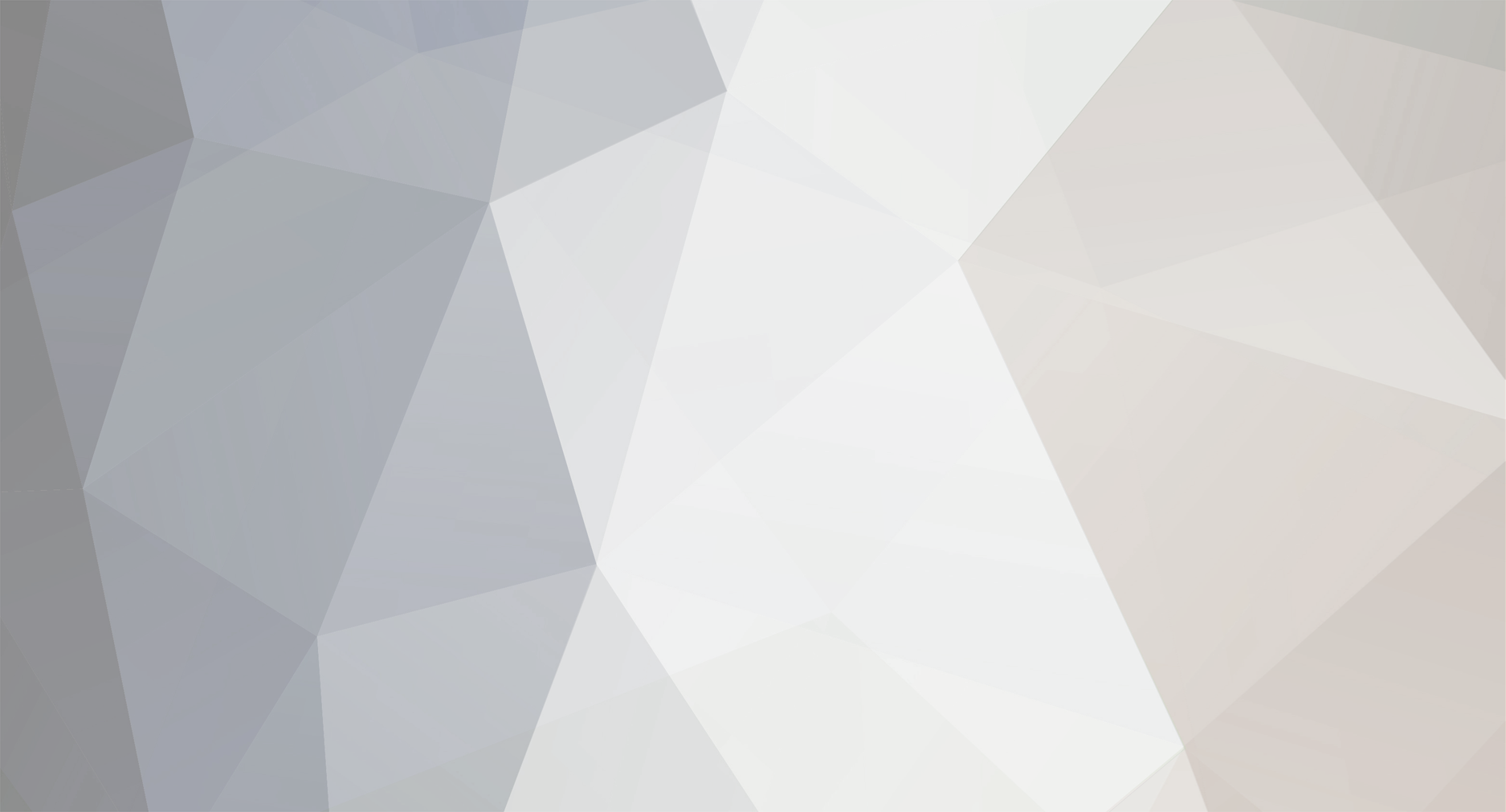
skippydiesel
-
Posts
6,893 -
Joined
-
Last visited
-
Days Won
69
skippydiesel replied to Lyndon's topic in Aircraft General Discussion
skippydiesel replied to Lyndon's topic in Aircraft General Discussion
skippydiesel replied to danny_galaga's topic in AUS/NZ General Discussion
skippydiesel replied to Garfly's topic in AUS/NZ General Discussion
skippydiesel replied to Lyndon's topic in Aircraft General Discussion
skippydiesel replied to Lyndon's topic in Aircraft General Discussion
skippydiesel replied to red750's topic in Aircraft Incidents and Accidents
skippydiesel replied to Lyndon's topic in Aircraft General Discussion
skippydiesel replied to Lyndon's topic in Aircraft General Discussion
skippydiesel replied to Lyndon's topic in Aircraft General Discussion
skippydiesel replied to Lyndon's topic in Aircraft General Discussion
skippydiesel replied to Garfly's topic in AUS/NZ General Discussion
skippydiesel replied to Christin's topic in Aircraft Building and Design Discussion
skippydiesel replied to pmccarthy's topic in Aircraft Incidents and Accidents
skippydiesel replied to Peasant_Pilot's topic in Aircraft Building and Design Discussion
skippydiesel replied to Peasant_Pilot's topic in Aircraft Building and Design Discussion
skippydiesel replied to Garfly's topic in Aircraft Incidents and Accidents
skippydiesel replied to Garfly's topic in Aircraft Incidents and Accidents
skippydiesel replied to Garfly's topic in Aircraft Incidents and Accidents
skippydiesel replied to Garfly's topic in Aircraft Incidents and Accidents
skippydiesel replied to danny_galaga's topic in Aircraft General Discussion