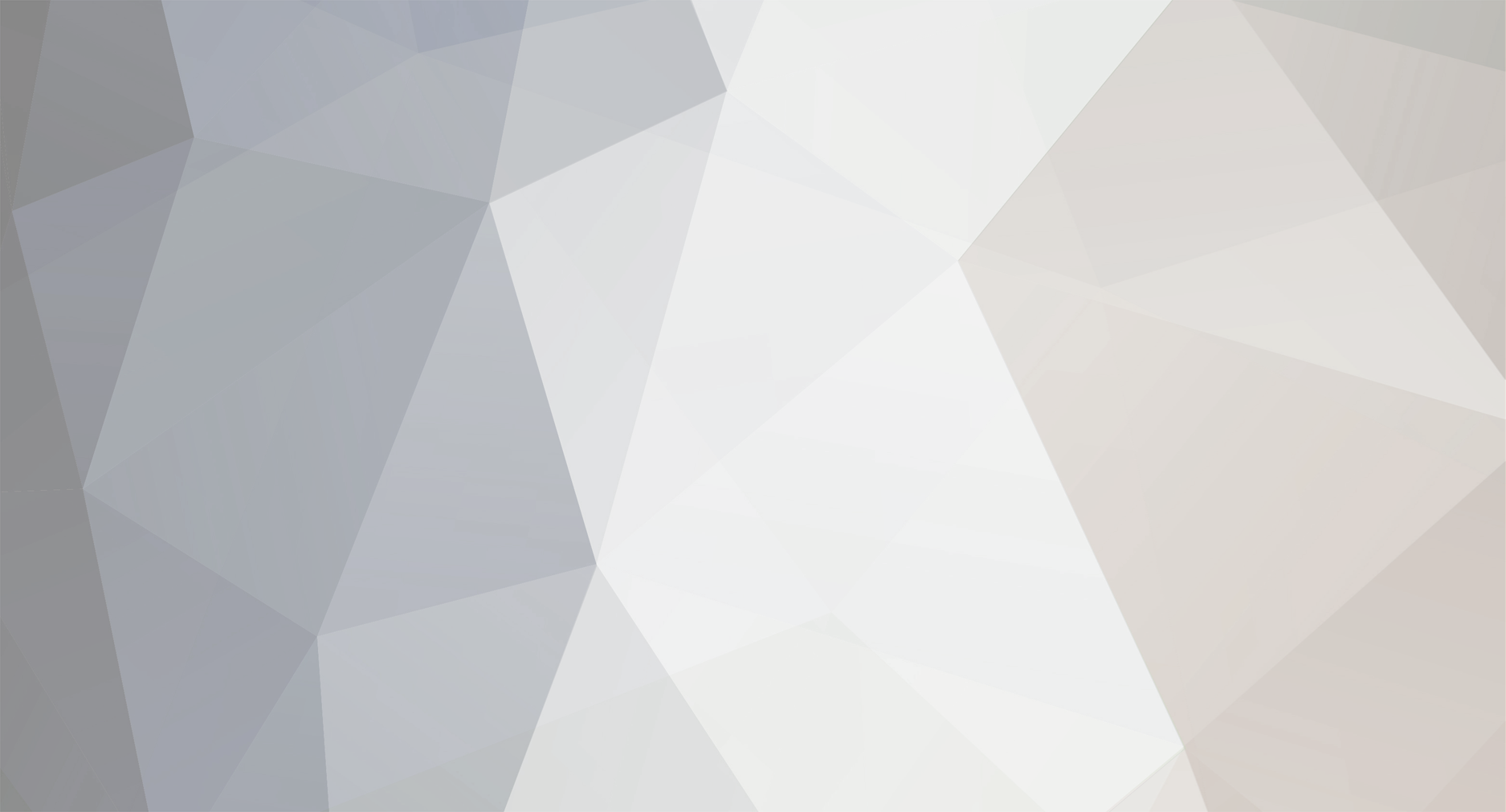
Bruce Robbins
Members-
Posts
153 -
Joined
-
Last visited
-
Days Won
1
Content Type
Profiles
Forums
Gallery
Downloads
Blogs
Events
Store
Aircraft
Resources
Tutorials
Articles
Classifieds
Movies
Books
Community Map
Quizzes
Videos Directory
Everything posted by Bruce Robbins
-
G'Day OME, The strut attachment points at the fuselage and undersurface of the wing consist of a fibreglass lug with an aluminium insert screwed and bonded into the fibreglass lug. It's not uncommon for the aluminium insert to work loose in the fibreglass lug, particularly after several thousand student landings! The fix is to remove the insert, clean everything up and then re-bond the insert into the lug. We have done a few already on airframes around the 1000 hour mark. I expect that is what Jabiru think also, hence their lack of urgency. I would however have a good look at the attachment point and ensure that is all it is. That wing strut is a rather important little gadget when it comes to preventing the wings clapping! Cheers, Bruce
-
Flat spin recovery in RA Aircraft
Bruce Robbins replied to Willborne's topic in AUS/NZ General Discussion
http://airsafety.info/wp-content/uploads/xas110522.pdf Bruce -
OK, thanks.
