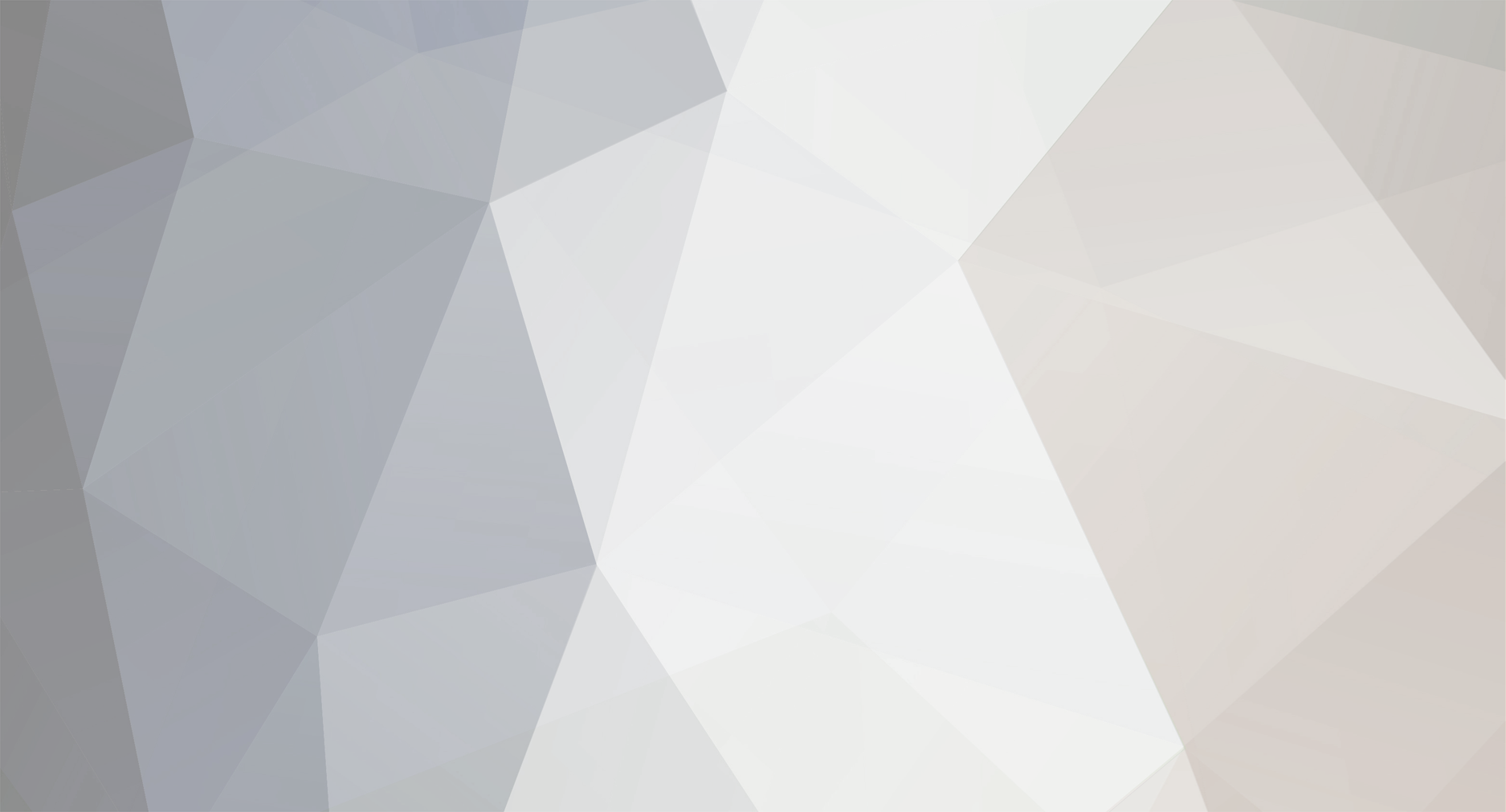
Oscar
Members-
Posts
2,485 -
Joined
-
Last visited
-
Days Won
67
Content Type
Profiles
Forums
Gallery
Downloads
Blogs
Events
Store
Aircraft
Resources
Tutorials
Articles
Classifieds
Movies
Books
Community Map
Quizzes
Videos Directory
Everything posted by Oscar
-
jj - I think I have confused myself, and you are correct. Mind out to lunch, I suspect...
-
Apologies: my previous post re the CAMit TOCA was not well-worded. I have the '88-degree' thermostat installed, which ( as I understand it), means it 'cracks' at 88 C and is fully open at about 96C. The location of the standard Jab. OT sensor places it in the oil that is cooled by heat transfer from the alloy sump in the general air blast from the oil cooler intake, creating an 'inversion layer' in the oil in the sump. What that causes, is a fairly thin layer of well-cooled oil, over the top of which the hotter recirculated oil slides around the engine. The TOCA thermostat reacts to the OT being delivered at the oil cooler take-off - i.e. effectively the last point in the oil delivery system. Unlike the OT sensor, it is getting the oil that has done the work of lubricating (and cooling) of the engine bearing surfaces.
