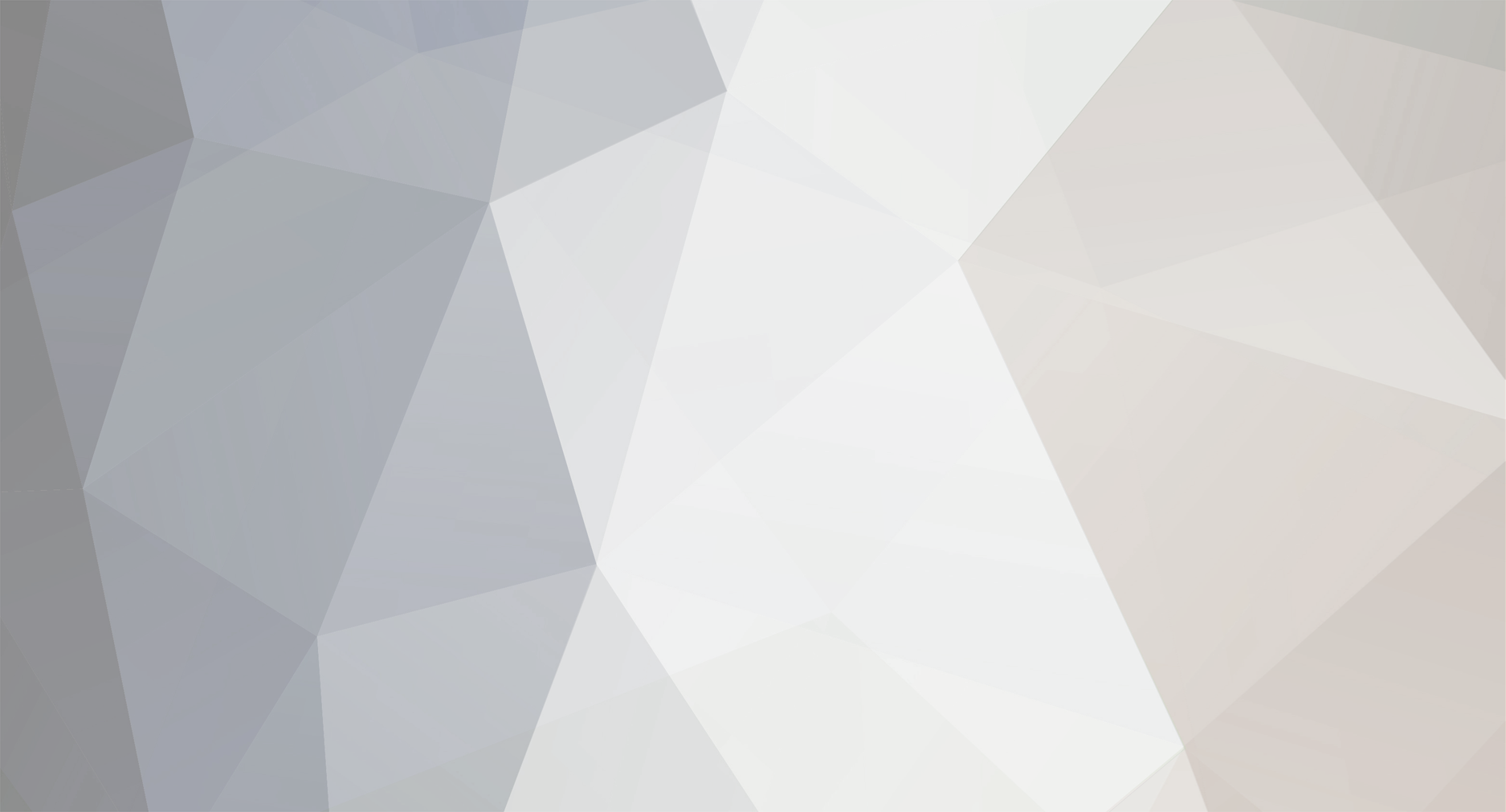
skippydiesel
Members-
Posts
6,891 -
Joined
-
Last visited
-
Days Won
69
Content Type
Profiles
Forums
Gallery
Downloads
Blogs
Events
Store
Aircraft
Resources
Tutorials
Articles
Classifieds
Movies
Books
Community Map
Quizzes
Videos Directory
Everything posted by skippydiesel
-
ATSB prelim report vid on The Oaks mid-air.