-
Thanks Brian, I have Dynon gear in three of the aircraft I'm operating, so already have the instrumentation. Was more interested in your thermocouples, particularly the EGT. Are they also from MGL? I presume the EGT clamps to the exhaust headers with a probe up against the tubing. If so, do you know what sort of accuracy you get, or is it just the comparison of temp spreads you're after? Thanks, Bruce
-
Hi Brian, What is the portable gear you've installed? Could be a very useful troubleshooting tool. Regards, Bruce
-
AirNav VFR - what happens when the charts expire?
Bruce Robbins replied to rdarby's topic in AUS/NZ General Discussion
G'Day Ryan, I use AirNav. In my version the software just refuses to load once the maps have expired. You cannot even look at old flight plans. Bruce -
Where in the Sydney area?
Bruce Robbins replied to wenimbig's topic in Student Pilot & Further Learning
Hi Skydancer, I am currently operating at Wollongong as a satellite to Dave's Flying School at The Oaks. You can call me direct on 0412 209 953. Regards, Bruce -
Where in the Sydney area?
Bruce Robbins replied to wenimbig's topic in Student Pilot & Further Learning
Shawn, I operate RAA flight training from Wollongong airport 6 days a week. Jabiru J160, J170, J230 (x2) and a Piper Sport. You can pm me for details. Regards, Bruce -
Jetjr, I too bought one of those pumps and have to agree. It is pretty well useless for aircraft tyres. Bought a $10 pump from local SuperCheap type auto store that works like a charm and is not too heavy. Is a little bulky though. It is the old fashioned 2 foot long metal tube with fold out lugs at the bottom to stand on and a T handle at the top to pump with. Have used it several times when fixing a flat tyre and it works like a charm. Pops tyre bead back onto the rim and inflates tyre to 45psi in only a minute or two. A good quality auto foot pump is also good, although usually a bit heavier. Avoid the cheap $10 ones, they only seem to last a few uses before falling to bits. (Sorry Ian, never got around to letting you know about your pump.) Cheers, Bruce
-
G'Day Bruce, The blue fiish on the discs is a preserving film. You should clean it off with solvent before using the disks. Try taking the disk back off and cleaning them up with an orbital sander. New pads and disks work well, but not with the film.
-
G'Day Ian, Looks like we agree on the end result (loss of tension in the bolts) but not the cause. .....looks like a fatigue break. The likely cause is loss of tension in the bolts, leading to movement, fatigue, and then breakage. Yep. Movement. Not enough clamp. But the studs were prone to strip if reefed up. (..and I still believe the problem is with sub standard nuts, not the bolts themselves. Have a good look at some fairly recent used base nuts, and see how little of the thread area is actually load bearing) If one stud breaks from fatigue, the others are all moving down the same road. Arguably if one breaks, the right thing is to replace all of them. (agree, or at least all the bolts and studs on the affected cylinders) Fretting and oil leaks from the cylinder bases, and what looked like the start of fretting between the crankcase halves. Not enough clamp. Movement. Fatigue ...... (due to a base nut that had loosened slightly after less than 80 hours on a rebuilt engine, leading to loss of tension and clamping. We replaced the nuts only. Problems dissapeared and the engine is still running strongly). the newly designed ones on our latest spec six cylinder motor Nuts are not "specially designed". They are an off the shelf item from ARP. (Our latest motor is a brand new unit. The nuts are a different design, NOT the 12 point ARP nuts as per the SB which we have fitted to all oour 2200 motors. They are a hexagon nut with a deep flange under the hex. Look like they could be CNC made by Jabiru themselves, though that is just my speculation, considering the cost of the ARP nuts) Bruce
-
Strange response to carby heat
Bruce Robbins replied to sfGnome's topic in AUS/NZ General Discussion
Hi Gnome, A side effect of carby heat is to richen the mixture. Sounds like that is what was happening. Your engine is on the lean side, especially at 7,500 and carby heat was richening the mixture enough to return it to smooth running. Bruce -