-
Retained water in the oil can boil (turn to steam) at high-temp bearing points, expressing the oil film and causing scouring damage. In the CAMit development research, several instances of this were found in Main bearings of Jab engines sent to CAMit for a 'CAMit rebuild" , (identified by one of the experts in bearing shells in Australia) which was previously thought to be over-compression in the crank-case halves. The role of oil-cooling as a medium of extracting heat from engines has been used very effectively in motorcycle engines ( the GSX-R Suzuki inline 4 and the Honda VFR v4 are examples) - but the engine has to be designed for this. The Jab. engine is not. To get the best result from increased oil-cooling on a Jab. engine, one needs to have the CAMit TOCA ( thermostatically-controlled Oil Cooler Adaptor) installed. It maintains flow to the oil-cooler ABOVE the minimum desirable temperature ( set for the CAMit TOCA at about 96C). Then, with a decent oil-cooler set-up, you will operate within a band of 96C and tops 100 or so C in extreme conditions. Sadly, the CAMit TOCA is no longer available, but there is a British version which I believe is available to order. I have a CAMit TOCA and an Aero-classics 7-row cooler on my engine. I don't have flight testing on the efficacy of that yet - but I won't be prised loose of the CAMit TOCA by a large hammer.
-
DooMaw - building a STOL
Oscar replied to Head in the clouds's topic in Aircraft Building and Design Discussion
Great to see you back on the case, HITC!. And - as always - the pictures of your construction work are, to me, both a joy to look at from the excellence of structural integrity and humbling for the quality of your work. Any tube-frame structure looks to be really simple, BUT to get the force lines being taken out absolutely concentrically to the tubes and properly resolved through the projected lines through the centre of a join in a multiple-angle, multiple-tube joint cluster is work bordering on the mystical and arcane, for most people other than those deeply immersed on this sort of work. I've only done a couple of mounts ( a Jab. 2200 into a Motor-Falke, and an engine test cell mount for Jab. engines) and the time, patience and occasional wasted tube I had to expend on those, gives me huge respect for your stuff. I reckon you'd get a tick of approval from Barry Manktelow anytime. Anybody who reckons that it'd be easy to just hang the engine out the front where you want it to end up, and then cut and weld tubes to make that actually happen, has never tried it. Having recently made up an airbox for my Jab. project, I am most interested to see what you will come up with as an alternative to what - I assume - was a standard Rotax airbox? If it IS a standard Rotax airbox, to me (only from looking at your piccy of it), it has a monumental deficiency in terms of meeting the FAR requirements ( not necessary for an Experimental, of course, but still worthy of noting as an operator..) The FAR requirement for an airbox requires not just to provide heated air (I think from unreliable memory, it's a 20C air temp rise over ambient but don't jump on me if I am wrong here) when selecting 'carby heat', but also to provide an alternate inlet tract path in the case of blockage of the air filter. That might sound unlikely - but in Australian conditions, you could get that from a take-off in bulldust / heavy chaff from a recently stripped wheat paddock/ grasshopper swarm, for instance. Or a dead budgie sucked onto the inlet scoop.. Probably not problems anticipated in operation in a European environment. The FAR requirement is for the hot air intake to bypass the filter. I assume that this has been predicated on the idea that hot air is only pulled when in flight, where the air filter is pretty much unnecessary. My airbox meets that requirement - the original Jab. one in my very early Jab. did not - and it was a PITA to achieve it. I think all later Jab airboxes DO do it. With the Bing carbies used on both Rotax and Jab. engines, it is also important to have the carby balance tube intake(s) situated where switching to hot air doesn't screw up the balance air. When doing the certification tests for the Gazelle, a family member found that pulling hot air reduced the full-power revs by over 2K - if climbing out and the filter had blocked enough to collapse under full-power load, the thing would have mushed to a crash. Further work on that got the revs. drop to less than 200, (again,from memory - may have even been less than that). Just throwing on a pair of filters upstream of the carbies on a Rotax, will work fine - until they don't. At which point, I suspect, life becomes 'interesting'. -
As opposed to repairs according to what some bloke at the pub, whose mate once made a surfboard, told me? There is nothing wrong with using 'text-books' as a source of knowledge and a way to gain reliable information. 'Word of mouth' advice - unless absolutely and definitely coming from an expert - can be unreliable - and there is also the chance of mis-communication, as in the 'I know you heard what I said but I wonder if you understood what I meant?' syndrome. For those who do not have the background or the opportunity to confer with (or preferably, be trained by!) an 'expert' in the field, a reliable text will at least provide a basis on which to evaluate word-of-mouth information as to its value. We used to have, on this site, a self-proclaimed 'expert', some of whose information was so wrong as to be dangerous. I've heard some 'hangar experts' proclaim - with the certainty of bringing tablets down from the Mount - complete nonsense.