skippydiesel replied to Garfly's topic in Aircraft Incidents and Accidents
The Jab was returning from an aborted X country. The C180 from Camden circuits. Dont know about you, my transponder & SE2, go on just prior to TO and are not shut down until after Landing (usually on taxiing in). C180 (GA registered) would have had his transponder on, to do circuits at Camden. Not that I get to fly with other pilots these days, however no recollection of transponders (once on) being shut down in circuit. -
ATSB prelim report vid on The Oaks mid-air.
skippydiesel replied to Garfly's topic in Aircraft Incidents and Accidents
You guys did not read the JAB HAD AN SE2 and the C189 HAD A TRANSPONDER - do I have to explain further????😈 -
ATSB prelim report vid on The Oaks mid-air.
skippydiesel replied to Garfly's topic in Aircraft Incidents and Accidents
Your point? -
Insurance for RA-AUS aircraft
skippydiesel replied to danny_galaga's topic in AUS/NZ General Discussion
As an RAA member/aircraft owner, I have the RAA insurance (public liability) as part of my annual membership fee. On top of RAA, I have hull, through Geof Tonkins (GT) (broker). My last premium was so high, I very nearly scraped the whole lot. In addition to my usual premium, was an offer of increased public liability - I declined. We live in this crazy environment where we are scared into paying for ever more insurance, just in case.....!!! Unless you are incredibly wealthy, I don't think it is actually possible to afford a, so called, "comprehensive" insurance policy. I don't know how often RAA level aircraft/pilots have a successful claim against them, I suspect not often. My aircraft carries a placard "Yout fly in this aircraft at your own risk............" My preflight checklist requires I draw their attention to the placard ; Passenger Briefing This is a Recreational aircraft; Its construction & maintenance standards are not as for Certified aircraft and may be below certified standards. You- Fly in this aircraft at your own risk May not smoke in or near any aircraft Must wear your safety harness, securely fastened at all times Must obey the pilot’s safety instructions Must not touch any controls Should you feel uncomfortable/unwell please let me know ASAP, so that I may do what I can to improve your situation. In the event of a forced landing; Unlock your harness thus - Operate the cockpit locks thus - Exit the aircraft as soon as the engine is turned off consistent with your safety Activate the PLB (location) A basic first aid kit is on board (location) Mission details – duration, speed, altitude etc. I understand that, in the event of a claim against me/my estate, should I be found negligent, the above will provide little protection. Not counting the RAA premium, over three years (since aircraft first registered) I have spent about 10% of the aircrafts new value, in insurance premiums. I am not sure that I will insure my aircraft next year - the premium is more than I would spend in operating & maintenance combined, for probably 2 or more years ( I try not to think about it). -
Sooo! How good are these "press the switch" jobs??? Crazy I know, I have 5 ride-ons & two push mowers, ranging in size from 3hp-25 hp, up to a commercial level zero turn 60" deck. I have never purchased a mower - all are hopeless cases, that somehow come back to life (usually a carb clean does the trick) owners already moved on/purchased a new one. I don't have a trailer big enough for the 60", so used mainly for maintaining our 3km street roadside verges. For helping out at the airstrip, have nice Husqvarna 21 hp (made in China). Lots of power, has cruise control, poor lawn finish but good enough around aircarft. Couple of Toro's that the wife likes to use around the house/yard. Do a good job. One realy old metal bonnet Toro, waiting for a donor hydro transmission to appear - when working cut a beaut lawn. Can't get rid of it, engine still good, unlike the modern versions "built like the proverbial brick S...H...." Anyone got a hydro transmission in good order (almost any lawn tractor style, up to about 17 hp, can probably be mad to fit)?? Two pushers are for finishing off, where the ride-ons can't access. All run on 91 RON (would love a diesel), Annual oil changes/service. Do not cut wet grass, be generous with grease (especially spindle heads). Never wash down with water - use compressed air, to remove ALL chaff & dust, after every work period. Will your battery job measure up????😈
-
What specific info does Ra Aus need for propellers?