fly_tornado, The SB does not say the block is twisting, but may sometimes be fretting along the joint between the crankcase halves. I am relatively new to Jab engines, but have flown behind them now for five years. Initially an hour or two a week, then weekend instructing and finally full time instructing. For the first four years I saw no issues with through bolts in five heavily used aircraft. In the last twelve months however I have had three different engines in three different aircraft break a through bolt or stud. Engine times since new or since overhaul ranging from 850 down to just 200. Two were four cylinder, one was a six cylinder. I have shown or discussed the broken bolts with a number of mechanical engineers and L2's. All said the same thing - " .....looks like a fatigue break. The likely cause is loss of tension in the bolts, leading to movement, fatigue, and then breakage." I had another engine reconditioned by the factory that was showing signs of possible impending failure after just 80 hours in service. Fretting and oil leaks from the cylinder bases, and what looked like the start of fretting between the crankcase halves. Investigation discovered a loose base nut. We replaced the nuts with the new 12 point nuts and all the signs dissapeared. The engine even seemed to run smoother. That engine did another 150 hours before moving on to another school with no further problems. There are many things that can cause a loss of tension in the bolt, but I am convinced in my mind (although I have no actual stats or evidence) that the reason for losing tension was cylinder base nuts that were not up to spec with regards to material, dimensions or thread pitch angle. The nuts mentioned in the SB, and the newly designed ones on our latest spec six cylinder motor seem to have solved the problem, provided they are installed and tensioned correctly. After starting to lose confidence in the Jabiru engines, I am comfortable to once again fly behind them and hire them out to customers. I believe the problem was in the base nuts, and appears to have been addressed. Regards, Bruce
-
Remember that most of what these guys are talking about refers to fuel injected engines with manual mixture control. Carburettors often don't give the even mixtures and granular control needed to safely run lean of peak, as Jabiru found to their detriment.
-
Cessnock Crash this morning - R 44 - Fatal
Bruce Robbins replied to pilotdave69's topic in AUS/NZ General Discussion
The passenger was identified in our local paper as Sam Bateo from Mudgee. Hope that's not the same Sam Bateo from Mudgee that has been on this forum from the beginning. Bruce -
Bit of a bugger to top up the oil!
-
Hi BlackRod, Aircraft strength and various "V" speeds is a complex subject, and has come up here quite a few times. I suggest you make a nice big coffee and sit down in a quiet corner for a while and plough through John Brandon's excellent tutorials on the subject. eg:Airspeed (xhtml w3c 12/09) . A basic rule of thumb for the types of aircraft we fly, (and I'll get pedants jumping all over me for this) is that VNE is usually limited by flutter or component strength, and is one of the few speeds quoted in TAS. Turbulence Penetration Speed (which strictly speaking is a different speed to Va, whic is defined as "design manoeuvring speed") is related to the stall speed. Being very simplistic, the idea is that the wing stalls before it can generate enough force to break the aeroplane. So if you have a high stall speed, you can hit a vertical gust at a higher speed, because the wing stalls earlier. So the lower the designer makes the stall speed, the lower the Turb Penetration Speed becomes. Some larger GA aircraft (eg: Cessna 182) will quote two different Turbulence Penetration Speeds. The one for MTOW is higher than the one for Minimum weight. Aircraft structure and aerodynamic loading is a complex subject, with a lot of the lessons we've learned since Wilbur and Orville being written in blood, but fortunately for us nowadays, follow the advice and limitations quoted in the POH and all should be OK. Regards, Bruce ps: Just for interest: Flutter - I've seen carbon fibre model aircraft built to be able to withstand over 20G, explode in midair due to flutter. G Loading and Turbulence speeds - When Grumman were designing the Bearcat ni the mid 40's, they initially designed the outer section