-
Every comment here is absolutely spot-on and very, very worth noting.. I would add a couple of (sub)-points. Inevitable result of that is excess weight or reduced strength, and/or the introduction of high-stress points into the adjoining structure. Examples of the latter include the mainspar carry-through on the early Foxbat A22, the u/c outer attachment on the Tecnam Echo, (same fault on some Citabrias). Making one part overstrong (or too rigid) may overload another part. Basically the same as above, with the added danger in a repair situation, that the resultant failure of another area in the load-path chain may present an unanticipated structure-critical failure point that could have catastrophic results where a failure in the original structure may have been relatively benign. Remember: in the testing phase, the aircraft is 'original', so the stress-chain for testing is 'original' manufacture. A repair that introduces non-standard stress concentrations HAS NOT BEEN TESTED.. A triangulated steel truss is easy to repair, relatively. Yes, this is completely true ( though getting access to replacement of a bent/fractured tube in a steel truss structure may be a PITA). In a truss structure, the load paths are entirely direct and the material composition is (almost) always 4130 tube - so any good LAME authorised aircraft welder can cut out the damage and replace it with same-spec. tube and it will not alter the integrity of the structure. As a further point: when training for my DoT authorisation as a minor repairer and CoA inspector, one of the points drilled into us was to appreciate and inspect for the 'collateral' damage (though it wasn't called that) that can occur. Example: damage to a wingtip from contact with say a fence-post or tree in a difficult outlanding. You have a dented/fractured tip. What is the first thing you go to look for? The answer is: the wing attachment points at the fuselage. The tip may be somewhat damaged - but the entire kinetic energy at the moment of damage transferred to the wing attachment points happened some 7+ metres away from the attachment points (for a standard-class glider). The loads on the wing attachment points are HUGE - and also not 'design loads'. It's not very useful if you just repair the tip damage and the wing falls off next flight. Tends to be a bit of a downer for the day. My point here is: aircraft are designed to very close tolerances for strength/weight. Repairing them is not quite the same proposition as - say - repairing the cracks on an FJ45 chassis.
-
It depends upon the part. I used to hold a DoT (predecessor to CASA, for aircraft regulation) Authorisation for 'minor' repairs and approved modifications to 'glass gliders (also a C of A Inspectors Authority). Now, this was 'back in the day' - 1978, to be precise - so my 'approved' expertise would not be relevant to higher-tech. composite structures ( e.g. c/f, vac-bagged or infused laminates, post-cured structures, aramid-fibre laminates, vinylester laminates). However, it IS relevant to the materials and techniques used by Jabiru. As it happens, I grew up spending a lot of my time 'playing' in the workshop of one of the finest luthiers of the C20, so I was taught quite a lot about woodwork, as well. Competent scarfing of a join in wood is considerably more difficult and demanding than for a simple composite lay-up (though ironically, the optimum scarf angle of 12:1 is the same, in most cases.) For wood, you need a drum-sander and a scarfing jig, so the join is an extremely accurate fit and you have not 'polished-off' the grain ends which prevents proper glue penetration. THEN, you need uniformly distributed clamping pressure over the entire length of the scarf. I cannot think of a way for this to be possible in a main bulkhead on a built Jab. fuselage without some extremely sophisticated techniques involving bespoke clamping structures pulled together from the front and back-side by torque-limited clamp arrangements (which WOULD need design input). With a laminate repair, IF you know what you are doing, you can prepare the scarf to the 'old' laminate with an air-tool mini angle grinder by hand - the input laminate lay-up will conform to any minor irregularities. BUT - I stress - If you know what you are doing. I've watched the guys at Aircraft Composites Australia ( Aircraft Composites Australia ) at work, and they are artists by comparison to just about all of us lesser mortals (me included). Seriously, it's like watching brain surgery vs. your local GP stitching up your cut from falling through a barb-wire fence. This has been a most interesting thread - to me anyway, who is returning a written-off Jab. - with now many modifications, I can't help myself from seeing things I would like to do differently - to the air. I salute all who have contributed for refraining from the 'Jab bashing' milieu that pervaded this site previously. The OP asked for advice, and I think much has been supplied, all in good intent. However, the range of opinions has made me think: How do you - if you're not very well conversant to the subject in hand - judge what is 'expert' opinion? I know that I have extreme difficulties making such judgements for areas ( such as Share portfolio management) where I do not even know what questions to ask.. Probably a subject for a discrete thread.
