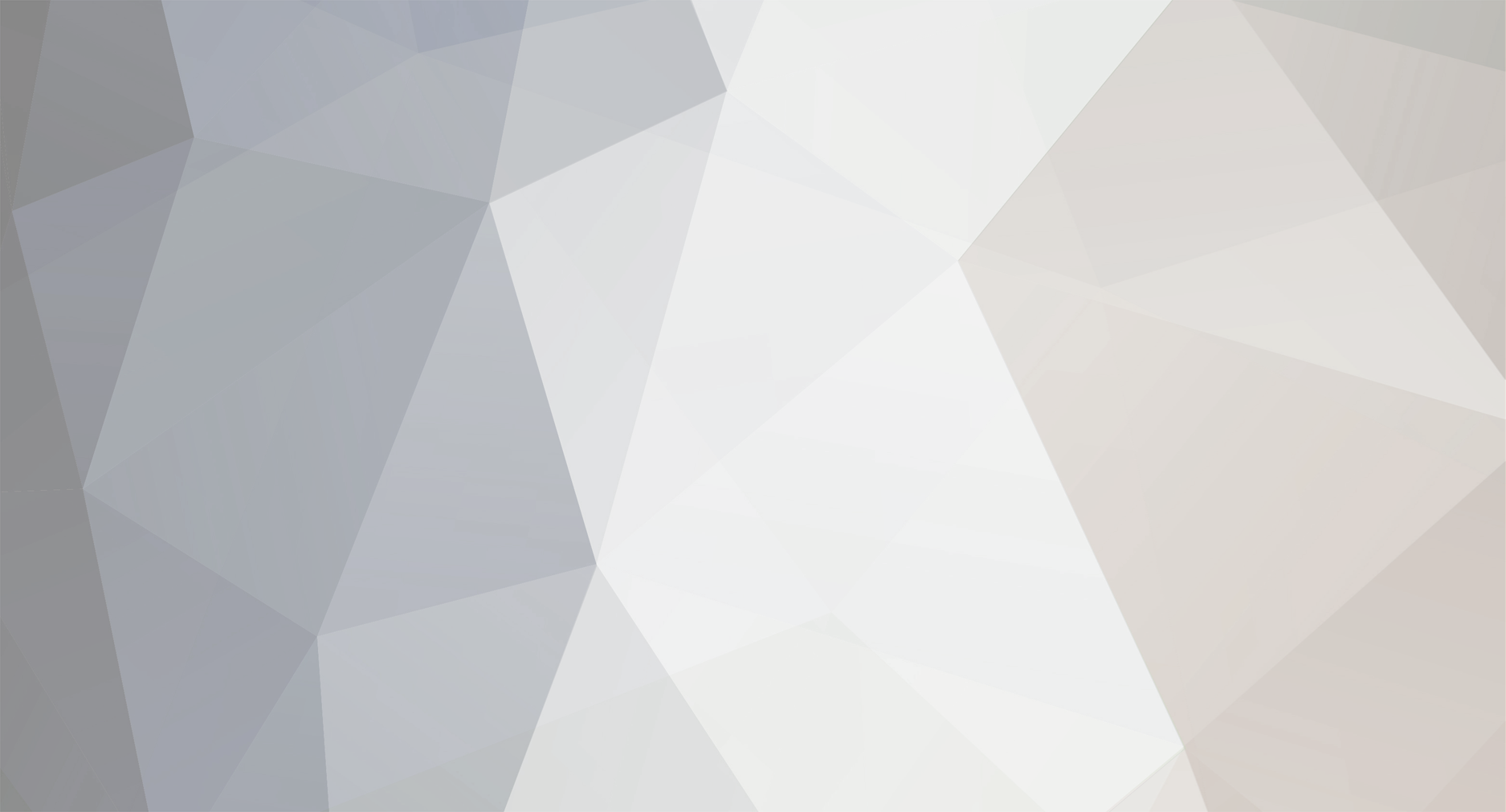
Raytol
Members-
Posts
110 -
Joined
-
Last visited
Content Type
Profiles
Forums
Gallery
Downloads
Blogs
Events
Store
Aircraft
Resources
Tutorials
Articles
Classifieds
Movies
Books
Community Map
Quizzes
Everything posted by Raytol
-
I got stung 6 cents/ dollar for a recent exchange from AUD to USD! Don't believe the exchange rates quoted by your bank as they can add fees and charges on top of that as well. I think Zongshen make the Chonda motors in all the cheapy outdoor equipment. Large manufacturer and getting good.