skippydiesel replied to danny_galaga's topic in Engines and Props
Just relating my experince, which seems a little different to yours. All the best😈 -
What specific info does Ra Aus need for propellers?
skippydiesel replied to danny_galaga's topic in Engines and Props
The Max TO weight increase, was just a month or so ago. I can't comment on why RAA would impose changes to existing TO wt. As for Certified W&B. It would seem that RAA had its authority, to approve W&B, removed for some reason. This meant that anyone requiring a W&B, had to go the CASA/Certified rout, including me. I shopped around and found a Certified service provider, at a considerably better price (almost 1/2) than what you have quoted. -
ATSB prelim report vid on The Oaks mid-air.
skippydiesel replied to Garfly's topic in Aircraft Incidents and Accidents
We will never know why the C182, with two experienced pilots on board, was; Not calling on or apparently monitoring, The Oaks CTAF. At circuit height. If joining, was doing so on 36, opposite to established traffic on 18 (including the Jab he collided with). His transceiver had been working, minutes earlier, on the Camden frequency - failed to switch over? selected wrong frequency? failure? (unlikly). It was a Saturday morning in reasonable weather (moderate turbulence at altitude), normally busy with small aircraft movements, why did the C180 pilots not think it was strange that they had no comms with The Oaks (which shars 126.7 with nearby Mittagong). The Jab had a SkyEcho2, presumably the C180 had a operational transponder (would have been required to enter Camden airspace) how did ATC not see the two aircraft on a collision course? How did the Jab pilot not "see" the C180 with his SE2 on iPad? How did none of the 3 pilots see the other aircraft? So many questions, that will never be answered - very sad for all. -
What specific info does Ra Aus need for propellers?
skippydiesel replied to danny_galaga's topic in Engines and Props
May be. When I registered my 19, late 2022, Aircraft varies significantly from factory plans. I supplied everything asked for, which included prop make/model, instrument calibration/certification, independent inspection/comments, W&B, test performance data and Max TO weight, etc, etc. I used the factory recommended Max TO Wt. Found out later, as builder, I could have nominated whatever Wt I chose. Contacted factory requesting approval for one off higher TO Wt, with reasoning- flat refusal. Months later factory upped Max TO Wt (to meet new US guidelines for class of aircraft) with no structural changes. Applied to RAA for Wt increase - told my prerogative as builder - send in photo of revised panel placard - done & approved. So much for all that BS about home builder having to stick rigidly to factory plans/specs. 😈 -
Red - EBay temps quoted, are in Cruise eg OAT 20C/ EBay 35C. After flight, taxi, shutdown, can get to 65C Onetrack -Temperatures verified by using three additional, temporary, IN/OUT digital thermometers. Thanks for the "Cooling Tips" unfortunately is mostly about engine oil/coolant/CHT cooling. All of mine are well within Rotax specifications however EBay temps are, in my view, far too high. Read my opening statement. Thruster - Cowl flap, inoperative at the moment - waiting for replacement linear actuator. Not just my "...quest for performance and efficiency..." also trying to minimise potential heat damage to components (mainly electrical) and fuel vaporisation (vapour lock) Spacesailor - "Very few ( if any ) air-outlet's are at the top of the ebay ," Tried this (read opening statement). Could be, like my experince, ineffective. Which could be something to do with external air pressure/flow, internal airflow/direction/pressure or combination thereof???? Will certainly help with, after flight, ground temps. Thanks Gents. Keep the suggestions 😈
-
Turbo, Try not to; Make accusations directly or by inference, that you can not defend. Suggest I have done anything other than give factual information, as I understand it. Repeat "ad nauseam" indefensible actions, where the owner/operator fails to look after his/her equipment, as they should and then blame the fuel. Repeat urban myths as fact. If Rotax accepts E10 can safely be used in their engines, the likelihood of your "white powder" deposits being a the result of E10 use without any other contributing factors is diminishingly small. Fail to make a rational argument. That an owner use a fuel, that is not compatible with their engine or its ancillary systems, is the fault of the owner, not the fuel. Example for you: Owner puts diesel in a