-
Bruce's post above is an excellent summary, with which I totally agree. And his Point #5 is the crux of the matter, indeed. Proved one can achieve the same structural result as the original then ipso facto the resultant structure is 'as good as new'. One of the real difficulties is, of course, achieving certainty that one HAS achieved the same result. Documentation, test samples ( e.g. resin coupons, lay-up coupons etc.) may be essential for that, and practical load testing may also be required. It most certainly CAN be done: Alan Kerr's advice to me when developing the scheme for my own written-off Jab. was: 'anything can be repaired, the question is - is it economically viable?' Since Alan not only did a huge amount of work on the early Jabs. (and continues to be a consultant to Jabiru), was the Jab. 'factory builder' for a while, and has also fixed problems on the F16 ( I think it was) fin and large USAF jet freighter mainspars, I reckon he knows that of which he speaks.
-
Yes, this is absolutely correct, in every respect. Jabs. are one of the most damage-tolerant and simple to repair aircraft there are, due to the 'low-tech' philosophy of construction. The resin (Araldite LC3600) is ambient-temp cure, with a decent spread of working temp. and humidity tolerance - ideally, 24C and no more than about 50% RH. The various 'glass reinforcement is also readily available - it is GOOD stuff, not Bunnings Aerospace crap - but when supplied from a reputable source ( e,g, Gurit, or CG Composites), you won't go wrong. However, there is rather more than JUST having the right resin and 'glass. You MUST know not just the correct repair techniques, but also the laminate lay-up schedule. If you do not have that information, and the expertise in 'glass repair work to aircraft standards, you are taking a huge risk.
-
C172 sitting in Paddock near LTV
Oscar replied to alf jessup's topic in Aircraft Incidents and Accidents
OH, yes... Cows are merely curious and somewhat clumsy, but all of a Bull's IQ swings between its hind legs. Sort of Like Donald Trump, but WAY heavier.., -
C172 sitting in Paddock near LTV
Oscar replied to alf jessup's topic in Aircraft Incidents and Accidents
ABSOLUTELY! -
I had a pair of ST1 wings transported from Perth to Sydney, crated and top-loaded, for a little over $1200. The huge cost of two-way transport W.A - Bundaberg and return transport for the repair quoted by Jabiru would be very much affected by the volume of a J2x fuselage with horizontal stabiliser and fin already attached, not the weight. Without the horizontal stabiliser and fin attached, I suspect that cost would be very, very much less for the one-way trip Bundaberg-Perth. The installation of the horizontal stabiliser and the fin is documented (I assume) in the J230 kit build instructions, so there is no 'repair scheme' cost. The work involved will be far easier than trying to achieve a fully satisfactory bonding and laminate build-up to an assembled fuselage: when you are working from the 'outside-in' on a structure that is assembled from the 'inside-out', it is exponentially more difficult (I speak from experience here.) When we were doing the fin replacement on our own Jab., my co-owner, who was filming the operation for the records, at one point asked me: 'Did you train as a Proctologist, or are you making this up as you go along?' ( it was the latter..)
-
C172 sitting in Paddock near LTV
Oscar replied to alf jessup's topic in Aircraft Incidents and Accidents
Cows are an even greater menace for gliders.... if you outland in a cow-infested paddock and only have enough tie-downs for the tail and one wing (normal), they have been known to walk on the wing that's grounded. I once outlanded near(ish) to Tocumwal; had selected a nice field capable of aero-tow retrieve; as I went to turn final I realised there were about 40 cows sheltering in the shade under the trees at the side of the paddock I had not seen from the air. Cue slam brakes and flaps away and fly down ( at fence-height, but with a couple of knots in hand) to the next paddock, which had irrigation ditches at 45 degrees to the paddock orientation. Squeaked over the fence and popped it down, ending about 100 yards from the downwind fence.. The retrieve crew from Toc. was NOT pleased with my choice of field - having had to drive for several hours to get there, plus dismantle and return time meaning a very late supper.. until I pointed out the cows in the better field. Ingo Renner, the CFI at the time, was not pleased that I had outlanded at all, (Ingo had a private arrangement with the god of Lift but that coverage did not extend to me..) but was gruffly pleased that he had a fully unbent IS29D2 ready to be used next day. -
The point made about the desirability of access to the factory mould(s) is well taken, but from more than just cosmetic reasons. The entire rigging of the aircraft necessitates accurate alignment of the primary structure, of which the front bulkhead and the lift-strut carry-through are critical members. The Jab. fuselage is effectively a tube (albeit a tapered one, so perhaps more correctly described as a 'cone'.) This example has damage to BOTH of those, so it is going to be hard, at the least, to ensure accurate end-to-end alignment from the bulkhead back to the tail-feathers without access to the assembly jig. Once the damaged section of the front bulkhead is cut out, the (already compromised) longitude accuracy of the 'cone' will be affected as it is no longer a 'sealed' tube (structurally speaking), and the damaged glass areas will tend to hold it out of alignment so setting up a temporary jig taken off the