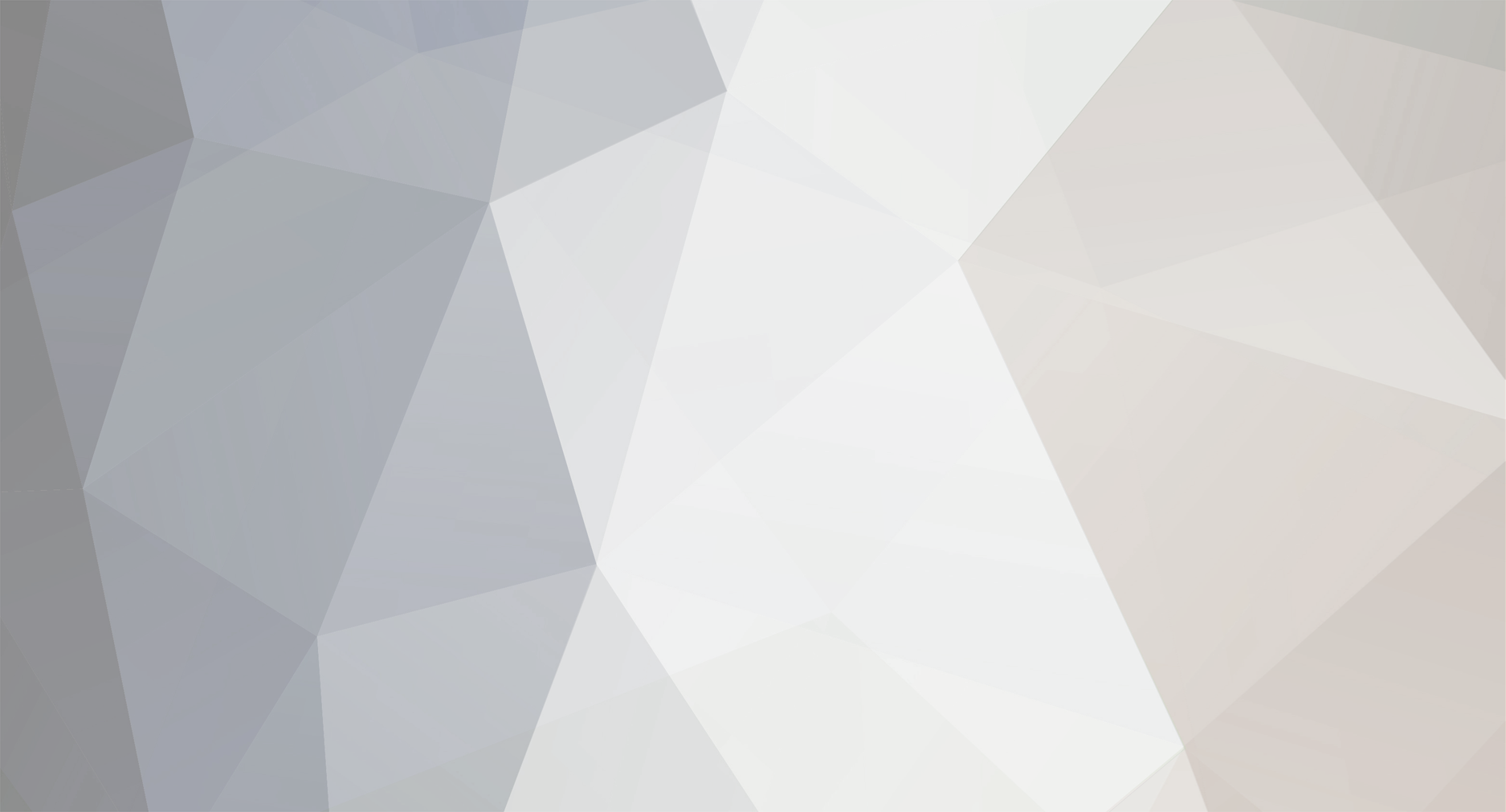
scsirob
Members-
Posts
60 -
Joined
-
Last visited
About scsirob
- Birthday 03/05/1963
Information
-
Aircraft
PH-ANR
-
Location
EHTE
-
Country
Netherlands
Recent Profile Visitors
The recent visitors block is disabled and is not being shown to other users.
scsirob's Achievements

Well-known member (3/3)
-
Note that some very old GPS receivers are not useful anymore. One of the counters in the GPS data has rolled over in 2019, and several older GPS receivers were not designed to deal with that. See: https://en.wikipedia.org/wiki/GPS_week_number_rollover
-
Actually, the oil sender fails from rapid fluctuations in the oil pressure. Several have researched this and it comes from the pressure regulator valve hammering open-close-open-close. The oil pressure sender is just a wire-wound potentiometer resistor with a mechanical wiper, and it dances with the rapid pressure pulses. This quickly wears out the wire and that makes the sensor fail.
