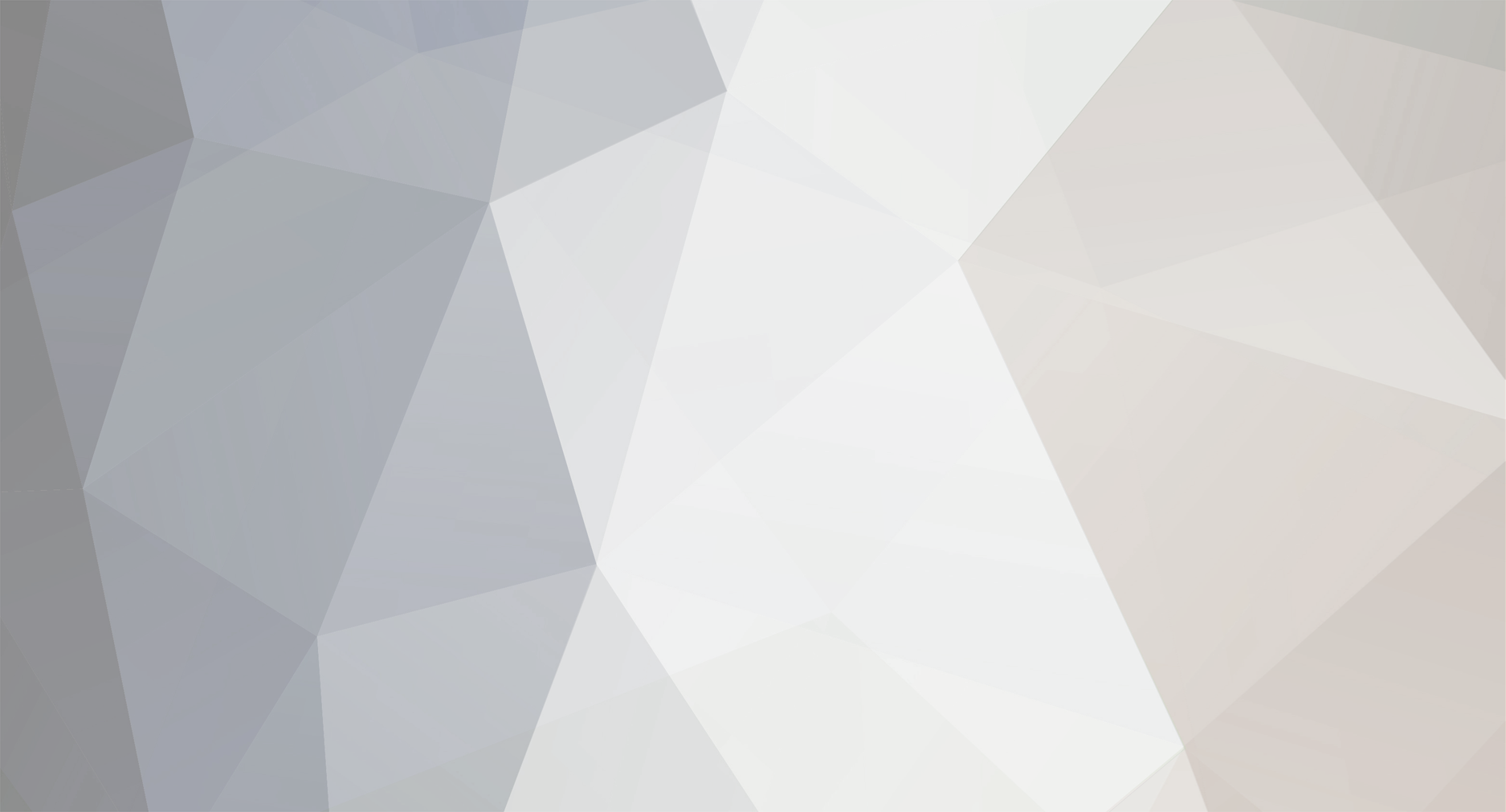
scsirob
Members-
Posts
60 -
Joined
-
Last visited
Content Type
Profiles
Forums
Gallery
Downloads
Blogs
Events
Store
Aircraft
Resources
Tutorials
Articles
Classifieds
Movies
Books
Community Map
Quizzes
Videos Directory
Everything posted by scsirob
-
I consider dynamic balancing as icing on the cake after a lot of other stuff has been addressed. - Static balance is important. - Identical setting of the blade angle on adjustable props. One blade half a degree in or out can make a big difference. - Proper tip tracking. If the tip of one blade follows a different path (>2mm or so), you'll have more vibration. - Even compression on the cylinders. One weak cylinder can cause a lot of vibration that you won't be able to balance out. - On Rotax engines, poorly balanced carbs will mess up an otherwise smooth engine too. Once all those are taken care of, a dynamic balance can squeeze out the last bit of comfort. On my plane I have marked relative position for all parts of the prop, spinner and backplate so I can pull the prop, reassemble and still have perfect balance.