-
CO is dangerous because it sneaks up on you. I was qualified to do repairs to underground fiberglass storage tanks. Our instructor told us that in this situation it is usual for three people to die. The first person passes out and the second person rushes in to help them. Then later a third person investigates to see why they haven't been seen for a while, and goes in ( by this time the compressor/ generator/ water blaster engine has stopped) and they die as well! I had just finished repairing some methanol tanks at the water treatment plant in Canberra. I was driving home and heard on the radio that just this scenario had just happened on a farm in the area! I was very grateful for all the safety gear I had to use under my Safe Work Management Scheme!
-
Struggling With Aircraft Classifications
Raytol replied to walrus's topic in AUS/NZ General Discussion
Lovely, concise explanation. Thanks Kasper -
I think that C of G and weight distribution only matters on aircraft that don't have all flying tailplanes. All flying tailplanes will keep the stability right up to when the tailplane stalls in both the downward AND upward lift situations. This is one of the biggest advantages of this configuration of aircraft. This means that the pitching moment generated by the wing can be positive OR negative. We flew a Sapphire ( which has the same symmetrical section design as my Grasshoppers, Stingrays and Morgan Aeroworks aircraft) at 66% with no noticeable difference in stability or control. I wanted to go to 99% but the owner chickened out! The symmetrical all flying tail doesn't generate the high coefficient of lift that the "flap" effect does on a TP/elevator system does but it does fly at the minimum drag for the wing/TP situation therefore lowering the overall drag of the aircraft. I can't understand why so many Morgan aircraft are flown at such forward Centre of Gravity's! The ingrained thinking that forward Cof G equals safety is not always correct!
-
LSA's are 13 x more dangerous than motorbikes?
Raytol replied to APenNameAndThatA's topic in Aircraft Incidents and Accidents
The old saying was " you are more likely to be killed driving/ riding to the airport than flying in your aircraft". Not sure this is statistically correct but it sounds good! -
In these days of technology taking over everything, why doesn't someone come up with an voice recognition app on their smartphone that can translate their intentions, that then can be Bluetoothed to the airband radio for broadcast.
-
The Hoffmann props have a very good system. 3 position, very light. A spring loaded three step collar gives the different blade pitches. Unfortunately, no local prop service centre available now.
-
Great photo! Thanks Cobalt.
-
LSA in USA • 15 years on (AFJ article).
Raytol replied to Garfly's topic in AUS/NZ General Discussion
Hi OME, Why not come to Camden and have a look at the latest Sierra/ Cougar. CroMo frame from firewall to seat back. The aluminium tube spar is not the best use of material. It is about the moment of Inertia of the material. I think Bede used to chemically mill the tube to thin the wall at the tip. The best use of materials is a box, I-beam or C section. -
I find plastic sheeting a pain with vinylester as it will curl up. I use baking paper which is less slippery, can be folded and stays in shape for ages while wet. If doing repairs, I draw the shape of the repair patches on the baking paper back-to-front and then turn it over before wetting out, so that the drawn lines don't show up on the repair glass! The PVC foam comes in segmented and mini segmented sheets which have a glass scrim on one side to hold the blocks together. A touch of car bog holds things together quickly.
-
Hi Bruce, Great to have you back. Misdiagnosis!!!! I would love to come and see how you are going with the construction. Ray
-
I flew an ASW-19 with one water ballast tank full and the other one empty to see what would happen. There was no discernible difference in flight characteristics but on landing, as I slowed down, I could not hold the heavy wing up with aileron. This lead me to think that the load is distributed across the wingspan and the concentration of load is also somewhat spread along the wingspan. This is why pilots can't feel the fuel tanks levels. I guess that is why they put gauges in the tanks to measure the fuel levels!
- 48 replies
-
- 1
-
-
- atc
- emergency landing
-
(and 1 more)
Tagged with:
-
Resorcinol, Epoxy or Polyurethane?
Raytol replied to old man emu's topic in Aircraft Building and Design Discussion
West System is fantastic for coating timber as it has a "wicking agent" in it to help penetrate the timber. It is ok for laminating fiberglass but there is better. West also have a great range of fillers and other chemicals for different uses which are handy. I am keeping an eye on the cyanoacrylate glues as well. They now have gap filling slower and less brittle ones. -
I'm sad to hear this! David and his team did a great job and did not deserve this. There is just not enough people who are interested in flying to have annual AirVenture type show.
-
The XPB Stage 1 underway.
Raytol replied to bexrbetter's topic in Aircraft Building and Design Discussion
Try www.wedgetailaircraft.com.au -
The XPB Stage 1 underway.