petrol tank - engine damaged. Owner can (irrationally) blame fuel all he/she likes , the fault is all theirs. I clearly disagree with your advice "........have told people the specific fuels to avoid ...." You seem unable to separate the fuel supply/storage (tank) delivery (hosses) metering system (usually a carburettor on small engines) from the engine itself - do I need to spoon feed you? While its is possible to damage the engine when one of the above fails, this is unlikly. If one or more of the the above, incompatible to E component fails, it can be replaced by a compatible component and the engine will run. If its so old that parts can't be found, why was it being run on E10???? Let any fuel go stale, in a carburettor, will likly result in a dysfunctional metering system (engine will not start/runs rough/stalls/etc) - preventive solution DRAIN FUEL (my preference) or use a fuel stabiliser (no experience). Corrective solution - CLEAN CARBURETTOR If you are in doubt about the compatibility of your engine system to E - DON'T USE E 10 (as I don't) A very old saying ; The Bad Workman Blames His Tools Once again, just for you - E10 is a perfectly usable fuel subject to the fuel delivery/metering system being compatible with ethanol. If as, you boringly repeat, your carburettor/other fuel system gets clogged with some form of deposit, your hoses/tank have disolved/rotted away, your O rings swollen/disintegrated, seals started to leak, you have; Failed to heed my warnings about E compatibility Failed to drain the fuel system completely before long term storage Failed to use a fuel stabiliser/storage enhancer That E10 may not "store" as well/long (stay "fresh") as, say 91 RON, is a management issue. If you do not address the management of the fuel (as with any fuel) you may have problems "down the track" - this is not the fault of the fuel, it's a human problem. Put another way, ALL fuels have long term storage problems, particularly when open to atmosphere. The failure of the maintainer to recognise this and take steps to avoid/mitigate, is a human, not a fuel, problem. That I recognise that most of my small engines, were produced before E10 became available, therefore may not be compatible with E and I not wishing to take the risk, use only 91 RON, illustrates the sort of management decision an owner should/could make.😈
-
Hmmm! In reverse order; "Also: where specifically are you measuring the temperatures? Air temperatures tend to be very location specific, by which I mean there will be quite different temperatures in various places under the cowl." EBay temp is measured top left of firewall, not far from the left carb conical filete. I did place additional temporary temp sensors on cone filters - gave temps within 2C of fixed unit. In recognition of the potential for some sort of hot air pooling: I install, one each side, 50mm ID ducts, from front of cowl (cool ram air) too close to cone filters - small reduction in air temp. Then one each side 70 mm ID ducts running from close to cone filters, to exit air just below firewall, hoping for air to be drawn away from top rear of EBay - small reduction in air temp Fan? - Did try a fan back when I had oil/coolant cooling issues, now solved by relocation of radiator & oil cooler (fan on shelf). I guess I could try putting it over the carbs to pull more (cooling) air over them - will check into the feasibility. My preference is always for a KISS solution where possible - not discounting it but to me a fan = complexity/weight😈
-
Full disclosure - I have never use or intend to use, any fuel that I know contains E. Having said that I still do not believe E damages the engine - yes! there can be issues with related components but these are parts of the fuel delivery and or metering system - not the engine. And yes! if you don't properly look after your small engines E fuel, there can be issues that you may not experince to the same extent with "straight" petrol. Again this is not the fault of the fuel - its the operator! I think we should make a distinction between operator error (ie failure to look after an engine/fuel supply correctly) a fuel supply system that may not be compatible with E and an actual problem with the fuel itself. With fuel compatible O rings/gaskets/fuel hoses/tanks/sealants/etc there is no reason why E 10, can not be used in any petrol engine. I chose not to use E10 because most of my small engines were built before E 10 was thought of. Without actually being sure, I assume their fuel delivery/metering systems are not compatible with E. I don't want the hassle/expense of sourcing and installing compatible components, for nil performance or service life advantage.😈