-
Thanks! I built a plenum around the sump so the air passes along the sump and through the oil cooler, then down and out through the bottom of the cowl. That way it doesn't upset the low pressure needed for head cooling too much. Got two 3-into-1 CAMit mufflers, so there's ample space. The cooler is a universal type, I got it from a local VW hotrod shop: https://www.hotrod.nl/shop/contents/nl/p3271_Oliekoeler_element_48_rijen_____280_x_190_x_40_mm_.html I've seen similar ones in webshops around the world. In retrospect I should have gotten one size smaller, perhaps I'll swap it out later this year.
-
I'm using your Version 2 on my CAMit engine install. Works a treat, most of the year I have to block a large portion of the cooler to get the oil over 80 degrees C. Thinking about exchanging for a smaller cooler.
-
C/S prop installation on Jabiru 2200 &fuel injection
scsirob replied to lyle janke's topic in Engines and Props
If you want a Jabiru with proven EFI and electronic ignition, why not buy a UL-Power engine? They are a bit more expensive but less so than a Jabiru engine plus all the gizmo's you want to add, plus the installation and tweak time. -
Sounds like a great adventure! Just let me know when (if?) you are visiting The Netherlands, would be great to meet! Hele fijne reis en misschien tot ziens 😉
-
That would be 33SLRE-64 then, the '5' is actually an 'S'. Never found a decoder ring for the letters, but SL probably means 'Solid Lifter' (which they all are). The serial number is past the early piston spring issues and before Camit had to scrape the bottom of the barrel for parts. Others may know more about the piston issues, but I'd take that engine any day.
-
Do you know the serial number? I have 0112L which was produced a month or two, maybe three before the demise of Camit. It runs pretty sweet, no signs of trouble after ~250hrs in my Rans S-6S. When mine was built, Camit was already struggling. The highest serial number I have heard of was from someone in South America, around 0121 or so. Early Camit engines were said to have been fitted with wrong material piston rings and/or fragile pistons, but that would have shown after less than 200 hrs. Ask for maintenance logs, ask if there was any major work done, ask why the owner wants to sell after just 200 hrs.
-
Jabiru seems to not know that. They have used sealant on the rubber rings of the intake manifold from day one. They also use sealant on the oil pump that also has O rings installed, both on the back plate as well as the housing. On the Gen-4 engine they have changed the back plate design to include a second O ring (found in the CAMit engine), and they removed the sealant requirement there.
-
Can we add Zoche to this list?
-
This is my local experience in The Netherlands. I ran my previous Jabiru 3300 exclusively on Mogas (Euro-95) without ill effects. My current CAMit 3300 has 150 hours on it with Mogas as well. Last year after local authorities upped the Euro-95 ethanol content to 10% I started to notice rough running in some situations. I moved to Euro-98 BP Ultrium. This is labelled E5 which means up to 5% ethanol, but we have written confirmation that BP Ultrium for now has zero ethanol in it. Mogas keeps the engine relatively clean.
-
cutting holes in an aluminium instrument panel
scsirob replied to danny_galaga's topic in Instruments, Radios and Electronics
I've made several prototype panels using a simple jigsaw for the holes. File and sand for good fit. When entirely happy, I then drew them in a simple CAD program and sent the resulting AutoCAD file to a local waterjet shop. €100 for three panels. Then had them stove painted for another €25. -
For our visiting friends from abroad, please note that on November 7th, The Netherlands will have a new CTR and changes to the airspaces around Lelystad Airport (EHLE). It will be class D airspace with mandatory radio contact, crossing clearances etc. Please make a mental note and check the AIP here: https://www.lvnl.nl/eaip/website_EFF_10OCT2019/2019-09-12-AIRAC/html/index-en-GB.html
-
It's attached to the input side of the carb. The largest risk of ice forming is at the opposite side, at the butterfly. Especially with low power settings and the butterfly almost closed. The engine is a huge air pump. At 4600 rpm and 1200-1350cc displacement, you are looking at about 40 liter of air per second passing through that venturi. That's a lot of cooling capacity. Having 50W or 100W of electric heater on the outside of the carb body won't make a dent in the temperature of the mixture passing the butterfly.
-
From the pictures it looks like it is on the input side of the carby. That makes no sense. No amount of available electric power on that side will significantly raise the input air temperature enough to avoid carb ice. There's other electric carb heaters producing about 50W that attach to the butterfly side where it may help a bit, and they are hardly effective. I'd opt to remove this pre-heater contraption and find a way to install proper hot air carb heat from near the exhaust pipes