existing damaged airframe is fairly likely to simply reinforce the mis-alignment. If one had access to an undamaged 230 airframe, that would of course be easier. Even a slight amount of twist in the 'cone' could introduce some nasty effects. For a start, you could get a change in the engine offset angles (both horizontal and vertical would be affected). A minute change in the relationship between the lift-strut pick-up points would change the wing downflow over the tail, possibly leading to unbalanced flying at cruise ( not trimming straight and level..) and a tendency for the thing to break harder in a stall in one direction vs. the other. Then, there is the possible question of a requirement to at least proof-test the repairs to manufacturer's specs. It is worth watching: https://www.youtube.com/watch?v=XIV1ddkF-uM to see the complexity of the rig (which had calibrated test instrumentation).It is not impossible to do that, if you know what you are doing. But it IS complex to achieve. I replaced the fin and rudder on my aircraft, to a repair scheme provided by Alan Kerr (the gentleman in the blue shirt seen in the referenced video). Rod Stiff not only provided me with a new fin and rudder ( at 'mates rates'- many thanks to him, but there is a long history behind that that goes back to the original LSA55 development) but blessed the upgrade from the original LSA55 fin and rudder to the UL/J120 version. It was NOT a trivial exercise! Alan provided a 'proof-test' scheme designed for the level of a competent 'back-yard' workshop. I should add, that he knows my level of competence rather well. This is the 'backyard' test arrangement that reproduces, with sufficient accuracy, that undertaken by the complex test mechanism you can see in operation from about 1:40 to 2:30 in the referenced video: That arrangement is a 'whiffle-tree' that applies the load ( around 73kgs at the primary load-point, FYI) correctly across the whole of the fin structure. Despite the fact that it looks totally 'bush-mechanic' ( the load is water in containers, validated by double-weighing and water volume), it meets a very tight standard of loading specification ( and I am happy to say, met it NO WORRIES). But the major point is: without a scheme for loading provided by the guy who DID the testing for Jabiru, it wouldn't have demonstrably met squat. Now, think of the test mechanism that would be needed to be developed to meet the standards of the factory tests shown in the referenced video. You are talking loads of WAY over 70kgs, needing to be not just applied but also reacted out correctly. Personally, I wouldn't try it. Alan Kerr will tell you - and his is the definitive opinion, not just an idle comment - that ANYTHING on a Jabiru is repairable, due to its simple and durable construction. He will ALSO tell you ( I speak from personal experience) that the real issue is always: 'is it economic to do it?' The actual glass work is not all that difficult: the resin is Araldite LC3600 ( I enthusiastically recommend CG Composites in Brisbane as suppliers), the 'glass is readily available - but you absolutely need to know WHAT 'glass, and WHAT lay-up schedule: what weights, weave, weave orientation. Also, whether there is Coremat in the lay-up. Jabs are 'ambient cure' ( the ambient needs to be around 24C), so it IS possible. On the figures quoted by the OP, I personally think I would be going for a bare 230 fuselage from Jabiru and transferring all my good bits to that. The end result should be a 230 worth all of its real value, and a heap less angst.. An EL-restricted 230 will be worth a lot less. And I say that from the POV of a fanatic about doing it myself, for around the last 50 years.
-
Oh, yes, indeedy. I used to ride a mate's Darmah sometimes, with the standard Silentiums, but another mate had a 900SS (sliver/blue tank, octagonal case) with Contis. I used to like to sit on his tail through the twisties just to listen to it.. ( The Darmah wasn't a bad handler at all, not disgraced, though I think he was being just a little kind to me, he was a damn good rider). I used to keep my yacht in Pittwater, behind Scotland Island. The road into the National Park - (a magnet for motorcyclists) wound around the hills... You could hear a good punter with Contis coming around for maybe five minutes. Now, this was in the mid-80's when Car alarms were fairly crude, but it was a rich area and many BMWs and Mercs were parked out on the street because they couldn't get up/down the drives to the houses.. Contis, on a trailing throttle when 'making progress' as the English used to say, would set off car alarms. And - particularly on weekends, when the owners were out on their boats enjoying the serenity - the bloody alarms would shriek for hours on end. Nobody complained about the bikes - but there was a spate of attacks on high-priced cars from people driven out of their mind by the alarms. I've sometimes wondered what Contis would sound like on my 1986, (first model) VFR750, which below about 5k sounds just like a pair of Ducs in formation, though above 5k when the cam timing kicks in it howls like a dervish all the way to 12k. Would probably have me arrested for having too much fun.
-
Not running Contis, then....
-
It is interesting to look at the various claims for 'weight'. 'Dry weight', 'Wet weight', and 'Ramp weight'. For all practical purposes, 'Ramp weight' is the one you need to consider. That's the weight on the damn thing in a ready-to-fly condition, the one you need to calculate your adherence to MTOW ( and for that matter, W&B) on. It's a bit akin to IAS used as a claim for for VC and VSO vs. TAS for those..