-
A brain teaser for the Forum Brain Trust. After a lot of work, my engine oil/coolant temperature are all within Rotax (912ULS) recommended specifications ✔️ Unfortunatly my engine bay (EBay)/under cowl temperatures are high. Were about 25 C above ambient, have got it down to about 15 C above. Can't figure out how to get more cooling air into the EBay or hot air out. I understand Rotax recomend no more than 7 C above ambient(?) Why does this matter? High air/carb inlet temps reduce engine efficiency. May cause fuel vaporisation (vapour lock) and damage electrical systems. I have seen 65C on engine shutdown. For best engine efficiency, I was using a home built airbox, to deliver nice cool air to my carburettors. Unfortunately the airbox, hanging of the carburettor ,was negating the vibration damping of the rubber manifolds and causing fuel to be ejected from the carb float chambers. I have replaced the air box with Roatx standard conical filters (sucking hot air). Fixes (?) I have tried; Flown with cowl top inspection hatch removed - nill effect in flight, may have improved ventilation on the ground. Increased air outlet significantly - some benefit to temp reduction but likly have increased drag (a little). Ducted air from front of cowl to vicinity of carbs - some benefit. Ducted air from vicinity of carbs to exit air - some benefit. Refitting air box - very likely, will have to find some way of supporting it, independent of carbs, so as to prevent previous problem. Refitting the air box will improve engine performance but will do nothing for the Ebay temp and its potentially negative effects. I have toyed with the idea of additional exit air holes (proven a top vent will have little/no effect) wondering if side (lower cowl) vents might work. Your constructive thoughts will be most appreciated.😈
-
Thanks Aro - My focus was the diffrent nomenclature for essentially the same product - seems to confuse quite a few people. I probably should avoided straying into the technicalities of Octane (Cetaine for diesel not mentioned). I am surprised that no one took me up on "The use of E fuel is considered to be a less environmentally polluting (something I find difficult to believe)."
-
I stand to be corrected: Even pure Ethanol has no impact on the engine. Some S American countries have been using for years. Yes, in it pure form, it requires some modification to burn efficiently. In a petrol blend(E10) most petrol engines can use it. As far as I understand, the problem is the compatibility of downstream components such as "O" rings, some plastics & sealants being degraded by E.
-
Fuel names seem to confuse a lot of people. My understanding of the various fuel names & some associated comments: Petrol "Petroleum is a liquid mixture of hydrocarbons present in the rock strata of earth. It is extracted and refined to produce fuels including petrol, paraffin, and diesel oil. Petrol is one of the distillates of petroleum including Diesel and Kerosene" AvGas. The name is pretty well universal for aviation petrol, used in Spark Ignition Internal Combustion (SIIC) engines, currently containing a percentage of Tetraethyl Lead (lead). Around 100 RON.(Research Octane Number). To the best of my understanding, this is the only fuel, available in Australia, that contain lead. Can be used in almost all SIIC engines. If used over a prolonged period, some engines may not tolerate the lead component. MoGas=AutoGas=Gas=ULP=Petrol These are all, diffrent country, names for essentially the same product, automotive petrol Australia tends towards ULP (Unleaded Petrol) or Petrol, with USA etc, favouring Gas (Gasoline) / MoGas (Motor Gas) etc. This is an automotive fuel, for SIIC engines. In Australia comes in RON 91-95-98, E 10 (ULP petrol containing 10% ethanol) and E85 (which I have never seen). Rotax specifies a minimum RON of 95, recommends 98 and is compatible with E10 . So nothing wrong with using E10 in your Rotax (subject to the rest of the fuel system being ethanol compatible). 