Raytol replied to bexrbetter's topic in Aircraft Building and Design Discussion
Hi Bex, I love what you are doing on the computer but you don't seem to be allowing for the"grain" direction in the sheets of material. Aluminium sheets are rolled to thickness and so they are not really a homogeneous ( could not think of the correct term!) material. In "Alclad" sheets this is hidden by the pure aluminium coating but you can see it more clearly on the 6061-T6 sheets. It is much easier to crack aluminium bending it across the grain than with it and it also affects fatigue life. It will probably mean having to buy more sheets of material! When you do your parts for bending you will need to have a "bending allowance" which in most cases gains you material. Also you will need to supply the bending shop with a line to line up their blade for bending ( different if done on a bender or brake press). The bend radius is determined by the thickness of the material. All this information is available in " The Aircraftsman Handbook" or in AC-43. Ray -
I read a book detailing the early history of rotary engines. Felix Wankel tested several concepts before NSU took up the type we know today. It said that one of the concept engines had "too much torque at low RPM to be useful to NSU (as the maker of sports cars) and as NSU had already done the gearbox design the RPM of the engine output shaft was already determined"! That was the diameter of the star wheel was set early. This meant to me that 1/. The 3 pointed rotor in a two shaped chamber was not the only concept tested. I think it said that the "Truck" rotary had a 4 pointed rotor in a 3 shaped chamber. NSU said that it was too complex to machine ( in the days before CNC machines , additive manufacturing equipment). 2/. I don't know for sure but I would think that the "Truck" rotary would of had a much larger distance from the combustion chamber to the output shaft so that the torque of the engine is increased. 3/. In the early days chatter of the seals was a major pain, been sorted with materials technology a long time ago. 4/. Silicon Nitride seals now last a long time even in highly turbocharged engines. 5/. The high energy exhaust gasses are ripe for turbocharging and compounding. I don't think the concept of a rotary motor is dead but we may have to re-think the Mazda type set-up. I wish I still had this book but it was "borrowed" by someone.
-
new buildup of Aircraft structure and testing
Raytol replied to Davidnane's topic in Aircraft Building and Design Discussion
Thruster88 is correct. It is hard to design and build an aircraft and be safe! Knowledge is the key. Start by getting "Laminar Aircraft Structures" by Strojnik. This is the best/ easiest explaination for the structural design. I think it is available from "Aircraft Spruce and Specialty" in the USA. -
Thanks Turbo, Anyone know how he is getting on?
-
Is Sloper ( Mark) still on his Cougar project?
-
new buildup of Aircraft structure and testing
Raytol replied to Davidnane's topic in Aircraft Building and Design Discussion
Hi Davidnane, Is this homebuilt your own design or is it one that has been built before? -
I don't think it was a big an advantage as what they hoped otherwise it would be on every glider by now! The shape of this experiment is not correct. The tip feathers on birds are deflected so as to use the tip vortices or reduce them. They use a cascading effect to add stability especially at high Coefficients of Lift for landing. Each feather has it's own sensing system and can swing and rotate at the same time even when they are highly loaded ( deflected). A possible engineering solution would be to have say 5 tip winglets that can swing and rotate to the same effects. Maybe we need to strap a Wedge Tailed Eagle to the front of a glider to see what happens!
-
Hi Skippy, I was specifically referring to a Lancair 360's control surfaces which are all hinged with aluminium extruded hinge. I have done centre mounted hinges as well but they are a lot harder! I have never seen dust stick to the outer surface of the tape. I forgot to mention that the Lancair flaps are hinged on the bottom surface and the water and dust can stay so you need to lubricate the hinge more than normal.
-
Sure Bruce Tuncks it is easy. Go to Bunnings and look for "Norton Outdoor tape" it is a clearish tape with water resistant glue. It is about 50mm wide. The tape is put where the aluminium hinge is ( ailerons on the top and flaps on the bottom of the surfaces, etc). You can do all the hinged surfaces including the u/c doors! The tape spans the gap, try to get it roughly even on both sides of the hinge. There is some tricks....(1) deflect the surface fully away from the hinge. This allows the surface to keep full deflection and the tape does bunch up a bit but it is better to be sealed than worry about a small bump in the tape ( which seems to flatten in the air). .....(2) If possible extend the tape slightly past the end of the surface and round off the ends ( stops it peeling off). I've probably forgotten something... let me know how you go.
-
I have done gap seals for a Lancair 360 and a Lancair 4. The 360 got an extra 12- 15 knots and the 4 it reduced the overall drag by 17%. It is worth it on heavy slippery aircraft. On the gliders you can actually hear the drag reduction! Not so much on lightly loaded slower aircraft.