-
To the best of my knowledge, Jabiru and CAMit use the same guides. Jabiru opted to go with a Chinese valve vendor some years ago CAMit appear to have used valves from the UK vendor that Jabiru started out with. Either valve can be used, as long as you have matching collets.
-
Another factor is exchange rate. Rotax is European. Over the past 10 years the exchange rate has fluctuated from 0.45AU$ to 0.85AU$ for one €. Almost a factor of two. It's now at 0.63AU$ to 1€. That makes a steady business model very hard to do.
-
Well done! Great project you have there. A couple of years ago I modified a set of Kuntzleman position lights to include LED strobe lights. One side with a Bridgelux BXRA-N0802 LED, the other side with an array of smaller Cree XLamp MX6 LEDs. Rather than trying to regulate the current, I placed the Cree LEDs in series to have a string with nominal Vfwd of ~13.5V. Came out at 4 LEDs. Rather than try to regulate, I used a low ohm resistor in series. If you look at the Vfwd curve and Ifwd curve of the LEDs, you see it rises sharply once they reach normal working area. Say normal bus is 14.4V. For 1A of current and 13.5V Vfwd, you'd need to lose 0.9V across the resistor. A one Ohm resistor will take care of that. When bus power goes up to 15V, you'd see that the resistor absorbs up most of the current rise and Vfwd stays pretty close to normal. When bus voltage sags to below ~12V then the LEDs don't work anymore, but you'd have a different problem anyway.. In my application as strobe, duty cycle is low, and a bit of overcurrent isn't an issue. In fact I used a bit thinner AWG#22 wire to power the strobes in the wing tips and relied on the resistance of the long wires to limit the current ;) Perhaps you need to be more careful when running 100% duty cycle landing lights. Below is the circuit I designed. I (ab)used the white LED in the position light to provide a ~3.5V power to an ATTiny microcontroller (same as your PIC chip). I didn't design a PCB, I built it 'dead bug style' inside the position lights. Has served me well for the past 5 years.
-
If you want moving maps, they exist. It's called Dynon, MGL or Garmin, and costs accordingly. Or an iPad or Android-based software solution Even Avmap have a moving map (EKP-V), and it offers many of the HSI functions that the UltraEFIS has. For more $$$ and unfortunately not so stable.. The UltraEFIS works as designed. Low cost, many handy functions. You can insert your own waypoints including runways. Great backup for whatever GPS moving map you have available. It now offers NMEA out, which I use to feed into a PilotAware anti-collision device.
-
The first electric aircraft in Australia
scsirob replied to red750's topic in AUS/NZ General Discussion
I tried to put things in perspective. Pipistrel uses a 50kW motor. At 70% it would be running at around 35kW. Equivalent to a Rotax 503 or 582. You can get away with that with a slick, light plane like the Pipistrel. You can not do that with the equivalent of a Cessna or a Rans S-21. If you want the equivalent of a 150HP engine and 3 hours endurance then you will need 300kW worth of batteries. Tesla's equivalent weighs 1800kg. The 150kg Pipistrel pack has approx the same amount of energy density in kW/kg as the Tesla packs. You'd need roughly the same weight in Pipistrel packs if you want that 300kW of energy. And again, my point wasn't to show that the motor and battery technology can't be developed to fit. Perhaps in a few years all that will be reality. My point is that the charging infrastructure needed to keep a fleet of GA planes in the air is immense, and I don't see it happen. -
The first electric aircraft in Australia
scsirob replied to red750's topic in AUS/NZ General Discussion
Copying from what I wrote on the Ransclan forum, where the Pipistrel was mentioned as well, and the 'option' of an electric powered Rans S-21was discussed: --- I don't buy the viability of electric planes in the S-21 class. Let's do a bit of math. The sweetspot for the S-21 when looking at the options mentioned in this thread are engines that produce 120 - 180HP. Let's take 150HP as starting point. Cruise is between 65 and 75%, lets take 70%. So cruise power is 105HP, or 78kW. Now let's take a usable airborne time of 3 hours, which most of us would agree to be the minimum for a usable aircraft. Add 30 minutes reserve, you are looking at 275 kWh worth of power. Not sure what efficiency ratio you can get in electric but let's be optimistic and call it 90%. You'd need 300kWh battery installed. That's three Tesla Model S battery packs with the latest 100kWh batteries. Current