-
A most interesting post, and I looked at the 'Updates' referenced. My interpretation of all of that, is that D-motor are very much taking the same path, in essence, as CAMit took: analysing the information coming back to them from real-life experience and implementing changes to address weaknesses/improve the product. Good on them, I say. As an aside to that, those who have followed the Jabiru engines 'saga' on this site will surely remember the charges laid against Jabiru of using their customers as 'test pilots'. Well, just perhaps, could it be accepted that this is in fact 'real life' progress for a new engine design?. The testing regime for certification / certifying a new engine, is designed to 'replicate' - as far as possible in a time-constrained programme - 'real life'. It is a rigorous regime that subjects the engine to testing to determine the operational limits for the engine and to set things like TBO. It requires very, very complex test equipment that can not just measure, but also introduce conditions that take the engine to beyond their designated operational limits to determine where that line has to be drawn. You can't just strap the engine to a dyno and measure stuff and say" here's the result.' This is the sort of complexity of testing that I am talking about: shows the control needed just for cooling testing: ( the unconnected as yet central outlet shown here, is for the oil cooler airflow delivery, to allow testing at elevated oil temps). That's my personal engine sitting under those huge cooling ducts, each of which can be adjusted for airflow.. The rig also allows for torque measurement using a 'representative' propellor ( required for the tests), oil cooling adjustment etc. The test cell allows for replication of conditions from MSL to 10K feet AMSL and for load conditions from static to full climb. The CHT, EGT and oil pressure and temperature measurement requires calibrated instrumentation. HOWEVER: ( and you need to be a little creative in your thinking to perhaps take this on board!), there is an old saying that 'nothing is foolproof. because fools are so much more inventive'. If you take this a little more liberally, it means that 'real life' throws up more challenges than the test can envisage/replicate. Does anybody really think that in the early days of Lycoming, Continental, even Rotax, their engines were entirely trouble-free? Perhaps they were, I do not know. But we didn't have the depth of reporting that we've had in recent times, so I doubt if there is a documented history to which we can turn for comparison. It's also worth considering that - at least in the case of Lycoming and Rotax - the manufacturers had multiple thousands of engines in service ( not necessarily in aero-engine service!) upon which to draw for experience. Specialist small-volume aero-engine manufacturers do not have that luxury. Jabiru ( the first of these, really), UL Power, D-motor etc. have a very, very small base of engines from which to base their development experience. Rotax had a huge base of engines for snowmobiles, motorcycles etc. 'out there' doing testing duty.. Even the 'big' companies, can produce dogs of engines. Anybody remember the development of the Datsun 1600 engine ( a really terrific adaption of the BMW 1600), that morphed into the 200B engine, which was a disaster? Or the GM LS1 engine? Or Porsche's attempt at developing an aero-engine from their air-cooled flat six? Seriously: a small ( miniscule, in the context of say Rotax) aero-engine manufacturer faces a hill for development of which they cannot even imagine the height or steepness. I can say with absolute certainty - having observed it - that a company like CAMit relied on its designer spending all his waking hours on both running current production and undertaking development. I have personally seen Ian Bent of CAMit bashing away not just at his computer on design work but out there on the machines making the new parts for test on weekends, when he had the space to undertake the creation of development ideas. I imagine it is the same for the guys at D-motor, UL-Power.. Should we castigate these tiny companies if their products do not in all cases achieve perfection? Jeez, let's look at recent history.. Apple, with phones and tablets that combust. Samsung, with phones that explode, washing machines that catch fire. Takata with airbags that kill. Ferrari with cars that catch fire. Rolls-Royce with engines that explode mid-air. Ad that's just scratching the surface.