of the wings to break off when the pilot exceeded about 7G. The idea was that the shortened wing would then stop creating as much lift (ie: force) and save the entire wing from being torn off. A similar concept to turbulence penetration speeds and how the stall saves the wing before it breaks the aircraft. The idea worked perfectly, but was eventually dropped due to operational difficulties. "As a weight-saving concept the designers came up with detachable wingtips; if the g-force exceeded 7.5 g then the tips would be allowed to snap off, leaving a perfectly flyable aircraft still capable of carrier landing. While this worked very well under carefully controlled conditions in flight and on the ground, in the field, where aircraft were repetitively stressed by landing on carriers and since the wings were slightly less carefully made in the factories, there was a possibility that only one wingtip would break away with the possibility of the aircraft crashing.[6] This was replaced with an explosives system to blow the wings off together, which also worked well, however this ended when a ground technician died due to accidental triggering. In the end the wings were reinforced and the aircraft limited to 7.5 g.[7]"
-
I believe most altimeters only go up to 1050 mb. A quick internet search turned this up, from the FAA. Didn't check whether it is still current. Sec. 91.144 Temporary Restriction on Flight Operations During Abnormally High Barometric Pressure Conditions. (a) Special flight restrictions. When any information indicates that barometric pressure on the route of flight currently exceeds or will exceed 31 inches of mercury, no person may operate an aircraft or initiate a flight contrary to the requirements established by the Administrator and published in a Notice to Airmen issued under this section. (b) Waivers. The Administrator is authorized to waive any restriction issued under paragraph (a) of this section to permit emergency supply, transport, or medical services to be delivered to isolated communities, where the operation can be conducted with an acceptable level of safety. Federal Register Notes 59 FR 17450, No. 70, Apr. 12, 1994 SUMMARY: This final rule amends part 91 of the Federal Aviation Regulations (FAR) to provide for the issuance of temporary flight restrictions on certain operations when accurate altitude information is not available. The rule is warranted because barometric pressure higher than 31.00 inches of mercury (inHg) (1049.8 millibars) exceeds the capability of standard aircraft pressure altimeters and prevents the display of accurate altitude information. The rule provides restrictions on certain flight operations during periods of abnormal atmospheric pressure conditions and is necessary to promote flight safety during certain operations for which accurate altitude information is critical. EFFECTIVE DATE: May 12, 1994.
-
Bruce I'm not sure that I agree with "usually indicated as TAS". It is certainly true where flutter is the limiting factor, which I understand is a characteristic of many composite designs, but so far the aircraft I have flown (more traditional types), express it as IAS or don't clearly define it as either. Hi Spin, VNE is a complex limitation that I shouldn't have tried to summarise in one short sentence. The point I was trying to make was that of all the speed limitations that we fly within, VNE is the one that is more likely to be a function of TAS rather than indicated. However, most light aircraft GA or RA, tin or plastic, only have a IAS indicator, so it makes sense that the redline or VNE should be marked on this. That doesn't mean that we can happily approach redline on the IAS indicator with impunity. Fortunately below 10,000 feet it's not so much of an issue, but after much reading on this subject I've decided that I will always view VNE as TAS. Stick IAS TAS and VNE into a search engine and have fun wading through the results. :)
-
VNE is one of the few speeds that is usually quoted in TAS. Check your individual POH. The Pipistrel Virus actually has a table on the dash showing different VNE speeds (Indicated)for different heights. The higher you go, the lower the indicated VNE gets. The main reason is that VNE is usually set by flutter constraints, and flutter does not care about IAS, just the speed of the air past the surface.