98 RON is used in a lot of small aircraft (some may require a Supplemental Type Certificate to legally use it). Anecdotally results in cleaner oil, lower deposits. Some engines may experince accelerated wear of valve stems/seats etc. Most pilots will notice little if any performance difference between AvGas & 98 RON. Ethanol (E) can be produced from fermenting almost any plant containing sugars, most often Maize (sometimes called Corn). Compared with petrol has lower energy. E fuel and E+Petrol blend will deliver less energy/litre than straight petrol. This means less power & more fuel consumed /km/hr. I am told that using an E blend fuel will deliver lower combustion temperatures. Ethanol can react with certain parts of the fuel system - mainly non compatible rubber/sealants/some plastics - IT DOES NOT DAMAGE THE ENGINE! The use of E fuel is considered to be a less environmentally polluting (something I find difficult to believe). Jet Fuel = Jet A= Jet A-1 = Jet B = Aviation Turbine Fuel (ATF)= Aviation Kerosene All names for, essentially the same, fuel used in aircraft turbine engines and in aircraft diesel engines. It's a high grade/standardised diesel fuel. Jet A has a higher "flash point" (less likly to burn/explode) than petrol, making it a safer aviation fuel. Could be used in a ground based diesel engine. Diesel=Distillate=Derv Used in automotive Compression Ignition Engines (CIE/Diesel). Diesel could be used in an aviation engine however its to lower level quality control makes its performance/reliability less predictable. Diesel engines tend to produce more power/torque /litre fuel, than petrol equivalents & are therefore more economical to run. Diesel engines usually have a higher weight to power ratio, than petrol equivalents. This makes their application/use in aviation uncommon. There are a number of other fuels available in Australia that tend towards particular applications eg marine/taxi / trains/ etc
-
My thanks Pmccarthy. I will survive . The Forum is a truly wonderful resource, that I feel privileged to part of. I am on several forums, non as congenial and informative as this one.😈
-
Anyone notice the comments from Maxine Milera, From The CEO, regarding "lifetime membership cards" Except for the very rare member contributor delivering truly outstanding service I have always been sceptical about this practise. It usually start with good intentions, down the track deteriorates into a "perk for Committee members and the like.
-
Where in your Cessna /Piper/Homebuilt?etc would this "text" appear?😈
-
You sure of that? It's one thing to wish for a magazine that actually represents the organisation/its membership, seeks to inform and strive for unbiased reporting and quite another to end up with something akin to a glossy "trash mag". Sport Pilot is not fee. We pay for it. That it does not provide the expected service, is akin to fraud. 😈
-
You are a troll ! The Stewart System does not override the ATEC system - I used a combination, as any sensible person would, IN CONSULTATION WITH BOTH ATEC & STEWART, using each as and where appropriate, to achieve an excellent outcome. That's it I'm done with your ill-informed, selective out of context quoting, unfounded accusations, negative & destructive commentary. 😈
-
"The Stewart System does require rib stitching" It is some years since I used this system (adhesive/fabric/paints) however I do not recall any requirement for stiching and I did not do so. It is likly that Stewart say to stitch were stitching required and not where not. The Zephyr has relativly wide caps, on each rib and trailing edges to facilitate gluing - this may not be the case for a stitched system. In effect this makes every rib to rib, an almost self contained fabric over wood cell. "The fabric-fabric join is the strong joint, and they have specifications for the overlap required at the leading edge etc" Only the fabric covered control surfaces (later models had some/all? composite) were wrapped ie had an overlap, however the wings & horizontal stabiliser were not. "The theory is that the fabric envelopes the whole wing, and the load is carried by the fabric joints. " May be so for some aircraft, however the Zephyr had about half of the wing chord covered in plywood (later models may have had carbon fiber) and a large portion of the inner wing also fully covered in ply. This left an upper/lower wing "patch" in fiber. The Zephyr was/is not the only aircraft to use this (no stitch) system - I recall seeing an aircraft at a NSW air show with the same concept (unfortunately forget the name) "That's not to say you couldn't find an adhesive that gave you a good fabric to structure join. But I don't think the usual adhesives in these systems qualify, and it wouldn't be a standard practice." I used the Stewart System (certified) which include their adhesives - what is this ".... standard practice"?? .😈
-
"...............under most aerodynamic (lifting) stress is the trailing edge" This is about the potential for fabric separation from the underlying frame - not about wing lift. I will apologise only IF a genuinely knowledgeable person correct me on this.