-
May I offer a different perspective, based on personal experience? (And this is absolutely NOT a criticism of D-motor in any shape or form.) It is based on a long-time exposure to CAMit operation, and though I am somewhat reticent to discuss too much of that, I think I can draw some observations without compromising Ian Bent's IP - and there's no extant CAMit production - more is the damn pity. And yes, I AM going to beat a familiar drum, though I hope not too hard to cause flaming reaction - I believe there are lessons here that may now be too late to be taken on board, so for those who wish to flog a dead horse re all thing Jabiru or related, how about giving that away and looking at the broader issues? We see, in aviation, all too frequently, 'grand ideas' touted as the answer to the maiden's prayer. You can easily pick these: there is a flashy web-site, some CAD stuff, text promising revolutionary performance etc., and some oh, so beguiling mock-up images. And often, on the tabs to the web-site, one called 'Investors', offering the chance to get a piece of the action.. Not all that far removed from a Nigerian 'make a fortune' scam actually, but with images.. To develop an aero-engine to certificated or certified status takes a vast amount of energy, cost, time, research, trial, adjustment, re-test etc. From what I have seen, there are two distinct styles of 'manufacturer' ( to use the term loosely). The first example I will use here, is one with which I am personally acquainted ( for reasons that need not be explained, one of the Directors of this company buttonholed me in - an Aldi carpark!! - to ask me to join in the development exercise.). See: CoAxe Engine Company | Coaxial Engine Innovations This is a classic example of what I call the 'flashy BS' approach. Those with long memories will recall the name 'Ralph Sarich' ... Try: Ralph Sarich - Wikipedia What you will see, is a very successful investment campaign - Sarich became very, very rich. What you WON'T see, is any history of a produced 'Orbital Engine'.. Then there is the other approach: the true engineering professional one. This approach is the one used by those who actually intend to produce a good product. Very rarely do you even see anything of the early development, until there is at least a prototype running. The performance figures, the weight etc,. comes from RECORDED fact. In the case of CAMit, of course it was intricately linked to Jabiru from the first. And Jabiru itself also did the 'here's what we HAVE to sell you' route - not the 'here's your wet-dream machine, just send us a lot of $$ to get a place in the production queue' route. Rod Stiff and Phil Ainsworth put their money up front to make the things, CAMit came on board to develop and make the 2200 and 3300- engines. In neither case, was anybody asked to 'send us the money and hope for the product' - it was ENTIRELY: 'here's the product you can buy'. When CAMit decided to try to manufacture its own engine - based on the experience of having manufactured over 5,000 engines - it did not seek investment based on pretty pictures and BS text. It MADE the various developmental versions, tested them, had them running in customer aircraft with clients who understood that what they were installing was experimental. If real-time flight testing uncovered a problem, CAMit fixed it. ( including, problems entirely NOT of CAMit's making, such as a failed oil-cooler hose that necessitated a complete rebuild of the engine... that's customer service..) I don't follow either D-motor or UL-power with much interest, but in both cases, I note there are real examples flying and gathering data. Personally, I consider that to be proof positive that these companies are genuinely manufacturing a product worthy of consideration. If D-motor are not 'spruiking' their product at the moment, just perhaps it is because they have the ethics of not promising anything more than they can demonstrate they can deliver?
-
OK, you are exceedingly generous.. THIS, is the sort of thing that happens when one thinks: 'heck, I can do better'.. I don't like at all, the Jab. airbox and associated airflow delivery to the carby. So.... Started with a new airbox. There's a foam filter sitting under that spring-loaded flap that provides backfire relief to the filter. (old SCAT used for trial fitting, new will be installed) The Jab original (from their Installation manual) looks like this: I am biased, but I reckon mine looks neater..
-
The single ring-type thermocouple on NO #4 plus the lack of an ambient- temperature compensated cold junction has probably cost more Jabiru engines than any other single factor.. I think just about everybody who has moved from that set-up to a more modern set-up, such as using the MGL ( as an example) EMIS with temperature-compensation via their RDAC unit, and more accurate senders mounted between the plugs, has found that what they thought they were getting was very, very inaccurate and often very misleading. Jabiru has recommended full cylinder monitoring for many years now.. As Seb has found out - and we all should thank him profusely for sharing his 'Pilgrim's Progress' here - getting the cooling flow right is almost in the area of a 'dark art'.. And, lest he feel disappointed, I can say from the long, long experience of a family member who is an aeronautical engineer responsible for many engine swaps etc. - it is one of the hardest areas to get right. There is an old saying - attributed to, I believe, either Harvard or MIT - that: 'under known and controlled conditions of pressure, temperature and environment, the subject organism will do what it damn well pleases'... and cooling airflow is right up at the top there... It's not simply a matter of getting a big hole at the front and an even bigger one at the back... every change of direction, every change of area through which the air has to pass, creates its own influence. AND - just as an extra embuggerance - those changes, themselves change with pressure / airflow speed. What works well at say, cruise speed in flat flight, may NOT work at all well for climb.. ( and I KNOW I'm not telling anyone anything they haven't discovered) The Jab. ram ducts are, I believe , a particularly sensitive methodology of delivering cooling air, because they are a compact design. Lycs. and Continentals generally use large plenums which are less sensitive. That, at least, reduces 'choke' points for the airflow. I have gone, in my own radical development ( as yet, unproven in flight and may be a TOTAL stuff-up, so don't use it as anything but an 'idea' at this time!) for the more 'traditional' plenum idea - and then complicated it by splitting off the head cooling from the barrel cooling, but I did that as a research project, to back up a potential development that will probably never come - sadly - to fruition as the engine design for which that project was intended is unlikely to ever reach production now ( thank you, CASA..you bastards) If - in the fullness of time - it works well, I'll be happy to report on all the 'bits and tits' involved - it's taken hundreds of hours, from making new cowls onwards. If it doesn't, I will very probably slink away and take up macrame as a hobby..