weight is 600kg for each battery pack, but technology progresses. Perhaps battery weight can be slashed to acceptable weights. Let's assume it does. Now you've flown 3 hours and your battery is empty. What does the charge cycle look like? You want to return home after visiting the nearby restaurant, eat your $100 hamburger, have a chat with friends. Let's assume you want to return home after 4 hours. You have consumed 3x 78 = 234kW of power. That amount of energy needs to be charged back into the batteries. Again, let's assume 90% efficiency in charging, so in 4 hours you need to inject 260kW. Now take a commercial building 120/208V 3-phase connection. Each phase will need to deliver 180A continuous for 4 hours to make this happen. Mighty big cable, don't even think you can get those kind of current supplies on commercial outlets? You'd need to go 277/480V industrial to make this work. And it still takes 4 hours to 'fill her up'. Now take a look at a residential airport. How many planes fly in and out on a busy day? How many take 10 minutes to fill the tank? These all need 4 hours now. So put them all on a row and supply them with a charger cable. How many chargers would you need? That, times 180A 3-phase. My conclusion: Even if motor/battery dimensions are developed to fit, the issue will be the charging infrastructure. Every airport would need a mid-size nuclear power plant next-door to keep the planes flying. Not an option. The power density of gasoline is very hard to replace. Very slick low-drag aircraft may get an hour or so of airtime. Our relatively draggy Rans/Murphy/Cub/Cessna type planes will never be a viable option. Happy New Year to you all! -
I built mine, and I fly it regularly. The S6 is a very friendly plane, easy to fly, rugged and very roomy. Mine has the bubble doors, which ensures that you can even go up with a couple of big guys and not have shoulders rubbing. If you do buy one, ask for which type of wing it has. Depending on the wing type and age, there are differences in MTOW and speeds. It also supports a range of engines, starting with a Rotax 503, all the way up to 120HP Jabiru/CAMit, UL-Power and such. I have a CAMit 3300 up front. There's an active Rans community at www.ransclan.com where there's people with knowledge, ready to give you advice. As far as fabric, the stuff that Rans uses (Superflite) holds up well over time. Repairs are a bit more involved than what you'd do on metal aircraft, but well understood. My plane was built between 2000 and 2007, covered in 2003 and painted in 2005. The attached picture is from this summer.
-
Is this any good? Camguard Aviation Oil Additive.
scsirob replied to waraton's topic in Engines and Props
What you proved with this, is that the stuff protects against "extreme pressures" that are not a factor in tractor engines. A bit like bottled water, advertized as "0% Fat". -
On a dyno for 30 seconds, yes. In a street race for 1 minute, yes. Now try to run that level of power for a number of hours on end.
-
Jabiru cancels due to Bundaberg weather
scsirob replied to biggles's topic in AUS/NZ General Discussion
Ehhhh.. Dangerous?? -
Your bias is well justified, a true piece of art!
-
My AvMap EFIS has been running fine for 1.5 years. Never bothered to set up the compass, got a magnetic one anyway. Also had an AvMap V GPS. Buggy software, froze mid-air with no way to reset. Returned it for refund.
-
Light Aircraft down Near Bundaberg
scsirob replied to ave8rr's topic in Aircraft Incidents and Accidents
My €0.02 : The big red flag is the valve sticking out. That doesn't happen unless a piece of piston is found wedged under the valve, or it was stuck to start with. Stuck valves have happened before due to lead build-up, insufficient clearance, or burned oil residue from overheating. I'd put my money on overheating. Valve sticks, piston hits valve and shatters on first impact due to being weakened, valve bends. The investigation reveals the die grinder and sander marks, which are bad, but these are only secondary to the damage. -
Well, that makes sense, but how then can CASA prevent someone from having a plug/mould built by another company if that's not the factory? The factory built 49%, "others" built the remaining 51%. Is there anything dictating that none of the "others" can be a commercial entity? If someone buys an instrument or an autopilot, a commercial entity built the instrument. Does that go into the 49% or the 51% bucket? I'm asking because I think it is a non-sensical rule. As long as the factory themselves isn't involved in the 51%, it should fit the 51% rule. But that's just my logic.