-
Jack, From the internet. I have no personal experience with K Liners. VALVE GUIDE LINERS Boring out the original guides and installing thin wall bronze liners to restore proper clearances is not only a fast and economical guide repair option, it also provides the benefits of a phosphor/bronze guide surface (better lubricity, scuff resistance and wear characteristics than cast iron). Though liners are most often used to repair integral guides in cast iron heads, they are also a very effective way to repair replaceable guides in cast iron or aluminum heads, which saves time and eliminates the risks associated with driving out the old guides and pressing in new ones. Liners also save the cost of having to replace the valves. If the original valves are not worn, standard sized liners can be used to restore the inside diameter dimensions of the guides. If the valves are worn, the stems can be turned down .0050 in. to accommodate liners with slightly undersized inside diameters. Jerry Qualiana, vice president of aftermarket sales at K-Line Industries, Holland, MI, says their K-Line Bronze Bullet Guide Liner system has been authorized by Ford Motor Company and meets Ford Q-1 quality standards. According to Qualiana, the Bronze Bullet Guide Liner design is an enhanced design over previous bronze liners, incorporating an "Interrupted Spiral" which assists in retaining oil in the guide, while eliminating oil flow through the guide. In conjunction with the previously mentioned lubricity characteristics of phosphor bronze, Bronze Bullet Guide Liners offer improved guide life in today's oil starved valve guide environment. Also, Qualiana points out that because of the lubricity in the phosphor bronze, K-Line has always advocated valve to stem clearance at the low side of the manufacturer recommended specifications. Mike McElmurry, vice president of production at Sequal Corp.,Willow Springs, MO, says regarding K-Line's Bronze Bullet Guide Liner, "Because the final size is so easy to control, we have been able to tighten all of our valve to guide tolerances by at least .001 inch. This, along with the liner's ability to resist galling has reduced our warranty claims by as much as 75% "I have looked at other methods of valve guide repair, .015 inch overised valves, new and rechromed, .003 in undersize valves with replacement cast iron guides, but have found nothing that was cheaper to use than K-Line with .003 in. undersize valves. We grind our own valves and enjoy over $0.80 per guide savings over any of the combinations listed above." The key to using the Bronze Bullet Guide Liners successfully is proper installation. Qualiana says if the original guides are not worn more than .030 in. or cracked, they can be lined. Otherwise, replacement would be recommended. Installation of the Bronze Bullet Guide Liners is a five step process: 1. First, the old guides have to be bored out to accept the liners. Qualiana recommends using a KL1725CB Black Beauty carbide reamer in an air drill with a no load speed of 2100 to 3000 rpm. K-Line's KL9900 Boring Fixture has centering pilots that center the reamer off the valve seat (which maintains seat concentricity), and an air clamping fixture that holds the head securely in place while the guides are being bored. The guides should be bored dry with no lubricant, using steady consistent pressure. Once the guides have been bored out, they should be blown out and checked with a go-no go gauge to make sure they are the proper size. 2. The liners should then be pressed in from the top side of the head using an air hammer and K-Line's Auto Installer tool. The liners go in with the tapered side facing the guide hole. The liners are then driven in flush with the top of the guide boss. 3. Next, the liners are sized. Any of three different techniques may be used: roller burnishing (use with lubrication), broaching (driving a calibrated ball through the liner with an air hammer), or using K-Line's ball broach tool in an air hammer. Sizing the liners is a critical step because it accomplishes two things: it provides the proper clearances between valve stem and liner for proper lubrication and oil control, and it locks the liner in place so it will transfer heat efficiently to the surrounding metal for proper valve cooling. Bronze actually conducts heat more efficiently than cast iron, but requires a tight fit and metal-to-metal contact with the surrounding guide for good heat transfer. If the liner isnot sized properly, it may cause the valve to run hot, or worse yet, come loose. 4. After the liners have been sized, turn the head over an trim the liner to length. The liner should be cut flush with the guide boss in the port. This step is not necessary if precut liners are being used that have the correct length for the application. 5. The final step is to Flex Hone the liner after any seat work that is necessary has been completed. The Flex honing step removes any burrs left from trimming the liner to length, and leaves a nice crosshatch finish that improves oil retention. One pass in and out is all that is recommended to hone the liner. A flexible nylon brush should then be passed through the liner to clean the hole. Though the just described procedure sounds more complicated than it really is, a typical four cylinder or V8 can be relined in six to seven minutes says Qualiana. Also, the majority of the detailed steps listed regarding cleanliness and accuracy in the guide area are requirements no matter which method of guide repair the rebuilder chooses.
-
Jetr and David, I used to believe the same as you. "If I operate an RAA registered aircraft on my PPL I can go above 5000 feet." Unfortunately the regulations disagree. CAO 95.55 paragraph 5.1 (a) states that "the aeroplane may be flown 5 000 feet above mean sea level or higher: (i) only if it is flying over an area of land, or water, the condition, and location, of which is such that, during the flight, the aeroplane would be unable to land with a reasonable expectation of avoiding injury to persons on board the aeroplane; and (ii) only if it is equipped with a radiocommunication system"
-
"I have often flown above 5000' & to date have never been challenged by either Centre". "You wont get challenged as it is YOU who are restricted not the Aircraft and centre have no way of knowing if you are PPL or RA." Not right. According to the regs, the aircraft is restricted, not the pilot. Bruce
-
Hi W68, The 100 knots is TAS, not indicated.