-
Glider collision Bowenville
Oscar replied to fly_tornado's topic in Aircraft Incidents and Accidents
M6: would that bent stick have been in a Blanik? I ask, because a family member when a Gliding Instructor had a student freeze on the stick, and when trying to take command, felt the stick partially tear away from the cross-tube.. -
near beaudesert...2 deceased
Oscar replied to Kyle Communications's topic in Aircraft Incidents and Accidents
OK, I appear to have given the wrong impression here. I DO NOT deny the efficacy of a BRS to save lives ( if not really, save the aircraft -which I think is explicitly stated in the Cirrus brochures??) when things go irretrievably pear-shaped. If you lose a wing due to turbulence ( e.g. at least one Skyfox accident) - there is no other recourse than a BRS. If you are forced to land in a forest, it's probably preferable to be ab;e tpo pull the Big Red Handle - having positioned yourself into wind, and at a suitable height to achieve slow forward speed when hitting the tree canopy ( though some Jabirus have escaped serious occupant injury in that exact situation, due to their strong occupant capsule). As it happens, I started to design a personal aircraft (as best I could, given my non aero-engineering background) relying on the advice of one of the most respected aero-engineers in this country. Amongst the issues that we debated, was the cost/benefit of either going for a Certificated engine or a BRS as 'security' for operation over hostile terrain. The BRS came out best option, both on weight and cost. My concern about the more prevalent use of BRS, is that it appears to be becoming used as the first-resort option. This is, to me, akin to assuming that your air-bags will save you in your car crash and therefore you don't have to drive carefully or skillfully. Or even LEARN to drive carefully or skillfully. You can just buy the Volvo and go out on the road with not a care in the world for yourself, your passengers, or those around you. Perhaps I am showing my motorcyclist heritage here..( yes, I did have a 'Volvo Aware Rider' sticker on my motorcycles). Just pulling the BRS in a manageable situation is an abrogation of responsibility for flying competently. And relying on the BRS to save your ar$e because you choose to voluntarily fly into a danger envelope when other options are available, is equally irresponsible. -
near beaudesert...2 deceased
Oscar replied to Kyle Communications's topic in Aircraft Incidents and Accidents
FFS - with a functioning engine and an obvious clear and usable grass airstrip, you don't do a normal approach, hold off as long as possible after the round-out, cut the engine at the last moment and grease it on? Vs. pulling the BRS and smacking down? This reminds me of the incident somewhere in NSW where a Ford Explorer ( IIRC) had its cruise control jam on a freeway, and the stupid driver had time to call up 000 and shout something on the lines of 'It's out of control, I can't stop it, help, help' instead of turning off the ignition... Pulling the BRS in a situation that is easily controlled by a competent pilot, wrecks the aircraft because of stupidity. And as a result, all our insurance premiums go up, because Fwits throw away easily salvageable aircraft. I don't consider this to be a 'critical' situation where competent piloting would have made the outcome anything more than 'interesting'. As a reason to install a BRS, it fails the 'pub test' of acknowledgement that it in ANY way was the saving factor of a serious incident. Competent pilots have landed heavies full of passengers with failed nosegear with little more than a trail of sparks. -
Glider collision Bowenville
Oscar replied to fly_tornado's topic in Aircraft Incidents and Accidents
Ordinarily, I would not be bothered to react to the adverse posts on here to my comments, it's not worth the time or effort. However, in this particular case, I find the uninformed supposition on what is as yet an unexplained accident to be worse than unhelpful. As it happens, one of my family is a member of DDSC; and as it happens, the now widow of the Instructor was one of his students many years ago when he was an Instructor at Bathurst. He last talked to both the Instructor and his wife last week at the DDSC AGM, and his opinion of the Instructor corresponds exactly with Mike Borgelt's opinion expressed in post #8 of this thread. As it also happens, I have landed a glider in a situation of extreme medical incapacitation. Due to influenza and dehydration, I experienced an almost total physical collapse at about 2K feet AGL, just after release from the tug. I had not intended to fly that day but was asked by the CFI to move his personal racing glider ( a Hornet, and then current holder of the World record for a 500K triangle speed at the time), to the cross-strip at Narromine due to a 90-degree wind change. It was already hitched to the tug, it seemed the easy thing to do.. I cannot remember anything after turning final, until someone was pressing their fingers on my neck and shouting 'He's alive, I can feel a pulse'. As far as I am concerned, it basically landed itself due to correct setting of the trim at the FUST check. You fly MOST gliders (I cannot speak of personal experience for an ASK21) with your hand on your right knee and two fingers and your thumb on the stick. You do NOT have a 'death grip' on the stick that would force it into an extreme change of pitch even in a case of muscular spasm. This is a very,very sad event and the circumstances have yet to be revealed. Vicious defence of wild theories coming from a base of no knowledge of gliders, gliding, or glider pilot training does not help anybody's appreciation of actually what happened.