-
Not really. What I mean with 'real' aircraft engine, is any engine that's designed from the ground up with aviation in mind. Full ignition/injection redundancy, low stress design, low weight, KISS principle. The Lycosaurs fit that bill (weight, hmm...), but others are starting to get there as well. I consider UL-Power (Air-cooled metric Jabiru copy with modern injection/ignition) and D-Motor to be in that category as well, just not as high volume and long track record yet. CAMit could have been there, but oh well.. Not entirely sure about the 4-stroke 912 but the 503/582 2-strokes were designed for snow mobiles, not aircraft. The 912 does well but have had their share of gearbox issues. Also, selecting Ducati for their ignition and regulator circuits has shown to be problematic. The core is good. The ancillaries not so much. Converted Honda/Suzuki engines are designed for mass production and therefor pretty reliable and predictable in performance. Good cores. It's very often the reduction drives and other adaptations to make it fit an aircraft, that are the weak spot. Not enough volume and not enough R&D resources to become as reliable as the core engine. Subaru EA-81 boxer engines were originally designed for aircraft but ended up in cars. They were a nice starting point for converting (back) to aircraft, but even there, the reliability of the package was often low due to reduction gear issues. The bigger Subarus are in the sweet spot for many planes from a power perspective, but once again the reduction gears and other adaptations to make it work in a plane have been shakey. Once again, Google "Jan Eggenfellner" for details..
-
Perhaps The Belgian D-Motor is a reasonable option for those who want all the modern gizmo's (multi-point injection, dual ECU, dual ignition) but still have a 'real' aircraft design. Very light, very simple. Direct drive, flat-head design. Not as cheap as a conversion, but certainly a reasonable alternative for the 912ULS. www.d-motor.eu
-
AVMAP V and engine management thing
scsirob replied to rmorton's topic in Instruments, Radios and Electronics
I have an EKP V and an UltraEFIS. Both nice instruments but with some oddities. The UltraEFIS manual shows RS-232 out capability which their rep told me it would be available 'soon' at Oshkosh 2015. But despite asking support multiple times, it isn't being released yet. Last software version is from December 2015. EKP-V has a brilliant display, very easy to read in direct sunlight. The internal software is outdated though. It runs on Windows CE (like the old car navigation devices), and they are having trouble to update it into the modern world as well. It claims anti-collision facilities but those only exist for ZAON XRX which went belly up how many years ago? I'm afraid it seems the aviation group within Avmap is a very small crew with limited resources. If I had to choose today, I'd probably go for an iPad Mini or Tab S2 instead. More options to change software (EasyVFR, SkyDemon, Navaid, etc), and quicker with updates. -
So it's getting close to a month since impact. Has anyone been able to track the whereabouts of the equipment, plans, IP, spares, and perhaps Ian?
-
I'm confused.. How would those flaps prevent the air filter from being crushed when the flaps are on the intake side of the filter? Any backfire pressure will have to travel back through the filter to get there.
-
Just over AUD $20K including TOCA, CHT sensors, ram air ducts and air freight to Europe. Amazing delivery, less than a week from factory to my doorstep in The Netherlands. No GST gets offset by local import and VAT charges but in the end I was better off than buying my Jabiru in 2003.
-
I can't for the life of me imagine that all Jabiru owners who have been stung by the earlier issues and now abandoned engines, wake up in the morning and go "Oh what a beautiful day! Let's fork over another big chunk of change to the lovely people at Jabiru for serial number 1, 2 and 3 of their latest promise!". You may call me cynical. According to Rotax themselves, the 915IS (announced mid 2015) will not be available until mid-2017. Bit of a stretch to call that a success. The 912IS have had their share of issues, I'd be interested to find actual sales numbers, compared to the other 912 siblings. But to be fair, a so-so sales season for Rotax would make most other engine manufacturers freak out completely. It's lonely at the top.
-
Sue explicitly wrote that volume is very, very low. It was also mentioned that they had hardly any engines in stock anymore. So there's no volume to speak of. Now how much sense does it make for Jabiru to start an entire new engine production line with all associated costs, just to feed a few airframes a month, while Jabiru is already strapped for cash from the CASA situation? It defies logic.
-
Not want to digress too far from the main subject, but Rotec just posted a new video on Youtube. Rather than the previous ones showing off their latest and greates accomplishment, this one is more like a commercial. "We have all these engines in stock, come and get them...". What message does that send?