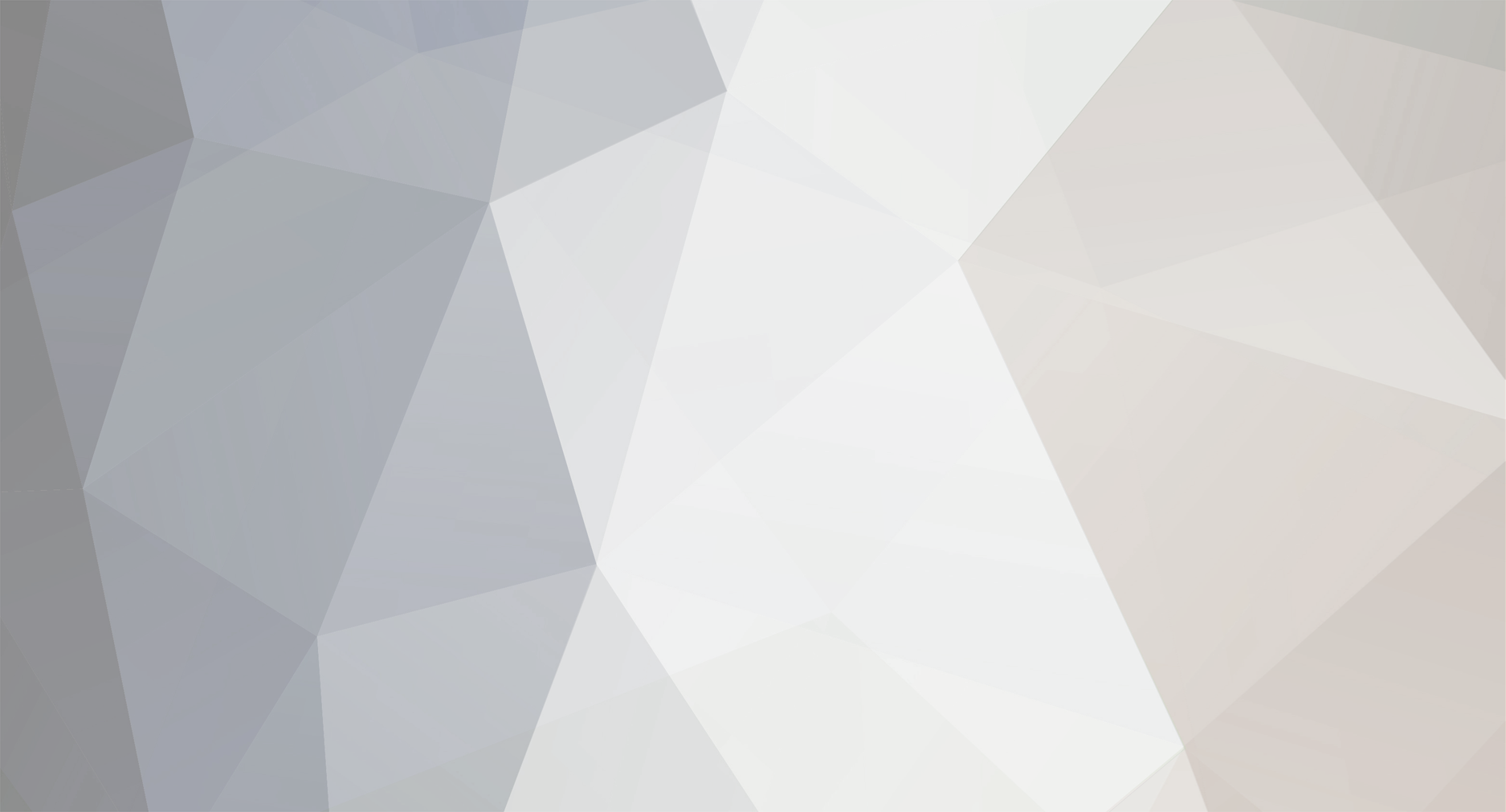
Nobody
-
Posts
720 -
Joined
-
Last visited
-
Days Won
3
Nobody replied to scre80's topic in Aircraft Incidents and Accidents
Nobody replied to bexrbetter's topic in Aircraft Building and Design Discussion
Nobody replied to bexrbetter's topic in Aircraft Building and Design Discussion
Nobody replied to bexrbetter's topic in Aircraft Building and Design Discussion
Nobody replied to Old Koreelah's topic in Governing Bodies
Nobody replied to bexrbetter's topic in Aircraft Building and Design Discussion
Nobody replied to bexrbetter's topic in Aircraft Building and Design Discussion
Nobody replied to Jerry_Atrick's topic in AUS/NZ General Discussion
Nobody replied to bexrbetter's topic in Aircraft Building and Design Discussion
Nobody replied to bexrbetter's topic in Aircraft Building and Design Discussion
Nobody replied to Nobody's topic in AUS/NZ General Discussion